Positioning Eco-Friendly Hard Brazing Filler Metal in Modern Manufacturing
The demand for eco-friendly hard brazing filler metal has never been more critical as manufacturers face increasing pressure to reconcile performance requirements with sustainability objectives. Hard brazing, a process characterized by its ability to join dissimilar metals at elevated temperatures, plays a pivotal role in industries ranging from aerospace and automotive to electronics and HVAC. However, traditional filler metals often contain hazardous elements such as cadmium, raising concerns about worker safety, environmental impact, and regulatory compliance.
In response, the industry is undergoing a strategic pivot toward alloys formulated without toxic heavy metals, prioritizing both functional integrity and reduced ecological footprint. This shift is fueled by stringent environmental regulations, heightened corporate social responsibility commitments, and a growing recognition that sustainable materials can enhance brand reputation and operational resilience.
As decision-makers navigate this evolving landscape, they must weigh technical performance metrics-such as joint strength, corrosion resistance, and thermal compatibility-against factors like material lifecycle impact, recycling potential, and supply chain transparency. By integrating eco-friendly filler metals into assembly protocols, companies can achieve critical performance milestones while demonstrating leadership in environmental stewardship. This introduction sets the stage for an in-depth exploration of the transformative trends, regulatory headwinds, segmentation dynamics, regional nuances, competitive benchmarks, and strategic imperatives driving the future of sustainable hard brazing materials.
Transformative Shifts Shaping the Brazing Materials Landscape
Over the past decade, a confluence of technological innovation, regulatory evolution, and supply chain recalibration has reshaped the hard brazing filler metal landscape. First, environmental regulations worldwide have tightened permissible limits for cadmium, silver-cadmium, and other toxic constituents, prompting alloy developers to engineer cadmium-free variants without sacrificing mechanical robustness. Such transformations have led to breakthroughs in silver-copper-phosphorus formulations and nickel-chrome alternatives, offering performance parity with legacy materials.
Simultaneously, digitalization and Industry 4.0 practices have permeated brazing operations. Advanced process monitoring, real-time thermal profiling, and closed-loop quality control systems enable precise temperature management and defect detection, reducing waste and enhancing joint consistency. Moreover, adoption of induction and vacuum furnace brazing methods has increased throughput while minimizing oxidation and flux residue.
Supply chains have also undergone strategic realignment. The rise of nearshoring initiatives and reshoring incentives in key manufacturing hubs has driven localized alloy production, mitigating risks associated with volatile raw material markets. Proactive partnerships among alloy producers, equipment manufacturers, and end users facilitate collaborative R&D, accelerating the commercialization of next-generation eco-friendly fillers.
Together, these transformative shifts underscore a broader industry commitment to sustainable, high-performance brazing solutions that meet the rigorous demands of modern assembly environments.
Assessing the Cumulative Impact of 2025 US Tariffs on Brazing Metals
In 2025, a new wave of United States tariffs on critical metals-including silver, nickel, copper, and aluminum-took effect, reshaping the cost dynamics of hard brazing filler metal production. The imposition of additional duties on imported alloys has driven manufacturers to reassess sourcing strategies and renegotiate supplier contracts. As a result, many have been compelled to diversify raw material portfolios, exploring domestic mines and secondary recycling sources to contain input costs while adhering to eco-friendly mandates.
These tariffs have also accelerated efforts to develop alloys that use lower-cost base metals or reduced precious-metal content while maintaining corrosion resistance and joint integrity. Consequently, alloy formulators have intensified research into composite fillers that blend nickel-chrome matrices with trace silver-phosphorus additives, striking an optimal balance between price and performance.
Moreover, tariff-driven cost pressures have spurred manufacturers to optimize brazing processes, leveraging energy-efficient furnaces and induction systems to offset increased material expenses. Enhanced process controls reduce scrap rates and rework, further buffering the financial impact of tariff-related input surcharges. In parallel, strategic stockpiling of precursor powders and master alloys has provided short-term relief against sudden duty hikes.
Ultimately, while these tariffs introduce complexity into procurement and production planning, they also catalyze innovation in alloy design and process efficiency-driving the industry toward more self-reliant, resource-efficient brazing ecosystems.
Key Insights from Market Segmentation
A nuanced understanding of market segmentation illuminates the diverse requirements and growth vectors within the eco-friendly hard brazing filler metal arena. Based on application, the aerospace sector-which encompasses airframe components, engine components and landing gear-demands alloys that deliver exceptional joint strength under extreme thermal cycling. The automotive domain, with its emphasis on brakes, engine components and exhaust systems, prioritizes corrosion-resistant, cadmium-free silver alloys that withstand high temperatures and corrosive combustion byproducts. Construction applications, spanning piping, structural components and welding joints, benefit from aluminum-silicon and aluminum-magnesium fillers that enable leak-free, load-bearing assemblies. In electronics & electricals, encompassing appliance components, circuit boards and connectors, silver-copper-phosphorus formulations offer superior electrical conductivity and flux-free brazing capabilities. HVAC & refrigeration use cases-covering compressor joints, heat exchanger coils and refrigerant circuits-leverage silver-cadmium-free alloys engineered for high thermal conductivity and long-term reliability. Jewelry & art applications, including decorative items and functional assemblies, place a premium on aesthetic finish and regulatory compliance, driving demand for silver-nickel and silver-copper-phosphorus blends.
When segmented by material, aluminum alloys-particularly aluminum-magnesium and aluminum-silicon variants-address lightweight, corrosion-resistant needs in construction and automotive sectors. Copper alloys such as brass, cupro-nickel and phosphor bronze cater to HVAC, refrigeration and decorative markets. Nickel alloy options, including Inconel, nickel-chrome and nickel-copper, satisfy high-temperature aerospace and industrial equipment requirements. Silver alloys-ranging from silver-cadmium-free blends to silver-nickel complexes-remain indispensable for electronics, automotive and jewelry applications.
Process segmentation further differentiates market offerings: dip brazing-via fluxed dip and salt bath techniques-excels in high-throughput manufacturing; furnace brazing-using batch and continuous furnaces-enables precise thermal profiles for intricate assemblies; induction brazing-through continuous and spot induction systems-delivers localized heating with minimal distortion; torch brazing-across automated and manual operations-provides flexibility for field repairs and low-volume production.
Finally, end-user industry segmentation highlights the strategic importance of the energy sector-oil & gas equipment and renewable energy systems-where corrosion-resistant nickel and copper alloys are critical. Industrial equipment fabrication, ranging from heavy machinery to precision components, relies on high-performance filler metals. Manufacturing end users, including aftermarket services, OEMs and repair shops, drive demand for versatile, easy-to-use brazing alloys that streamline maintenance and assembly workflows.
This comprehensive research report categorizes the Eco-Friendly Hard Brazing Filler Metal market into clearly defined segments, providing a detailed analysis of emerging trends and precise revenue forecasts to support strategic decision-making.
- Application
- Material
- Process
- End-User Industry
Regional Dynamics Influencing Eco-Friendly Brazing Metal Adoption
Regional dynamics play a decisive role in shaping the adoption and innovation of eco-friendly hard brazing filler metals. In the Americas, robust aerospace and automotive manufacturing clusters drive demand for silver-based and nickel-chrome alloys that adhere to stringent quality standards. Policy incentives aimed at revitalizing local production have encouraged investment in domestic alloy synthesis and recycling infrastructure, reducing dependency on volatile import channels.
Within Europe, Middle East & Africa, stringent environmental regulations-such as REACH and RoHS directives-have accelerated the phase-out of cadmium-containing fillers. This regulatory pressure has stimulated the development of silver-cadmium-free products and increased collaboration between alloy producers and furnace equipment manufacturers to optimize brazing parameters for compliance. Additionally, the region’s diverse industrial base, from renewable energy installations to heavy machinery fabrication, demands a broad spectrum of hard brazing solutions.
Asia-Pacific continues to be a growth engine, fueled by expansive electronics and HVAC manufacturing in China, high-precision automotive production in Japan and South Korea, and burgeoning energy infrastructure projects across India and Southeast Asia. Localized production of aluminum-silicon and copper-alloy fillers has surged, supported by government initiatives to enhance export competitiveness. Moreover, strategic partnerships between global alloy developers and regional distributors are streamlining supply chains, ensuring timely delivery of eco-friendly brazing materials to meet rapid industrial expansion.
This comprehensive research report examines key regions that drive the evolution of the Eco-Friendly Hard Brazing Filler Metal market, offering deep insights into regional trends, growth factors, and industry developments that are influencing market performance.
- Americas
- Asia-Pacific
- Europe, Middle East & Africa
Competitive Landscape and Company Highlights
The competitive landscape of eco-friendly hard brazing filler metals features a mix of global conglomerates and specialized alloy manufacturers, each leveraging unique capabilities to differentiate their offerings. Aufhauser Corporation has established a reputation for innovative silver-cadmium-free alloys tailored to aerospace and electronics applications. Belmont Metals, Inc. combines high-purity feedstock sourcing with proprietary flux technology to optimize joint quality across automotive and HVAC segments. Castolin Eutectic GmbH and Hangzhou Huaguang Advanced Welding Materials Co., Ltd. emphasize comprehensive furnace brazing solutions, integrating flux-less fillers with tailored thermal cycles.
Harris Products Group and Johnson Matthey, Inc. concentrate on advanced silver-phosphorus and silver-nickel formulations that meet stringent environmental and performance criteria. Lucas-Milhaupt, Inc. and Morgan Advanced Materials excel in copper-alloy and nickel-chrome variants, catering to renewable energy and heavy equipment applications. Oerlikon Metco (Switzerland) AG applies precision powder metallurgy techniques to produce high-performance alloys for industrial repair and additive manufacturing. UMICORE NV integrates circular economy principles into its product portfolio, offering recycled precious-metal fillers with verifiable sustainability credentials.
Meanwhile, the VBC Group and Voestalpine Böhler Welding have expanded their induction brazing capabilities, delivering localized heating solutions that minimize thermal distortion. Wall Colmonoy Corporation and Wieland Group prioritize supply chain transparency and end-to-end technical support, aiding customers in alloy selection, process optimization and regulatory compliance. Collectively, these companies are driving continuous innovation, forging partnerships across the value chain, and reinforcing the strategic importance of eco-friendly hard brazing filler metals.
This comprehensive research report delivers an in-depth overview of the principal market players in the Eco-Friendly Hard Brazing Filler Metal market, evaluating their market share, strategic initiatives, and competitive positioning to illuminate the factors shaping the competitive landscape.
- Aufhauser Corporation
- Belmont Metals, Inc.
- Castolin Eutectic GmbH
- Hangzhou Huaguang Advanced Welding Materials Co., Ltd.
- Harris Products Group
- Johnson Matthey, Inc.
- Lucas-Milhaupt, Inc.
- Morgan Advanced Materials
- Oerlikon Metco (Switzerland) AG
- UMICORE NV
- VBC Group
- Voestalpine Böhler Welding
- Wall Colmonoy Corporation
- Wieland Group
Actionable Recommendations for Industry Leaders
Industry leaders can accelerate their competitive advantage by implementing several targeted strategies. First, investing in research and development of cadmium-free, low-precious-metal alloys will address both regulatory mandates and cost pressures. Collaborative R&D partnerships with equipment manufacturers can further optimize alloy-process compatibility, ensuring superior joint performance and reduced scrap rates.
Second, diversifying raw material procurement to include domestic mining sources and secondary recycling streams will mitigate tariff exposure and supply chain disruptions. Establishing strategic alliances with recycler networks and metal recovery specialists can build resilience and support circular economy initiatives.
Third, integrating real-time process monitoring and digital quality assurance systems will enhance operational efficiency. Leveraging advanced thermal profiling, machine learning algorithms and closed-loop control mechanisms can reduce rework, minimize energy consumption and accelerate time-to-market for new alloy formulations.
Fourth, strengthening technical support and training programs for end users will facilitate smoother adoption of eco-friendly filler metals. On-site workshops, virtual simulations and certification courses can build customer confidence and drive volume uptake across aerospace, automotive and industrial segments.
Finally, engaging with regulatory bodies and industry consortia to shape emerging environmental standards will position organizations as thought leaders. Proactive participation in standards committees and collaborative trials will ensure timely alignment with global directives, safeguarding market access and reinforcing brand credibility.
Explore AI-driven insights for the Eco-Friendly Hard Brazing Filler Metal market with ResearchAI on our online platform, providing deeper, data-backed market analysis.
Ask ResearchAI anything
World's First Innovative Al for Market Research
Concluding Perspectives on the Future of Eco-Friendly Brazing Metals
The eco-friendly hard brazing filler metal sector stands at a transformative crossroads. Stakeholders must recognize that sustainability and performance are not mutually exclusive but rather complementary drivers of competitive differentiation. By embracing cadmium-free and low-precious-metal alloys, manufacturers can comply with stringent environmental regulations while maintaining joint integrity under demanding operating conditions.
Furthermore, innovations in digital process control and localized heating technologies offer clear pathways to reduce waste and energy consumption, aligning operational excellence with corporate sustainability goals. Strategic sourcing from diversified, resilient supply chains will further insulate manufacturers from geopolitical shifts and raw material volatility.
As the regulatory landscape evolves, early engagement with standards bodies and collaborative R&D initiatives will be critical for anticipating compliance requirements and influencing technical guidelines. Ultimately, the companies that integrate environmental stewardship into their core innovation processes will secure leadership in the rapidly maturing eco-friendly brazing market.
This section provides a structured overview of the report, outlining key chapters and topics covered for easy reference in our Eco-Friendly Hard Brazing Filler Metal market comprehensive research report.
- Preface
- Research Methodology
- Executive Summary
- Market Overview
- Market Dynamics
- Market Insights
- Cumulative Impact of United States Tariffs 2025
- Eco-Friendly Hard Brazing Filler Metal Market, by Application
- Eco-Friendly Hard Brazing Filler Metal Market, by Material
- Eco-Friendly Hard Brazing Filler Metal Market, by Process
- Eco-Friendly Hard Brazing Filler Metal Market, by End-User Industry
- Americas Eco-Friendly Hard Brazing Filler Metal Market
- Asia-Pacific Eco-Friendly Hard Brazing Filler Metal Market
- Europe, Middle East & Africa Eco-Friendly Hard Brazing Filler Metal Market
- Competitive Landscape
- ResearchAI
- ResearchStatistics
- ResearchContacts
- ResearchArticles
- Appendix
- List of Figures [Total: 24]
- List of Tables [Total: 953 ]
Next Steps for Accessing Comprehensive Market Analysis
To obtain comprehensive analysis, detailed company profiles and strategic insights that will inform your decision-making process, reach out to Ketan Rohom (Associate Director, Sales & Marketing) today. He will guide you through the report’s scope and facilitate access to actionable intelligence tailored to your organization’s needs. Elevate your market strategy by securing the definitive resource on eco-friendly hard brazing filler metals.
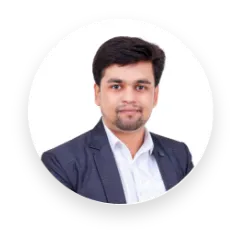
- When do I get the report?
- In what format does this report get delivered to me?
- How long has 360iResearch been around?
- What if I have a question about your reports?
- Can I share this report with my team?
- Can I use your research in my presentation?