Introduction: Elevating Precision and Productivity with Double Spindle Grinding
Double spindle grinding machines have emerged as critical assets in precision machining, delivering unparalleled accuracy and productivity for high-volume manufacturing environments. By integrating two grinding spindles that can operate simultaneously or sequentially, these systems enable faster cycle times and consistent surface finishes across diverse workpieces. Manufacturers benefit from the flexibility to handle complex geometries while minimizing changeover time, which enhances throughput and lowers per-unit costs. Furthermore, advancements in control systems and spindle stiffness have elevated the capability to maintain tight tolerances, an essential attribute in industries where micrometer-level precision is non-negotiable.
As the demand for compact and lightweight components escalates in sectors such as aerospace and automotive, double spindle grinders offer a competitive edge by accommodating high material removal rates without compromising surface integrity. Coupled with the integration of adaptive control algorithms, these machines can dynamically adjust parameters to compensate for tool wear, thermal expansion, and material inconsistencies. This not only extends the lifespan of grinding wheels but also ensures consistent part quality. Consequently, decision-makers seeking to optimize production lines and meet stringent quality benchmarks increasingly turn to double spindle grinding technology as a keystone in their manufacturing strategy.
Transitioning into the next section, we will explore the transformative shifts currently redefining the landscape of precision grinding and setting the stage for future innovations.
Transformative Shifts Shaping the Double Spindle Grinding Landscape
The landscape of double spindle grinding is undergoing transformative shifts driven by rapid technological convergence and evolving market pressures. Industry 4.0 initiatives have accelerated the adoption of IoT-enabled sensors and real-time data analytics, empowering operators to monitor spindle vibration, temperature, and wheel wear with unprecedented granularity. As a result, predictive maintenance strategies are replacing scheduled downtime, boosting equipment availability and reducing unplanned stoppages. Meanwhile, the integration of machine learning algorithms has enabled systems to learn optimal grinding parameters over time, improving consistency across batches and expediting setup procedures.
In parallel, sustainability imperatives are influencing coolant management and energy consumption in grinding operations. Innovations in cryogenic and minimum quantity lubrication systems address environmental concerns by reducing fluid usage and facilitating easier waste disposal. In addition, manufacturers are exploring hybrid grinding techniques to combine milling and grinding processes, enabling single-pass operations that reduce part handling and energy consumption. These advancements underscore a broader shift toward greener manufacturing practices without sacrificing performance.
Lastly, the rise of additive manufacturing has sparked collaboration between grinding specialists and 3D printing providers to finish complex, support-laden components. This synergy not only expands the application range of double spindle grinders but also paves the way for end-to-end digital workflows. Having outlined these transformative shifts, the focus now turns to how shifting trade policies, particularly United States tariffs in 2025, will shape the competitive environment.
Cumulative Impact of United States Tariffs in 2025 on Double Spindle Grinding
The cumulative impact of United States tariffs slated for 2025 is poised to reshape global supply chains and pricing dynamics in the double spindle grinding market. With duties targeting key components, spare parts and imported machinery, OEMs face increased procurement costs that will likely be passed on to end-users. This cost pressure compels manufacturers to reassess sourcing strategies, either by negotiating long-term supply contracts, relocating production closer to end markets, or accelerating the development of domestic supplier networks.
Moreover, tariffs have intensified the imperative for customization and local content. Companies that can adapt their machines to comply with regional standards and incorporate domestically sourced parts will gain an edge, particularly in sectors where long-term service contracts and aftermarket support underpin customer loyalty. Concurrently, the increased barrier to entry for foreign competitors may open windows of opportunity for domestic machine tool builders to capture market share by emphasizing shorter lead times and localized technical support.
At the same time, service providers specializing in retrofitting and rebuilding existing double spindle grinders stand to benefit. As capital expenditure for new equipment climbs, many end-users will prioritize extending the lifespan of current assets through upgrades, advanced control retrofits, and cycle-time enhancements. In the face of tariff-induced cost inflation, these aftermarket strategies offer a cost-effective route to maintain competitive capability. Understanding these dynamics is essential before delving into the granular segmentation that drives market opportunities.
Key Segmentation Insights Unveiling Market Dynamics
The market segmentation for double spindle grinding machines reveals nuanced dynamics that inform strategic decisions across multiple dimensions. Based on machine type, the landscape is studied across horizontal spindle and vertical spindle configurations: the horizontal spindle category further subdivides into reciprocating table and rotary table designs, while vertical spindle systems encompass fixed head and swivel head arrangements. When analyzing application industries, aerospace demands precision in landing gear systems and turbine components, whereas automotive focuses on tight tolerances for engine components and transmission parts. General manufacturing applications range from components for additive manufacturing to drilling applications and conventional metal cutting, and tool and die making zeroes in on cutting tools and mold components.
End-user segmentation distinguishes between aftermarket services, which include machinery upgrades and replacement parts, and OEMs that supply consumer electronics manufacturers and heavy machinery producers. Control type characterization separates CNC and manual operations: CNC offerings split into advanced systems with machine learning capabilities and standard variants, while manual systems cover basic manual and semi-automatic setups. Technology type differentiation highlights advanced grinding technologies such as nano grinding and precision grinding, conventional abrasive wheel technology, and hybrid methods that combine milling and grinding processes.
Material type segmentation divides the market into metals-comprising carbon steel, future categorization of alloys, and stainless steel-and non-metals like ceramics and composite materials. Functionality covers heavy-duty grinding for bulk metal removal and high-thick grinding and precision grinding featuring micro-finishing and ultra-precision applications. Finally, coolant system type segmentation addresses the environmental and performance needs of various operations, ranging from dry grinding in high-temperature contexts to wet grinding options including cryogenic applications, flood cooling and mist cooling. This comprehensive segmentation framework serves as a roadmap for pinpointing growth pockets and aligning product portfolios with evolving customer requirements.
This comprehensive research report categorizes the Double Spindle Grinding Machine market into clearly defined segments, providing a detailed analysis of emerging trends and precise revenue forecasts to support strategic decision-making.
- Machine Type
- Application Industry
- End-User
- Control Type
- Technology Type
- Material Type
- Functionality
- Coolant System Type
Key Regional Insights Driving Market Strategies
Regional analysis underscores distinct competitive landscapes and growth trajectories in the double spindle grinding sector. In the Americas, strong demand from the automotive and aerospace industries, coupled with significant investments in advanced manufacturing facilities, drives a robust market environment. Favorable trade agreements and government incentives further enhance the region’s appeal, encouraging both domestic innovation and foreign direct investment. These conditions foster collaboration among machine tool builders, technology suppliers and end-users to accelerate the deployment of Industry 4.0 initiatives.
Moving to Europe, Middle East & Africa, a mature industrial base prioritizes sustainability and energy efficiency, yielding heightened interest in eco-friendly coolant systems and electric motor optimizations. Regional regulations mandating reduced carbon footprints have prompted equipment suppliers to develop low-emission grinding solutions and closed-loop coolant recycling systems. In emerging Middle Eastern markets, infrastructure projects and defense contracts contribute to steady growth, while African regions are seeing rising demand in mining and heavy machinery sectors.
Asia-Pacific continues to dominate global production volumes, with China, Japan, South Korea and India leading in both consumption and manufacturing capabilities. Rapid urbanization and infrastructure development fuel demand, while competitive labor costs and government support for local tool makers attract international OEMs seeking cost-efficient production hubs. At the same time, increasing adoption of advanced CNC controls and automation technologies reflects a broader shift toward smart factories. Taken together, regional insights guide targeted investment and localized go-to-market strategies.
This comprehensive research report examines key regions that drive the evolution of the Double Spindle Grinding Machine market, offering deep insights into regional trends, growth factors, and industry developments that are influencing market performance.
- Americas
- Asia-Pacific
- Europe, Middle East & Africa
Key Companies Insights and Competitive Landscape
An examination of leading providers in the double spindle grinding segment highlights strategic priorities and competitive positioning across the industry. Amada Machine Tools Co., Ltd. focuses on expanding its global footprint through partnerships and localized service centers, while Canton Gear Co., Inc. leverages specialized gear grinding expertise to serve heavy-duty applications. Chiron-Werke GmbH & Co. KG and Danobat Group emphasize integrated automation solutions, embedding robotics and advanced sensor suites into their grinding platforms. DMG MORI and Doosan Machine Tools Co., Ltd. drive innovation through R&D collaborations, targeting next-generation spindle designs and enhanced thermal stability.
EMAG GmbH & Co. KG distinguishes itself with in-house e-machining cells that streamline both turning and grinding operations, whereas Fives Group advances digital offerings by embedding predictive analytics and remote monitoring features. Fritz Studer AG’s precision grinders set benchmarks in ultra-fine finishing, and Gleason Corporation’s gear grinding systems dominate aerospace drivetrain manufacturing. Haas Automation, Inc. continues to disrupt the market with cost-effective, operator-friendly CNC grinders, while JTEKT Corporation and Junker Group focus on high-speed grinding solutions tailored for automotive and bearing components, respectively.
Koyo Machinery USA brings heavy-duty and large-scale grinding expertise to mining and construction equipment markets. Makino Inc. leads in high-end precision grinding, particularly in semiconductor and medical device applications. Okuma America Corporation has built a reputation for IoT-enabled machine tools, and Toyoda Machinery USA offers robust, high-capacity grinders for rail and aerospace OEMs. Lastly, United Grinding Group AG’s extensive product portfolio spans multiple technologies, from nano and micro-grinding to hybrid systems, positioning it as a strategic partner for diversified manufacturing needs. These competitive insights illuminate pathways for collaboration, innovation and market differentiation.
This comprehensive research report delivers an in-depth overview of the principal market players in the Double Spindle Grinding Machine market, evaluating their market share, strategic initiatives, and competitive positioning to illuminate the factors shaping the competitive landscape.
- Amada Machine Tools Co., Ltd.
- Canton Gear Co., Inc.
- Chiron-Werke GmbH & Co. KG
- Danobat Group
- DMG MORI
- Doosan Machine Tools Co., Ltd.
- EMAG GmbH & Co. KG
- Fives Group
- Fritz Studer AG
- Gleason Corporation
- Haas Automation, Inc.
- JTEKT Corporation
- Junker Group
- Koyo Machinery USA
- Makino Inc.
- Okuma America Corporation
- Toyoda Machinery USA
- United Grinding Group AG
Actionable Recommendations for Industry Leaders
Industry leaders can take decisive steps to harness emerging opportunities and mitigate challenges in the double spindle grinding domain. First, investing in AI-driven CNC platforms and edge-computing architectures will refine process control, reduce setup times and enable closed-loop feedback systems for optimal wheel wear compensation. Second, diversifying supply chains by developing partnerships with regional suppliers can alleviate tariff pressures and shorten lead times, thereby enhancing resilience against geopolitical uncertainties.
Third, localizing production and service networks in high-demand regions-particularly in Asia-Pacific and the Americas-will strengthen customer relationships and provide faster technical support. Fourth, expanding aftermarket services through comprehensive upgrade packages and predictive maintenance contracts can generate recurring revenue streams while fostering deeper customer engagement. Fifth, adopting sustainable manufacturing practices, such as cryogenic cooling and coolant recycling systems, will align operations with environmental regulations and corporate ESG goals.
Additionally, manufacturers should prioritize modular machine architectures that facilitate rapid configuration changes, supporting mixed-model production without extensive downtime. Equally important is workforce upskilling: investing in specialized training programs will equip operators and maintenance teams with the expertise necessary to manage advanced CNC and automation systems. Finally, fostering R&D collaborations with universities and technology startups can accelerate innovation cycles and position companies at the forefront of next-generation grinding solutions.
Explore AI-driven insights for the Double Spindle Grinding Machine market with ResearchAI on our online platform, providing deeper, data-backed market analysis.
Ask ResearchAI anything
World's First Innovative Al for Market Research
Conclusion: Navigating the Next Wave of Precision Grinding
In conclusion, double spindle grinding technology stands at a pivotal juncture, shaped by rapid digitalization, shifting trade policies and heightened sustainability demands. Companies that embrace advanced control systems and integrate predictive maintenance strategies will secure competitive advantages in efficiency and uptime. At the same time, proactive adaptation to tariff-induced cost pressures-through supply chain diversification and localized manufacturing-will be critical to maintaining profitability.
Segmentation analysis underscores the importance of tailoring solutions across machine types, end-user requirements, and material handling processes. Regional insights point to growth pockets in the Americas, EMEA and Asia-Pacific, each with unique regulatory landscapes and industry clusters. Competitive intelligence reveals both established players and agile challengers that are redefining the market through strategic partnerships, digital toolkits and specialized application expertise.
Ultimately, the convergence of automation, sustainability and material innovation sets the stage for a new era in precision grinding. Stakeholders who act decisively-investing in modular machine platforms, environmental stewardship and workforce development-will be well-positioned to lead the next wave of growth and innovation in the global double spindle grinding market.
This section provides a structured overview of the report, outlining key chapters and topics covered for easy reference in our Double Spindle Grinding Machine market comprehensive research report.
- Preface
- Research Methodology
- Executive Summary
- Market Overview
- Market Dynamics
- Market Insights
- Cumulative Impact of United States Tariffs 2025
- Double Spindle Grinding Machine Market, by Machine Type
- Double Spindle Grinding Machine Market, by Application Industry
- Double Spindle Grinding Machine Market, by End-User
- Double Spindle Grinding Machine Market, by Control Type
- Double Spindle Grinding Machine Market, by Technology Type
- Double Spindle Grinding Machine Market, by Material Type
- Double Spindle Grinding Machine Market, by Functionality
- Double Spindle Grinding Machine Market, by Coolant System Type
- Americas Double Spindle Grinding Machine Market
- Asia-Pacific Double Spindle Grinding Machine Market
- Europe, Middle East & Africa Double Spindle Grinding Machine Market
- Competitive Landscape
- ResearchAI
- ResearchStatistics
- ResearchContacts
- ResearchArticles
- Appendix
- List of Figures [Total: 32]
- List of Tables [Total: 1202 ]
Take the Next Step Towards Strategic Advantage through Expert Market Intelligence
To further explore comprehensive insights and detailed strategies, reach out to Ketan Rohom (Associate Director, Sales & Marketing at 360iResearch) and secure your market research report today. Empower your organization with the knowledge needed to drive strategic decisions and achieve sustained competitive advantage.
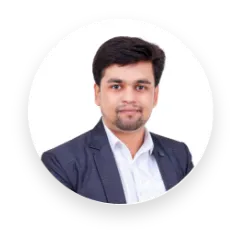
- When do I get the report?
- In what format does this report get delivered to me?
- How long has 360iResearch been around?
- What if I have a question about your reports?
- Can I share this report with my team?
- Can I use your research in my presentation?