Uncovering the Vital Role of Flange-Connected Diaphragm Seals
Flange-connected diaphragm seals serve as critical interfaces between process environments and instrumentation. By isolating sensitive pressure measurement devices from aggressive media, these seals enhance reliability and prolong equipment lifespans. The robust design ensures minimal dead volume while maintaining rapid pressure transmission and effective corrosive resistance. In applications where product purity and operator safety are paramount, the flange connection delivers a secure mounting solution that accommodates high-pressure and high-temperature conditions without compromising measurement accuracy.
Across industries ranging from chemical processing to power generation, diaphragm seals with flange connections mitigate leakage risks and prevent contamination. They streamline maintenance cycles by reducing downtime associated with diaphragm replacement and recalibration. Engineers rely on these components to uphold process integrity under extreme conditions, including rapid pressure fluctuations and exposure to corrosive compounds. As smart sensors and digital control systems expand their footprint within plants, the compatibility of diaphragm-sealed instruments with remote monitoring platforms underscores their strategic importance in contemporary automation infrastructures.
This executive summary distills the essential developments shaping the global diaphragm seal market. It outlines the transformative forces influencing raw material preferences, supply chain dynamics, and competitive strategies, setting the stage for informed decision-making. Subsequent sections explore policy impacts, segmentation nuances, regional divergences, leading company tactics, and actionable recommendations, all designed to equip stakeholders with the insights needed to navigate an evolving industrial landscape.
Emerging Forces Reshaping the Diaphragm Seal Landscape
Recent advancements in automation and digital twin methodologies have accelerated the integration of intelligent monitoring within diaphragm seal assemblies. Suppliers now embed sensor health diagnostics and wireless connectivity, enabling real-time performance tracking and predictive maintenance. Concurrently, escalating environmental and safety regulations compel manufacturers to adopt materials and designs that minimize fugitive emissions and facilitate sterilization. These regulatory imperatives foster innovation in diaphragm materials and flange configurations that balance resilience with compliance.
Material science breakthroughs represent another catalytic force. The emergence of advanced polymers and high-performance alloys delivers unprecedented resistance to chemical attack and thermal cycling. As a result, design optimization efforts increasingly focus on reducing dead band and enhancing response times. Growth in end use sectors such as renewable energy, specialty chemicals, and biopharmaceuticals introduces new performance criteria, prompting a reappraisal of traditional manufacturing processes. Developers are responding with modular, field-replaceable assemblies that align with stringent operational demands while maintaining cost effectiveness.
At the same time, globalization and digital supply chain management are reshaping procurement strategies. End users leverage advanced analytics to source both materials and finished assemblies based on total cost of ownership rather than initial price. This shift elevates the importance of lifecycle services, technical support, and rapid spare parts availability. Suppliers that invest in distributed manufacturing and regional stocking hubs gain a competitive edge by delivering shorter lead times and enhanced on-site support. The convergence of digital innovations, regulatory imperatives, and material evolution is redefining the competitive landscape.
Assessing the Ripple Effects of 2025 US Tariffs on Supply Chains
The imposition of new tariffs on key raw materials and finished assemblies in the United States has introduced volatility and complexity into diaphragm seal supply chains. Manufacturers sourcing elastomers, high-performance polymers, and specialty alloys from global suppliers now face increased input costs and extended lead times. The resulting price adjustments have led many vendors to explore alternative suppliers in low-tariff jurisdictions or pursue localized material production. These adaptations aim to balance cost containment with the exacting performance requirements inherent to critical measurement applications.
Tariff-induced cost pressure also reverberates through distribution channels. Distributors and end users renegotiate long-term contracts to mitigate sudden price escalations, placing greater emphasis on transparent cost structures and risk-sharing arrangements. In some instances, higher landed costs have accelerated the adoption of online procurement platforms that aggregate demand and leverage collective purchasing power. This trend underscores the growing importance of digital marketplaces in neutralizing regional tariff differentials and streamlining transactions across the supply chain.
Research and development teams have intensified efforts to optimize component designs for material efficiency. By reducing diaphragm thickness where feasible, employing elastomer blends with comparable performance at lower cost, or substituting certain metal alloys with more economical alternatives, developers endeavor to offset tariff impacts. These strategies require rigorous validation to ensure consistency in durability and accuracy. To further mitigate risk, several manufacturers have established contingency production lines within the United States to circumvent import levies. Such domestic capabilities enable quicker response to regional demand surges and enhance supply chain robustness. The cumulative impact of 2025 tariffs thus extends beyond immediate cost burdens, catalyzing strategic realignments that will shape future market dynamics.
Segmented Perspectives Across Material, Application, and Performance
In examining material composition, the analysis differentiates among three primary categories: elastomeric seals, metal-seated diaphragms, and polytetrafluoroethylene (PTFE) variants. Elastomeric options encompass synthetic rubbers such as ethylene propylene diene monomer, neoprene, nitrile, and viton, each offering distinct resilience profiles against chemical attack and temperature extremes. Metal-seated designs rely on corrosion-resistant alloys including Hastelloy, Inconel, Monel, and stainless steel to withstand high pressures and prevent embrittlement in aggressive environments. Meanwhile, PTFE solutions are available in glass-filled and virgin forms, delivering exceptional chemical inertness and low friction under variable thermal conditions.
The study further dissects demand drivers based on end use across sectors that span chemical and petrochemical, food and beverage, oil and gas, pharmaceutical, and power generation industries. In chemical processing, the imperative for leak-free performance under corrosive conditions steers material strategy and flange standards, whereas food and beverage applications emphasize hygienic design and regulatory compliance. High-pressure scenarios in oil and gas operations require robust diaphragm thickness and reinforced flanges, while pharmaceutical processes demand sanitary interfaces and minimal dead volume. Power generation environments call for temperature resilience and compatibility with steam or thermal oil cycles.
Performance segmentation by pressure range classifies devices into categories optimized for high, medium, or low pressure applications, informing parameters such as diaphragm geometry and flange rating. Temperature segmentation isolates requirements for ambient, elevated, or cryogenic conditions, shaping material selection and sealing mechanisms. Mounting preferences span field, panel, and rail installations, reflecting diverse instrumentation architectures and maintenance protocols. Distribution pathways encompass direct sales, distributor networks, and online channels, each offering unique advantages in technical support, lead time, and cost transparency. These segmentation insights enable stakeholders to tailor product offerings with precision and capitalize on niche opportunities.
This comprehensive research report categorizes the Diaphragm Seal with Flange Connection market into clearly defined segments, providing a detailed analysis of emerging trends and precise revenue forecasts to support strategic decision-making.
- Material
- End Use Industry
- Pressure Range
- Temperature Range
- Mounting Location
- Distribution Channel
Spotlight on Regional Dynamics Driving Diaphragm Seal Adoption
North American demand for flange-connected diaphragm seals is anchored by well-established industries in oil and gas extraction, petrochemical processing, and power generation. In this region, end users prioritize rapid deployment and reliable aftersales support. Domestic manufacturing capabilities have expanded in response to tariff-induced incentives, fostering localized supply chains and reducing lead times. Strategic investments in regional stocking hubs and service centers highlight the importance of proximity to key customers, ensuring swift calibration and diaphragm replacement when process uptime is critical.
In Europe, the Middle East, and Africa, stringent safety and environmental regulations drive material selection and design innovation. Operators in these markets increasingly adopt advanced metal alloys and PTFE composites to satisfy emission control and contamination prevention standards. Collaborative ventures between European engineering firms and regional operators in the Middle East focus on customized solutions for extreme temperature and pressure conditions prevalent in petrochemical and energy projects. African end users, meanwhile, seek cost-effective designs that balance robust performance with maintenance ecosystems adapted to variable infrastructure quality.
Asia-Pacific emerges as a dynamic growth arena fueled by large-scale infrastructure projects, expanding chemical manufacturing, and rising demand for pharmaceuticals. Countries across the region are constructing new processing facilities and modernizing legacy systems, elevating the need for diaphragm seal technologies that deliver consistent performance under diverse operating conditions. Local manufacturers are scaling production to serve domestic markets while partnering with global suppliers to integrate cutting-edge materials and intelligent monitoring capabilities. The interplay of industrial modernization and regulatory convergence in Asia-Pacific underpins a robust appetite for flange-connected solutions that balance safety, efficiency, and streamlined maintenance.
This comprehensive research report examines key regions that drive the evolution of the Diaphragm Seal with Flange Connection market, offering deep insights into regional trends, growth factors, and industry developments that are influencing market performance.
- Americas
- Europe, Middle East & Africa
- Asia-Pacific
Competitive Strategies Defining Market Leadership
Leading diaphragm seal manufacturers differentiate themselves through a combination of technological innovation, extensive product portfolios, and strategic partnerships. Some global players emphasize proprietary material blends and advanced diaphragm geometries that yield superior response times and extended service intervals. Others capitalize on modular design platforms that support rapid customization, allowing customers to commission tailored assemblies with minimal engineering lead time. This flexibility extends to a variety of flange standards and diaphragm sizes, addressing both standard industrial requirements and highly specialized applications.
Investment in research and development remains a cornerstone of competitive positioning. Industry frontrunners allocate substantial resources to exploring next-generation elastomers and high-performance alloys capable of withstanding extreme chemical and thermal stressors. Concurrently, the integration of digital monitoring capabilities into seal assemblies has emerged as a key differentiator, with manufacturers embedding wireless sensors for real-time diagnostics and remote asset management. Partnerships with automation and analytics providers further enhance service offerings, while alliances with regional distributors extend market reach and local technical support.
Supply chain agility and aftermarket services add another layer of differentiation. By operating distributed manufacturing hubs and regional service centers, top-tier companies ensure rapid delivery of replacement diaphragms, flange fittings, and expert assistance. Warranty programs underpinned by on-site training and calibration services bolster customer confidence in product reliability. Pricing models structured around total cost of ownership reflect an understanding of end users’ needs for predictable maintenance budgets and long-term operational efficiency. Together, these competitive strategies form a robust foundation for sustaining market leadership in a dynamic environment.
This comprehensive research report delivers an in-depth overview of the principal market players in the Diaphragm Seal with Flange Connection market, evaluating their market share, strategic initiatives, and competitive positioning to illuminate the factors shaping the competitive landscape.
- Emerson Electric Co.
- Endress+Hauser AG
- ABB Ltd.
- Siemens AG
- Yokogawa Electric Corporation
- WIKA Alexander Wiegand SE & Co. KG
- KROHNE Messtechnik GmbH
- VEGA Grieshaber KG
- Ashcroft Inc.
- AMETEK Inc.
Strategic Imperatives to Strengthen Market Leadership
Industry leaders should prioritize the integration of digital monitoring features within diaphragm seal assemblies to deliver actionable insights on performance and maintenance requirements. Embedding wireless diagnostics and predictive analytics capabilities can elevate service contracts and reduce unplanned downtime by alerting end users to potential diaphragm fatigue or seal degradation before failures occur. These digital enhancements not only improve reliability but also position manufacturers as proactive partners in operational excellence, fostering deeper customer engagement and loyalty.
Diversifying material portfolios constitutes another strategic imperative. By investing in the development of next-generation elastomeric compounds and corrosion-resistant alloys, companies can address the unique demands of emerging segments such as biopharmaceutical production and renewable energy facilities. Collaborations with material science research institutions and polymer specialists will accelerate innovation cycles, enabling refined formulations that balance chemical resistance, temperature tolerance, and cost efficiency. A flexible manufacturing infrastructure that supports rapid prototyping and small-batch production will further enhance responsiveness to specialized requirements.
Strengthening regional supply chain resilience through localized production and inventory management is crucial in the wake of trade disruptions. Establishing additional manufacturing nodes in key markets supports lead time reduction and mitigates tariff impacts. Close partnerships with distributors and strategic warehousing arrangements ensure that replacement parts and technical teams are available precisely when needed, reinforcing customer trust and retention. Service agreements that include routine inspections, calibration, and technical consultation demonstrate a commitment to long-term performance and deliver clear benefits to industries focused on uptime and operational efficiency.
Data-Driven Approach to Ensure Analytical Rigor
The research underpinning this summary employs a tiered methodology that combines extensive secondary research with targeted primary interviews. Initially, a comprehensive review of industry publications, regulatory frameworks, and patent filings informed the identification of prevailing trends and technological advancements. This foundational work was enhanced by an in-depth examination of trade data, tariff schedules, and documented supply chain disruptions to assess the impact of recent policy changes on material availability and cost structures.
Structured interviews with key stakeholders validated these findings and provided qualitative insights into end user preferences and supplier strategies. Conversations with process engineers, procurement managers, and technical directors delivered nuanced perspectives on performance requirements, installation challenges, and aftermarket service expectations. Triangulation of data from multiple sources ensured consistency and mitigated bias, while consultations with material science and instrumentation experts refined the interpretation of complex performance trade-offs.
Finally, a synthesis phase integrated quantitative data and qualitative feedback into a cohesive narrative, placing emphasis on actionable intelligence rather than descriptive reporting alone. Rigorous cross-checking and peer review protocols were applied to guarantee accuracy, relevance, and clarity. This disciplined, data-driven approach yielded a robust intelligence framework capable of supporting strategic decisions, guiding investment priorities, and charting a clear path forward in the diaphragm seal market.
Explore AI-driven insights for the Diaphragm Seal with Flange Connection market with ResearchAI on our online platform, providing deeper, data-backed market analysis.
Ask ResearchAI anything
World's First Innovative Al for Market Research
Charting the Path Forward in Flange-Connected Diaphragm Seal Markets
The convergence of material innovations, digital integration, and geopolitical shifts has elevated the strategic importance of flange-connected diaphragm seals within critical industrial processes. As regulatory mandates tighten and performance expectations rise, manufacturers and end users must carefully balance cost constraints with the imperative for reliability and safety. Embracing advanced elastomeric and alloy formulations while incorporating real-time monitoring capabilities will define the next generation of seal technologies.
In response to dynamic trade environments, localized production strategies and agile supply chains will prove indispensable. Organizations that establish diversified manufacturing footprints and optimize inventory management can navigate tariff fluctuations with minimal disruption. At the same time, a commitment to value-added services-from predictive maintenance to technical training-will distinguish market leaders and foster enduring customer relationships.
Looking ahead, collaborative innovation between material scientists, instrumentation experts, and digital solution providers will unlock new performance frontiers. By forging partnerships that integrate design, manufacturing, and service ecosystems, stakeholders can address emerging demands in sectors ranging from renewable energy to biopharmaceuticals. Furthermore, precise segmentation by material composition, application sector, and performance parameters will empower companies to align product roadmaps with shifting end user needs and capitalize on specialized opportunities. This integrated approach promises to enhance safety, drive efficiency, and secure sustainable growth in the diaphragm seal market.
This section provides a structured overview of the report, outlining key chapters and topics covered for easy reference in our Diaphragm Seal with Flange Connection market comprehensive research report.
- Preface
- Research Methodology
- Executive Summary
- Market Overview
- Market Dynamics
- Market Insights
- Cumulative Impact of United States Tariffs 2025
- Diaphragm Seal with Flange Connection Market, by Material
- Diaphragm Seal with Flange Connection Market, by End Use Industry
- Diaphragm Seal with Flange Connection Market, by Pressure Range
- Diaphragm Seal with Flange Connection Market, by Temperature Range
- Diaphragm Seal with Flange Connection Market, by Mounting Location
- Diaphragm Seal with Flange Connection Market, by Distribution Channel
- Americas Diaphragm Seal with Flange Connection Market
- Europe, Middle East & Africa Diaphragm Seal with Flange Connection Market
- Asia-Pacific Diaphragm Seal with Flange Connection Market
- Competitive Landscape
- ResearchAI
- ResearchStatistics
- ResearchContacts
- ResearchArticles
- Appendix
- List of Figures [Total: 28]
- List of Tables [Total: 419 ]
Engage with Ketan Rohom for In-Depth Market Research Access
To secure comprehensive insights and strategic guidance on diaphragm seal markets, reach out to Ketan Rohom, Associate Director of Sales & Marketing. With extensive expertise in industrial instrumentation and market analysis, he can provide access to the full research report, which offers an in-depth examination of material trends, tariff impacts, regional dynamics, and competitive strategies. Engaging directly will enable you to align your strategic priorities with the latest intelligence, optimize procurement decisions, and identify growth opportunities. Connect with Ketan Rohom today to discuss how this tailored market study can support your organization’s operational and investment goals.
Whether you seek to refine product development roadmaps, enhance supply chain resilience, or strengthen customer engagement, this report delivers the actionable intelligence necessary to drive informed decisions and sustain market leadership.
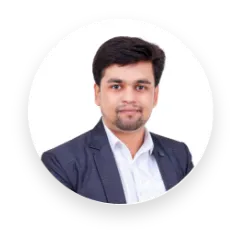
- When do I get the report?
- In what format does this report get delivered to me?
- How long has 360iResearch been around?
- What if I have a question about your reports?
- Can I share this report with my team?
- Can I use your research in my presentation?