The Diesel Engine Remanufacturing Market size was estimated at USD 37.79 billion in 2024 and expected to reach USD 40.76 billion in 2025, at a CAGR 7.98% to reach USD 59.92 billion by 2030.

An incisive overview of the fundamental drivers, technological advancements, and strategic imperatives transforming the diesel engine remanufacturing landscape
The diesel engine remanufacturing sector represents a pivotal intersection of industrial efficiency, environmental stewardship, and cost optimization. At its core, remanufacturing breathes new life into worn engine assets by restoring critical components to original-equipment performance standards. This process has gained momentum as fleet operators, OEMs, and maintenance providers strive for sustainable practices while mitigating the economic burdens of new engine procurement.
In recent years, regulatory pressures aimed at reducing carbon footprints have elevated remanufacturing from a niche maintenance function to a strategic imperative. Stricter emissions regulations have incentivized the refurbishment of heavy machinery and commercial vehicles, driving demand across diverse applications. Concurrently, technological advancements in nondestructive testing, precision machining, and additive manufacturing have enhanced the viability of remanufactured components, ensuring reliability and compliance with rigorous performance benchmarks.
As supply chain resilience becomes a corporate focal point, remanufacturing offers a buffer against component shortages and price volatility. Companies are increasingly integrating reman operations within their broader service offerings, reflecting a shift toward circular economy models. Consequently, industry stakeholders view reman as both a cost-effective alternative to new production and a lever for achieving sustainability targets. This introduction frames subsequent discussions on transformative market shifts, policy impacts, segmentation insights, and strategic recommendations.
Exploring the disruptive forces, emerging technologies, and market dynamics that are catalyzing transformative shifts within diesel engine remanufacturing
The diesel engine remanufacturing landscape is undergoing transformative shifts driven by an interplay of disruptive forces and emerging technologies. Electrification trends and the transition toward lower-emission powertrains are compelling remanufacturers to innovate, integrating digital solutions that optimize lifespan and performance of legacy diesel assets. Predictive diagnostics powered by machine learning algorithms now enable proactive maintenance, reducing unplanned downtime and extending component life cycles.
Furthermore, the convergence of Internet of Things sensors and digital twin technologies has created a closed-loop feedback system for continuous improvement. Real-time monitoring during acceptance testing and post-reassembly performance validation provides granular data on wear patterns, guiding iterative process enhancements. Simultaneously, advances in laser cleaning and ultrasonic-assisted disassembly have streamlined cleaning and inspection stages, lowering turnaround times and improving quality control.
In addition, growing emphasis on circular economy principles is reshaping business models, with remanufacturers adopting service-based contracts and performance guarantees. Strategic partnerships among OEMs, aftermarket specialists, and logistics providers are consolidating reverse supply chains, ensuring efficient collection and redistribution of core engine components. As a result, companies are redefining competitive boundaries, moving from transactional refurbishments to integrated asset management services that promise greater value to end users.
Assessing the compounding effects of recent United States tariff measures on supply chains, cost structures, and competitiveness in diesel engine remanufacturing
Since early 2025, the cumulative implementation of United States tariff measures has exerted significant pressure on diesel engine remanufacturing supply chains and cost structures. Building on the long-standing Section 232 tariffs that impose levies on imported steel and aluminum, new Section 301 actions have targeted specific engine components such as iron castings, steel forgings, and precision-machined parts. These measures have introduced additional duties in the 10 to 15 percent range, compounding existing import costs.
Consequently, remanufacturers have faced escalating procurement expenses for critical components like crankshafts and cylinder heads, prompting a reevaluation of sourcing strategies. Many have sought to mitigate these cost increases by nearshoring fabrication operations and renegotiating contracts with domestic foundries. However, the transition to localized suppliers has required substantial investment in capacity expansion and quality certification, which has, in turn, influenced production lead times.
Moreover, the tariff-induced cost burdens have accelerated vertical integration initiatives among leading remanufacturers. By expanding in-house capabilities for reworking and precision machining, companies aim to internalize value-added processes and insulate themselves from external tariff fluctuations. In parallel, some service providers are passing incremental costs onto end users through adjusted pricing models, shifting part of the financial impact downstream. Overall, the compounded effect of 2025 tariff measures has driven a strategic realignment of supply networks, cost management practices, and product portfolio decisions.
Unveiling critical segmentation perspectives across engine types, remanufacturing processes, key components, and end-use applications that drive market dynamics
In examining segmentation perspectives, engine type distinctions reveal divergent maintenance needs and reman strategies. Heavy-duty engines, prevalent in commercial trucking and large-scale industrial applications, drive the highest volume of reman activities due to their intensive service cycles. Light-duty engines, often found in delivery fleets and regional transport, are increasingly targeted for reman as operators seek lower total cost of ownership. Medium-duty engines occupy an intermediary position, balancing duty cycles with cost-effective refurbishment opportunities.
Process-oriented segmentation underscores the critical stages that create value in reman operations. Acceptance testing sets the quality baseline, ensuring cores meet performance criteria before moving into disassembly and cleaning. The investigation phase leverages advanced diagnostic tools to pinpoint fatigue and wear, guiding targeted restoration. Subsequent reassembly reintroduces precision-engineered components, and reworking applies proprietary finishing techniques to enhance durability and efficiency. Together, these stages form a cohesive workflow that underpins consistent engine restoration outcomes.
Component-based segmentation highlights the diverse parts that underpin reman activities. Crankshafts represent a high-value focus area, with remanufacturing processes that require exceptional machining accuracy. Cylinder heads and turbochargers follow, as thermal stress and wear drive frequent refurbishment cycles. Exhaust systems and pistons also command attention due to corrosion and high-temperature exposure. Flywheels, while less frequent, necessitate stringent balance and structural integrity checks.
Application segmentation captures end-use demands across various sectors. Agricultural machinery operators prioritize cost-effective upkeep to minimize downtime during planting seasons. Construction equipment managers focus on reliability under harsh operating conditions. Marine vessels depend on reman solutions to sustain long-haul operations, and mining equipment demands robust restoration to handle abrasive environments. Power generation facilities value precision reman services that guarantee consistent output and minimize unplanned outages.
This comprehensive research report categorizes the Diesel Engine Remanufacturing market into clearly defined segments, providing a detailed analysis of emerging trends and precise revenue forecasts to support strategic decision-making.
- Engine Type
- Remanufacturing Process
- Component
- Application
Mapping divergent regional trends, regulatory landscapes, and growth drivers across the Americas, Europe Middle East & Africa, and Asia-Pacific markets
Regional dynamics play a pivotal role in shaping diesel engine remanufacturing strategies. In the Americas, infrastructure investments and regulatory support for sustainability initiatives have fostered growth in reman operations. Fleet operators across North America leverage domestic reman facilities to mitigate the impact of recent tariffs, while in South America, expanding agricultural and mining activities drive steady demand for component restoration.
Conversely, Europe, the Middle East & Africa exhibit a complex regulatory tapestry. Stringent emissions standards in the European Union have elevated reman adoption rates, with operators extending engine life to comply with environmental mandates. In the Middle East, investment in oil and gas infrastructure continues to underpin demand for heavy-duty reman services, while in Africa, nascent reman ecosystems are emerging as local governments prioritize cost-effective maintenance solutions for essential equipment.
In Asia-Pacific, diverse economic conditions and government incentives influence reman trajectories. China’s industrial modernization programs have spurred investment in advanced reman technology and reverse logistics networks. India’s focus on rural infrastructure and mechanization has boosted reman requirements for agricultural engines, whereas Southeast Asian shipping hubs prioritize marine engine refurbishments. Across the region, partnerships between local service providers and global OEMs are strengthening supply chains and introducing best practices in quality assurance and process efficiency.
This comprehensive research report examines key regions that drive the evolution of the Diesel Engine Remanufacturing market, offering deep insights into regional trends, growth factors, and industry developments that are influencing market performance.
- Americas
- Europe, Middle East & Africa
- Asia-Pacific
Highlighting leading corporate strategies, innovation trajectories, and partnership models shaping the competitive landscape in diesel engine remanufacturing
Key players in the diesel engine remanufacturing space are deploying differentiated strategies to secure competitive advantage. Leading OEM-affiliated remanufacturers are deepening vertical integration, combining core collection services with in-house machining and testing capacities to streamline workflows and reduce dependency on third-party suppliers. They are also expanding digital platforms for core tracking and performance monitoring, enhancing transparency and customer engagement.
Independent reman specialists are focusing on niche capabilities, such as advanced coating applications and high-precision balancing, to cater to premium segments that demand extended component lifespans. These companies often form strategic partnerships with technology providers to incorporate additive manufacturing techniques in reworking complex geometries. Moreover, several mid-sized firms are leveraging joint ventures with foundries and logistics operators to bolster reverse supply chains and improve turnaround times in key markets.
Mergers and acquisitions activity has reshaped the competitive landscape, with larger entities acquiring specialized workshops to augment service portfolios. Concurrently, emerging players are entering the market by offering subscription-based reman solutions, aligning service fees with uptime guarantees. Across the board, successful companies are those that blend operational excellence with innovative business models, ensuring both performance quality and cost efficiency in their offerings.
This comprehensive research report delivers an in-depth overview of the principal market players in the Diesel Engine Remanufacturing market, evaluating their market share, strategic initiatives, and competitive positioning to illuminate the factors shaping the competitive landscape.
- AER Manufacturing, LP
- ATK Engines
- Autocraft Solutions Group Limited
- Bells Engines
- Capital Reman Exchange
- Caterpillar Inc.
- CRD Centro Rotazione Diesel S.r.l.
- Cummins Inc.
- Deere & Company
- Detroit by Daimler Truck North America LLC
- DEUTZ AG
- DFC Diesel
- DieselWorks
- Hindle Group Ltd
- JASPER Engines & Transmissions
- LKQ Corporation
- Marinediesel Sweden AB
- mtu by Rolls-Royce plc
- Perkins Engines Company Limited
- Reviva Inc.
- Springfield ReManufacturing Corp.
- TVH Parts Holding NV
Delivering strategic recommendations for industry leaders to enhance operational efficiency, capitalize on market shifts, and drive sustainable growth
Industry leaders should prioritize investments in digital testing and predictive maintenance platforms to enhance process visibility and reduce unexpected failures. By integrating advanced analytics into acceptance testing and investigation phases, operators can identify wear patterns earlier, optimize repair cycles, and extend core lifespans.
Simultaneously, companies must diversify their supplier networks to mitigate tariff exposures and ensure continuity of critical components. Establishing strategic alliances with domestic foundries and machining vendors can unlock nearshoring opportunities and stabilize procurement costs. Furthermore, expanding in-house reworking capabilities will allow firms to internalize value-added processes and maintain pricing flexibility in volatile market conditions.
To capitalize on segmentation insights, remanufacturers should tailor service packages for high-demand engine types and applications. For instance, offering retrofit kits for light-duty engines in urban delivery fleets can meet the growing demand for sustainable transport solutions. Similarly, developing turnkey restoration services for agricultural machinery during off-peak seasons can solidify customer retention and balance facility utilization.
Finally, embracing circular economy principles through performance-based contracts will differentiate service offerings. Industry leaders must collaborate with OEMs and end users to structure outcome-driven agreements, linking service fees to uptime or fuel efficiency improvements. Such models foster long-term partnerships and position remanufacturing as an integral component of asset management strategies.
Detailing the rigorous research methodologies, data sources, and analytical frameworks that underpin comprehensive diesel engine remanufacturing market insights
This report’s findings are grounded in a rigorous, multi-phased research methodology encompassing both qualitative and quantitative approaches. Initially, primary interviews with industry executives, technical experts, and end users provided deep insights into operational challenges and innovation priorities. These interviews were complemented by consultations with regulatory bodies and trade associations to understand evolving policy impacts.
Secondary research included an extensive review of technical papers, patent filings, and publicly available financial disclosures to map technology adoption trends and investment flows. Supply chain data was analyzed through trade databases and customs records to chart tariff exposures and component sourcing patterns. Additionally, process benchmarking studies were conducted at remanufacturing facilities to validate cycle times, quality control measures, and cost structures.
Analytical frameworks such as SWOT and Porter’s Five Forces were applied to assess competitive dynamics, while segmentation analyses leveraged custom-built models to evaluate demand drivers across engine types, processes, components, and applications. Regional market assessments drew on economic indicators, infrastructure expenditure profiles, and environmental regulations to contextualize growth trajectories. The research team employed triangulation methods to cross-verify data points and ensure the robustness of insights presented herein.
Explore AI-driven insights for the Diesel Engine Remanufacturing market with ResearchAI on our online platform, providing deeper, data-backed market analysis.
Ask ResearchAI anything
World's First Innovative Al for Market Research
Synthesizing the key findings and strategic takeaways to inform decision-making and future planning in the evolving diesel engine remanufacturing environment
The convergence of environmental imperatives, technological innovations, and trade policy dynamics is redefining the diesel engine remanufacturing landscape. Stakeholders must navigate a complex interplay of regulatory pressures, cost inputs, and evolving customer expectations. By understanding the compounded effects of tariff measures and embracing digital transformation, organizations can enhance process efficiencies and secure resilient supply chains.
Strategic segmentation insights reveal that operators should align service portfolios with high-value engine types and applications, while component-specific capabilities can unlock additional revenue streams. Regional nuances underscore the importance of localized strategies tailored to distinct regulatory frameworks and infrastructure development priorities. In parallel, competitive analysis highlights the necessity for integrated business models that blend vertical integration, partnerships, and innovative service offerings.
Looking ahead, companies that adopt performance-based contracts and circular economy principles will differentiate themselves by delivering measurable value to customers. Whether through predictive maintenance platforms or advanced reworking techniques, the ability to guarantee uptime and efficiency will become increasingly central to competitive positioning. These strategic imperatives, grounded in thorough research, equip decision-makers with the insights needed to thrive in this dynamic market environment.
This section provides a structured overview of the report, outlining key chapters and topics covered for easy reference in our Diesel Engine Remanufacturing market comprehensive research report.
- Preface
- Research Methodology
- Executive Summary
- Market Overview
- Market Dynamics
- Market Insights
- Cumulative Impact of United States Tariffs 2025
- Diesel Engine Remanufacturing Market, by Engine Type
- Diesel Engine Remanufacturing Market, by Remanufacturing Process
- Diesel Engine Remanufacturing Market, by Component
- Diesel Engine Remanufacturing Market, by Application
- Americas Diesel Engine Remanufacturing Market
- Europe, Middle East & Africa Diesel Engine Remanufacturing Market
- Asia-Pacific Diesel Engine Remanufacturing Market
- Competitive Landscape
- ResearchAI
- ResearchStatistics
- ResearchContacts
- ResearchArticles
- Appendix
- List of Figures [Total: 26]
- List of Tables [Total: 392 ]
Contact Associate Director Ketan Rohom to unlock diesel engine remanufacturing insights and secure your strategic advantage with our comprehensive report
To discover how these in-depth analyses can inform your next strategic move, reach out to Associate Director Ketan Rohom. His expertise in translating comprehensive market intelligence into actionable strategies will empower your organization to optimize operations, navigate tariff complexities, and harness emerging technologies in diesel engine remanufacturing. Engage today to secure early access to the full report and position your business at the forefront of industry innovation.
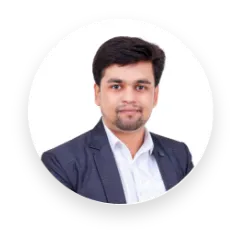
- How big is the Diesel Engine Remanufacturing Market?
- What is the Diesel Engine Remanufacturing Market growth?
- When do I get the report?
- In what format does this report get delivered to me?
- How long has 360iResearch been around?
- What if I have a question about your reports?
- Can I share this report with my team?
- Can I use your research in my presentation?