Introduction to the Deburring and Finishing Machinery Market
The deburring and finishing machinery market stands at the forefront of advanced manufacturing, addressing both aesthetic and functional demands across diverse industries. As product lifecycles accelerate and precision tolerances tighten, effective removal of burrs and surface imperfections has become indispensable. Manufacturers are under mounting pressure to enhance throughput, ensure repeatable quality, and comply with stringent regulatory standards. Against this backdrop, deburring equipment has evolved far beyond manual tools; today’s solutions integrate high-speed automation, adaptive controls, and real-time monitoring to achieve consistent finishes with minimal operator intervention.
This report delves into the latest technological breakthroughs, market dynamics, and strategic implications shaping the sector. It synthesizes insights on machine architectures, abrasive media, and process methodologies, providing decision-makers with a clear understanding of competitive drivers and growth levers. By examining emerging end-user requirements and macroeconomic factors, this analysis equips stakeholders with the context needed to navigate a rapidly transforming landscape and to harness opportunities in precision surface finishing.
Transformative Shifts Reshaping the Deburring Equipment Landscape
Manufacturing has entered a new era characterized by digital integration and heightened demand for flexibility. Industry 4.0 platforms now converge with deburring processes, enabling predictive maintenance and adaptive control of cutting forces. Robotic workcells coordinate with laser and ultrasonic modules to tackle complex geometries, while data-driven analytics optimize abrasive consumption and cycle times. Meanwhile, environmental regulations and sustainability goals have prompted a shift toward closed-loop fluid management and eco-friendly abrasive materials.
Moreover, as supply chains become more agile, customization at scale is gaining importance. End users in aerospace and medical devices increasingly require tightly controlled surface conditions to ensure component performance and safety. In response, manufacturers are investing in multi-axis systems capable of transitioning seamlessly between heavy deburring and fine polishing within the same production cell. These transformative shifts underscore the convergence of digitalization, sustainability, and precision in reshaping the future of deburring machinery.
Assessing the Cumulative Impact of US Tariffs in 2025 on Deburring Equipment
The introduction of new tariff measures by the United States in 2025 has created significant ripple effects across the deburring machinery supply chain. Higher duties on imported steel and aluminum have elevated raw material costs for equipment fabricators, leading to margin compression and selective price adjustments. At the same time, domestic steel producers have ramped capacity to meet increased demand, creating opportunities for local sourcing but also requiring qualification of new supplier streams.
As a result, original equipment manufacturers (OEMs) are reevaluating their global footprints and supply strategies. Some have relocated critical machining centers closer to end-user clusters to mitigate tariff exposure, while others have accelerated the adoption of modular platforms that can be assembled in multiple regions. Tier-one system integrators are factoring duty differentials into long-term procurement contracts, negotiating cost-sharing arrangements and alternative material specifications. Collectively, these strategic responses illustrate how tariff pressures are reshaping not only cost structures but also collaborative ecosystems across the deburring equipment market.
Key Segmentation Insights Across Machine Types, Materials, and Technologies
Segmentation analysis reveals nuanced market dynamics driven by varied customer demands and technological capabilities. When examining machine type, automatic machines lead demand in high-volume plants, manual machines retain relevance for low-volume and prototype runs, and robotic machines are favored in applications requiring complex tool paths. Based on material substrate, metal components dominate overall usage, yet ceramics and composites are gaining traction in aerospace, while plastic parts require specialized belt and brush configurations. In terms of abrasive type, bonded abrasives excel at heavy stock removal, ceramic abrasives offer durability for precision finishing, and coated abrasives deliver consistent performance on delicate surfaces.
Applications in aerospace and automotive continue to drive innovation in edge radiusing and surface conditioning, while medical device manufacturers emphasize surface smoothing to meet biocompatibility standards. Across end-user industries, aerospace & defense and automotive manufacturing remain the largest adopters, though electronics & semiconductor production is emerging due to miniaturized component requirements. Operation mode choices between dry processing and wet processing hinge on environmental controls and surface cleanliness targets. Controlled force systems and laser technology are reshaping traditional approaches, with ultrasonic technology carving out niches in micro-debur and finishing tasks.
Capacity segmentation shows heavy deburring equipment handling large batch sizes, moderate deburring systems balancing throughput and flexibility, and light deburring modules tailored for fine tolerance work. Tooling system distinctions between fixed, linear, and rotary configurations-with rotary further differentiated into double disc and single disc-enable precise adaptation to part geometries. Component segmentation highlights the continued relevance of abrasive belts and discs alongside brushing and buffing tools. Process type classifications underscore the coexistence of chemical, mechanical, and thermal finishing methods, each offering specific surface interaction benefits.
Production volume segmentation differentiates solutions for high volume production lines from those optimized for medium and low volume orders. Functionality requirements span edge radiusing, surface conditioning, and surface smoothing, with finishing surface considerations varying between external and internal geometries. Integration preferences range from fully integrated systems-seamlessly interfacing with upstream and downstream processes-to stand-alone units offering operational independence. Business models oscillate between full equipment purchase and leasing arrangements, providing financial flexibility. Finally, price range segmentation-from economy to mid-range to premium-reflects a spectrum of performance, automation, and support offerings catering to diverse capital investment capacities.
This comprehensive research report categorizes the Deburring Finishing Machine market into clearly defined segments, providing a detailed analysis of emerging trends and precise revenue forecasts to support strategic decision-making.
- Machine Type
- Material Substrate
- Abrasive Type
- Application
- End-User Industry
- Operation Mode
- Technology
- Capacity
- Tooling System
- Component
- Process Type
- Production Volume
- Functionality
- Finishing Surface
- Integration
- Business Model
- Price Range
Regional Dynamics: Insights from Americas, EMEA, and Asia-Pacific
Regional market profiles exhibit distinct characteristics driven by industrial ecosystems and regulatory frameworks. In the Americas, strong domestic automotive and aerospace sectors have fueled robust demand for high-precision deburring systems; reshoring initiatives have further solidified local supply partnerships and encouraged investment in modular, scalable equipment. Meanwhile, Europe, Middle East & Africa benefit from a concentration of defense contractors and luxury automotive manufacturers that demand exacting surface finishes, leading to widespread adoption of laser-assisted and ultrasonic deburring technologies.
Across Asia-Pacific, rapid capacity expansions in electronics and semiconductor fabrication centers have elevated requirements for ultra-clean and precise surface treatments. Manufacturers in this region also demonstrate a strong appetite for cost-effective automated deburring solutions, often integrating dry processing modules to minimize fluid handling infrastructure. Furthermore, stringent environmental standards in parts of Asia-Pacific and Europe are accelerating the shift toward sustainable abrasive media and closed-loop filtration systems, reinforcing the global trend toward greener finishing operations.
This comprehensive research report examines key regions that drive the evolution of the Deburring Finishing Machine market, offering deep insights into regional trends, growth factors, and industry developments that are influencing market performance.
- Americas
- Asia-Pacific
- Europe, Middle East & Africa
Competitive Landscape: Leading Players Driving Innovation and Growth
The competitive arena is populated by established players and innovative newcomers, each contributing unique strengths. Abrasive Finishing Inc. and Bel Air Finishing Supply are renowned for their specialized belt and brush systems, while ActOn Finishing Ltd. and Vibra Finish, LLC excel in turnkey automation cell design. Burr King Manufacturing Co., Inc. and Extrude Hone LLC leverage decades of expertise in honing and mass finishing, complementing Finish Tech Corp’s portfolio of high-speed tumbling and vibratory systems. Gala Industries, Inc. and Tipton Manufacturing Company offer precision deburring modules that cater to aerospace and medical device specifications.
European leaders such as BENSELER Oberflächentechnik GmbH, Otec Präzisionsfinish GmbH, and Rosler Oberflächentechnik GmbH have driven advances in automated blast finishing and recirculation systems, while Rösler International GmbH & Co. KG and Walther Trowal GmbH & Co. KG focus on scalable solutions for global production lines. NS Máquinas Industriais, Lda and Kramer Industries, Inc. serve niche industrial engineering markets with customized mechanical and thermal finishing technologies, and Suhner Schweiz AG is a pioneer in portable high-precision deburring tools. Collectively, these companies form an ecosystem characterized by continuous innovation, strategic partnerships, and diverse product portfolios.
This comprehensive research report delivers an in-depth overview of the principal market players in the Deburring Finishing Machine market, evaluating their market share, strategic initiatives, and competitive positioning to illuminate the factors shaping the competitive landscape.
- Abrasive Finishing Inc.
- ActOn Finishing Ltd.
- Bel Air Finishing Supply
- BENSELER Oberflächentechnik GmbH
- Burr King Manufacturing Co., Inc.
- Extrude Hone LLC
- Finish Tech Corp
- Gala Industries, Inc.
- KADIA Produktion GmbH + Co
- Kramer Industries, Inc.
- NS Máquinas Industriais, Lda
- Otec Präzisionsfinish GmbH
- Rosler Oberflächentechnik GmbH
- Rösler International GmbH & Co. KG
- Suhner Schweiz AG
- Tipton Manufacturing Company
- Vibra Finish, LLC
- Vibraclean Ltd.
- Walther Trowal GmbH & Co. KG
Actionable Recommendations for Industry Leaders in Deburring Technology
To maintain a competitive edge, industry leaders should prioritize investment in adaptable automation platforms that accommodate evolving product geometries and batch sizes. Embracing open-architecture control systems will facilitate seamless integration with enterprise resource planning and quality management software, enabling real-time performance monitoring and predictive maintenance. Diversifying supply chains by qualifying regional material sources can mitigate tariff risks and accelerate response times to order fluctuations.
Furthermore, companies should pursue sustainable process strategies by adopting closed-loop fluid systems and eco-friendly abrasive media, thereby reducing operational costs and meeting regulatory targets. Strategic partnerships with technology providers specializing in laser and ultrasonic finishing can unlock novel applications and shorten time to market for complex parts. Finally, offering flexible financial models-ranging from equipment leasing to performance-based service contracts-will broaden accessibility for small and medium-sized manufacturers and foster long-term customer loyalty.
Explore AI-driven insights for the Deburring Finishing Machine market with ResearchAI on our online platform, providing deeper, data-backed market analysis.
Ask ResearchAI anything
World's First Innovative Al for Market Research
Conclusion: Positioning for Success in a Dynamic Market
The deburring and finishing equipment market stands at a pivotal juncture where technological innovation, supply chain realignment, and sustainability demands converge. Organizations that embrace digitalization and modular design will accelerate their path to higher throughput, greater precision, and lower total cost of ownership. At the same time, cultivating resilient supplier networks and investing in eco-efficient processes will ensure adaptability amid policy shifts and environmental regulations.
By strategically aligning R&D initiatives with emerging end-user requirements-such as micro-debur for electronics or biocompatible finishing for medical devices-manufacturers can capture premium market segments. Collaboration across the value chain, including system integrators, abrasive media suppliers, and software developers, will enable holistic solutions that deliver quantifiable performance gains. Ultimately, stakeholders who balance innovation with operational agility will be best positioned to capitalize on growth opportunities and to define the next generation of surface finishing excellence.
This section provides a structured overview of the report, outlining key chapters and topics covered for easy reference in our Deburring Finishing Machine market comprehensive research report.
- Preface
- Research Methodology
- Executive Summary
- Market Overview
- Market Dynamics
- Market Insights
- Cumulative Impact of United States Tariffs 2025
- Deburring Finishing Machine Market, by Machine Type
- Deburring Finishing Machine Market, by Material Substrate
- Deburring Finishing Machine Market, by Abrasive Type
- Deburring Finishing Machine Market, by Application
- Deburring Finishing Machine Market, by End-User Industry
- Deburring Finishing Machine Market, by Operation Mode
- Deburring Finishing Machine Market, by Technology
- Deburring Finishing Machine Market, by Capacity
- Deburring Finishing Machine Market, by Tooling System
- Deburring Finishing Machine Market, by Component
- Deburring Finishing Machine Market, by Process Type
- Deburring Finishing Machine Market, by Production Volume
- Deburring Finishing Machine Market, by Functionality
- Deburring Finishing Machine Market, by Finishing Surface
- Deburring Finishing Machine Market, by Integration
- Deburring Finishing Machine Market, by Business Model
- Deburring Finishing Machine Market, by Price Range
- Americas Deburring Finishing Machine Market
- Asia-Pacific Deburring Finishing Machine Market
- Europe, Middle East & Africa Deburring Finishing Machine Market
- Competitive Landscape
- ResearchAI
- ResearchStatistics
- ResearchContacts
- ResearchArticles
- Appendix
- List of Figures [Total: 50]
- List of Tables [Total: 822 ]
Next Steps: Connect with Ketan Rohom to Secure the Full Market Research Report
Ready to gain unparalleled insights and actionable intelligence? Connect directly with Ketan Rohom, Associate Director, Sales & Marketing, to secure your comprehensive market research report on deburring and finishing machinery. Empower your strategic decisions with data-driven analysis and expert guidance-reach out today to unlock your competitive advantage.
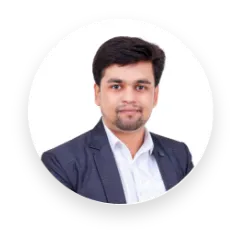
- When do I get the report?
- In what format does this report get delivered to me?
- How long has 360iResearch been around?
- What if I have a question about your reports?
- Can I share this report with my team?
- Can I use your research in my presentation?