Introduction
The oil and gas industry depends on the performance and reliability of drill collars to support the drill string, maintain trajectory, and optimize bit weight under intense downhole conditions. Drill collars, typically heavy, thick-walled tubulars made of high-strength steels or specialty alloys, act as the workhorse between the drill bit and drill pipe. In recent years, market demands have shifted toward collars engineered for greater durability, precise dimensional tolerances, and real-time performance monitoring. These requirements stem from deeper, more complex reservoirs, extended-reach drilling campaigns, and the drive to reduce non-productive time.
As exploration moves into ultra-deepwater and unconventional plays, operators prioritize collars offering enhanced fatigue resistance, superior load capacity, and corrosion protection. Advanced manufacturing techniques such as forging followed by precision machining and heat treatment deliver the mechanical properties required for these challenging environments. Concurrently, the integration of sensors and data analytics into “smart” collars enables real-time downhole monitoring, alerts to drilling dysfunctions, and predictive maintenance strategies that drive cost efficiencies.
This executive summary provides a concise overview of the factors shaping the drill collar market, examines recent policy developments, highlights key segmentation insights, and identifies the leading companies and regions defining the competitive terrain. It concludes with actionable recommendations designed to guide industry leaders in adapting their strategies, maximizing value creation, and securing operational excellence.
Transformative Shifts in the Drill Collar Landscape
The drill collar landscape has undergone a series of transformative shifts driven by technological innovation, operational complexity, and evolving regulatory frameworks. Operators now demand collars that go beyond basic structural support to deliver data intelligence, extend service life, and minimize downtime. In parallel, materials science breakthroughs have introduced high-performance alloys and specialty stainless grades, enabling collars that withstand higher pressures, aggressive corrosive environments, and extreme temperature variation.
Additive manufacturing and modular engineering approaches are reshaping production models. By leveraging near-net-shape forging combined with precision finishing techniques, manufacturers can reduce lead times and scrap rates while maintaining tight tolerances on diameter, wall thickness, and weight distribution. Meanwhile, automated quality-assurance protocols, including digital inspection procedures and integrated certification standards, ensure consistency and traceability across large production volumes.
On the operational front, the integration of IoT-capable sensors and real-time data analytics into drill collars transforms the downhole monitoring paradigm. Data streams tracking vibration, torque, axial load, and fatigue accumulation allow drilling teams to adjust parameters on the fly, optimize bit-to-formation interaction, and extend tool life. These shifts are accelerating the adoption of smart drilling solutions and fostering closer collaboration between service companies, technology providers, and operators to drive continuous improvement in drilling performance.
Cumulative Impact of United States Tariffs 2025
In 2025, the imposition of higher tariffs on drill collar imports into the United States has exerted significant pressure on global supply chains. With duties rising by up to 20 percent on collars originating from key manufacturing hubs, operators and service companies have been forced to reassess procurement strategies. The increased cost burden has translated into higher landed costs, prompting some end users to extend service intervals or explore alternative sources.
Manufacturers outside the tariff zone have ramped up capacity to capture displaced volume, accelerating expansion plans in regions such as Southeast Asia and Europe. Domestic producers have seized this opportunity, reinvesting the additional margin into production capacity upgrades and advanced machining centers. However, the sudden spike in demand for onshore collar fabrication has strained raw material supply, causing intermittent shortages of alloy steel billets and specialty stainless bars.
These dynamics have also spurred a wave of strategic alliances and joint ventures between U.S. fabricators and international technology providers. By localizing critical manufacturing steps-such as heat treatment, forging, and sensor integration-these partnerships mitigate tariff impacts and ensure faster turnaround times. At the same time, operators are evaluating hybrid sourcing models that blend domestic production of standard collars with offshore supply of high-performance, sensor-embedded variants. This dual approach aims to balance cost efficiency with the advanced functionality required in complex drilling scenarios.
Key Segmentation Insights
A comprehensive view of drill collar offerings reveals distinct groups based on material composition, dimensions and specifications, manufacturing processes, application types, operational performance, technology integration, quality assurance, customization capabilities, environmental and safety considerations, and market dynamics. Collars fashioned from alloy steel and carbon steel dominate baseline applications, while cast iron and stainless steel grades serve niche corrosion-resistant needs. Specialty materials such as high performance alloys ensure longevity under severe downhole conditions.
Precision requirements further differentiate collars by diameter categories, length variation, wall thickness, and weight range, catering to everything from slimhole completions to heavy-weight drilling. Underlying these physical parameters are varied manufacturing routes-casting for foundational shapes, forging for superior grain structure, heat treatment for tailored mechanical properties, and finishing techniques that deliver exact tolerances.
On the application side, customized models accommodate client-specific drilling programs, heavy- and high-performance models excel in extended-reach and high-pressure wells, operational drilling variants focus on reliability during long-cycle operations, and standard models offer cost-effective solutions for routine work. Performance metrics such as durability, fatigue resistance, load capacity, long-term reliability, and vibration control form the basis for comparing candidate collars in any scenario.
The rise of smart collars highlights the technology integration segment, where automated controls, data analytics capabilities, IoT-enabled functionality, sensor embedding, and smart monitoring define a new frontier. This category includes real-time data processing under the IoT-enabled banner, offering operators actionable insights during drilling. Rigorous quality assurance protocols-covering certification standards, compliance parameters, inspection procedures, and warranty and support-underpin reliability across all product lines.
Customization capabilities range from client-specific requirements and flexible engineering solutions underpinned by modular options, to performance optimization and tailored designs. Environmental and safety priorities have spawned collars built with eco-friendly materials, recyclable components, integrated safety mechanisms, and sustainable manufacturing driven by green technologies. Finally, market dynamics such as competitive landscape assessment, demand fluctuations, innovation trends featuring emerging technologies, price trends, and supply chain efficiency round out the segmentation framework, guiding stakeholders in selecting the optimal drill collar solution.
This comprehensive research report categorizes the Drill Collars in Oilfield market into clearly defined segments, providing a detailed analysis of emerging trends and precise revenue forecasts to support strategic decision-making.
- Material Composition
- Dimension And Specifications
- Manufacturing Process
- Application Type
- Operational Performance
- Technology Integration
- Quality Assurance
- Customization Capabilities
- Environmental And Safety
- Market Dynamics
Key Regional Insights
Regional analysis underscores significant contrasts in demand drivers and supply structures across the Americas, Europe, Middle East & Africa, and Asia-Pacific. In the Americas, established shale and offshore programs emphasize heavy-duty and customizable collar variants, backed by a robust network of onshore fabricators and service centers. Inventory strategies in North America increasingly favor domestic supply to hedge against import tariffs and logistics disruptions.
In Europe, Middle East & Africa, deepwater Gulf of Guinea operations and North Sea well interventions generate sustained demand for high-performance and sensor-embedded collars. Regional manufacturers leverage advanced heat treatment and forging capabilities to meet stringent certification standards. The Middle East’s strategic investments in localized production hubs and the EMEA cluster’s push toward sustainable manufacturing have further diversified supply options.
Asia-Pacific stands out as both a production powerhouse and a rapidly growing consumption market. Fabricators in China, South Korea, and India have scaled up output of standard and specialty collars to serve local and export markets. At the same time, emerging offshore basins off Australia and Southeast Asia rotate high-weight collars through extended offshore campaigns, driving interest in fatigue-resistant and IoT-capable solutions. The region’s supply chain maturity, combined with favorable government incentives for advanced manufacturing, positions Asia-Pacific as a strategic alternative to traditional sources.
This comprehensive research report examines key regions that drive the evolution of the Drill Collars in Oilfield market, offering deep insights into regional trends, growth factors, and industry developments that are influencing market performance.
- Americas
- Asia-Pacific
- Europe, Middle East & Africa
Key Companies Insights
The competitive landscape features a blend of global energy service giants, specialized equipment providers, and nimble innovators. Leading oilfield services companies such as Baker Hughes Company, Halliburton Company, National Oilwell Varco, Schlumberger Limited, and Weatherford International deliver integrated drilling solutions that bundle drill collars with downhole tools and data analytics platforms. Major drilling contractors, including Transocean Ltd., Nabors Industries, and Patterson-UTI Energy, leverage in-house collar inventories to optimize operational readiness.
Equipment specialists like Advanced Drilling Systems, Diamond Offshore Drilling Inc., DSI Oilfield Services, Eclipse Drilling Solutions, and Fortress Drilling Supplies focus on high-tolerance machining and custom solutions. Frontier Drill Technologies, Global Drill Collars Inc., Ironclad Drill Tools, and MetroDrill Dynamics concentrate on material science innovations and fatigue-resistant designs. NOV Inc., Oilfield Solutions Corporation, and ProDrill Technologies champion modular manufacturing approaches and rapid-turn custom engineering.
Pure-play collar fabricators such as FieldTech Drilling & Equipment, Precision Drills Inc., Precision Oilfield Equipment, Titan Oil Tools, and Zenith Oilfield Products reinforce their positions through targeted investments in quality assurance and localized support networks. Emerging players like DeepDrill Innovations, Helmerich & Payne Inc., Nova Drill Engineering, RigTech Engineering, and Superior Energy Services Inc. differentiate with IoT-enabled monitoring, sustainable manufacturing practices, and end-to-end life-cycle services. Together, these companies drive competition, spur innovation, and expand the palette of solutions available to operators.
This comprehensive research report delivers an in-depth overview of the principal market players in the Drill Collars in Oilfield market, evaluating their market share, strategic initiatives, and competitive positioning to illuminate the factors shaping the competitive landscape.
- Advanced Drilling Systems
- Baker Hughes Company
- DeepDrill Innovations
- Diamond Offshore Drilling Inc.
- DSI Oilfield Services
- Eclipse Drilling Solutions
- FieldTech Drilling & Equipment
- Fortress Drilling Supplies
- Frontier Drill Technologies
- Global Drill Collars Inc.
- Halliburton Company
- Helmerich & Payne Inc.
- Ironclad Drill Tools
- MetroDrill Dynamics
- Nabors Industries
- National Oilwell Varco
- NOV Inc.
- Nova Drill Engineering
- Oilfield Solutions Corporation
- Patterson-UTI Energy
- Precision Drills Inc.
- Precision Oilfield Equipment
- ProDrill Technologies
- RigTech Engineering
- Schlumberger Limited
- Superior Energy Services Inc.
- Titan Oil Tools
- Transocean Ltd.
- Weatherford International
- Zenith Oilfield Products
Actionable Recommendations for Industry Leaders
Industry leaders should prioritize a multi-pronged approach to navigate evolving market dynamics. First, accelerate adoption of sensor-embedded and IoT-capable collars by forging partnerships with digital technology providers and embedding real-time data processing capabilities into tool designs. Second, bolster domestic manufacturing footprints-particularly in regions affected by tariffs-by investing in advanced forging, heat treatment, and finishing centers that reduce lead times and enhance quality control.
Third, deploy flexible modular engineering solutions that allow rapid configuration of diameter, wall thickness, and length to match specific well architectures. Modular options streamline production planning and mitigate supply chain risks. Fourth, engage in sustainability initiatives, including the use of eco-friendly materials, recyclable components, and green manufacturing processes, to meet tightening environmental regulations and operator ESG mandates.
Fifth, refine quality assurance frameworks by standardizing inspection procedures, reinforcing certification compliance, and extending warranty and support services that differentiate offerings. Sixth, implement dynamic pricing models that reflect raw material costs, demand fluctuations, and competitive positioning, enabling responsive adjustments without compromising margins. Finally, cultivate strategic alliances-whether joint ventures between producers and service providers or co-development agreements with technology firms-to share risk, accelerate innovation trends, and capture emerging opportunities in high-growth basins.
Explore AI-driven insights for the Drill Collars in Oilfield market with ResearchAI on our online platform, providing deeper, data-backed market analysis.
Ask ResearchAI anything
World's First Innovative Al for Market Research
Conclusion
Drill collars will remain a cornerstone of drilling operations as the industry tackles deeper reservoirs, complex geology, and stringent environmental standards. The transition toward integrated, smart drilling systems underscores the importance of tool reliability, data-driven decision making, and agile supply chains. Companies that master advanced materials, precision manufacturing, and digital connectivity will capture market share and deliver superior well performance. Concurrently, those that align production strategies with regional policy shifts and sustainability goals will secure long-term competitive advantage.
By weaving together technological innovation, quality assurance, and collaborative partnerships, stakeholders can navigate volatility, optimize costs, and sustain operational excellence. This confluence of factors highlights the critical role of drill collars not only as mechanical components but as enablers of performance gains, safety improvements, and environmental stewardship in the evolving energy landscape.
This section provides a structured overview of the report, outlining key chapters and topics covered for easy reference in our Drill Collars in Oilfield market comprehensive research report.
- Preface
- Research Methodology
- Executive Summary
- Market Overview
- Market Dynamics
- Market Insights
- Cumulative Impact of United States Tariffs 2025
- Drill Collars in Oilfield Market, by Material Composition
- Drill Collars in Oilfield Market, by Dimension And Specifications
- Drill Collars in Oilfield Market, by Manufacturing Process
- Drill Collars in Oilfield Market, by Application Type
- Drill Collars in Oilfield Market, by Operational Performance
- Drill Collars in Oilfield Market, by Technology Integration
- Drill Collars in Oilfield Market, by Quality Assurance
- Drill Collars in Oilfield Market, by Customization Capabilities
- Drill Collars in Oilfield Market, by Environmental And Safety
- Drill Collars in Oilfield Market, by Market Dynamics
- Americas Drill Collars in Oilfield Market
- Asia-Pacific Drill Collars in Oilfield Market
- Europe, Middle East & Africa Drill Collars in Oilfield Market
- Competitive Landscape
- ResearchAI
- ResearchStatistics
- ResearchContacts
- ResearchArticles
- Appendix
- List of Figures [Total: 36]
- List of Tables [Total: 694 ]
Call to Action (CTA) with Ketan Rohom
Ready to gain deeper insights and strategic guidance on the global drill collar market? Contact Ketan Rohom (Associate Director, Sales & Marketing) to secure your comprehensive report and enable data-driven decisions that drive operational excellence and competitive advantage.
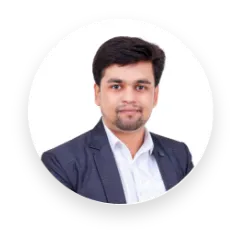
- When do I get the report?
- In what format does this report get delivered to me?
- How long has 360iResearch been around?
- What if I have a question about your reports?
- Can I share this report with my team?
- Can I use your research in my presentation?