Introduction to Die and Flip-Chip Bonding Technologies
Die bonding and flip‐chip bonding technologies have emerged as critical enablers in semiconductor assembly, underpinning rapid advancements across multiple industries. From the precision required in aerospace navigation equipment to the miniaturization demands of wearable electronics, these bonding processes deliver reliable interconnects between chips and substrates. Today’s market is characterized by relentless innovation, driven by trends such as the proliferation of electric vehicles, the rollout of 5G infrastructure, and the integration of diagnostic wearables in healthcare. As product lifecycles accelerate, manufacturers seek bonding solutions that combine speed, accuracy, and cost‐effectiveness. This report unpacks the evolving landscape of die bonders and flip‐chip bonders, highlighting transformative shifts, regulatory impacts, and competitive dynamics. By examining both mature and emerging applications, it provides a holistic view of where value is created and how stakeholders can position themselves to capitalize on growth opportunities. Through a blend of strategic insight and technical analysis, this introduction sets the stage for a detailed exploration of market segmentation, regional trends, key players, and actionable recommendations.
Transformative Shifts Shaping the Bonding Landscape
The die bonder and flip‐chip bonder market has undergone seismic shifts in recent years, propelled by the convergence of miniaturization, higher performance requirements, and Industry 4.0 automation. Innovations in fine‐pitch interconnects have enabled finer aluminum and gold wire bond configurations as well as advanced copper bond processes. At the same time, the emergence of automatic wedge bonding and ultrasonic copper bonding has enhanced throughput while maintaining reliability under demanding operating conditions. Across applications such as electric vehicles with sophisticated driver assistance systems and medical imaging equipment demanding sub‐micron accuracy, advanced flip‐chip processes have gained prominence.
Concurrently, the push toward heterogeneous integration has fostered hybrid solutions that marry ball bonding and flip‐chip technologies within single platforms, reducing assembly steps and improving yields. A growing emphasis on real‐time analytics and machine learning for process control has further accelerated the transition to smart bonding cells. These transformative shifts are reshaping competitive dynamics, with traditional bonder manufacturers partnering with equipment automation specialists to deliver end‐to‐end solutions.
Assessing the Cumulative Impact of U.S. Tariffs in 2025
The introduction of expanded United States tariffs in 2025 has introduced a new layer of complexity for equipment suppliers and end users. Tariffs targeted at advanced bonder technologies-including high‐precision flip‐chip platforms and premium gold wire bonders-have elevated landed costs for imports into the Americas. These levies have prompted multinational equipment manufacturers to reassess global supply chains, optimize production footprints, and negotiate tariff mitigation strategies such as domestic assembly and joint ventures.
Despite increased duties, demand in automotive and consumer electronics sectors has remained robust, leading some suppliers to absorb incremental costs while others have redirected shipments to Europe, Middle East & Africa and Asia‐Pacific to preserve margins. Meanwhile, original equipment manufacturers are adjusting component sourcing strategies by qualifying additional regional suppliers and exploring in‐territory financing incentives. Across the board, companies that proactively updated their trade compliance protocols and invested in localized service networks have mitigated the most adverse effects of the new tariffs.
Unveiling Key Market Segmentation Insights
Application‐driven insights reveal that aerospace and defense equipment, spanning communication devices, navigation systems, and radar platforms, require bonders with ultra‐low alignment tolerances and high reliability under thermal cycling. Automotive applications such as advanced driver assistance systems, electric powertrain modules, and in‐vehicle infotainment demand both speed and robust process control, driving significant uptake of both copper bonding and flip‐chip techniques. Consumer electronics markets, encompassing home appliances, smartphones, tablets, and wearables, prioritize compact footprints and high yield, favoring automated ball and wedge bonders with integrated vision systems. In healthcare, diagnostic devices, medical imaging platforms, and wearable sensors rely on bonding technologies that ensure biocompatibility and long‐term stability. Industrial automation employs power modules, robotics, and sensor assemblies that must endure harsh operating environments, accelerating demand for eutectic bonding methods with advanced material characterization.
On the technology front, fine aluminum wire bonding and heavy gold wire bonding are used where cost-sensitive connections meet reliability requirements, while thermo-compression and ultrasonic copper bonding address the need for higher electrical conductivity and thermal dissipation. Traditional flip‐chip remains relevant for legacy packages, but advanced flip‐chip processes-such as micro-bump arrays with underfill enhancements-are gaining share. Automatic wedge bonding enhances throughput for high‐volume runs, whereas manual wedge bonding retains a role in specialty, low-volume production settings. Device type segmentation shows chip scale, wafer‐level, and RCP packages each demanding optimized bonder toolsets, while displays and optical sensors in optical devices benefit from submicron alignment features. Fully automatic vacuum bonders dominate high-volume semiconductor assembly lines, with semi-automatic platforms serving niche and prototype flows. End user dynamics include component manufacturers and semiconductor fabs in the contract manufacturing space, automotive and electronic device OEMs investing in dedicated in-house assembly, and research and development institutes-both corporate and university labs-evaluating next-generation bonding processes. Bonding type insights indicate that capillary bonding with advanced looping control remains foundational for wire interconnects, and eutectic bonding techniques continue to evolve through tailored metallurgical stacks and process refinements.
This comprehensive research report categorizes the Die Bonder & FC Bonder market into clearly defined segments, providing a detailed analysis of emerging trends and precise revenue forecasts to support strategic decision-making.
- Application
- Technology
- Device Type
- End User
- Bonding Type
Regional Dynamics Driving Growth Patterns
In the Americas region, industry players benefit from proximity to leading automotive manufacturers and aerospace prime contractors, supported by government incentives for semiconductor fabrication and R&D. Supply chain resilience initiatives here focus on reshoring critical component production and expanding in‐country service capabilities. Europe, Middle East & Africa shows heterogeneous adoption patterns, with Western Europe driving high‐end medical imaging and defense applications, and emerging markets in the Middle East investing in smart infrastructure projects that leverage advanced bonding technologies. Meanwhile, Africa remains an emerging frontier, with nascent electronics manufacturing clusters exploring automation solutions. Across Asia‐Pacific, rapid growth in consumer electronics and electric vehicle assembly hubs has fueled demand for both entry-level and fully automated bonders. Strong domestic manufacturers in China, Japan, and South Korea are intensifying competition, while Southeast Asian markets are evolving as key contract manufacturing sites.
This comprehensive research report examines key regions that drive the evolution of the Die Bonder & FC Bonder market, offering deep insights into regional trends, growth factors, and industry developments that are influencing market performance.
- Americas
- Asia-Pacific
- Europe, Middle East & Africa
Leading Players and Their Strategic Positioning
Global suppliers have differentiated themselves through a combination of technological leadership, service networks, and strategic partnerships. ASM Pacific Technology Limited has strengthened its market position by integrating real-time process analytics into its flip-chip platforms, achieving high throughput in wafer‐level packaging. BE Semiconductor Industries (Besi) has expanded its footprint in European automotive markets, leveraging its fine-aluminum and wedge bonding solutions for ADAS modules. EV Group (EVG) focuses on advanced flip-chip and hybrid bonding processes tailored for 5G and photonics applications. F&K Delvotec Bondtechnik GmbH excels in customized wire bonder deployments for medical devices and aerospace systems. Hamni Semiconductor Equipment Manufacturing’s cost-effective wedge bonders have gained traction across consumer electronics assembly lines in Asia. Hesse GmbH’s modular bonders cater to both capillary and eutectic processes, appealing to contract manufacturers with mixed production requirements. K&S Company continues to innovate in thermo-compression copper bonding, targeting power module integration. Kulicke & Soffa Industries, Inc. offers end-to-end solutions, combining ball, wedge, and flip-chip bonders with advanced automation. MRSI Systems has carved a niche with its high-precision bonder platforms for research institutions. Palomar Technologies leads in wedge and ball bonding for semiconductor packaging, while Shinkawa Ltd. specializes in vacuum device bonding applications. TPT Wire Bonder GmbH & Co. KG and West-Bond, Inc. round out the competitive landscape by delivering tailored bonder solutions to specialty markets and research laboratories.
This comprehensive research report delivers an in-depth overview of the principal market players in the Die Bonder & FC Bonder market, evaluating their market share, strategic initiatives, and competitive positioning to illuminate the factors shaping the competitive landscape.
- ASM Pacific Technology Limited
- Besi (BE Semiconductor Industries)
- EV Group (EVG)
- F&K Delvotec Bondtechnik GmbH
- Hamni Semiconductor Equipment Manufacturing Co., Ltd.
- Hesse GmbH
- K&S Company
- Kulicke & Soffa Industries, Inc.
- MRSI Systems
- Palomar Technologies
- Shinkawa Ltd.
- TPT Wire Bonder GmbH & Co. KG
- West-Bond, Inc.
Actionable Recommendations for Industry Leaders
To maintain a competitive edge, industry leaders should prioritize investments in machine-learning enabled process control and inline defect detection systems to boost yields and reduce downtime. Collaborative partnerships across the supply chain-linking equipment OEMs, materials suppliers, and end users-will accelerate the development of hybrid bonding platforms that combine the strengths of ball, wedge, and flip-chip processes. Companies should also explore flexible business models that incorporate equipment-as-a-service offerings, enabling customers to scale production capacity without large capital outlays. Expanding localized service networks and training programs in growth regions will strengthen customer loyalty and shorten repair cycles. Additionally, aligning R&D roadmaps with sustainability objectives-such as reducing wire bond materials usage and optimizing energy consumption in bonder tools-will resonate with environmentally conscious customers and regulators. Finally, scenario planning for trade policy shifts and supply chain disruptions will ensure that contingency measures are in place to safeguard operations and customer commitments.
Explore AI-driven insights for the Die Bonder & FC Bonder market with ResearchAI on our online platform, providing deeper, data-backed market analysis.
Ask ResearchAI anything
World's First Innovative Al for Market Research
Conclusion: Navigating the Future of Bonding Solutions
The evolution of die bonder and flip-chip bonder markets underscores the imperative for continuous innovation and strategic agility. As applications diversify and material requirements become more demanding, equipment providers and end users alike must embrace integrated solutions that offer both precision and throughput. Geopolitical developments, including trade policies and regional manufacturing incentives, will continue to shape supply chain strategies and competitive positioning. By leveraging advanced analytics, automation, and collaborative partnerships, stakeholders can unlock new value streams while mitigating risk. The convergence of multiple bonding technologies into unified platforms promises to reduce complexity and cost, driving wider adoption across end markets. As this landscape evolves, those who balance technical excellence with market responsiveness will secure long‐term leadership.
This section provides a structured overview of the report, outlining key chapters and topics covered for easy reference in our Die Bonder & FC Bonder market comprehensive research report.
- Preface
- Research Methodology
- Executive Summary
- Market Overview
- Market Dynamics
- Market Insights
- Cumulative Impact of United States Tariffs 2025
- Die Bonder & FC Bonder Market, by Application
- Die Bonder & FC Bonder Market, by Technology
- Die Bonder & FC Bonder Market, by Device Type
- Die Bonder & FC Bonder Market, by End User
- Die Bonder & FC Bonder Market, by Bonding Type
- Americas Die Bonder & FC Bonder Market
- Asia-Pacific Die Bonder & FC Bonder Market
- Europe, Middle East & Africa Die Bonder & FC Bonder Market
- Competitive Landscape
- ResearchAI
- ResearchStatistics
- ResearchContacts
- ResearchArticles
- Appendix
- List of Figures [Total: 26]
- List of Tables [Total: 993 ]
Next Steps: Secure Your In-Depth Market Intelligence Today
Contact Ketan Rohom, Associate Director, Sales & Marketing, to obtain comprehensive insights and guidance from this in-depth market research report. Elevate your strategic planning and capitalize on emerging opportunities in die bonding and flip-chip bonding technologies today.
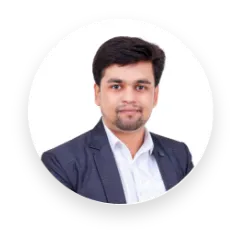
- When do I get the report?
- In what format does this report get delivered to me?
- How long has 360iResearch been around?
- What if I have a question about your reports?
- Can I share this report with my team?
- Can I use your research in my presentation?