Unlocking Critical Insights into Electronic Thickness Gauge Technologies Driving Precision Measurement Innovation Across Industries
The electronic thickness gauge has emerged as a foundational tool across industries that demand precision measurement, from aerospace component validation to automotive coating inspection. Advances in sensor technology and data acquisition have elevated these gauges from simple thickness readers to sophisticated instruments capable of nondestructive evaluation. In sectors where material integrity and consistency are critical, manufacturers and quality assurance teams rely on these devices to ensure compliance with rigorous standards while minimizing waste and production delays. Consequently, electronic thickness gauges now occupy a central role in modern quality control workflows, enabling rapid, accurate assessments that underpin product reliability and safety.
Amidst this growing significance, the market for electronic thickness gauges continues to evolve rapidly. New entrants and established companies alike are integrating digital communications, cloud connectivity, and advanced analytics to differentiate their offerings. As a result, organizations face mounting pressure to stay ahead of technological developments and regulatory changes. This executive summary offers a comprehensive overview of the current landscape, highlights the most transformative shifts, and provides actionable insights into how best to align strategic priorities with emerging opportunities in precision measurement. By synthesizing industry drivers and challenges, we aim to equip decision-makers with the clarity needed to navigate an increasingly complex environment.
Examining How Technological Advancements and Industry 4.0 Are Transforming Electronic Thickness Gauges into Intelligent Quality Control Solutions
The landscape of electronic thickness gauges has been fundamentally altered by the convergence of Industry 4.0 concepts and the Internet of Things. Traditional standalone gauges are giving way to networked systems that transmit measurement data in real time to centralized quality management platforms. This shift toward connectivity enables predictive maintenance, as anomalies in coating or substrate thickness can trigger automated alerts before they lead to defects or downtimes.
Simultaneously, miniaturization of sensor elements and the integration of artificial intelligence algorithms have enhanced the capabilities of handheld and online measurement systems. AI-driven pattern recognition allows gauges to adapt to different surface textures and materials on the fly, improving measurement accuracy across heterogeneous substrates. Furthermore, advancements in laser and ultrasonic technologies have expanded the range of detectable materials and thicknesses, opening new application areas in composites manufacturing and advanced coatings. As these transformative shifts coalesce, stakeholders must reassess their measurement strategies, invest in interoperable architectures, and cultivate the digital expertise required to harness next-generation gauge solutions.
Analyzing the Cumulative Effects of 2025 United States Tariff Measures on Supply Chains Manufacturing Costs and Market Dynamics for Thickness Gauges
The introduction of new United States tariffs in 2025 has reshaped supply chain dynamics across the electronic thickness gauge value chain. Increased duties on imported sensor components and finished instruments have driven instrument providers to reevaluate sourcing strategies. Many suppliers have shifted production to local or tariff-free regions to mitigate cost pressures, thus fostering regional manufacturing hubs that better align with end-user demand in North America.
In parallel, end users have adjusted procurement practices to accommodate higher landed costs. Quality managers are exploring alternate materials and low-duty substitute components to maintain operational budgets without sacrificing measurement precision. At the same time, distributors and channel partners are offering comprehensive service agreements that bundle calibration and maintenance, helping customers spread costs over longer intervals. The net effect of the 2025 tariff adjustments has been a more localized supply ecosystem, a heightened focus on total cost of ownership, and accelerated collaboration among manufacturers, customs experts, and logistics providers to navigate evolving trade conditions.
Unveiling Critical Segmentation Patterns Revealing How Type Application End User Range Technology and Sales Channels Shape the Thickness Gauge Market
Deep insights into market segmentation reveal distinct growth vectors shaped by technology, application and user requirements. In terms of measurement modality, eddy current systems have solidified their position in metal thickness evaluation, while laser and optical instruments enable rapid, noncontact readings for transparent or painted surfaces and offer high resolution on smooth substrates. Ultrasonic gauges, by contrast, provide versatility for applications ranging from plastic and polymer to multilayer composites where optical methods fall short.
Application-driven distinctions further refine market dynamics. In the paint and coating domain, automotive coating inspection has become more rigorous as OEMs demand uniform film thickness for corrosion resistance and aesthetic quality. Industrial coating processes likewise benefit from inline measurement solutions that reduce rework. Paper and film markets rely on labeling gauges to ensure adhesive tolerances, whereas packaging substrates require homogeneous film thickness to balance strength and flexibility. Plastic and polymer inspections often utilize a blend of ultrasonic and optical systems to accommodate varying formulations and translucent materials.
End-user segments exhibit nuanced priorities according to their operational contexts. Aerospace suppliers insist on the tightest tolerances for both commercial airframes and defense components to assure reliability under extreme conditions. Automotive customers, whether in OEM lines or aftermarket service centers, value durability and portability in handheld devices. Construction inspectors deploy gauges on both commercial and residential projects to verify protective coatings that guard against environmental degradation. Manufacturing environments split between discrete parts makers and process-driven operations, each demanding different integration approaches. Oil and gas operators in upstream exploration add corrosion monitoring mandates, while downstream refiners track internal coating thickness in pipelines and vessels. Academic and government research institutions further extend the market by exploring novel materials and advanced measurement techniques.
Thickness range preferences create another layer of segmentation. Instruments tailored to very thin materials zero in on 0–2 mm or 2–10 mm subsurfaces, supporting electronics and thin-film coating processes. Mid-range solutions spanning 10–25 mm or 25–50 mm accommodate structural components in machinery or vehicle frames. Heavy-duty ultrasonic gauges rated for 50–75 mm and 75–100 mm suit thick composites and industrial equipment, while specialty transducers design for 100–200 mm or over 200 mm thickness address pipeline and large-scale fabrication tasks.
Technology platforms and sales channels intersect with these considerations. Handheld offerings, whether wired or wireless, emphasize ease of use and field portability. Offline bench instruments and desktop workstations cater to laboratory settings requiring high throughput. Online, in-process systems provide data logging and real-time monitoring for automated production lines. Direct manufacturer relationships and OEM partnerships coexist with authorized distributors and independent resellers, while expanding digital marketplaces and e-commerce sites create alternative paths for procurement. These overlapping segmentation layers illuminate the multifaceted nature of the electronic thickness gauge market.
This comprehensive research report categorizes the Electronic Thickness Gauge market into clearly defined segments, providing a detailed analysis of emerging trends and precise revenue forecasts to support strategic decision-making.
- Type
- Application
- End User
- Thickness Range
- Technology
- Sales Channel
Distilling Regional Nuances across the Americas Europe Middle East Africa and Asia Pacific to Highlight Divergent Trends in Gauge Adoption
Regional market nuances exert a profound influence on gauge adoption and technology integration strategies. In the Americas, robust manufacturing sectors in North America drive demand for both handheld and online measurement solutions. US-based OEMs and aftermarket service providers prioritize calibration accuracy and extended service networks, prompting suppliers to establish local repair centers and training programs. Latin American markets, by contrast, increasingly adopt portable devices for infrastructure and automotive maintenance, balancing cost constraints with performance requirements.
Within Europe, Middle East and Africa, regulatory harmonization and environmental mandates encourage the deployment of advanced thickness gauges for industries such as oil and gas, aerospace, and construction. European automotive OEMs leverage integrated measurement systems for on-line quality assurance, while Middle Eastern petrochemical operators underscore corrosion monitoring in pipeline networks. African resource-extraction operations prefer rugged handheld instruments capable of functioning in remote and harsh field conditions.
Asia-Pacific presents a diverse tapestry of demand drivers. Industrial powerhouses in China, Japan and South Korea invest heavily in high-precision laser and ultrasonic gauges to support semiconductor fabrication and automotive export lines. Southeast Asian nations emphasize cost-effective, entry-level handheld models to sustain growing infrastructure projects. Meanwhile, India’s expanding manufacturing base and government pushes for Make in India initiatives have spurred localized production of electronic gauges, fostering partnerships between international technology providers and regional distributors.
This comprehensive research report examines key regions that drive the evolution of the Electronic Thickness Gauge market, offering deep insights into regional trends, growth factors, and industry developments that are influencing market performance.
- Americas
- Europe, Middle East & Africa
- Asia-Pacific
Profiling Leading Industry Players to Illuminate Strategic Initiatives Innovation Pipelines and Competitive Differentiators in Thickness Gauge Space
Key players in the electronic thickness gauge market continuously innovate to maintain their competitive advantages. Established sensor manufacturers are expanding product portfolios with integrated software platforms that offer advanced analytics, reporting functions, and connectivity with enterprise resource planning systems. Meanwhile, equipment providers are forging strategic alliances with IoT and cloud service specialists to deliver turnkey solutions that streamline data ingestion and quality management for end users.
R&D investments have focused heavily on enhancing sensor accuracy, reducing measurement variability, and developing adaptive calibration routines. Companies have introduced modular designs that allow customers to upgrade transducers or add new measurement modes without replacing the entire instrument. Moreover, a trend toward subscription-based services is emerging, in which users pay recurring fees for ongoing software updates, remote diagnostics, and access to expanded data sets maintained on secure cloud networks.
Competitive differentiation also derives from after-sales support and global service footprints. Leading suppliers are bolstering training programs, offering accreditation courses for quality engineers, and creating virtual reality-based calibration simulations. These initiatives aim to mitigate downtime risks and ensure consistent measurement reliability. Finally, mergers and acquisitions have reshaped market structure, enabling some technology providers to integrate complementary competencies in nondestructive testing, optical measurement and materials characterization under unified corporate umbrellas.
This comprehensive research report delivers an in-depth overview of the principal market players in the Electronic Thickness Gauge market, evaluating their market share, strategic initiatives, and competitive positioning to illuminate the factors shaping the competitive landscape.
- Olympus Corporation
- Hitachi High-Tech Corporation
- Mitutoyo Corporation
- Fischer Technology GmbH
- Defelsko Corporation
- Elcometer Limited
- TQC Sheen BV
- DGH Technology, Inc.
- Suga Test Instruments Co., Ltd.
- C&M Digitals Private Limited
Delivering Strategic Action Frameworks to Empower Industry Leaders with Tactical Roadmaps for Investment Innovation and Sustainable Growth in Measurement Tech
Industry leaders can capitalize on emerging opportunities by adopting a multipronged strategic framework. Prioritizing connectivity and real-time data integration will be essential as manufacturers move toward fully automated quality ecosystems. Executives should evaluate current measurement infrastructures and partner with technology providers to pilot IoT-enabled online gauges that feed into advanced analytics platforms for predictive insights.
Supply chain diversification represents another critical priority. In response to evolving tariff landscapes and logistics challenges, companies should identify alternative sourcing regions while strengthening relationships with authorized distributors. Developing localized calibration and service capabilities not only reduces lead times but also fosters customer loyalty through responsive technical support.
Expanding end-user engagement through targeted training and service models can unlock new revenue streams. By launching certified operator programs and immersive training modules, measurement solution providers enhance the value proposition of their instruments and embed themselves deeper into customer processes. Building strategic partnerships with OEMs and integrators will also streamline the integration of thickness gauging into broader manufacturing execution systems.
Finally, organizations must stay attuned to regulatory shifts and standards evolution. Dedicating resources to standards committees and industry consortiums enables early visibility into upcoming changes in coating, substrate and nondestructive testing specifications. This proactive stance ensures that product roadmaps remain aligned with end-user requirements and that compliance becomes a differentiating advantage rather than an operational burden.
Detailing Rigorous Research Framework Integrating Qualitative Interviews Quantitative Surveys and Competitive Benchmarking to Ensure Comprehensive Market Analysis
This analysis combines robust qualitative and quantitative research methods to ensure a comprehensive understanding of the electronic thickness gauge market. Secondary research drew upon a wide array of publicly available sources, including patent filings, regulatory standards documentation and white papers from industry associations. These materials provided foundational context on historical trends, technology evolution and regulatory drivers.
Primary research involved in-depth interviews with senior executives at gauge manufacturers, quality managers in key end-user industries, channel partners and calibration service providers. These interviews yielded nuanced perspectives on adoption challenges, emerging feature requirements and the strategic priorities guiding next-generation product development. To complement the qualitative inputs, a survey of engineers and procurement specialists across aerospace, automotive, construction and process-driven manufacturing operations gathered quantitative data on feature preferences, pain points and purchasing dynamics.
Triangulation of findings ensured that insights were cross-validated across multiple sources and stakeholder groups. Data points were further assessed through competitive benchmarking to map product capabilities, pricing strategies and service offerings across leading vendors. Finally, a dedicated review panel comprising subject-matter experts in nondestructive testing and materials science vetted the analysis for technical accuracy and relevance, ensuring that the final conclusions reflect both market realities and technological opportunities.
Explore AI-driven insights for the Electronic Thickness Gauge market with ResearchAI on our online platform, providing deeper, data-backed market analysis.
Ask ResearchAI anything
World's First Innovative Al for Market Research
Synthesizing Insights to Chart the Future Trajectory of Electronic Thickness Gauges Amidst Evolving Technologies and Market Transformations
The convergence of digital transformation, trade policy shifts and evolving end-user expectations signals a new era for electronic thickness gauges. Stakeholders who embrace connectivity, data-driven decision making and service innovation will be best positioned to capture the value unlocked by advanced measurement capabilities. In this context, measurement accuracy is no longer a standalone metric but a component of a broader ecosystem encompassing predictive maintenance, process optimization and compliance management.
Regional disparities in regulatory environments and manufacturing maturity will continue to shape adoption pathways, demanding tailored go-to-market strategies and localized support networks. At the same time, ongoing technological advancements in sensor materials, AI algorithms and cloud computing will push the boundaries of what thickness gauges can achieve in terms of speed, precision and adaptability.
By synthesizing the insights presented here, industry participants can align their product roadmaps, channel strategies and service models to the most compelling trends. Actors who proactively navigate tariff challenges, diversify supply chains and invest in end-user training will emerge as market leaders. Ultimately, the future trajectory of electronic thickness gauges will be defined by a blend of innovation rigor, operational agility and customer-centric execution.
This section provides a structured overview of the report, outlining key chapters and topics covered for easy reference in our Electronic Thickness Gauge market comprehensive research report.
- Preface
- Research Methodology
- Executive Summary
- Market Overview
- Market Dynamics
- Market Insights
- Cumulative Impact of United States Tariffs 2025
- Electronic Thickness Gauge Market, by Type
- Electronic Thickness Gauge Market, by Application
- Electronic Thickness Gauge Market, by End User
- Electronic Thickness Gauge Market, by Thickness Range
- Electronic Thickness Gauge Market, by Technology
- Electronic Thickness Gauge Market, by Sales Channel
- Americas Electronic Thickness Gauge Market
- Europe, Middle East & Africa Electronic Thickness Gauge Market
- Asia-Pacific Electronic Thickness Gauge Market
- Competitive Landscape
- ResearchAI
- ResearchStatistics
- ResearchContacts
- ResearchArticles
- Appendix
- List of Figures [Total: 30]
- List of Tables [Total: 2154 ]
Seize the Opportunity to Access In Depth Market Intelligence and Propel Your Thickness Gauge Strategy with Personalized Insights from Ketan Rohom
Ready to deepen your understanding of the electronic thickness gauge market and secure your competitive advantage? Reach out to Ketan Rohom, Associate Director of Sales & Marketing, to request a personalized briefing or to purchase the full market research report. Our team will work closely with you to tailor insights to your strategic priorities, highlight the most relevant trends for your business, and provide dedicated support throughout your decision-making process. By partnering directly with Ketan, you ensure access to the latest data, expert analysis, and actionable recommendations designed to accelerate your growth in the precision measurement industry. Don’t miss the chance to transform uncertainty into opportunity and to position your organization at the forefront of innovation in electronic thickness measurement technologies.
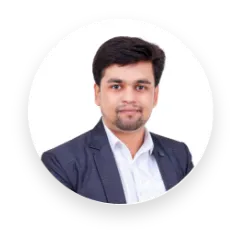
- When do I get the report?
- In what format does this report get delivered to me?
- How long has 360iResearch been around?
- What if I have a question about your reports?
- Can I share this report with my team?
- Can I use your research in my presentation?