The Cutting Equipment Market size was estimated at USD 4.96 billion in 2024 and expected to reach USD 5.20 billion in 2025, at a CAGR 4.76% to reach USD 6.56 billion by 2030.

Unveiling the Cutting Equipment Market’s Pivotal Role in Modern Manufacturing
The cutting equipment market has emerged as a cornerstone of modern manufacturing, enabling unprecedented levels of precision and throughput across diverse industries. As global supply chains evolve and end users demand thinner tolerances with minimal waste, advanced cutting solutions have become indispensable. From automotive body panels and aerospace alloys to intricate sheet metal in architectural design, the ability to execute complex cuts with speed and accuracy underpins operational excellence and drives competitive differentiation.
Over the past decade, technological breakthroughs in laser, plasma, oxyfuel, and waterjet cutting have expanded the boundaries of what is achievable on the factory floor. These advancements have unlocked new applications, reduced total cost of ownership, and enhanced environmental sustainability. In parallel, manufacturers are investing in digital control systems that streamline setup, optimize cutting paths, and facilitate real-time monitoring, thereby minimizing downtime and improving yield.
This executive summary distills the critical forces shaping the market today, from evolving customer requirements and shifting regulatory landscapes to the strategic maneuvers of leading equipment suppliers. By examining transformative shifts, the cumulative impact of recent trade policies, deep segmentation insights, regional dynamics, and forward-looking recommendations, this analysis equips decision-makers with the actionable intelligence needed to navigate a rapidly changing ecosystem and capitalize on emerging opportunities.
Drawing on primary interviews with OEM executives, data from key industry associations, and rigorous analysis of market trends, this concise synthesis highlights critical areas of growth and risk. It is designed to support strategic planning initiatives, guide investment decisions, and inform product development roadmaps, ensuring that stakeholders remain at the forefront of innovation and market leadership
Shifting Paradigms in Precision Cutting Technologies
In recent years, the cutting equipment landscape has undergone profound transformation driven by accelerating digitalization and Industry 4.0 initiatives. Manufacturers increasingly seek systems that integrate seamlessly with enterprise resource planning platforms, enabling automated job scheduling, predictive maintenance, and analytics-driven optimization. This shift toward connected manufacturing fosters greater agility, allowing users to pivot rapidly between product variants and adapt to fluctuating demand without sacrificing throughput or quality.
Concurrently, the industry has witnessed a surge in demand for sustainable practices, prompting suppliers to develop machines that reduce energy consumption, lower carbon footprints, and minimize material waste. Laser cutting solutions have been enhanced with servo-driven beam delivery and optimized gas management, achieving cleaner cuts at faster speeds. Plasma cutting systems now leverage high-definition technology to deliver fine edge quality with reduced slag, while waterjet platforms incorporate abrasive recycling and closed-loop water purification to limit environmental impact.
Material innovation has further expanded the frontier of cutting capabilities, with advanced alloys, composites, and hybrid structures challenging traditional processing methods. The convergence of additive and subtractive manufacturing in a single platform is emerging as a key differentiator, enabling manufacturers to produce complex geometries with minimal post-processing. Looking ahead, the integration of artificial intelligence and machine learning promises to elevate cutting precision through adaptive process control, real-time defect detection, and continuous self-optimization.
How 2025 Tariffs Reshape the United States Market Dynamics
The implementation of new tariff measures in 2025 has materially altered the competitive landscape for cutting equipment suppliers and end users in the United States. By imposing additional duties on imported steel, aluminum, and select cutting machine components, policy makers have sought to revitalize domestic manufacturing capacity. While these measures have provided a short-term boost to local producers of raw materials, they have also introduced price volatility and supply constraints for equipment assemblers who rely on global sourcing networks.
As material costs climb, original equipment manufacturers have been compelled to reevaluate their procurement strategies, shifting toward nearshoring and dual-sourcing arrangements to mitigate risk. Higher input prices have translated into increased capital expenditure requirements for end users, prompting some to delay or downsize system upgrades. Conversely, certain market segments, such as large-scale job shops and heavy-industry fabricators, have seized the opportunity to invest in in-house manufacturing and maintenance capabilities, thereby reducing long-term operating expenses and supply chain exposure.
The ripple effects of these tariff adjustments are evident in the accelerated adoption of domestic service networks and aftermarket support models. Equipment providers are expanding on-shore parts inventories and localized service centers to maintain high uptime levels and ensure rapid response to critical breakdowns. Meanwhile, policy uncertainty around future trade agreements has heightened the importance of flexible contract terms and collaborative risk-sharing arrangements between suppliers and customers. Collectively, these dynamics underscore the necessity for industry stakeholders to adopt proactive strategies that balance cost management with supply chain resilience.
Decoding Market Segments to Reveal Growth Catalysts
Understanding market segmentation is essential for identifying high-potential opportunities and tailoring solutions to specific needs. When equipment type is considered, the landscape comprises laser cutting machines, which are further differentiated into CO2 laser, fiber laser, and Nd:YAG laser variants, each offering distinct advantages in terms of speed, precision, and material compatibility. Oxyfuel cutting machines continue to serve budget-sensitive applications with robust performance on thicker sections, while plasma cutting machines, available as either conventional plasma or high-definition plasma models, provide a cost-effective alternative for mild steel processing. The waterjet cutting category, encompassing both abrasive waterjet and pure waterjet systems, is prized for its ability to cut heat-sensitive materials and create intricate profiles without thermal distortion.
Power source emerges as a critical determinant of machine performance and lifecycle cost. Electric drives dominate in applications requiring rapid positioning and fine control, whereas hydraulic power remains prevalent in heavy-duty systems that necessitate high mechanical force. Pneumatic powered units are favored in settings where simplicity and ease of maintenance are paramount. In parallel, the choice between computer numerical control and manual operation influences both throughput and skill requirements; CNC platforms enable unattended operation and high repeatability, while manual systems offer lower capital expenditure for entry-level users.
Machine footprint and capacity are equally pivotal, with large, medium, and small configurations addressing everything from mass production lines to shop-floor prototyping environments. Larger machines deliver high cutting velocities and greater sheet handling capabilities, while smaller units excel in tight spaces and low-volume runs. End user industries shape demand patterns, as the aerospace sector’s stringent tolerance and certification prerequisites drive investment in advanced laser and waterjet solutions. The automotive industry’s need for rapid throughput favors high-definition plasma and fiber laser technologies, while construction applications, both commercial and residential, lean toward oxyfuel and abrasive waterjet machines for structural steel and stone.
Within metal fabrication, industrial fabricators and job shops exhibit divergent purchasing behaviors. Industrial fabricators prioritize total cost of ownership and long-term service agreements, whereas job shops place greater emphasis on versatility and quick lead times. Shipbuilding demands cutting systems capable of handling thick steel plates and corrosion-resistant alloys, underscoring the value of robust oxyfuel and high-power plasma configurations. The application spectrum ranges from pipe cutting and plate cutting to profile, sheet, and tile cutting, each presenting unique toolpath requirements and consumable usage profiles. Finally, distribution channels bifurcate into offline and online paths, with traditional dealer networks retaining strength in asset-heavy installations and digital platforms gaining traction for spare parts and accessory sales. By aligning segment-specific product features, service models, and pricing structures with customer expectations, market participants can unlock targeted growth and reinforce competitive positioning.
This comprehensive research report categorizes the Cutting Equipment market into clearly defined segments, providing a detailed analysis of emerging trends and precise revenue forecasts to support strategic decision-making.
- Equipment Type
- Power Source
- Control Type
- Machine Size
- End User Industry
- Application
- Distribution Channel
Regional Dynamics Steering Global Cutting Equipment Adoption
Regional market dynamics significantly influence the adoption and evolution of cutting equipment technologies. In the Americas, strong manufacturing bases in North America, coupled with recent investments in reshoring, have sustained demand for advanced laser and plasma systems. The focus on operational resilience has prompted end users to upgrade legacy equipment and embrace integrated automation, while major OEMs continue to expand their service networks to meet rapid response requirements across key industrial hubs.
Europe, Middle East & Africa presents a more nuanced picture, with stringent environmental regulations and energy efficiency targets driving uptake of low-emission cutting solutions. Western European countries lead in deploying fiber laser machines for high-precision applications, whereas emerging economies in the Middle East and Africa invest predominantly in oxyfuel and conventional plasma systems to support infrastructure and construction projects. Cross-regional partnerships and government-led industrial initiatives are catalyzing technology transfers, fostering a mix of mature and growth-oriented markets.
Asia-Pacific remains the fastest-growing region, underpinned by robust demand from electronics, automotive, and shipbuilding industries. Cost competitiveness and large-scale production imperatives have propelled manufacturers to adopt high-throughput fiber laser platforms and automated production lines. In parallel, the rise of digital manufacturing hubs in East Asia is accelerating cloud-based process optimization and remote monitoring solutions. As regional players seek to differentiate through service excellence and local customization, strategic alliances and joint ventures are reshaping the competitive landscape and unlocking new avenues for market penetration.
This comprehensive research report examines key regions that drive the evolution of the Cutting Equipment market, offering deep insights into regional trends, growth factors, and industry developments that are influencing market performance.
- Americas
- Europe, Middle East & Africa
- Asia-Pacific
Competitive Landscape Spotlight on Leading Industry Innovators
Leading equipment manufacturers continue to leverage innovation as a primary catalyst for differentiation in a highly competitive market. Key global players have focused on expanding their laser portfolios to include high-power fiber, ultrafast pulsed, and hybrid laser-waterjet systems that address emerging material processing challenges. These firms have also invested heavily in software development, offering proprietary nesting algorithms and artificial intelligence-driven process control modules that reduce scrap and accelerate cycle times.
Several companies have pursued strategic acquisitions to broaden their service capabilities and geographic reach, integrating aftermarket support providers and specialty consumable manufacturers into their portfolios. By consolidating the value chain, they enhance customer retention through turnkey solutions that bundle equipment, installation, training, and long-term maintenance under unified contracts. Meanwhile, regional challengers in Asia and Eastern Europe are gaining ground by offering cost-competitive alternatives that deliver compelling performance for standard fabrication tasks.
Collaborations between OEMs and technology startups are also gaining traction, with partnerships focusing on the integration of robotics, automated material handling, and real-time quality inspection systems. These alliances are enabling customers to deploy modular cutting cells that can be reconfigured rapidly for different product lines, thereby supporting just-in-time manufacturing strategies. In tandem, service-oriented business models, such as equipment-as-a-service and outcome-based contracts, are emerging as viable pathways to deepen customer engagement and secure recurring revenue streams. By monitoring competitor moves and aligning R&D efforts with evolving customer requirements, industry players can sustain their leadership positions and capture the next wave of market growth.
This comprehensive research report delivers an in-depth overview of the principal market players in the Cutting Equipment market, evaluating their market share, strategic initiatives, and competitive positioning to illuminate the factors shaping the competitive landscape.
- TRUMPF GmbH + Co. KG
- Amada Co., Ltd.
- Bystronic Laser AG
- Yamazaki Mazak Corporation
- Mitsubishi Heavy Industries, Ltd.
- DMG Mori AG
- Messer Cutting Systems GmbH
- Prima Industrie S.p.A.
- Hypertherm, Inc.
- Flow International Corporation
Strategic Imperatives for Industry Leadership and Growth
To thrive in a dynamic cutting equipment market, industry leaders must embrace a forward-looking strategy that balances technological investment, operational resilience, and customer intimacy. A critical priority is the acceleration of digital transformation initiatives. Deploying advanced IoT sensors and cloud-based analytics platforms can unlock productivity gains, enable predictive maintenance, and deliver real-time performance benchmarking. By integrating these capabilities into service offerings, equipment providers can reinforce value propositions and foster long-term partnerships.
Supply chain diversification is equally imperative in light of recent trade policy fluctuations and material cost volatility. Establishing regional sourcing hubs and forging strategic supplier alliances can mitigate risk and ensure consistent access to critical components. Simultaneously, adopting modular machine architectures facilitates swift reconfiguration and simplifies spare parts logistics, reducing lead times and minimizing downtime for end users.
Sustainability must be woven into every phase of the product lifecycle, from design and manufacturing through to operation and end-of-life recycling. Investing in energy-efficient drives, eco-friendly consumables, and closed-loop water management will not only reduce environmental impact but also align with customer sustainability targets and regulatory requirements. Furthermore, cultivating a service-oriented culture that emphasizes rapid response, remote support, and skills training will enhance customer satisfaction and unlock aftermarket revenue streams. By executing these strategic imperatives with discipline and agility, industry participants can secure competitive advantage and capture emerging opportunities within the evolving global ecosystem.
Rigorous Methodology Underpinning Market Insights
The insights presented in this report are grounded in a comprehensive research framework that combines primary and secondary sources to ensure accuracy and depth. Primary data was collected through in-depth interviews with original equipment manufacturers, end-user facility managers, industry analysts, and domain experts across key regions. These conversations provided firsthand perspectives on technology adoption rates, procurement criteria, and service expectations.
Secondary research involved a systematic review of corporate publications, technical journals, trade association reports, and government datasets to validate and enrich primary findings. Market segmentation was meticulously defined by equipment type, power source, control type, machine size, end-user industry, application, and distribution channel. Data triangulation techniques were applied to reconcile disparate inputs and arrive at coherent insights.
Quantitative data was analyzed using statistical models to uncover correlations between market variables, while qualitative analysis highlighted emerging trends and strategic imperatives. Rigorous quality control protocols, including peer review and consistency checks, were implemented at each stage to uphold methodological integrity. This robust approach ensures that the report not only captures current market realities but also provides a reliable foundation for strategic decision-making.
Explore AI-driven insights for the Cutting Equipment market with ResearchAI on our online platform, providing deeper, data-backed market analysis.
Ask ResearchAI anything
World's First Innovative Al for Market Research
Synthesis of Findings and Strategic Outlook
This analysis illuminates the convergence of technological innovation, trade policy dynamics, and evolving customer demands that define the current cutting equipment market. The transition toward digitally integrated machining platforms, coupled with heightened emphasis on sustainability, underscores the industry’s trajectory toward smarter, greener operations. Tariff adjustments in the United States have reinforced the need for supply chain resilience and have catalyzed investments in localized manufacturing and service networks.
Deep segmentation insights reveal that equipment type, power source, control systems, machine size, end-user industry, and application each play a pivotal role in shaping procurement and usage patterns. Regional dynamics-from reshoring efforts in the Americas to regulatory drivers in Europe, the Middle East & Africa, and the rapid growth of Asia-Pacific-further contextualize market opportunities. Competitive analysis highlights the strategic fusion of product innovation, aftersales services, and collaborative business models as key differentiators for leading players.
Looking ahead, industry participants that align technology roadmaps with customer objectives, diversify supply chains, and adopt outcome-oriented service frameworks will be best positioned to capture emerging demand. This synthesis serves as a strategic compass for executives and investors seeking to navigate uncertainties, seize growth avenues, and establish sustainable competitive advantage in a rapidly evolving global marketplace.
This section provides a structured overview of the report, outlining key chapters and topics covered for easy reference in our Cutting Equipment market comprehensive research report.
- Preface
- Research Methodology
- Executive Summary
- Market Overview
- Market Dynamics
- Market Insights
- Cumulative Impact of United States Tariffs 2025
- Cutting Equipment Market, by Equipment Type
- Cutting Equipment Market, by Power Source
- Cutting Equipment Market, by Control Type
- Cutting Equipment Market, by Machine Size
- Cutting Equipment Market, by End User Industry
- Cutting Equipment Market, by Application
- Cutting Equipment Market, by Distribution Channel
- Americas Cutting Equipment Market
- Europe, Middle East & Africa Cutting Equipment Market
- Asia-Pacific Cutting Equipment Market
- Competitive Landscape
- ResearchAI
- ResearchStatistics
- ResearchContacts
- ResearchArticles
- Appendix
- List of Figures [Total: 30]
- List of Tables [Total: 550 ]
Secure Your Comprehensive Market Intelligence Today
For executives and decision-makers poised to leverage the insights from this in-depth analysis, personalized guidance is just one conversation away. Contact Ketan Rohom, Associate Director of Sales & Marketing, to discuss how tailored research insights can inform your strategic planning, optimize procurement decisions, and identify white-space opportunities. By partnering with an expert who understands the nuanced dynamics of cutting equipment markets, you can accelerate time to value and safeguard your competitive positioning. Reach out today to secure your copy of the full market research report and embark on a data-driven pathway to growth and innovation.
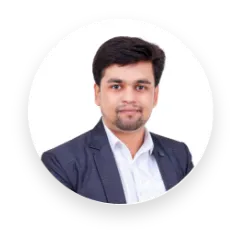
- How big is the Cutting Equipment Market?
- What is the Cutting Equipment Market growth?
- When do I get the report?
- In what format does this report get delivered to me?
- How long has 360iResearch been around?
- What if I have a question about your reports?
- Can I share this report with my team?
- Can I use your research in my presentation?