Introduction to the Corrosion Resistant Spring Market Landscape
Corrosion resistant springs play a pivotal role across high-performance industries by ensuring reliable mechanical function even under extreme conditions. As sectors such as aerospace, oil & gas, renewable energy, and medical devices demand components that withstand harsh chemical, thermal, and mechanical stresses, these specialized springs have transitioned from niche applications to critical design elements. Advances in material science, including the development of superalloys and high-performance stainless steels, coupled with innovations in precision manufacturing, have elevated corrosion resistance and mechanical endurance. In this dynamic marketplace, stakeholders must understand evolving material options, surface treatment breakthroughs, and regulatory drivers to optimize component selection, reduce total cost of ownership, and enhance product lifecycle. This executive summary offers a clear, data-driven exploration of emerging trends, supply chain challenges, and competitive forces shaping the corrosion resistant spring market-arming decision-makers and technical leaders with actionable insights to capture growth opportunities and reinforce resilience against environmental and geopolitical headwinds.
Transformative Shifts Shaping the Corrosion Resistant Spring Sector
Over the past five years, transformative shifts have redefined the corrosion resistant spring sector. First, material innovation accelerated: the emergence of custom alloys combining copper and molybdenum with nickel-base matrices has unlocked previously unattainable strength-to-weight ratios and corrosion tolerance. Second, additive manufacturing and laser-assisted precision machining have streamlined complex geometries, reduced lead times, and minimized waste. Third, environmental and regulatory pressures intensified, prompting broader adoption of passivation, polymer-coated finishes, and life-cycle assessment frameworks. Fourth, digitalization infiltrated quality control: inline sensors now monitor fatigue life and surface integrity in real time, enabling predictive maintenance. Finally, industry leaders have shifted toward collaborative, end-to-end partnerships with OEMs to co-develop springs tailored to critical applications in aerospace, defense, and renewable energy. Together, these converging forces are reshaping value chains, unlocking new application domains, and challenging traditional players to rethink product portfolios and operational strategies.
Cumulative Impact of United States Tariffs 2025 on Corrosion Resistant Springs
Beginning in early 2025, the United States implemented a series of cumulative tariffs targeting imported raw materials and finished metal components, exerting significant pressure on corrosion resistant spring manufacturers. Tariff rates on select alloys rose by 5% to 15%, effectively raising procurement costs for specialty nickel alloys, titanium, and custom composite materials. In response, many producers have adapted through nearshoring of coil stock supply, renegotiated long-term contracts with domestic mills, and implemented surcharges to preserve margin. Despite these efforts, small and medium-sized manufacturers face heightened risk of margin erosion, as passing full cost impacts to end customers remains challenging in highly competitive segments such as consumer electronics and industrial machinery. Simultaneously, larger enterprises are leveraging integrated supply chains to absorb duties and maintain price stability while exploring alternative materials that balance corrosion performance with tariff-exempt classifications. This evolving tariff landscape underscores the need for agile procurement strategies, robust scenario planning, and proactive engagement with trade regulators to mitigate financial exposure.
Key Segmentation Insights for Corrosion Resistant Springs
Insightful segmentation analysis reveals distinct performance and growth dynamics across material composition, end use industry, application type, manufacturing process, temperature resistance, mechanical properties, and surface treatment categories. Within material composition, custom alloys typified by copper alloy and molybdenum alloy blends compete alongside established options such as Inconel, nickel alloys, stainless steel, and titanium, each offering unique corrosion profiles and cost structures. In the end use industry dimension, aerospace applications-split between commercial and defense platforms-drive premium pricing and stringent quality requirements, while automotive, electronics, industrial machinery, medical, oil and gas, and renewable energy segments demand scalable volumes with adaptable performance grades. Regarding application type, compression springs dominate standard force requirements, constant force springs address specialized load curves, extension springs provide tensile resilience, precision springs-especially micro springs-serve miniaturized devices, and torsion springs enable rotational energy storage. Cold coiling, die cutting, hot coiling, and precision machining processes-further refined through CNC machining and laser cutting-determine production throughput, dimensional accuracy, and cost efficiency. Temperature resistance tiers, from low to ultra high, align with downstream operating environments, while mechanical properties such as creep resistance, cyclic load resistance (a subset of fatigue resistant), high strength, impact resistance, and lightweight design inform alloy selection and heat-treatment protocols. Finally, surface treatment options, including anodized, metal coated, polymer coated, passivated, and uncoated finishes, provide tailored protection against corrosive media and abrasion.
This comprehensive research report categorizes the Corrosion Resistant Spring market into clearly defined segments, providing a detailed analysis of emerging trends and precise revenue forecasts to support strategic decision-making.
- Material Composition
- End Use Industry
- Application Type
- Manufacturing Process
- Temperature Resistance
- Mechanical Properties
- Surface Treatment
Key Regional Insights in the Corrosion Resistant Spring Industry
Regional dynamics reveal differentiated demand drivers and competitive landscapes across the Americas, Europe Middle East & Africa, and Asia-Pacific zones. In the Americas, mature automotive and aerospace supply chains foster high-value applications, underpinned by recent nearshoring trends that secure alloy feedstock. Europe Middle East & Africa benefits from robust industrial machinery and oil & gas projects, with stringent environmental regulations accelerating adoption of coated and passivated finishes. Meanwhile, Asia-Pacific stands out for rapid capacity expansion, especially in China, Japan, and South Korea, where renewable energy investments and consumer electronics manufacturing exert sustained demand for micro springs and precision components. Supply chain resilience priorities also diverge: the Americas emphasize domestic sourcing, Europe Middle East & Africa invest in surface treatment technologies, and Asia-Pacific drives cost competitiveness through process automation. Collectively, these regional nuances underscore the importance of tailored market entry strategies, localized production networks, and collaborative R&D partnerships to capture growth pockets and mitigate geopolitical and supply chain risks.
This comprehensive research report examines key regions that drive the evolution of the Corrosion Resistant Spring market, offering deep insights into regional trends, growth factors, and industry developments that are influencing market performance.
- Americas
- Asia-Pacific
- Europe, Middle East & Africa
Key Companies Driving Corrosion Resistant Spring Innovations
Competitive intensity in the corrosion resistant spring market is shaped by a broad spectrum of specialized and diversified players. Leading firms such as AccuGuard Spring Technologies, Advanced Corrosion Solutions Inc., AlloySpring Industries LLC, ChemCorro Springs International, CorroMax Mechanical Solutions, CorroShield Spring Systems Inc., CorroVac Springs Inc., Durasteel Mechanical Inc., EcoDurable Springs Corp., EliteCorro Industries Inc., Empower Spring Technologies Inc., Everlasting Spring Industries Ltd., Fusion Alloy Springs Inc., FutureProof Springs LLC, HighCycle Springs & Engineering Inc., Inox Springs Ltd., Integrity Springs Co., MarineGuard Springs Ltd., MarineTech Spring Co., NovaSpring Technologies, Olympus Springs and Components Inc., Precision Stainless Hardware Inc., PrimeCorrosion Resistant Springs Inc., ProCorrosion Spring Solutions, Resilient Springs & Products Inc., SecureMat Springs Corporation, Sparkling Corrosion Solutions Inc., Stainless Springs Corporation, TrueAlloy Spring Manufacturing and Zenith Alloy Springs Ltd. differentiate through proprietary alloy formulations, integrated surface finishing capabilities, and advanced analytics for lifecycle management. Niche innovators focus on micro spring precision, while larger integrators leverage scale economies and global service networks. Strategic collaborations between material suppliers and equipment manufacturers further strengthen competitive moats by accelerating time-to-market for novel corrosion resistant solutions. In this environment, success hinges on continuous innovation, regulatory compliance expertise, and the ability to deliver turnkey services that span design validation, production, and post-sales support.
This comprehensive research report delivers an in-depth overview of the principal market players in the Corrosion Resistant Spring market, evaluating their market share, strategic initiatives, and competitive positioning to illuminate the factors shaping the competitive landscape.
- AccuGuard Spring Technologies
- Advanced Corrosion Solutions Inc.
- AlloySpring Industries LLC
- ChemCorro Springs International
- CorroMax Mechanical Solutions
- CorroShield Spring Systems Inc.
- CorroVac Springs Inc.
- Durasteel Mechanical Inc.
- EcoDurable Springs Corp.
- EliteCorro Industries Inc.
- Empower Spring Technologies Inc.
- Everlasting Spring Industries Ltd.
- Fusion Alloy Springs Inc.
- FutureProof Springs LLC
- HighCycle Springs & Engineering Inc.
- Inox Springs Ltd.
- Integrity Springs Co.
- MarineGuard Springs Ltd.
- MarineTech Spring Co.
- NovaSpring Technologies
- Olympus Springs and Components Inc.
- Precision Stainless Hardware Inc.
- PrimeCorrosion Resistant Springs Inc.
- ProCorrosion Spring Solutions
- Resilient Springs & Products Inc.
- SecureMat Springs Corporation
- Sparkling Corrosion Solutions Inc.
- Stainless Springs Corporation
- TrueAlloy Spring Manufacturing
- Zenith Alloy Springs Ltd.
Actionable Recommendations for Industry Leaders
Industry leaders should take decisive steps to capitalize on emerging opportunities and fortify against volatility. First, invest in advanced alloy research targeting enhanced corrosion tolerance and reduced reliance on tariff-sensitive materials. Second, diversify supplier networks across multiple regions to hedge against trade disruptions and raw material shortages. Third, integrate inline digital inspection and predictive analytics to optimize quality control and minimize warranty risk. Fourth, deepen partnerships with OEMs in aerospace, renewable energy and medical segments to co-develop application-specific springs that command premium margins. Fifth, accelerate development of eco-friendly surface treatments and proprietary coatings to meet tightening environmental regulations. Sixth, explore strategic mergers, acquisitions or joint ventures to expand capacity, access new geographies and bolster technical capabilities. Finally, engage proactively with policymakers and trade bodies to influence tariff policies and safeguard supply chain resilience.
Explore AI-driven insights for the Corrosion Resistant Spring market with ResearchAI on our online platform, providing deeper, data-backed market analysis.
Ask ResearchAI anything
World's First Innovative Al for Market Research
Conclusion on Market Opportunities and Challenges
The corrosion resistant spring market stands at an inflection point where material ingenuity, digital transformation, and geopolitical forces converge. Manufacturers that align R&D investments with evolving end-use requirements, embrace agile supply chain practices, and leverage data-driven quality assurance will outpace competitors. Simultaneously, regulatory compliance and sustainability imperatives will reshape product development roadmaps, favoring eco-conscious surface treatments and circular economy principles. As regional dynamics diverge, developing localized production footprints and strategic alliances will ensure cost efficiency and market access. Ultimately, success depends on a holistic approach-melding technical excellence with commercial acuity-to deliver corrosion resistant springs that meet the most exacting performance standards while navigating a complex trade and regulatory environment.
This section provides a structured overview of the report, outlining key chapters and topics covered for easy reference in our Corrosion Resistant Spring market comprehensive research report.
- Preface
- Research Methodology
- Executive Summary
- Market Overview
- Market Dynamics
- Market Insights
- Cumulative Impact of United States Tariffs 2025
- Corrosion Resistant Spring Market, by Material Composition
- Corrosion Resistant Spring Market, by End Use Industry
- Corrosion Resistant Spring Market, by Application Type
- Corrosion Resistant Spring Market, by Manufacturing Process
- Corrosion Resistant Spring Market, by Temperature Resistance
- Corrosion Resistant Spring Market, by Mechanical Properties
- Corrosion Resistant Spring Market, by Surface Treatment
- Americas Corrosion Resistant Spring Market
- Asia-Pacific Corrosion Resistant Spring Market
- Europe, Middle East & Africa Corrosion Resistant Spring Market
- Competitive Landscape
- ResearchAI
- ResearchStatistics
- ResearchContacts
- ResearchArticles
- Appendix
- List of Figures [Total: 30]
- List of Tables [Total: 601 ]
Connect with Ketan Rohom to Acquire the Complete Market Research Report
To gain comprehensive insights, detailed analysis, and strategic guidance on corrosion resistant spring market dynamics, contact Ketan Rohom, Associate Director, Sales & Marketing at 360iResearch. He will provide customized information on methodology, detailed segmentation data, and exclusive recommendations that empower your organization to make informed decisions and secure competitive advantage.
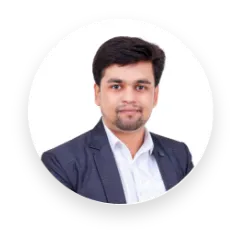
- When do I get the report?
- In what format does this report get delivered to me?
- How long has 360iResearch been around?
- What if I have a question about your reports?
- Can I share this report with my team?
- Can I use your research in my presentation?