The Electronics Conformal Coatings Market size was estimated at USD 1.11 billion in 2024 and expected to reach USD 1.17 billion in 2025, at a CAGR 5.87% to reach USD 1.56 billion by 2030.

Embracing the Future: An Introduction to Electronics Conformal Coatings
Electronics conformal coatings serve as the invisible guardians of modern electronic assemblies, shielding critical components from moisture, dust, chemicals, and thermal stress. As devices become increasingly miniaturized and integrated into demanding environments-from automotive sensors operating under high temperature cycles to medical implants requiring biocompatibility-the need for reliable protective layers has never been greater. This executive summary offers an authoritative overview of the latest developments, emerging technologies, and strategic imperatives that define the conformal coatings landscape today.
The rapid evolution of materials science and process engineering has given rise to novel formulations that balance performance with sustainability, while advanced application methods enhance precision and throughput. At the same time, shifting regulatory frameworks and global trade dynamics introduce both challenges and opportunities for manufacturers, suppliers, and end-users. This document synthesizes critical insights on transformative trends, the impact of recent trade policies, granular segmentation analysis, and regional market drivers.
By delivering a concise, multi-dimensional perspective, this summary equips industry executives and technical leaders with the knowledge required to make informed investment decisions, optimize production workflows, and anticipate future demand patterns. In the pages that follow, we delve into the factors shaping the conformal coatings market’s trajectory and outline strategic pathways to foster resilience and growth in a rapidly changing environment.
Shifting Currents in the Conformal Coatings Landscape
The conformal coatings sector is undergoing a period of profound transformation driven by converging technological, environmental, and market forces. Innovative resin chemistries paired with advanced delivery systems are enabling ultra-thin, uniform films that meet stringent reliability requirements in miniature electronic devices. Concurrently, the rise of additive manufacturing and 3D-printed circuitry calls for novel coatings capable of conforming to complex geometries without compromising adhesion or dielectric strength.
Sustainability imperatives are reshaping product development strategies, with stakeholders increasingly prioritizing low-VOC formulations and recyclable packaging. Regulatory momentum toward more rigorous environmental standards is accelerating the adoption of moisture and UV-curable systems that minimize solvent use and energy consumption. In parallel, the proliferation of connected devices in Internet of Things ecosystems is driving demand for coatings that combine robust electromagnetic interference shielding with corrosion resistance.
These transformative shifts are compelling manufacturers to reexamine their R&D investments, collaborate with specialty chemical providers, and leverage digital monitoring solutions for in-line quality assurance. As the market landscape recalibrates, companies that anticipate the interplay between emerging application requirements and evolving regulatory norms will secure a competitive edge. The ensuing analysis unpacks these forces and their implications for stakeholders across the value chain.
Navigating the Ripple Effects of 2025 U.S. Tariffs
In early 2025, the United States implemented a new tranche of tariffs targeting raw materials and intermediate chemicals integral to conformal coatings production. These measures have elevated input costs for resin suppliers and dispersed added expenses throughout the value chain. Original equipment manufacturers, in response, are renegotiating long-term contracts and exploring alternative sourcing strategies, including supply-chain diversification across Southeast Asia and Latin America.
The tariff impact extends beyond immediate cost inflation. It has stimulated conversations around near-shoring of component fabrication to mitigate exposure to trade disruptions, prompting increased investment in domestic capacity expansion. Simultaneously, some suppliers have accelerated material innovation to formulate blends that rely less on tariff-impacted inputs without sacrificing performance.
Equipment manufacturers are also evaluating process optimization techniques-such as adjunct curing technologies and real-time thickness monitoring-to improve yield and offset rising overheads. In the aftermarket segment, service providers face margin compression, driving a shift toward value-added offerings like customized coatings and predictive maintenance solutions.
This chapter examines the multifaceted repercussions of U.S. tariff policies on pricing structures, supply-chain resilience, and strategic investment decisions, and highlights how industry participants are adapting to maintain competitiveness in a more protectionist trade environment.
Key Segmentation Dynamics Driving Coatings Demand
A nuanced understanding of the conformal coatings market emerges when examined through multiple segmentation lenses. In terms of coating material, the spectrum spans versatile acrylic formulations prized for their rapid curing and reworkability, durable epoxy systems favored in harsh environments, ultra-thin parylene films offering superior barrier properties, flexible polyurethane layers, silicone chemistries designed for high thermal tolerance, and emerging styrenated block-copolymer blends that bridge performance with cost efficiency.
Application method introduces another dimension of strategic choice, where brush coating remains indispensable for touch-up operations, while dip coating excels in high-volume batch processes. Selective coating techniques deliver precision coverage in complex assemblies, and spray coating meets the demands of automated, inline manufacturing. Each method influences throughput, material utilization, and end-product consistency.
Thickness range further refines market dynamics: coatings applied at less than 25 microns cater to ultra-miniaturized electronics, mid-range films between 25 and 100 microns represent the bulk of general-purpose protection, and specialized applications requiring over 100 microns address high-voltage or severe environment demands. Curing system selection-whether via evaporative, moisture, thermal, or UV processes-affects energy consumption, cycle times, and compatibility with temperature-sensitive substrates.
Finally, end-user industries encompass a broad array of sectors, including aerospace and defense, automotive and transportation, consumer electronics, energy and utilities, healthcare and life sciences, information technology and telecommunication, as well as general manufacturing. This granular segmentation analysis illuminates demand patterns and tactical imperatives across materials, processes, and end markets.
This comprehensive research report categorizes the Electronics Conformal Coatings market into clearly defined segments, providing a detailed analysis of emerging trends and precise revenue forecasts to support strategic decision-making.
- Coating Material
- Application Method
- Thickness Range
- Curing System
- End-User
Mapping Regional Strengths in Conformal Coatings
Regional market performance reveals distinct drivers and challenges across the Americas, Europe Middle East and Africa, and Asia-Pacific. In the Americas, robust investment in aerospace, defense, and electric vehicle manufacturing underpins steady growth, with manufacturers emphasizing domestic sourcing and stringent quality standards. Emerging hubs in Mexico and Brazil further diversify supply-chain geographies, while the U.S. market continues to prioritize regulatory compliance and technological differentiation.
Across Europe Middle East and Africa, stringent environmental regulations and sustainability targets are accelerating the transition to low-emission materials and energy-efficient curing systems. Research collaborations between European specialty chemical firms and academic institutions have produced innovative, bio-derived formulations. Simultaneously, growing defense expenditures in the Middle East are fueling demand for high-reliability coatings capable of withstanding extreme climates.
In the Asia-Pacific region, rapid industrialization, expanding consumer electronics manufacturing, and increased spending on renewable energy infrastructure drive substantial demand for conformal coatings. China’s vast production ecosystem remains the epicenter for cost-competitive manufacturing, while Japan and South Korea focus on high-performance, next-generation materials. Southeast Asian nations are emerging as alternative production sites due to favorable trade agreements and government incentives.
This regional overview underscores the importance of tailoring strategies to local market conditions, regulatory frameworks, and end-user requirements.
This comprehensive research report examines key regions that drive the evolution of the Electronics Conformal Coatings market, offering deep insights into regional trends, growth factors, and industry developments that are influencing market performance.
- Americas
- Europe, Middle East & Africa
- Asia-Pacific
Key Company Insights Shaping Market Leadership
The competitive landscape is defined by a mix of global chemical conglomerates, specialized coating providers, and agile niche players. Industry leaders differentiate through extensive R&D pipelines, expansive product portfolios, and vertically integrated supply-chain models that ensure quality control and cost efficiencies. Breakthroughs in polymer chemistry and curing technologies often originate from dedicated innovation centers operated by large-scale manufacturers.
Mid-tier and emerging companies capitalize on market gaps by offering customizable solutions, rapid prototyping services, and local technical support. Partnerships between application equipment manufacturers and chemical suppliers foster co-development of fully integrated turnkey systems, enabling rapid adoption of new formulations on existing production lines. Strategic alliances with research institutions further accelerate the introduction of bio-based and low-VOC coatings.
Mergers and acquisitions remain a key growth lever, as players seek to broaden geographic reach, complement complementary portfolios, and secure proprietary technologies. Simultaneously, small to medium-sized enterprises carve out niches by focusing on specialized applications such as medical-grade coatings, high-voltage dielectric insulation, and polymeric encapsulation for harsh environments.
Across tiers, success hinges on the ability to anticipate regulatory shifts, invest in digital quality control platforms, and foster collaborative ecosystems that bring together formulators, applicators, and end-users under a unified vision of reliability and sustainability.
This comprehensive research report delivers an in-depth overview of the principal market players in the Electronics Conformal Coatings market, evaluating their market share, strategic initiatives, and competitive positioning to illuminate the factors shaping the competitive landscape.
- Aalpha Conformal Coatings
- AI Technology, Inc.
- Avantor, Inc.
- Chase Corporation
- CHT Germany GmbH
- Conins Pune
- CSL Silicones Inc. by PETRONAS Chemicals Group Berhad
- Dymax Corporation
- ELANTAS GmbH by ALTANA Group
- Electrolube
- H.B Fuller Company
- Henkel AG & Co. KGaA
- Illinois Tool Works Inc.
- MG Chemicals
- Micron Aerosol by Deepak Industries
- Miller-Stephenson Chemical, Inc.
- Momentive Performance Materials Inc.
- MR BOND POLYCHEM
- RS Components & Controls (I) Ltd.
- Shanghai Huitian New Material Co., Ltd.
- Shin-Etsu Chemical Co., Ltd.
- Specialty Coating Systems Inc. by KISCO Ltd.
- The Dow Chemical Company
- Vinsa Chemicals Private Limited
Actionable Strategies to Lead the Conformal Coatings Sector
Industry leaders must pursue a multifaceted strategy to capitalize on emerging opportunities and mitigate risks. Prioritizing investments in sustainable chemistries and energy-efficient curing platforms not only addresses regulatory pressures but also resonates with the growing demand for eco-friendly solutions. Simultaneously, integrating digital process controls and real-time analytics can optimize material usage, improve consistency, and reduce downtime.
Cultivating strategic partnerships across the value chain-from chemical innovators to equipment manufacturers and end-user integrators-will accelerate co-development of tailored solutions and shorten time to market. Expanding technical support networks and offering application training workshops further enhances customer loyalty and unlocks upsell and cross-sell potential. Additionally, companies should explore flexible contract manufacturing arrangements and geographic diversification to bolster supply-chain resilience against tariff fluctuations and geopolitical disruptions.
Talent management represents another critical pillar; organizations that attract polymer scientists, application engineers, and data analysts position themselves to lead next-generation advancements. Establishing cross-functional innovation hubs encourages collaboration and rapid iteration. Finally, maintaining rigorous compliance frameworks and proactive engagement with regulatory bodies will smooth market entry and minimize product approval timelines.
By executing these targeted recommendations, industry participants can fortify their competitive positioning, accelerate innovation pipelines, and secure sustainable growth in the evolving conformal coatings ecosystem.
Methodology Behind the Market Analysis
This market analysis is founded on a rigorous, multi-stage research methodology designed to ensure accuracy, relevance, and comprehensiveness. Initial desk research aggregated public and proprietary sources, including industry journals, technical papers, regulatory filings, and corporate disclosures. Secondary data formed the backbone of the competitive landscape and historical trend analysis.
Primary research encompassed in-depth interviews with key stakeholders, including formulators, major OEM procurement officers, application equipment specialists, and end-user engineering teams. These discussions provided real-world perspectives on material performance, process challenges, and strategic priorities. Quantitative data were triangulated using market mapping techniques and validated against public financial reports.
Segmentation models were constructed to reflect distinct market dimensions-such as coating chemistry, application method, thickness range, curing system, and end-use verticals-enabling granular demand profiling. Regional analyses incorporated macroeconomic indicators, trade policies, and infrastructure developments. A series of expert panel workshops further refined insights and stress-tested emerging scenarios.
Quality assurance measures included peer reviews by subject-matter experts, cross-validation with external data providers, and iterative feedback loops with interview participants. This structured approach ensures that the findings presented herein deliver actionable intelligence aligned with the highest standards of market research integrity.
Explore AI-driven insights for the Electronics Conformal Coatings market with ResearchAI on our online platform, providing deeper, data-backed market analysis.
Ask ResearchAI anything
World's First Innovative Al for Market Research
Concluding Perspectives on Electronics Conformal Coatings
The landscape of electronics conformal coatings is characterized by dynamic innovation, regulatory evolution, and shifting trade patterns. Through detailed segmentation and regional assessments, this report has illuminated the key drivers influencing material and process choices across diverse end markets. The 2025 U.S. tariffs have underscored the importance of supply-chain agility, while advancements in sustainable chemistries and digital quality control promise to redefine performance benchmarks.
Successful players will be those that align R&D initiatives with emerging application requirements, cultivate cross-industry collaborations, and invest in robust compliance and risk-mitigation frameworks. Organizations that adopt the recommended strategies-ranging from sustainable material development to enhanced process analytics-will be well-positioned to capture growth in aerospace, automotive, consumer electronics, energy, and healthcare markets.
As the conformal coatings arena continues to evolve, staying informed about global trade developments, material breakthroughs, and application innovations remains essential for decision-makers. The insights provided in this executive summary are intended to guide strategic planning, inform investment priorities, and support operational excellence.
By synthesizing the latest market intelligence and expert perspectives, this document equips stakeholders with a clear vision of the opportunities and challenges that lie ahead in the conformal coatings domain.
This section provides a structured overview of the report, outlining key chapters and topics covered for easy reference in our Electronics Conformal Coatings market comprehensive research report.
- Preface
- Research Methodology
- Executive Summary
- Market Overview
- Market Dynamics
- Market Insights
- Cumulative Impact of United States Tariffs 2025
- Electronics Conformal Coatings Market, by Coating Material
- Electronics Conformal Coatings Market, by Application Method
- Electronics Conformal Coatings Market, by Thickness Range
- Electronics Conformal Coatings Market, by Curing System
- Electronics Conformal Coatings Market, by End-User
- Americas Electronics Conformal Coatings Market
- Europe, Middle East & Africa Electronics Conformal Coatings Market
- Asia-Pacific Electronics Conformal Coatings Market
- Competitive Landscape
- ResearchAI
- ResearchStatistics
- ResearchContacts
- ResearchArticles
- Appendix
- List of Figures [Total: 26]
- List of Tables [Total: 245 ]
Secure Your Market Edge by Contacting Ketan Rohom
Secure unparalleled insights into the world of electronics conformal coatings by reaching out to Ketan Rohom, Associate Director of Sales & Marketing. Ketan brings a deep understanding of market dynamics and client needs, ensuring that your organization gains actionable intelligence to drive innovation and competitiveness. By engaging directly with him, you can customize the scope of the report to focus on the most critical trends, regions, and segments that matter to your strategic objectives.
Don’t miss the opportunity to equip your team with the comprehensive analysis required to navigate regulatory changes, emerging technologies, and evolving end-user demands. Contact Ketan today to arrange a detailed consultation and secure your copy of the in-depth market research report that will empower your decision-making and accelerate growth in the conformal coatings industry.
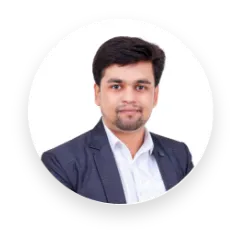
- How big is the Electronics Conformal Coatings Market?
- What is the Electronics Conformal Coatings Market growth?
- When do I get the report?
- In what format does this report get delivered to me?
- How long has 360iResearch been around?
- What if I have a question about your reports?
- Can I share this report with my team?
- Can I use your research in my presentation?