Unveiling the New Era of Direct Aluminum Extrusion Press Innovation
The direct aluminum extrusion press sector stands at a pivotal juncture, driven by accelerating technological innovation and shifting end-use demands. As manufacturers strive to achieve greater precision, higher throughput and enhanced energy efficiency, extrusion press capabilities have evolved far beyond their traditional roots. Today’s presses combine robust mechanical frameworks with adaptive drive systems to accommodate the broadest range of applications, from lightweight aerospace components to heavy-duty construction profiles. This dynamic transformation reflects a broader industrial agenda in which sustainable production practices and digital integration are no longer optional but essential.
Against this backdrop, decision-makers face a complex intersection of market forces. Raw material price volatility, regulatory changes and regional infrastructure initiatives each exert pressure on production costs and capital expenditure plans. Meanwhile, evolving design specifications in consumer electronics and the automotive aftermarket demand unprecedented flexibility in extrusion profiles and alloy processing. Navigating this landscape requires not only an understanding of current capabilities but also a forward-looking view of emerging material science breakthroughs and process automation trends.
By examining the state of press technology, supply chain dynamics and downstream application requirements, this summary equips stakeholders with the clarity needed to align investments with growth opportunities. Through a balanced analysis of operational imperatives and market catalysts, readers will gain a comprehensive orientation to the factors shaping present conditions and the forces likely to define the next wave of industry advancement.
Identifying Transformative Shifts Reshaping the Industry
In recent years, the direct aluminum extrusion industry has undergone transformative shifts that have redefined competitive benchmarks and investment priorities. Process automation, once confined to peripheral functions such as billet handling and temperature control, has moved to the core of press operations. Advanced control systems now orchestrate real-time adjustments to ram speed, die lubrication and extrusion temperature, ensuring consistent output quality even under high-volume demands. Simultaneously, the integration of Industry 4.0 sensors across press lines provides unprecedented visibility into machine health, enabling predictive maintenance strategies that minimize unplanned downtime and optimize asset utilization.
Another significant shift has emerged in the realm of material alloys. The pursuit of lighter, stronger and more corrosion-resistant profiles has accelerated research into novel aluminum formulations and composite blends. These new alloys often require precise extrusion parameters, driving equipment manufacturers to refine press frame rigidity and customize drive torque profiles. Suppliers who can deliver modular press platforms that accommodate rapid die changes and variable load conditions are gaining a distinct competitive edge.
Lastly, sustainability mandates and carbon reduction targets are reshaping capital allocation decisions. Energy-efficient press drives and heat recovery systems have transitioned from niche offerings to core performance metrics. Producers who strategically invest in hybrid drive configurations-merging hydraulic power with electric amplification-are realizing both energy savings and enhanced operational agility. Taken together, these shifts signal a market that increasingly values digital intelligence, material versatility and environmental stewardship above mere production scale.
Assessing the Cumulative Impact of US Tariffs in 2025
The imposition of new tariffs by the United States in 2025 has introduced a layer of complexity to global trade flows and supply chain configurations across the direct extrusion press sector. Manufacturers that previously relied on lower-cost billet imports from traditional exporters have been compelled to reevaluate sourcing strategies. Some have accelerated partnerships with domestic smelters to reduce exposure to variable duty rates, while others have diversified supply lines into alternative regions that benefit from preferential trade agreements or more favorable logistical channels.
At the same time, the tariff environment has prompted capital expenditure reappraisals for export-oriented press builders. Companies that once eyed the U.S. market as a growth engine are now weighing the incremental cost burden against local assembly or licensing arrangements. In certain cases, collaborative manufacturing hubs have emerged as a mitigation strategy, allowing international press OEMs to maintain market access without incurring steep tariff penalties on finished equipment.
Perhaps most notably, end-use industries have begun internalizing the downstream effects of these duties. Automotive and defense integrators that depend on precision-extruded components are exploring nearshoring options and vertical integration models to shield themselves from input-cost volatility. This trend underscores a broader strategic realignment in which tariff-driven cost pressures accelerate the adoption of localized manufacturing ecosystems and reinforce the importance of flexible press technologies that can adapt to shifting production footprints.
Deep-Dive into Multi-Dimensional Market Segmentation
A nuanced understanding of the direct aluminum extrusion press market emerges only when one considers the interplay of multiple segmentation dimensions. Based on end-use industry, the landscape spans from the high-tolerance demands of aerospace and defense-where commercial aviation and military aerospace components coexist-to the rigorous performance requirements of the automotive sector, balancing original equipment manufacturer supply chains with aftermarket customization needs. Within construction, the press market supports a broad spectrum of commercial, infrastructure and residential projects, each dictating specific profile geometries and surface finishes. Meanwhile, the electrical and electronics segment encompasses consumer gadgets, energy distribution systems and telecom hardware, each relying on uniquely engineered profiles and die configurations.
Press type segmentation further refines competitive positioning. Single-stage machines offer streamlined operations for standardized profiles, while multi-stage presses and tandem configurations deliver compound extrusion sequences that reduce secondary processing steps. Press capacity delineates operational boundaries, from compact systems up to 500 tonnes suited for niche applications, through mid-range solutions in the 500–1000 tonne class for balanced throughput, to robust platforms in the 1000–1500 tonne bracket and above 1500 tonnes designed for heavy-duty output. Drive technologies add another layer of differentiation: hydraulic systems continue to dominate general-purpose applications, mechanical drives excel in high-speed extrusion, and hybrid architectures blend the strengths of both to achieve energy efficiency without sacrificing performance. Finally, product type segmentation-spanning bars and rods, foils, pipes and tubes, as well as complex profiles-illustrates the breadth of downstream applications and the corresponding demands placed on press design and die technology.
This comprehensive research report categorizes the Direct Aluminum Extrusion Press market into clearly defined segments, providing a detailed analysis of emerging trends and precise revenue forecasts to support strategic decision-making.
- End-Use Industry
- Press Type
- Press Capacity
- Drive Type
- Product Type
Critical Regional Dynamics Shaping Market Growth
Geographic dynamics play a pivotal role in shaping demand patterns and investment priorities. In the Americas, a combination of automotive production hubs and defense modernization programs underpins steady requirements for direct extrusion capacity, spurring upgrades to existing lines and greenfield facility expansions. Europe, the Middle East and Africa exhibit a heterogeneous mix of mature markets with stringent regulatory frameworks alongside emerging economies focused on infrastructure growth, which together drive diversified product portfolios and service models. Across the Asia-Pacific region, rapid urbanization and the proliferation of consumer electronics manufacturing have created a surge in demand for lightweight yet high-performance profiles, motivating both local press builders and global OEMs to enhance their regional footprints and tailor offerings to specific market segments.
These regional developments are interlinked through global supply chains, yet each territory reflects unique macroeconomic drivers. Infrastructure spending priorities, regulatory landscapes and energy costs all inform procurement strategies for extrusion equipment, compelling strategic agility from manufacturers seeking to serve multiple geographies with differentiated service and support capabilities.
This comprehensive research report examines key regions that drive the evolution of the Direct Aluminum Extrusion Press market, offering deep insights into regional trends, growth factors, and industry developments that are influencing market performance.
- Americas
- Europe, Middle East & Africa
- Asia-Pacific
Leading Players Driving Competitive Innovation
Leading equipment suppliers are leveraging distinct competitive advantages to capture market share and set performance benchmarks. Established European press manufacturers have built reputations for engineering excellence and customized automation solutions that cater to complex alloy formulations. Japanese and South Korean companies, known for precision manufacturing and advanced drive systems, have focused on high-speed extrusion applications and integration with robotic material handling. In North America, cohesive service networks and localized production facilities enable rapid response to aftermarket demands and ongoing maintenance requirements.
Strategic partnerships and joint ventures have also emerged as pivotal growth levers. Collaborations between technology providers and materials scientists are driving breakthroughs in die design and alloy development, while alliances with digital platform vendors are enabling real-time monitoring and data analytics services. At the same time, smaller niche players are carving out specialized positions by offering modular press upgrades and retrofit packages that extend the life cycle of aging equipment. These diverse competitive approaches underscore a market where differentiation stems not only from capital equipment performance but also from service excellence, intellectual property portfolios and the ability to co-innovate with end-users.
This comprehensive research report delivers an in-depth overview of the principal market players in the Direct Aluminum Extrusion Press market, evaluating their market share, strategic initiatives, and competitive positioning to illuminate the factors shaping the competitive landscape.
- SMS group GmbH
- UBE Machinery Corporation, Ltd.
- Achenbach Buschhütten GmbH & Co. KG
- Bühler Vertech GmbH
- Comet Group S.p.A.
- Danieli & C. Officine Meccaniche S.p.A.
- Bausano & Figli S.p.A.
- Tecno Press S.r.l.
- Mitsubishi Heavy Industries, Ltd.
- Sany Heavy Industry Co., Ltd.
Strategic Imperatives for Industry Leaders to Capitalize on Market Shifts
To thrive amid evolving market conditions, industry leaders must adopt a multi-pronged strategic approach. First, investing in adaptive automation and predictive maintenance capabilities will not only optimize throughput but also reduce unplanned downtime, translating into immediate cost savings. Simultaneously, companies should pursue alloy and material partnerships to co-develop extrusion solutions tailored to emerging application needs, such as electric vehicle battery frames or lightweight architectural elements.
Second, supply chain resilience can be enhanced by establishing dual-sourcing strategies for billets and forging alliances with regional smelters. This diversification diminishes exposure to tariff fluctuations and logistics disruptions. Third, expanding service offerings through digital platforms-such as remote diagnostics and lifecycle analytics-creates new revenue streams and strengthens customer retention. In parallel, exploring joint manufacturing ventures or licensing arrangements in key markets can mitigate tariff barriers and accelerate market entry.
Finally, adopting a customer-centric development process, which integrates feedback loops from end-use operators into design iterations, will ensure new press platforms deliver measurable efficiency gains. By aligning R&D investments with end-market insights and regulatory requirements, organizations can anticipate demand shifts and position themselves as trusted innovation partners rather than mere equipment suppliers.
Rigorous Research Methodology Underpinning Our Analysis
Our analysis draws upon a robust research methodology that combines primary interviews with senior executives, engineers and procurement leaders across the extrusion ecosystem, with extensive secondary research from industry journals, regulatory filings and technical white papers. Data triangulation ensures the reconciliation of disparate data sources, while quality assurance protocols validate all quantitative inputs against publicly available financial reports and trade statistics.
A structured segmentation framework underpins the assessment of end-use verticals, equipment typologies, drive configurations and geographic zones. Competitive benchmarking leverages a proprietary database of press OEM product specifications and aftermarket performance metrics. All findings undergo multiple rounds of expert review to confirm relevance and accuracy, with iterative drafts refined based on direct feedback from domain specialists. This rigorous process guarantees that the insights presented here reflect both macroeconomic trends and on-the-ground realities within manufacturing facilities worldwide.
Explore AI-driven insights for the Direct Aluminum Extrusion Press market with ResearchAI on our online platform, providing deeper, data-backed market analysis.
Ask ResearchAI anything
World's First Innovative Al for Market Research
Concluding Insights on the Future of Direct Aluminum Extrusion Press
The confluence of technological innovation, trade policy shifts and regional demand variations has created an environment of both opportunity and complexity in the direct aluminum extrusion press market. Organizations that proactively embrace digital automation, strategic supply chain partnerships and customer-driven R&D will emerge as industry leaders, while those that remain static risk falling behind faster-moving competitors. A nuanced segmentation approach reveals the importance of tailoring product offerings to the unique performance requirements of aerospace, automotive, construction and electronics applications. Geographic insights highlight the need for localized support and market-specific strategies, especially as tariff regimes and infrastructure investments evolve.
Ultimately, the capacity to integrate new materials, optimize energy consumption and deliver predictive service models will define the next generation of competitive advantage. As this landscape continues to transform, companies that marry engineering excellence with strategic foresight will be best positioned to capture growth and drive sustainable value across the extrusion press ecosystem.
This section provides a structured overview of the report, outlining key chapters and topics covered for easy reference in our Direct Aluminum Extrusion Press market comprehensive research report.
- Preface
- Research Methodology
- Executive Summary
- Market Overview
- Market Dynamics
- Market Insights
- Cumulative Impact of United States Tariffs 2025
- Direct Aluminum Extrusion Press Market, by End-Use Industry
- Direct Aluminum Extrusion Press Market, by Press Type
- Direct Aluminum Extrusion Press Market, by Press Capacity
- Direct Aluminum Extrusion Press Market, by Drive Type
- Direct Aluminum Extrusion Press Market, by Product Type
- Americas Direct Aluminum Extrusion Press Market
- Europe, Middle East & Africa Direct Aluminum Extrusion Press Market
- Asia-Pacific Direct Aluminum Extrusion Press Market
- Competitive Landscape
- ResearchAI
- ResearchStatistics
- ResearchContacts
- ResearchArticles
- Appendix
- List of Figures [Total: 26]
- List of Tables [Total: 417 ]
Engage Expert Guidance to Drive Strategic Market Decisions
To unlock the full potential of the direct aluminum extrusion press market and gain unparalleled strategic insights, reach out to Ketan Rohom, Associate Director of Sales & Marketing at 360iResearch. His deep industry knowledge and consultative approach will guide you through the findings and help you align the report’s insights with your organization’s goals. Don’t miss the opportunity to equip your team with data-driven recommendations and competitive benchmarks. Secure your access today to drive innovation, optimize operations, and stay ahead in a rapidly evolving landscape.
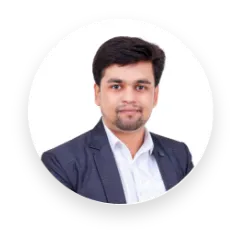
- When do I get the report?
- In what format does this report get delivered to me?
- How long has 360iResearch been around?
- What if I have a question about your reports?
- Can I share this report with my team?
- Can I use your research in my presentation?