Introduction: Harnessing the Power of Electric Forging in Modern Manufacturing
Electric power forging is redefining the boundaries of precision, efficiency, and sustainability in modern manufacturing. By utilizing electromagnetic fields to shape metals, this advanced technology offers a step change over traditional mechanical and hydraulic forging methods. Not only does it deliver faster cycle times and tighter tolerances, but electric power forging also reduces energy consumption and minimizes material waste. As global supply chains evolve and end users demand lighter, stronger components, electric power forging emerges as a strategic enabler for sectors ranging from automotive and aerospace to construction and industrial equipment.
In this executive summary, we explore the transformative shifts reshaping the electric forging landscape, examine the far-reaching effects of new United States tariffs in 2025, and unpack the key segmentation dimensions driving market diversity. We complement these insights with a regional and competitive overview, spotlighting leading players whose innovations and partnerships are steering the industry forward. Finally, we offer actionable recommendations designed to help you navigate regulatory changes, unlock new growth pockets, and fortify your operational footprint. Whether you are an equipment OEM, a service provider, or an end-user in need of high-performance forged components, this analysis provides a clear roadmap for capitalizing on electric power forging’s unique value proposition. By focusing on core levers such as technology adoption, material specialization, and market positioning, organizations can accelerate time to market, enhance product reliability, and secure a competitive edge in a rapidly evolving industrial landscape.
Transformative Shifts in the Electric Forging Landscape
The electric forging sector is experiencing a wave of innovation and disruption driven by several converging forces. First, advances in automation have expanded the scope of fully automated, semi-automated, and manual electric forging cells, enabling manufacturers to tailor throughput and precision to specific application requirements. Second, the process portfolio has broadened from traditional hot forging to include cold and warm forging variants, each offering distinct advantages in surface finish, dimensional consistency, and mechanical strength. Third, material science breakthroughs have unlocked new opportunities for forging advanced alloys-everything from high-strength aluminum and stainless steel to lightweight magnesium alloys such as AZ91D and ZM21-thus meeting the exacting demands of next-generation engine, steering, and transmission components in the automotive sector.
These technological shifts are intertwined with macroeconomic and environmental imperatives. Stricter emissions regulations and global decarbonization targets have intensified the push toward energy-efficient manufacturing. Electric power forging, with its lower energy footprint and ability to minimize scrap generation, aligns perfectly with sustainability objectives. Simultaneously, the rapid rollout of smart factory architectures and Industry 4.0 platforms is reinforcing real-time process monitoring and predictive maintenance, further boosting equipment uptime and yield. In essence, manufacturers that integrate advanced drives, sensors, and analytics into their electric forging operations are not only cutting costs but also forging a resilient, future-proof operational model. This confluence of automation trends, material innovation, and environmental drivers is reshaping the competitive landscape, compelling both incumbents and new entrants to elevate their game.
Cumulative Impact of United States Tariffs in 2025
The implementation of new United States tariffs in 2025 is set to reshape the competitive dynamics of the electric forging market by altering cost structures, supply-chain flows, and sourcing decisions. Tariffs targeting imports of forged components and blank materials are effectively raising landed costs for a range of steel and non-ferrous inputs, such as alloy steel, copper, and magnesium. As a result, domestic producers with integrated electric forging capabilities stand to benefit from a relative cost advantage, provided they can scale operations to meet rising demand.
However, the tariff regime also introduces complexity for original equipment manufacturers and aftermarket service providers that rely on tightly managed global supply chains. The higher import duties on cold-forged and warm-forged parts may prompt a strategic pivot toward local forging partners, driving consolidation among service providers. Conversely, semi-automated and manual electric forging workshops with flexible capacity are likely to see incremental orders as buyers seek to diversify risk and mitigate tariff exposure.
Further compounding these effects, the reconfiguration of supply chains has sparked renewed interest in reshoring and nearshoring initiatives. Companies are evaluating investments in closed die and precision forging cells closer to key end markets to avoid tariff encumbrances and reduce lead times. As tariffs continue to influence capital allocation decisions, manufacturers offering turnkey solutions-from impression die design to post-forge heat treatment-will find lucrative opportunities to capture market share. Ultimately, the 2025 tariff landscape will favor agile players that can balance short-term cost pressures with long-term investments in electric forging technology and capacity.
Key Segmentation Insights
Understanding the full breadth of electric forging requires a granular view of how technology, material, application, industry vertical, end-user, forging methodology, and component type intersect to drive distinct value pools. Based on technology type, the market divides into automation level-spanning fully automated, semi-automated, and manual-and electrical forging process type, which includes cold forging, hot forging, and warm forging. From a material perspective, the emphasis on lightweighting has elevated the demand for aluminum and advanced magnesium alloys such as AZ91D and ZM21 alongside traditional alloy steel, copper, and stainless steel. Application segmentation highlights the automotive sector, where engine components, steering components, and transmission parts benefit from the tighter tolerances and surface quality that electric forging delivers.
Turning to industry verticals, electric forging has cemented its role in aerospace aerostructures and precision aircraft components, as well as in construction fixtures and structural elements that demand both strength and dimensional accuracy. End users encompass aftermarket service providers-ranging from automotive aftermarket specialists to industrial maintenance firms-and original equipment manufacturers, including aerospace and automotive OEMs that require consistent, high-volume output. In forging methodology, closed die, open die, and precision forging techniques each offer specific advantages, with closed die processes often relying on impression die tooling to achieve complex geometries. Finally, component type segmentation underscores the importance of forged bearings and pistons, which benefit from improved fatigue life and reduced porosity when processed via electric forging. This multi-faceted segmentation framework not only clarifies the market’s diverse drivers but also reveals distinct entry points for strategic investment and partnership.
This comprehensive research report categorizes the Electric Power Forging market into clearly defined segments, providing a detailed analysis of emerging trends and precise revenue forecasts to support strategic decision-making.
- Technology Type
- Material Type
- Application Area
- Industry Vertical
- End User
- Forging Methodology
- Component Type
Key Regional Insights
Regionally, the Americas region commands significant influence owing to its mature automotive and aerospace supply chains, substantial mineral and alloy resources, and proactive reshoring initiatives. Meanwhile, Europe, the Middle East & Africa combines stringent regulatory requirements with advanced manufacturing clusters in Germany, France, and the U.K., positioning it as a hub for high-precision electric forging applications. In parallel, the Gulf Cooperation Council states leverage strategic infrastructure investments and energy-efficiency mandates to propel growth, particularly in the building fixtures and structural components sectors. Across the Asia-Pacific region, rapid industrialization, rising domestic demand, and aggressive capacity expansions in China and India are driving electrification of forging processes. Japan and South Korea remain focal points for cutting-edge automation and the integration of smart factory solutions. Collectively, these regional dynamics underscore the need for geographically tailored strategies that align production capabilities, supply-chain resilience, and end-market requirements.
This comprehensive research report examines key regions that drive the evolution of the Electric Power Forging market, offering deep insights into regional trends, growth factors, and industry developments that are influencing market performance.
- Americas
- Asia-Pacific
- Europe, Middle East & Africa
Key Companies Insights
Within the competitive landscape, several leading firms are shaping the trajectory of electric forging through technological innovation, strategic partnerships, and capacity augmentation. Alcoa Corporation continues to invest in next-generation electric drive systems for aluminum forging, while Arconic Corporation leverages its deep expertise in high-strength alloy development to optimize process parameters. ATI (Allegheny Technologies Incorporated) focuses on advanced material formulations, including specialty stainless steels, to meet stringent aerospace fatigue and corrosion resistance standards. Bharat Forge Limited and Farinia Group, both with significant manufacturing footprints in emerging markets, emphasize flexible production lines capable of rapid changeovers between cold, warm, and hot forging protocols.
Meanwhile, Hitachi, Ltd. integrates digital twins and IoT sensor networks into electric forging cells to deliver predictive maintenance and yield maximization. L&T Forging Ltd. has carved out a niche in closed die impression forging, targeting structural components for infrastructure projects. Precision Castparts Corp (PCC) combines casting and electric forging in hybrid processes to achieve complex geometries with improved metallurgical properties. Rothe Erde India Pvt. Ltd. excels in specialty copper and copper-alloy forgings, while Siemens AG drives industrial electrification through advanced power supply solutions and process control systems. Together, these companies reflect a diverse ecosystem of capabilities that spans raw material innovation, process automation, and services integration.
This comprehensive research report delivers an in-depth overview of the principal market players in the Electric Power Forging market, evaluating their market share, strategic initiatives, and competitive positioning to illuminate the factors shaping the competitive landscape.
- Alcoa Corporation
- Arconic Corporation
- ATI (Allegheny Technologies Incorporated)
- Bharat Forge Limited
- Farinia Group
- Hitachi, Ltd.
- L&T Forging Ltd.
- Precision Castparts Corp (PCC)
- Rothe Erde India Pvt. Ltd.
- Siemens AG
Actionable Recommendations for Industry Leaders
To capitalize on the electric forging opportunity, industry leaders must adopt a multi-pronged approach that balances technology investment, process optimization, and strategic collaboration. First, executives should prioritize the deployment of advanced automation platforms and energy-efficient drives to enhance throughput and reduce per-unit energy consumption. Second, forging decision makers need to standardize data-driven quality control protocols and integrate real-time analytics to minimize scrap rates and accelerate troubleshooting. Third, organizations should cultivate partnerships across material suppliers, toolmakers, and system integrators to create end-to-end solutions-spanning impression die design, process simulation, and post-forge heat treatment-that differentiate their value proposition.
Fourth, forging operations must reevaluate their supply-chain footprint in light of recent tariff shifts, exploring reshoring or nearshoring options where warranted to mitigate elevated import duties and logistics costs. Fifth, leadership teams should invest in workforce upskilling and digital training programs to build proficiency in smart factory tools and predictive maintenance methodologies. Finally, senior managers must continuously monitor regulatory and environmental developments to align forging strategies with sustainability objectives, such as carbon footprint reduction and waste minimization. By orchestrating these initiatives in tandem, companies can accelerate innovation cycles, enhance operational resilience, and secure lasting competitive advantage in a rapidly evolving market.
Explore AI-driven insights for the Electric Power Forging market with ResearchAI on our online platform, providing deeper, data-backed market analysis.
Ask ResearchAI anything
World's First Innovative Al for Market Research
Conclusion
Electric power forging stands at the intersection of precision engineering, sustainable manufacturing, and digital transformation. The convergence of advanced automation, material science breakthroughs, and shifting trade policies has created an environment where agile players can outpace rivals by delivering high-performance components with reduced lead times and carbon footprints. As the industry continues to evolve, success will hinge on the ability to integrate robust process monitoring, flexible capacity configurations, and collaborative ecosystem partnerships.
The cumulative impact of United States tariffs in 2025 underscores the importance of strategic supply-chain realignment, while regional dynamics highlight the need for localized investment and market development. Leading companies are already harnessing the latest electric drive systems, forging methodologies, and alloy formulations to push the boundaries of what is possible-from lightweight aerospace aerostructures to high-volume automotive transmission parts. By maintaining a clear focus on technology adoption, quality assurance, and sustainability imperatives, manufacturers can navigate uncertainty, capitalize on emerging growth pockets, and reinforce their position as trusted providers of critical forged solutions.
This section provides a structured overview of the report, outlining key chapters and topics covered for easy reference in our Electric Power Forging market comprehensive research report.
- Preface
- Research Methodology
- Executive Summary
- Market Overview
- Market Dynamics
- Market Insights
- Cumulative Impact of United States Tariffs 2025
- Electric Power Forging Market, by Technology Type
- Electric Power Forging Market, by Material Type
- Electric Power Forging Market, by Application Area
- Electric Power Forging Market, by Industry Vertical
- Electric Power Forging Market, by End User
- Electric Power Forging Market, by Forging Methodology
- Electric Power Forging Market, by Component Type
- Americas Electric Power Forging Market
- Asia-Pacific Electric Power Forging Market
- Europe, Middle East & Africa Electric Power Forging Market
- Competitive Landscape
- ResearchAI
- ResearchStatistics
- ResearchContacts
- ResearchArticles
- Appendix
- List of Figures [Total: 30]
- List of Tables [Total: 806 ]
Call to Action: Reach Out to Ketan Rohom for In-Depth Market Analysis
Unlock the full potential of electric power forging with a comprehensive market research report tailored to your strategic objectives. Reach out to Ketan Rohom, Associate Director of Sales & Marketing, to gain access to detailed analyses on technological trends, tariff impacts, segmentation breakdowns, and competitive benchmarking. Engage today to make informed decisions, anticipate industry shifts, and drive sustainable growth.
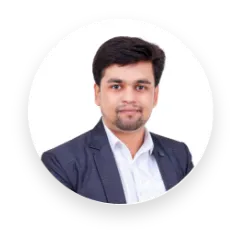
- When do I get the report?
- In what format does this report get delivered to me?
- How long has 360iResearch been around?
- What if I have a question about your reports?
- Can I share this report with my team?
- Can I use your research in my presentation?