Introduction to the Evolving ED Copper Foil Manufacturing Landscape
ED copper foil manufacturing equipment plays a pivotal role in enabling high-performance electronic and energy storage applications. As demand for thinner, stronger, and more conductive copper layers intensifies, manufacturers are investing in advanced electrodeposition reactors, precision rollers, and real-time monitoring systems. This introduction provides a concise yet comprehensive overview of the current market dynamics, emphasizing the intersection of evolving customer requirements and technological innovation.
The confluence of automotive electrification, flexible electronics, and renewable energy storage has elevated the strategic importance of copper foil manufacturing. Equipment vendors are responding to shifting specifications for ultra-thin foils used in state-of-the-art printed circuit boards and the robust, thicker foils required in electric vehicle battery electrodes. Recent breakthroughs in deposition uniformity and surface treatment have unlocked new performance enhancements, reducing defects and accelerating throughput. Simultaneously, supply chain resilience and cost optimization have emerged as key competitive differentiators, compelling original equipment manufacturers to refine modular designs and integrate predictive maintenance.
Rising environmental regulations are also driving the adoption of closed-loop material handling and waste reduction systems. Equipment suppliers are innovating with water treatment modules, low-emission anode technologies, and energy recovery circuits to ensure compliance and reduce operating costs. Material traceability and quality assurance features are now embedded in many new installations, offering real-time defect detection and end-to-end process visibility. Stakeholders across the value chain-from raw foil suppliers to assembly line integrators-are collaborating on standardization efforts to accelerate time-to-market and enhance compatibility across platforms.
As we navigate through this executive summary, the interplay of market drivers, disruptive technologies, and strategic priorities will become clear. The following sections delve into transformative shifts reshaping the landscape, the cumulative impact of newly implemented United States tariffs in 2025, nuanced segmentation insights, regional variations, competitive positioning of key players, and targeted recommendations for leaders seeking to maintain and expand their market presence.
Transformative Shifts in Copper Foil Manufacturing Technology and Market Dynamics
Over the past decade, digital transformation and materials innovation have converged to reshape ED copper foil manufacturing. Industry 4.0 initiatives are driving the integration of advanced sensors, machine learning algorithms, and cloud-based analytics into deposition lines. Real-time process control now enables adaptive adjustments to temperature, current density, and pH levels, resulting in tighter thickness tolerances and fewer production stoppages. Meanwhile, additive and hybrid manufacturing methods are augmenting traditional electrodeposition, opening pathways to custom foil geometries and localized property enhancements.
On the materials front, specialty copper foils featuring anodized surfaces and graphene coatings are gaining traction in markets requiring superior thermal performance and electromagnetic shielding. Simultaneously, ultra-thin and thick-foil segments are expanding in response to diverse customer specifications for flexible circuit assemblies and heavy-duty bus bars. This dual expansion has prompted equipment makers to develop modular reactor designs capable of rapid changeovers between foil thicknesses and process chemistries.
Furthermore, sustainability imperatives are influencing capital investment decisions. Equipment platforms now incorporate energy recovery modules, closed-loop rinse systems, and low-emission anode materials to minimize environmental footprints and operating expenses. The move toward circular economies is also fostering partnerships between equipment suppliers and recyclers, creating integrated solutions for end-of-life foil reclamation. These transformative shifts in technology and market dynamics set the stage for a deeper exploration of policy impacts, segmentation nuances, regional variations, competitive landscapes, and strategic recommendations.
Assessing the Cumulative Impact of United States Tariffs Implemented in 2025
The introduction of United States tariffs in 2025 has introduced tangible cost pressures across the ED copper foil equipment supply chain. Import duties on key components such as precision rollers, anode assemblies, and control system modules have led OEMs and end-users to reassess sourcing strategies and production footprints. As a result, capital expenditure budgets are now being redirected toward domestic equipment providers and localized manufacturing partnerships to mitigate tariff-related expenses.
In addition to immediate pricing impacts, the tariffs have accelerated discussions around vertical integration. Several major battery and electronics manufacturers are evaluating the feasibility of in-house electrodeposition lines to secure uninterrupted access to critical foil substrates. This shift has spurred equipment suppliers to offer turnkey solutions that bundle deposition reactors, chemical management systems, and automation packages under single procurement agreements.
Moreover, tariff-induced supply chain realignment has elevated the importance of alternative materials and process chemistries. Research into copper-nickel alloys and hybrid metallization techniques is gaining momentum as organizations seek to diversify risk. Collaborative efforts between equipment vendors, chemical suppliers, and research institutes aim to develop compatible processing platforms that can accommodate a broader range of foil types without extensive capital modifications.
Transitioning from reactive cost management to proactive supply chain optimization, industry stakeholders are forging strategic alliances, expanding service networks, and implementing digital procurement tools. These measures are designed to offset tariff impacts, protect profit margins, and preserve agility amid an evolving trade policy landscape.
Key Segmentation Insights into Applications, Processes, Industries, Material Types, Technologies, and Components
When segmented by application, the market spans automotive, electronics, and energy storage. Within automotive, demand is driven by autonomous driving systems, electric vehicles, and hybrid vehicles; the electronics segment covers flexible circuit boards, printed circuit boards, and semiconductors; energy storage encompasses battery manufacturing and capacitor manufacturing. Examining production process segmentation, continuous casting and ingot casting define the casting category, while acid copper plating and electrochemical deposition lead electrodeposition, and cold press laminations alongside hot press laminations characterize lamination.
Considering end-user industry segmentation, the automotive sector divides into internal combustion engine components and renewable energy systems; the consumer electronics arena includes laptops, smartphones, and wearables; telecommunications focuses on data centers and network infrastructure. Material type segmentation highlights specialty copper foil, thick copper foil, and ultra-thin copper foil; within specialty foil, anodized and graphene-coated variants stand out, thick foil ranges from 35 to above 70 microns, and ultra-thin foil spans from 12 to below 12 microns.
Technology segmentation differentiates additive manufacturing with 3D printing and laser sintering, hybrid manufacturing through direct imaging and laser direct structuring, and subtractive manufacturing via chemical etching and photoresist strip. Finally, key component segmentation identifies anodes subdivided into graphite and silicon anodes, electrolyte solutions divided into liquid and solid-state formulations, and substrate materials encompassing glass and polymer substrates. This multi-dimensional segmentation framework illuminates market entry points, growth pockets, and areas requiring tailored equipment configurations.
This comprehensive research report categorizes the ED Copper Foil Manufacturing Equipment market into clearly defined segments, providing a detailed analysis of emerging trends and precise revenue forecasts to support strategic decision-making.
- Application
- Production Process
- End-User Industry
- Material Type
- Technology
- Key Components
Key Regional Insights Across the Americas, EMEA, and Asia-Pacific Markets
In the Americas, the market is shaped by significant investments in electric vehicle battery lines and high-performance electronics hubs. North American policymakers are supporting domestic capacity expansions through tax credits and grants, while Latin American resource regions are emerging as key suppliers of raw copper and anode materials. This dynamic has prompted equipment providers to establish service centers and technical collaborations across the hemisphere.
Within Europe, Middle East and Africa, stringent environmental regulations and decarbonization targets are prompting rapid adoption of closed-loop processing systems and energy-efficient deposition equipment. Major automotive OEMs in Germany, France, and the UK are integrating advanced copper foil lines to support next-generation electric drivetrains. In the Middle East, emerging technology parks are investing in electronics and renewable energy storage, and in Africa, increasing interest in local battery assembly plants has sparked early-stage equipment deployments.
The Asia-Pacific region remains the largest volume market, driven by extensive electronics manufacturing ecosystems in China, Taiwan, South Korea, and Japan. Here, flexible display technologies and high-density interconnect boards require ultra-thin copper foils, while burgeoning battery industries demand thick-foil electrodeposition systems. The prevalence of regional champions and specialized contract manufacturers has led equipment vendors to offer scalable platforms, localized support networks, and joint development agreements to capture growth in this diverse and fast-evolving landscape.
This comprehensive research report examines key regions that drive the evolution of the ED Copper Foil Manufacturing Equipment market, offering deep insights into regional trends, growth factors, and industry developments that are influencing market performance.
- Americas
- Asia-Pacific
- Europe, Middle East & Africa
Competitive Landscape: Leading Players in Copper Foil Manufacturing Equipment
The competitive landscape is characterized by established equipment specialists, regionally focused innovators, and integrated material suppliers. Arcotech Ltd. has distinguished itself through precision patterning tools and tailored electrodeposition cells. Chang Chun Group combines chemical expertise with deposition systems, while Circuit Foil Luxembourg SARL focuses on ultra-thin foil processing technologies. Co-Tech Development Corp. and Doosan Corporation Electro-Materials BG offer turnkey solutions optimized for battery foil production.
Furukawa Electric Co., Ltd. and Guangdong Chaohua Technology Co., Ltd. leverage deep process know-how to deliver high-throughput, low-defect platforms. Hitachi Metals, Ltd. and Ju Teng International Holdings Limited integrate material development with equipment innovation to accelerate time-to-market. JX Nippon Mining & Metals Corporation and LS Mtron Co., Ltd. emphasize vertical integration and global service networks, whereas Luvata Co., Ltd. and Mitsubishi Materials Trading Corporation focus on customizable reactor modules for niche applications.
Nan Ya Plastics Corporation and Olin Brass (Global Brass and Copper Holdings, Inc.) bring polymer and alloy synergy to advanced copper foil processes. Shandong Chaoyue Electronic Co., Ltd. and Shandong Fangyuan Nonferrous Metals Group Co., Ltd. cater to high-volume domestic demand, and SKC Solmics Co., Ltd. along with Sumitomo Metal Mining Co., Ltd. prioritize sustainable production and resource efficiency. These diverse approaches underline the importance of strategic differentiation, service excellence, and technology leadership.
This comprehensive research report delivers an in-depth overview of the principal market players in the ED Copper Foil Manufacturing Equipment market, evaluating their market share, strategic initiatives, and competitive positioning to illuminate the factors shaping the competitive landscape.
- Arcotech Ltd.
- Chang Chun Group
- Circuit Foil Luxembourg SARL
- Co-Tech Development Corp.
- Doosan Corporation Electro-Materials BG
- Furukawa Electric Co., Ltd.
- Guangdong Chaohua Technology Co., Ltd.
- Hitachi Metals, Ltd.
- Ju Teng International Holdings Limited
- JX Nippon Mining & Metals Corporation
- LS Mtron Co., Ltd.
- Luvata Co., Ltd.
- Mitsubishi Materials Trading Corporation
- Nan Ya Plastics Corporation
- Olin Brass (Global Brass and Copper Holdings, Inc.)
- Shandong Chaoyue Electronic Co., Ltd.
- Shandong Fangyuan Nonferrous Metals Group Co., Ltd.
- SKC Solmics Co., Ltd.
- Sumitomo Metal Mining Co., Ltd.
Actionable Recommendations for Industry Leaders to Capitalize on Emerging Opportunities
Invest in modular, digitally enabled equipment that supports rapid reconfiguration between foil thicknesses and process chemistries to address changing application requirements. Develop strategic partnerships with chemical and materials suppliers to co-innovate new electrodeposition recipes and surface treatments that enhance foil performance without extensive capital outlays. Implement predictive maintenance programs leveraging machine learning models trained on process data to reduce unplanned downtime and extend equipment lifespan.
Diversify supply chains by qualifying secondary component sources and establishing regional assembly or service hubs to mitigate tariff exposure and logistical disruptions. Prioritize the integration of closed-loop water treatment and energy recovery systems in new installations to achieve both environmental compliance and cost savings. Foster collaboration with academic institutions and industry consortia to standardize process parameters and accelerate technology adoption across adjacent markets.
By executing these measures, industry leaders can strengthen resilience, accelerate innovation cycles, and maintain margins in an environment of shifting trade policies, sustainability imperatives, and dynamic end-user demands.
Explore AI-driven insights for the ED Copper Foil Manufacturing Equipment market with ResearchAI on our online platform, providing deeper, data-backed market analysis.
Ask ResearchAI anything
World's First Innovative Al for Market Research
Conclusion: Navigating the Future of ED Copper Foil Production
The ED copper foil equipment market stands at the intersection of advanced materials science, automated manufacturing, and evolving end-user needs. Navigating this landscape demands a balanced approach that aligns technological innovation with strategic supply chain management. By understanding the transformative shifts in process automation, the implications of recent tariff policies, and the granular segmentation insights, decision-makers can better position their organizations for sustainable growth.
Regional nuances and competitive dynamics underscore the need for adaptive strategies that address localized requirements while leveraging global best practices. As key players differentiate through customization, service excellence, and R&D collaboration, agility becomes a defining attribute for market leaders. Organizations that proactively integrate digital capabilities, diversify procurement channels, and champion eco-efficient processes will be best equipped to capture the full spectrum of application opportunities, from flexible electronics to energy storage solutions.
This section provides a structured overview of the report, outlining key chapters and topics covered for easy reference in our ED Copper Foil Manufacturing Equipment market comprehensive research report.
- Preface
- Research Methodology
- Executive Summary
- Market Overview
- Market Dynamics
- Market Insights
- Cumulative Impact of United States Tariffs 2025
- ED Copper Foil Manufacturing Equipment Market, by Application
- ED Copper Foil Manufacturing Equipment Market, by Production Process
- ED Copper Foil Manufacturing Equipment Market, by End-User Industry
- ED Copper Foil Manufacturing Equipment Market, by Material Type
- ED Copper Foil Manufacturing Equipment Market, by Technology
- ED Copper Foil Manufacturing Equipment Market, by Key Components
- Americas ED Copper Foil Manufacturing Equipment Market
- Asia-Pacific ED Copper Foil Manufacturing Equipment Market
- Europe, Middle East & Africa ED Copper Foil Manufacturing Equipment Market
- Competitive Landscape
- ResearchAI
- ResearchStatistics
- ResearchContacts
- ResearchArticles
- Appendix
- List of Figures [Total: 28]
- List of Tables [Total: 1076 ]
Take the Next Step with Expert Insights from Ketan Rohom
To obtain a comprehensive market research report and tailored insights, please reach out to Ketan Rohom, Associate Director, Sales & Marketing. He can guide you through detailed analyses, segmentation deep dives, and executable strategies designed to support your strategic planning and capital investment decisions. Contact him directly to secure your copy and gain a competitive edge.
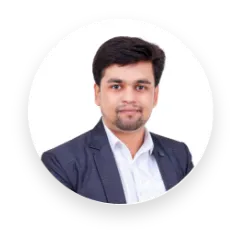
- When do I get the report?
- In what format does this report get delivered to me?
- How long has 360iResearch been around?
- What if I have a question about your reports?
- Can I share this report with my team?
- Can I use your research in my presentation?