Introduction to Double Flap Airlock Valves and Their Industrial Importance
Airlock valves play a pivotal role in maintaining airtight seals between pressurized and non-pressurized systems, ensuring reliable material transfer while preventing contamination and energy loss. Among these, the double flap airlock valve stands out for its dual-seal mechanism, which enhances performance in challenging environments such as pneumatic conveying, dust collection, and bulk material handling systems. This introduction frames the significance of double flap configurations: their ability to accommodate abrasive powders, granular solids, and hygroscopic compounds with minimal wear and optimal throughput.
Throughout this summary, we will explore how ongoing technological innovations, regulatory pressures, and shifting trade policies have reshaped the competitive dynamics of the valve industry. By examining the mechanical advantages of dual-door systems, their material compatibility, and the critical industries that rely on them, readers will gain a comprehensive understanding of why this valve segment commands growing attention from engineering teams and procurement specialists alike. Our analysis balances technical depth with strategic perspective, setting the stage for an informed discussion on developments that drive both short-term decisions and long-term planning.
Transformative Shifts in Technology, Materials, and Sustainability
Industrial processes are experiencing a profound transformation driven by digital integration, sustainability mandates, and demand for operational agility. Pioneering manufacturers have begun embedding sensors into airlock valves to enable real-time monitoring of cycle times, material flow, and seal integrity. This predictive approach not only reduces unplanned downtime but also optimizes maintenance schedules, unlocking significant cost savings over a valve’s service life.
Simultaneously, material science breakthroughs-particularly in polymer-composite alloys-are redefining the performance envelope of sealing components. These advanced composites resist corrosion and abrasion far better than traditional metals, expanding applicability in corrosive chemical processing environments and high-temperature energy production systems. Coupled with enhanced computational design tools, valve developers can now rapidly prototype custom double flap assemblies that precisely meet the needs of niche applications.
Finally, sustainability concerns have elevated energy efficiency and dust containment to boardroom priorities. Stricter emissions regulations in many regions compel end users to adopt valves with minimized leakage rates and low power consumption. Consequently, double flap architectures are gaining traction as they offer superior sealing performance compared to single-door counterparts, underscoring a clear shift toward environmentally conscious engineering solutions.
Cumulative Impact of U.S. Tariffs on Materials and Supply Chains
The implementation of new U.S. tariff schedules in 2025 has introduced considerable complexity into the procurement of raw materials and import components essential to valve manufacturing. Tariffs on steel and aluminum have escalated input costs, prompting original equipment manufacturers to reassess their material strategies. In response, some producers have intensified research into stainless steel grades that offer equivalent mechanical properties at reduced duty exposure, while others are experimenting with polymer-composite substitutes to mitigate cost pressures.
Beyond material selection, supply chain structures are undergoing strategic realignment. Companies that once relied heavily on overseas foundries for castings and machined parts are now diversifying their sourcing networks, incorporating regional suppliers in North America to avoid punitive duties. This reshoring trend not only safeguards against future tariff volatility but also shortens lead times, enhancing responsiveness to urgent maintenance requests and custom project requirements.
Nevertheless, the tariff landscape has also created margin challenges for small-to-medium valve fabricators, which may lack the negotiating leverage of larger multinationals. These pressures increase consolidation risk within the industry, as smaller players explore joint ventures or acquisition by global mechanical technology providers to remain competitive in a tariff-strained environment.
Key Segmentation Insights Across Types, Materials, Industries, and Processes
When evaluating valve performance across different architectures, it becomes clear that double flap mechanisms offer enhanced sealing compared to gravity discharge designs, ensuring consistent material isolation in pressure-sensitive operations. Conversely, split flap models provide space-saving benefits and simpler maintenance, appealing to compact conveying installations. These functional distinctions guide engineering teams toward the most suitable configuration for their process requirements.
Material composition also critically influences valve longevity and maintenance cycles. Aluminum variants deliver weight savings and corrosion resistance for food processing lines, whereas carbon steel assemblies excel under abrasive bulk handling conditions. Meanwhile, polymer-composite alloys have emerged as a hybrid solution, marrying chemical inertness with reduced wear rates-attributes highly sought in pharmaceutical manufacturing. Stainless steel remains the go-to choice for hygienic applications, thanks to its cleanability and compliance with stringent industry standards.
Industry use cases further diversify demand. Chemical processing plants prioritize valves that withstand corrosive catalysts and high temperatures, while energy production facilities focus on airlock seals capable of handling fly ash and biomass particles. Within food processing, hygienic design takes precedence to minimize contamination risk, even as throughput volumes surge. Pharmaceutical manufacturers demand ultra-precise dosing and minimal cross-contamination, leading to specialized sealing geometries and surface finishes.
Finally, end-use processes impose unique performance criteria. Bulk material handling demands robust doors that endure repeated cycling under heavy loads. Conveying equipment applications emphasize low leakage rates to sustain pneumatic pressure. Dust collection systems rely on tight seals to prevent particulate escape, protecting worker health and meeting regulatory standards. Understanding these nuanced requirements is essential for tailoring valve solutions to each operational context.
This comprehensive research report categorizes the Double Flap Airlock Valve market into clearly defined segments, providing a detailed analysis of emerging trends and precise revenue forecasts to support strategic decision-making.
- Valve Type
- Material Used
- Application Industry
- End-Use Processes
Key Regional Dynamics in the Airlock Valve Market
Across the Americas, high energy production and processing capacities drive strong demand for airlock valves that can handle large-scale coal, biomass, and petroleum by-products. Regional manufacturing hubs in the U.S. and Canada further bolster localized supply chains, offsetting some tariff-induced cost increases through domestic sourcing. In contrast, Europe, the Middle East, and Africa are characterized by stringent emissions regulations and a focus on renewable energy transitions, prompting rapid adoption of valves with advanced composite seals and real-time performance tracking.
Asia-Pacific markets exhibit the fastest growth trajectory in chemical and energy sectors, fueled by infrastructure expansions in Southeast Asia and industrial upgrades in China and India. These regions prioritize scalability and cost efficiency, leading engineers to specify high-throughput double flap designs with corrosion-resistant coatings. Moreover, increased investment in dust collection systems across emerging economies is elevating the importance of airlock valve reliability to maintain air quality and comply with health and safety codes.
Regardless of region, cross-border collaborations between local fabricators and multinational engineering firms are becoming more common, fostering technology transfer and standardization of best practices. Such partnerships help operators navigate regulatory complexity while benefiting from the latest valve design innovations.
This comprehensive research report examines key regions that drive the evolution of the Double Flap Airlock Valve market, offering deep insights into regional trends, growth factors, and industry developments that are influencing market performance.
- Americas
- Asia-Pacific
- Europe, Middle East & Africa
Competitive Landscape: Insights on Leading Valve Manufacturers
ABCD Valves Inc. has distinguished itself through the development of proprietary seal coatings that significantly extend the service intervals of double flap assemblies, particularly in abrasive environments. Their robust distribution network across North America and Europe ensures rapid delivery and field support. Evolve.MechTech LLC has carved a niche by integrating IoT sensors directly into valve housings, enabling customers to harness data analytics for predictive maintenance and process optimization.
Global Dynamics Corporation offers a vertically integrated solution, combining in-house foundry capabilities with precision machining and assembly. This end-to-end approach reduces lead times and allows for seamless quality control. Precision Flow Systems Ltd. has built its reputation on bespoke configurations, collaborating closely with pharmaceutical and food processing clients to meet the most exacting sanitary requirements and regulatory standards.
Together, these companies exemplify the spectrum of strategic positioning-from specialized niche offerings to full-scale manufacturing platforms-illustrating how competitive differentiation in the valve industry hinges on innovation, service agility, and technical expertise.
This comprehensive research report delivers an in-depth overview of the principal market players in the Double Flap Airlock Valve market, evaluating their market share, strategic initiatives, and competitive positioning to illuminate the factors shaping the competitive landscape.
- ABCD Valves Inc.
- Evolve.MechTech LLC
- Global Dynamics Corporation
- Precision Flow Systems Ltd.
Actionable Recommendations for Industry Leaders
First, invest in sensor-enabled valve designs to transition from reactive maintenance to predictive strategies, thereby reducing downtime and avoiding emergency replacements. Simultaneously, explore advanced material blends-particularly polymer-composite alloys-to circumvent tariff limitations on metals while enhancing corrosion and wear resistance. Second, diversify sourcing networks by forging partnerships with regional foundries and distributors, mitigating the risk of single-source dependencies and shielding operations from future trade disruptions.
Third, prioritize compliance and sustainability by benchmarking valve performance against the strictest regional regulations, then standardize those specifications across global operations. This proactive stance will streamline product approvals and foster brand credibility among end users focused on emissions control and worker safety. Fourth, cultivate cross-industry collaborations, especially between energy producers and chemical processors, to exchange best practices on valve deployment and maintenance procedures.
Finally, allocate resources to workforce development, ensuring that engineers and maintenance teams possess the technical skills to install, calibrate, and troubleshoot advanced airlock systems. A well-trained staff accelerates adoption of cutting-edge valve technologies and maximizes return on investment.
Explore AI-driven insights for the Double Flap Airlock Valve market with ResearchAI on our online platform, providing deeper, data-backed market analysis.
Ask ResearchAI anything
World's First Innovative Al for Market Research
Conclusion: Integrating Innovation, Compliance, and Strategy
The evolving landscape of double flap airlock valves underscores a clear shift toward integrated, data-driven solutions that align with stringent environmental and operational demands. Technological advances in sensor instrumentation and polymer-composite materials are redefining performance benchmarks, while trade policy realignments-particularly U.S. tariffs-have catalyzed supply chain diversification and material innovation.
Segment-specific insights reveal that valve type, material composition, application industry, and end-use process each play a critical role in solution selection. Regional analysis highlights distinct priorities: the Americas emphasize domestic sourcing, EMEA mandates regulatory compliance, and Asia-Pacific pursues scale and cost efficiency. Industry leaders that adapt to these contours-by embracing digital monitoring, optimizing material use, and strengthening strategic partnerships-will secure competitive advantage.
In summary, the intersection of engineering innovation, regulatory impetus, and market dynamics offers a wealth of opportunities for organizations that can nimbly integrate new technologies with robust supply chain strategies. By following the recommendations outlined above, decision-makers can optimize performance, manage risk, and drive sustainable growth in the double flap airlock valve sector.
This section provides a structured overview of the report, outlining key chapters and topics covered for easy reference in our Double Flap Airlock Valve market comprehensive research report.
- Preface
- Research Methodology
- Executive Summary
- Market Overview
- Market Dynamics
- Market Insights
- Cumulative Impact of United States Tariffs 2025
- Double Flap Airlock Valve Market, by Valve Type
- Double Flap Airlock Valve Market, by Material Used
- Double Flap Airlock Valve Market, by Application Industry
- Double Flap Airlock Valve Market, by End-Use Processes
- Americas Double Flap Airlock Valve Market
- Asia-Pacific Double Flap Airlock Valve Market
- Europe, Middle East & Africa Double Flap Airlock Valve Market
- Competitive Landscape
- ResearchAI
- ResearchStatistics
- ResearchContacts
- ResearchArticles
- Appendix
- List of Figures [Total: 24]
- List of Tables [Total: 193 ]
Call-To-Action: Connect with Ketan Rohom to Secure Your Detailed Market Report
Ready to gain deeper insights and make informed decisions backed by rigorous research? Reach out to Ketan Rohom, Associate Director, Sales & Marketing, to acquire the full market research report on double flap airlock valves. Leverage comprehensive analysis, expert interviews, and detailed segmentation to guide your next strategic move. Contact Ketan Rohom today to ensure your organization stays at the forefront of this critical industry.
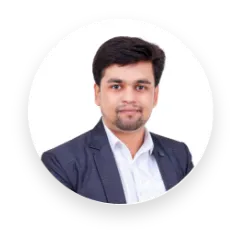
- When do I get the report?
- In what format does this report get delivered to me?
- How long has 360iResearch been around?
- What if I have a question about your reports?
- Can I share this report with my team?
- Can I use your research in my presentation?