The Die Casting Market size was estimated at USD 73.98 billion in 2024 and expected to reach USD 79.16 billion in 2025, at a CAGR 6.67% to reach USD 109.03 billion by 2030.

Unveiling the Dynamic World of Die Casting
The die casting sector stands at the intersection of precision engineering and high-volume production, delivering critical components for industries that demand both performance and reliability. As global supply chains evolve and end-use industries intensify their requirements for lighter, stronger, and more cost-effective parts, die casting emerges as a cornerstone technology. From consumer electronics that rely on intricate housings to the automotive sector’s pursuit of lightweight solutions, the die casting method continues to redefine manufacturing boundaries.
In recent years, the industry has witnessed a convergence of advanced materials, digital process control, and sustainability mandates, all of which have propelled die casting from a traditional production technique to a driver of innovation. Companies are leveraging sophisticated alloy formulations to meet stringent strength-to-weight ratios, while automation and real-time analytics have transformed shop floors into agile, data-driven environments. These shifts are not merely incremental; they represent a fundamental reimagining of how metal components are conceptualized, designed, and delivered at scale.
Against this backdrop, decision-makers must grasp the evolving dynamics shaping the die casting landscape. This introduction sets the stage for an in-depth exploration of transformative market forces, regulatory impacts, segmentation strategies, and regional dynamics that collectively define the sector’s trajectory.
Navigating Transformative Shifts Reshaping the Die Casting Arena
The die casting arena is undergoing transformative shifts that extend beyond the factory floor, each reshaping competitive positions and investment priorities. Digitalization stands at the forefront, with Industry 4.0 solutions enabling predictive maintenance and process optimization through real-time sensor data. This evolution reduces unplanned downtime and elevates quality control, transforming traditional plants into smart, interconnected environments that respond dynamically to production demands.
Simultaneously, sustainability has emerged as a strategic imperative. Manufacturers are adopting closed-loop systems to recapture and recycle alloys, significantly reducing waste and energy consumption. Novel material blends, such as high-silicon aluminum and hot-work steel alloys, deliver performance gains while aligning with increasingly stringent environmental regulations.
The electrification of transportation is another powerful catalyst, driving unprecedented demand for lightweight, thermally conductive parts. Vehicle manufacturers collaborate closely with die casters to develop bespoke alloys and optimized gating designs that enhance battery cooling and structural integrity. In parallel, additive manufacturing technologies are being integrated to produce complex cores and molds, accelerating design iterations and reducing time to market.
These forces, together with geopolitical realignments and labor dynamics, are converging to redefine competitive advantage. Companies that embrace digital transformation, prioritize sustainable practices, and partner across the value chain will be best positioned to capitalize on growth opportunities and navigate emerging challenges.
Assessing the 2025 U.S. Tariff Repercussions on Die Casting
The imposition of U.S. tariffs in 2025 has introduced a new paradigm for die casting supply chains, compelling manufacturers to reassess sourcing strategies and cost structures. Imported ingots and subassemblies now carry elevated duties, eroding traditional cost advantages and prompting a surge in domestic alloy production. In response, many suppliers have invested in local melting capabilities, forging partnerships with scrap processors to secure feedstock at competitive rates.
These measures have triggered broader ripple effects across end-use sectors. Automotive suppliers, facing higher input costs, are negotiating long-term contracts and exploring alternative materials to mitigate tariff impacts. Consumer electronics firms, reliant on precision castings, have diversified their supplier base, expanding into Mexico and Canada to leverage trade agreement benefits and maintain delivery reliability.
While short-term inflationary pressures have intensified, the strategic realignment of supply chains promises greater resilience. Companies that successfully navigated the tariff landscape have optimized inventory buffers, renegotiated logistics agreements, and automated customs compliance processes. This proactive stance has not only stabilized production flows but also unlocked pathways for nearshoring and manufacturing footprint consolidation.
Looking ahead, the cumulative impact of these tariff measures will continue to influence capital expenditure decisions, alliance structures, and product development cycles. Stakeholders who maintain agility in procurement and embrace collaborative innovation will drive sustainable value creation amid evolving trade policies.
Decoding Market Segments to Uncover Growth Pathways
An in-depth examination of market segmentation reveals the multifaceted nature of growth drivers and competitive pressures in die casting. Material segmentation underscores aluminum’s dominance, prized for its strength-to-weight ratio and thermal conductivity, while copper alloys carve out specialized applications in electrical components. Magnesium alloys are gaining traction for ultra-lightweight structures, and zinc continues to serve corrosion-resistant needs in consumer goods.
Across end-use industries, aerospace demands high-precision castings that meet rigorous certification standards, whereas the automotive sector leverages die casting for both commercial and passenger vehicle platforms. The electric vehicle segment further pushes boundaries with bespoke designs that integrate structural and thermal functions. Consumer goods manufacturers rely on die cast housings for everything from power tools to kitchen appliances, and electronics producers capitalize on the process to deliver complex geometries in connectors and heat sinks. Industrial applications, spanning pumps and valves to robotics, further diversify the demand profile.
Process segmentation highlights two primary methods: cold chamber casting, suited for high-temperature alloys such as aluminum and copper, and hot chamber casting, the preferred choice for zinc and magnesium processes. Machine type segmentation showcases the spectrum of automation-from fully automatic systems optimized for high production rates to manual setups ideal for low-volume, specialized runs, with semi-automatic configurations bridging the gap for medium-scale production.
Product attributes also play a critical role, as gear components, precision housings, and large structural elements each command unique design and mold considerations. Furthermore, variations in product size-large, medium, and small-drive differences in cycle times, mold maintenance, and material utilization. By understanding these segmentation dynamics, stakeholders can tailor strategies to target high-growth niches and optimize resource allocation.
This comprehensive research report categorizes the Die Casting market into clearly defined segments, providing a detailed analysis of emerging trends and precise revenue forecasts to support strategic decision-making.
- Material
- End Use Industry
- Process
- Machine Type
- Die Casting Type
- Product Size
Regional Dynamics Driving Die Casting Expansion Globally
Regional dynamics exert a profound influence on die casting evolution, shaping cost structures, regulatory landscapes, and innovation ecosystems. In the Americas, established manufacturing hubs in the United States and Mexico benefit from integrated supply networks and favorable trade agreements, fostering both high-volume automotive and aerospace casting centers. Domestic suppliers invest heavily in alloy recycling and digital manufacturing to maintain competitiveness amid wage inflation and environmental mandates.
Across Europe, the Middle East, and Africa, Germany and Italy anchor a mature market defined by precision engineering and advanced process controls. Sustainability initiatives and circular economy frameworks are driving widespread adoption of remelt technologies, while emerging regions are investing in capacity expansion to serve local infrastructure and heavy machinery demands. Regulatory harmonization across the European Union further streamlines cross-border trade and standardizes quality requirements.
Asia-Pacific remains the largest production base, led by China’s expansive casting facilities and India’s burgeoning industrial sector. Japan and South Korea excel in high-precision, low-tolerance applications, whereas Southeast Asian nations attract investment through cost advantages and improving logistics. Rapid electrification and infrastructure spending throughout the region are fueling demand for specialized alloy components, prompting global players to deepen their presence and forge strategic joint ventures.
These regional distinctions underscore the importance of tailored market entry and growth strategies. By aligning investment decisions with local industry drivers and regulatory environments, companies can capitalize on regional strengths while mitigating geopolitical and operational risks.
This comprehensive research report examines key regions that drive the evolution of the Die Casting market, offering deep insights into regional trends, growth factors, and industry developments that are influencing market performance.
- Americas
- Europe, Middle East & Africa
- Asia-Pacific
Strategic Positioning of Leading Die Casting Players
Leading die casting firms are leveraging strategic investments and partnerships to reinforce market leadership and drive technological innovation. Major players with extensive global footprints are integrating advanced process controls and digital monitoring systems to enhance throughput and quality consistency. Concurrently, specialized manufacturers are carving out niches by offering value-added services such as in-house machining, surface finishing, and assembly integration.
Mergers and acquisitions remain a key growth lever, enabling companies to broaden their material portfolios and consolidate regional operations. Several global suppliers have pursued bolt-on acquisitions in emerging markets to secure local customer relationships and streamline logistics. Meanwhile, joint ventures between foundries and original equipment manufacturers facilitate co-development of bespoke alloys and cast geometries tailored to next-generation product requirements.
Strategic capital expenditure focuses on automation and sustainability. Industry leaders are deploying robotic die handling, closed-loop melting furnaces, and energy-recovery systems to reduce costs and environmental impact. Collaborative research programs with material science institutes are yielding novel alloy formulations that meet increasingly stringent performance standards while adhering to circular economy principles.
By continuously refining their value propositions through technology adoption and strategic alliances, these companies are setting new benchmarks for operational excellence. Their actions serve as a blueprint for other stakeholders seeking to elevate capabilities, optimize supply chains, and capture emerging opportunities across critical end-use industries.
This comprehensive research report delivers an in-depth overview of the principal market players in the Die Casting market, evaluating their market share, strategic initiatives, and competitive positioning to illuminate the factors shaping the competitive landscape.
- Nemak S.A.B. de C.V.
- Dynacast International
- Ryobi Limited
- Linamar Corporation
- UACJ Corporation
- Bharat Forge Limited
- Endurance Technologies Limited
- Georg Fischer AG
- Magna International Inc.
- Nucor Corporation
Strategic Imperatives for Industry Leaders to Secure Competitive Edge
To navigate the complexities of the evolving die casting landscape, industry leaders must embrace a strategic playbook that emphasizes agility, innovation, and resilience. Investing in automation platforms equipped with real-time analytics will elevate productivity and empower predictive maintenance, minimizing downtime and fortifying operational stability. Concurrently, diversifying material capabilities-expanding beyond traditional aluminum frameworks to include advanced copper, magnesium, and zinc alloys-will unlock new application verticals and reduce dependency on single-source technologies.
Forming collaborative partnerships across the value chain enhances innovation velocity and risk sharing. Engaging in co-development agreements with automotive and aerospace OEMs ensures that cast components align precisely with system-level performance targets. Similarly, aligning with logistics and customs experts will streamline cross-border material flows, enabling nearshoring strategies that mitigate tariff impacts and geopolitical volatility.
Sustainability must underpin every decision, from alloy recycling initiatives to energy efficiency programs in foundries. Establishing clear environmental KPIs and integrating them into capital investment criteria will resonate with customers and regulators alike. Simultaneously, building digital twins of critical processes will facilitate rapid scenario planning and continuous improvement, safeguarding competitiveness in an environment defined by swift technological change.
By adopting this multifaceted approach, industry leaders can fortify their market positions, drive margin expansion, and capitalize on the shifting contours of global manufacturing.
Rigorous Methodology Underpinning Comprehensive Market Analysis
This research employs a rigorous methodology designed to deliver comprehensive and reliable insights into the die casting market. Secondary research began with an exhaustive review of industry reports, trade publications, and regulatory filings, establishing a foundational understanding of material trends, process technologies, and regional dynamics. Proprietary databases were leveraged to capture company financials, patent landscapes, and supply chain structures.
Primary research involved in-depth interviews with senior executives, plant managers, and process engineers across major die casting hubs. These conversations yielded qualitative perspectives on operational challenges, investment priorities, and emerging demand patterns. Quantitative data points were validated through cross-referencing multiple sources, ensuring accuracy and consistency.
Data triangulation techniques were applied to reconcile discrepancies and refine segmentation parameters. Market drivers, restraints, and competitive forces were assessed through collaborative expert panels, whose consensus views shaped the analytical framework. Regional and segment-level analyses were constructed using standardized metrics, enabling meaningful comparisons and trend identification.
All findings underwent a multi-stage quality assurance process, including peer reviews and statistical validation, to guarantee methodological integrity. This approach ensures that decision-makers receive actionable intelligence grounded in robust research principles and reflective of the latest industry developments.
Explore AI-driven insights for the Die Casting market with ResearchAI on our online platform, providing deeper, data-backed market analysis.
Ask ResearchAI anything
World's First Innovative Al for Market Research
Concluding Insights on a Pivotal Moment for Die Casting
The die casting industry occupies a pivotal position within the broader manufacturing ecosystem, bridging the gap between innovative design and mass production. As market dynamics evolve under the dual forces of technological progress and regulatory change, stakeholders must remain vigilant, informed, and proactive. This summary has illuminated the key transformative shifts, tariff impacts, segmentation nuances, regional drivers, and competitive strategies shaping the sector.
Collectively, these insights underscore the importance of adopting a holistic perspective-one that integrates material science, digital transformation, and sustainability into every strategic decision. Organizations that successfully align their capabilities with emerging demand patterns will be poised to capture high-value market segments and fortify their supply chain resilience.
In an era defined by rapid innovation and geopolitical complexity, a detailed understanding of market subtleties is indispensable. The ability to anticipate shifts, forge strategic alliances, and execute targeted investments will determine leadership trajectories and drive long-term growth.
By synthesizing rigorous research with actionable recommendations, this report empowers decision-makers to navigate uncertainty and seize opportunities within the dynamic die casting landscape.
This section provides a structured overview of the report, outlining key chapters and topics covered for easy reference in our Die Casting market comprehensive research report.
- Preface
- Research Methodology
- Executive Summary
- Market Overview
- Market Dynamics
- Market Insights
- Cumulative Impact of United States Tariffs 2025
- Die Casting Market, by Material
- Die Casting Market, by End Use Industry
- Die Casting Market, by Process
- Die Casting Market, by Machine Type
- Die Casting Market, by Die Casting Type
- Die Casting Market, by Product Size
- Americas Die Casting Market
- Europe, Middle East & Africa Die Casting Market
- Asia-Pacific Die Casting Market
- Competitive Landscape
- ResearchAI
- ResearchStatistics
- ResearchContacts
- ResearchArticles
- Appendix
- List of Figures [Total: 28]
- List of Tables [Total: 373 ]
Unlock In-Depth Die Casting Insights with Expert Guidance
To explore these strategic insights in greater depth and gain access to comprehensive analyses, detailed data tables, and expert perspectives, engage directly with Ketan Rohom, Associate Director, Sales & Marketing. His expertise in guiding organizations through complex market landscapes ensures that your team will receive tailored recommendations and actionable intelligence. Secure your competitive advantage today by reaching out to Ketan Rohom and initiating the purchase process for the full die casting market research report, designed to empower your decision-making and drive sustainable growth.
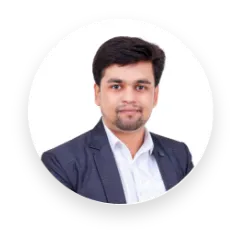
- How big is the Die Casting Market?
- What is the Die Casting Market growth?
- When do I get the report?
- In what format does this report get delivered to me?
- How long has 360iResearch been around?
- What if I have a question about your reports?
- Can I share this report with my team?
- Can I use your research in my presentation?