The Die Casting & Forging Market size was estimated at USD 120.61 billion in 2024 and expected to reach USD 131.65 billion in 2025, at a CAGR 8.98% to reach USD 202.14 billion by 2030.

Unlocking the Future of Die Casting and Forging in Machinery Production
The world of die casting and forging stands at an inflection point where technological innovation and changing global dynamics compel industry stakeholders to rethink traditional approaches. As manufacturers seek greater efficiency, precision, and sustainability, the interplay between advanced processes and evolving materials is reshaping how components are produced across critical end-use industries. From lightweight aerospace parts to complex automotive engine components, the competitive pressure to deliver high-performance outputs with rapid turnaround times has never been greater.
In this context, decision-makers must navigate a marketplace characterized by intensifying supply-chain complexity and emerging geopolitical challenges. Executives and engineers alike require an authoritative synthesis of current trends, transformative breakthroughs, and regulatory impacts to chart a successful path forward. This executive summary distills the essential insights you need to understand the forces driving market evolution, segment-level nuances, and actionable strategies to secure a leadership position in the die casting and forging sector. By examining recent technological advancements, policy shifts, and competitive dynamics, the following sections will equip you with a clear roadmap for strategic growth and innovation.
Navigating the Forces Reshaping Die Casting and Forging Markets
In recent years, several transformative shifts have redefined the landscape of die casting and forging. Automation and digitalization have moved beyond pilot projects to become mainstream drivers of production efficiency. As smart foundries integrate sensors, real-time analytics, and digital twins, manufacturers can anticipate maintenance needs, optimize material flow, and minimize downtime with unprecedented precision.
Simultaneously, the industry is experiencing a paradigm shift toward sustainability. Lightweight alloys, such as magnesium and aluminum, are increasingly adopted to reduce vehicle emissions and improve fuel efficiency. Manufacturers are also pioneering closed-loop systems for scrap recovery and adopting energy-efficient furnaces to lower carbon footprints. The convergence of eco-friendly practices with stricter environmental regulations is fostering a new generation of low-impact manufacturing solutions.
Another key development is the rise of additive-aided processes. While traditional die casting and forging remain core competencies, hybrid manufacturing that combines 3D-printed molds or direct metal deposition for critical features is enabling more complex geometries and shorter time-to-market. As these transformative shifts gain momentum, companies that invest in digital infrastructure, sustainable practices, and hybrid production models will emerge as leaders in a rapidly evolving competitive environment.
Assessing the Ripple Effects of U.S. Tariffs on Material Supplies
The United States has increasingly relied on tariffs as a tool to protect domestic industries, and the cumulative impact of measures introduced in 2025 underscores this trend. New levies on imported aluminum, steel, and specialized alloys have raised input costs for die casting and forging operations that depend on cost-competitive raw materials. Domestic producers with sufficient capacity have seen relief from some external competition, but downstream manufacturers face margin pressure as material procurement becomes more expensive.
These tariff changes have also altered global trade flows, incentivizing sourcing shifts toward alternative suppliers in regions not subject to punitive duties. As a result, supply chains have become more fragmented, compelling manufacturers to diversify their vendor base and reconsider inventory strategies to mitigate cost volatility. Lead times have fluctuated as suppliers in non-tariffed markets scale up production, creating both opportunities and logistical challenges for end users.
Moreover, the ripple effects of U.S. tariffs extend beyond material costs. International competitors have responded with their own countermeasures and subsidies, intensifying the complexity of cross-border investment decisions. Companies that proactively manage tariff exposure through strategic hedging, localized partnerships, and flexible production footprints are better positioned to maintain competitiveness in a landscape where regulatory shifts can have immediate financial consequences.
Deciphering Market Dynamics Through Multidimensional Segmentation
The die casting and forging market can be dissected across multiple dimensions to reveal critical avenues for targeted growth. Based on process, the landscape divides into two primary streams: die casting and forging. The die casting segment encompasses gravity, low pressure, pressure, squeeze, and vacuum techniques, each offering distinct advantages in terms of dimensional accuracy, surface finish, and cycle times. The forging segment captures closed die, open die, precision, and roll forging processes, delivering superior mechanical properties and grain structures that suit high-stress applications.
Material type further refines the market profile. Aluminum remains a cornerstone for its light weight and recyclability, while copper and zinc offer specialized conductivity and corrosion resistance. Steel continues to dominate in heavy-duty applications, and magnesium is gaining traction for ultra-lightweight requirements. Each material category demands unique handling, mold design, and thermal control strategies.
End use industries illuminate demand drivers across aerospace and defense, automotive, construction, electrical and electronics, and industrial machinery. Aerospace and defense applications prioritize weight savings and reliability under extreme conditions, whereas automotive demands focus on high-volume production and cost efficiency. Construction and industrial machinery require durable structural components, while electrical and electronics segments call for intricate geometries and tight tolerances.
Product type segmentation underscores specific application areas such as brackets and frames, engine components, pump housings, structural components, and transmission components. Each product category presents unique design constraints and volume expectations. Finally, sales channels bifurcate into aftermarket and OEM, reflecting divergent service life, customization, and quality assurance requirements. By examining these segmentation lenses in concert, stakeholders can identify high-potential niches and optimize investment across processes, materials, industries, and end-user channels.
This comprehensive research report categorizes the Die Casting & Forging market into clearly defined segments, providing a detailed analysis of emerging trends and precise revenue forecasts to support strategic decision-making.
- Process
- Material Type
- End Use Industry
- Product Type
- Sales Channel
Unveiling Regional Growth Hotspots and Market Drivers
Regional perspectives reveal distinct growth trajectories shaped by economic conditions, infrastructure investment, and policy frameworks. In the Americas, robust automotive production hubs and defense manufacturing ecosystems are driving demand for both die casting and forging. Proximity to major raw material producers and strong aftermarket networks further bolster opportunities for process expansion and supply-chain collaboration.
Moving to Europe, Middle East & Africa, the market is characterized by stringent environmental standards and a surge in electrification initiatives. Automotive powertrain shifts, coupled with renewable energy infrastructure projects, are fueling demand for lightweight, high-strength components. Government incentives for green manufacturing and circular economy practices are accelerating the adoption of advanced alloys and closed-loop recycling systems.
Meanwhile, Asia-Pacific remains a powerhouse of production capacity, with China, India, Japan, South Korea, and Southeast Asia leading the charge. Rapid industrialization, expanding automotive and electronics sectors, and aggressive investments in smart manufacturing technologies are creating fertile ground for both die casting and forging suppliers. As regional players enhance process automation and digital integration, the competitive environment is set to intensify, driving continuous innovation in cost reduction and product differentiation.
This comprehensive research report examines key regions that drive the evolution of the Die Casting & Forging market, offering deep insights into regional trends, growth factors, and industry developments that are influencing market performance.
- Americas
- Europe, Middle East & Africa
- Asia-Pacific
Mapping the Competitive Landscape of Process and Innovation
The competitive landscape of die casting and forging is shaped by a blend of global leaders and specialized niche players. Tier-one manufacturers have strengthened their positions through strategic acquisitions of regional foundries, enabling them to offer end-to-end solutions that range from design engineering and prototyping to mass production and post-processing services. These companies often leverage integrated digital platforms to monitor quality in real time and optimize throughput across multiple facilities.
At the same time, nimble mid-tier and small-scale enterprises are carving out competitive advantages by focusing on specialized alloys, custom tooling, or short-run capabilities. Their agility allows for rapid adaptation to customer specifications and swift incorporation of new process innovations. Partnerships with research institutions further enable these players to pilot emerging materials and hybrid manufacturing approaches before scaling them commercially.
Investment in R&D remains a critical differentiator. Leading firms are allocating significant resources to develop next-generation mold materials, simulation software, and energy-efficient thermal management systems. Collaboration with automation specialists and software providers is fostering the creation of smart factory ecosystems, where predictive maintenance and adaptive process control drive both quality improvements and cost savings.
Overall, companies that align technological leadership with customer-centric service models are best positioned to navigate shifting demand patterns and regulatory landscapes. Those that combine global reach with localized expertise will continue to set the benchmark for performance, reliability, and innovation.
This comprehensive research report delivers an in-depth overview of the principal market players in the Die Casting & Forging market, evaluating their market share, strategic initiatives, and competitive positioning to illuminate the factors shaping the competitive landscape.
- Nemak, S.A.B. de C.V.
- Magna International Inc.
- Georg Fischer AG
- Tupy S.A.
- Ryobi Limited
- Signicast Investment Corp.
- Aisin Seiki Co., Ltd.
- Bharat Forge Limited
- Thyssenkrupp AG
- GKN Limited
Strategies for Driving Innovation and Sustainable Growth
Industry leaders seeking to capitalize on emerging opportunities should prioritize a holistic digital transformation strategy. Integrating the Internet of Things across production lines and leveraging advanced analytics will not only improve yield and reduce scrap but also enable data-driven decision making that aligns closely with evolving customer requirements. Embracing digital twins for process simulation can accelerate time-to-market and provide a sandbox for validating new material and mold designs before full-scale deployment.
Sustainability must be embedded into every stage of the value chain. Companies should invest in energy recovery systems, closed-loop alloy recycling, and low-emission furnaces to meet regulatory targets and enhance brand credibility. Developing life cycle assessment frameworks will help quantify environmental benefits and foster transparency with increasingly eco-conscious end users.
Cultivating strategic alliances is another critical success factor. Partnerships with technology providers, research institutions, and raw material suppliers can unlock access to specialized expertise and early-stage innovations. Likewise, collaboration with key customers through co-development agreements will ensure that product roadmaps remain aligned with long-term industry trends in electrification, lightweighting, and digital integration.
Finally, businesses must adopt an agile supply-chain model that balances local production resilience with global sourcing flexibility. By diversifying supplier networks and implementing robust risk management protocols, companies can mitigate tariff exposure, raw material shortages, and logistical disruptions, thereby securing a sustainable competitive advantage.
Ensuring Rigor Through a Multilayered Research Framework
This research is underpinned by a rigorous multi-stage methodology designed to ensure data integrity and actionable insights. The process begins with an exhaustive review of secondary sources, including industry journals, regulatory filings, company annual reports, and trade association publications. This foundational work establishes a comprehensive view of market structures, technological trends, and competitive landscapes.
Primary research follows, employing structured interviews with C-level executives, plant managers, and engineering experts across die casting and forging operations. These conversations validate secondary findings, uncover emerging opportunities, and gauge sentiment around regulatory impacts and investment priorities. Workflow site visits and process audits provide an on-the-ground perspective of operational realities and best practices.
Quantitative analysis is conducted using proprietary databases that track production volumes, material flows, and pricing benchmarks across key regions. Statistical modeling techniques are applied to identify correlation between macroeconomic indicators, policy shifts, and market performance. Sensitivity analyses further test scenario outcomes, helping to pinpoint catalysts and bottlenecks within the value chain.
Finally, all insights are synthesized through a cross-functional validation workshop involving industry veterans, academic researchers, and supply-chain specialists. This collaborative approach ensures that the final recommendations are robust, forward-looking, and closely aligned with the strategic objectives of manufacturing stakeholders.
Explore AI-driven insights for the Die Casting & Forging market with ResearchAI on our online platform, providing deeper, data-backed market analysis.
Ask ResearchAI anything
World's First Innovative Al for Market Research
Charting a Path to Leadership Amid Industry Disruption
As the die casting and forging industry navigates a period of rapid change, the ability to respond to technological, regulatory, and market dynamics will determine the leaders of tomorrow. The integration of digital technologies and sustainable practices offers a clear pathway to improved efficiency and reduced environmental footprint. Meanwhile, evolving trade policies underscore the importance of strategic supply-chain management and market diversification.
Segment-level insights reveal that players focused on lightweight materials and high-precision processes are well placed to capture growth across aerospace, automotive, and electronics applications. Regionally, North America’s established manufacturing base, EMEA’s regulatory incentives, and Asia-Pacific’s production scale each present distinct opportunities and competitive challenges. Successful companies will balance global capabilities with local market intelligence.
Ultimately, industry participants must embrace an agile mindset, pivoting quickly to incorporate emerging materials, hybrid processes, and digital solutions. Collaboration across the ecosystem-partnering with technology innovators, raw material suppliers, and key customers-will be essential to sustaining a competitive edge. By harnessing the insights and strategies outlined in this executive summary, manufacturing leaders can confidently steer their organizations toward long-term growth and resilience.
This section provides a structured overview of the report, outlining key chapters and topics covered for easy reference in our Die Casting & Forging market comprehensive research report.
- Preface
- Research Methodology
- Executive Summary
- Market Overview
- Market Dynamics
- Market Insights
- Cumulative Impact of United States Tariffs 2025
- Die Casting & Forging Market, by Process
- Die Casting & Forging Market, by Material Type
- Die Casting & Forging Market, by End Use Industry
- Die Casting & Forging Market, by Product Type
- Die Casting & Forging Market, by Sales Channel
- Americas Die Casting & Forging Market
- Europe, Middle East & Africa Die Casting & Forging Market
- Asia-Pacific Die Casting & Forging Market
- Competitive Landscape
- ResearchAI
- ResearchStatistics
- ResearchContacts
- ResearchArticles
- Appendix
- List of Figures [Total: 26]
- List of Tables [Total: 333 ]
Engage with Our Expert to Access the Full Die Casting and Forging Market Report
Ready to transform your strategic approach to die casting and forging markets? Connect with Ketan Rohom, Associate Director, Sales & Marketing at 360iResearch, to secure your copy of our comprehensive market research report. His expertise will guide you to the insights you need to outpace competitors and drive growth. Reach out today to unlock unparalleled market intelligence and propel your business forward
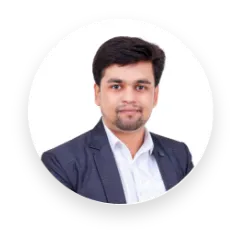
- How big is the Die Casting & Forging Market?
- What is the Die Casting & Forging Market growth?
- When do I get the report?
- In what format does this report get delivered to me?
- How long has 360iResearch been around?
- What if I have a question about your reports?
- Can I share this report with my team?
- Can I use your research in my presentation?