The End-of-line Packaging Market size was estimated at USD 5.58 billion in 2024 and expected to reach USD 5.98 billion in 2025, at a CAGR 6.98% to reach USD 8.36 billion by 2030.

Setting the Stage for Transformative Advancements in End-of-Line Packaging to Elevate Operational Efficiency and Sustainability
In a rapidly evolving manufacturing landscape, end-of-line packaging has become a cornerstone for optimizing operational efficiency and enhancing product quality. Stakeholders across industries are increasingly recognizing that packaging is no longer a mere logistical necessity but a strategic function that underpins brand reputation, cost management, and sustainability goals. As global supply chains face mounting pressures-from material shortages to regulatory mandates-companies are compelled to reimagine their packaging strategies to maintain resilience and deliver consistent value to customers.
This executive summary sets the stage for a deep exploration of the forces driving transformation in end-of-line packaging. It captures critical developments in automation technologies, highlights the multifaceted impacts of recent tariff policies, and distills key segmentation insights that inform targeted investments. By weaving together regional dynamics and competitive intelligence, this analysis offers a cohesive narrative designed to guide decision makers toward actionable recommendations. Through this lens, stakeholders will gain a comprehensive understanding of the current landscape and a clear vision for future-proofing their packaging operations.
Recognizing Pivotal Shifts Reshaping the End-of-Line Packaging Landscape Driven by Automation and Sustainability Imperatives
The landscape of end-of-line packaging is undergoing a profound shift, driven by the relentless march of automation and the imperative for sustainable operations. As manufacturers adopt advanced robotics, vision-guided systems, and programmable controls, legacy manual processes are being supplanted by solutions that deliver unmatched speed, precision, and repeatability. This transition is not only enhancing throughput but also reducing waste and downtime, thereby driving significant cost savings and environmental benefits.
Concurrent with the rise of automation, industry stakeholders are placing sustainability at the forefront of packaging decisions. Material innovations-such as lightweighting, recycled substrates, and compostable alternatives-are gaining traction as companies seek to meet consumer demands for eco-friendly products and adhere to stringent regulatory frameworks. Furthermore, integrated data analytics and traceability systems are enabling end-to-end visibility, empowering organizations to monitor performance metrics in real time. These converging trends underscore a pivotal moment in which technological prowess and environmental stewardship must align to shape the future of packaging.
Examining the Cumulative Implications of Recent United States Tariffs on End-of-Line Packaging Operations and Supply Chains
In 2025, the cumulative effect of newly imposed United States tariffs has reverberated throughout end-of-line packaging operations. Manufacturers reliant on imported components-from advanced robotic arms to specialized wrapping films-have faced escalating input costs, leading many to reevaluate vendor relationships and sourcing strategies. As a direct consequence, several operations have initiated nearshoring efforts, relocating portions of their supply chain to mitigate further tariff exposure and safeguard production continuity.
Moreover, the tariffs have catalyzed deeper collaboration between packaging equipment providers and material suppliers, as companies seek bundled solutions that balance cost predictability with performance. This environment has prompted a wave of contract renegotiations and consolidated procurement frameworks designed to streamline material flow and buffer against future policy fluctuations. As such, while tariff actions introduced short-term disruptions, they have also accelerated strategic adaptations that promise to enhance long-term resilience and provide a foundation for sustained innovation.
Uncovering Critical Segmentation Insights by Packaging Type Material End User Industry and Automation Level to Inform Strategy
Delineating the market through the lens of packaging type reveals a spectrum of specialized processes. Case packing operations are subdivided between pick-and-place mechanisms-where Cartesian and delta robots handle precise positioning-and robotic case packers that employ SCARA and six-axis configurations for complex arrangements. Palletizing landscapes range from conventional lines featuring mechanical and semi-automatic palletizers to fully automated robot-based systems, with ABB and Fanuc units dominating sophisticated deployments. In shrink bundling, heat guns and heat tunnels serve distinct throughput needs, with automatic and manual gun variants complementing shrink tunnels and sleeve applicators in high-volume contexts. Stretch wrapping solutions encompass rotary and turntable applications, differentiating between pre-stretch and post-stretch rotary posts as well as ring and table turntable variants to suit diverse load profiles.
When considering end user industries, the breadth of applications spans agrochemicals-supporting fertilizer and pesticide distribution-to high-precision medical devices in diagnostic and surgical settings. Bakery and confectionery producers leverage tailored packaging for bread and chocolate segments, while the electronics sector differentiates desktop and laptop enclosures. Personal care brands deploy specialized haircare and skincare packaging formats, and the dairy industry focuses on cheese and milk preservation. Petrochemical enterprises manage ethylene and propylene shipments, pharmaceutical manufacturers address injectable and solid dosage stability, and smartphone producers deliver distinct Android and iOS device configurations.
Material segmentation adds another dimension to strategic decision making. Aluminum substrates-categorized into foil and sheet-are prized for barrier performance, while corrugated solutions segment between single-wall and double-wall boards for load-bearing. Polyethylene selections weigh the benefits of high-density and low-density resins, and polypropylene applications differentiate between biaxially-oriented and cast-based films. Solid board materials include folding box and liquid packaging boards tailored for rigid or liquid containment, and steel variants range from carbon steel to stainless steel alloys to meet strength and hygiene requirements.
Examining automation levels further refines the market perspective. Manual operations persist in low-volume or highly variable contexts, whereas robotic systems bifurcate into programmable stations optimized for repeatable tasks and vision-guided assemblies that adapt to dynamic input. Semi-automated workflows bridge the gap with semi-automatic packers and wrappers, offering a balanced approach for mid-tier throughput and cost considerations. This multi-layered segmentation framework empowers stakeholders to pinpoint the precise combination of process, industry application, material choice, and automation sophistication that aligns with their strategic objectives.
This comprehensive research report categorizes the End-of-line Packaging market into clearly defined segments, providing a detailed analysis of emerging trends and precise revenue forecasts to support strategic decision-making.
- Packaging Type
- End User Industry
- Material
- Automation Level
Navigating Regional Dynamics Across Americas Europe Middle East Africa and Asia-Pacific to Capitalize on Diverse Market Opportunities
Across the Americas, established manufacturing hubs in North America and emerging centers in Latin America present a juxtaposition of mature operational expertise and rapid capacity expansion. In the United States and Canada, regulatory compliance and sustainability benchmarks drive high adoption rates for recycled materials and energy-efficient equipment. Further south, countries such as Mexico and Brazil are investing in infrastructure upgrades to support growing consumer markets, creating a fertile environment for integrated packaging solutions.
In Europe, Middle East, and Africa, the confluence of stringent environmental regulations and diverse economic landscapes is shaping unique packaging requirements. Western European markets emphasize circular economy principles, prompting substantial investment in reusable and returnable packaging models. Meanwhile, the Gulf Cooperation Council states are channeling capital into state-of-the-art manufacturing parks that prioritize digitalized production lines. Across Africa, rapid urbanization and evolving retail formats underscore the need for scalable, cost-effective end-of-line technologies that can adapt to fluctuating demand patterns.
Asia-Pacific dynamics are defined by a blend of high-volume manufacturing and innovation-driven markets. China maintains its position as a global epicenter for automation deployment, undertaking large-scale rollouts of robotic palletizing and integrated vision systems. Japan and South Korea continue to pioneer micro-robotics and precision packaging for sensitive electronics and medical devices. Southeast Asian economies, including India and Vietnam, are ramping up capacity through strategic joint ventures, with an emphasis on modular packaging lines that can be swiftly reconfigured to handle diverse product portfolios.
This comprehensive research report examines key regions that drive the evolution of the End-of-line Packaging market, offering deep insights into regional trends, growth factors, and industry developments that are influencing market performance.
- Americas
- Europe, Middle East & Africa
- Asia-Pacific
Exploring Competitive Landscape Highlights for Leading Providers to Identify Strategic Differentiators and Growth Vectors
Leading equipment manufacturers distinguish themselves through deep expertise in delivering turnkey automation packages. Their portfolios often combine state-of-the-art robotic arms, proprietary control software, and on-site implementation services that guarantee rapid time to value. In parallel, material innovators are forging partnerships to develop next-generation substrates with enhanced barrier properties, recyclability credentials, and compatibility with high-speed processing equipment.
System integrators and technology consultants play a critical role by bridging the gap between equipment vendors and end users. They architect holistic solutions that synthesize legacy assets with new automation modules, ensuring seamless data exchange and minimizing operational disruptions. Complementing these established players, agile startups are emerging with niche offerings-such as AI-driven vision inspection and modular conveyor platforms-that address specific pain points in defect detection and throughput variability.
Furthermore, collaborative consortiums comprising manufacturers, research institutes, and sustainability advocates are influencing industry roadmaps. These alliances facilitate standardization efforts, promote interoperability across different equipment brands, and accelerate the development of circular packaging ecosystems. By mapping the competitive landscape in this way, decision makers can identify partnership channels that amplify core competencies and unlock new revenue streams.
This comprehensive research report delivers an in-depth overview of the principal market players in the End-of-line Packaging market, evaluating their market share, strategic initiatives, and competitive positioning to illuminate the factors shaping the competitive landscape.
- Krones AG
- Syntegon Technology GmbH
- GEA Group Aktiengesellschaft
- Coesia S.p.A.
- KHS GmbH
- ProMach, Inc.
- MULTIVAC GmbH & Co. KG
- IMA S.p.A.
- Marchesini Group S.p.A.
- OPTIMA packaging group GmbH
Delivering Actionable Recommendations to Drive Innovation Maximize Efficiency and Enhance Competitive Positioning in Packaging
To succeed in today’s dynamic packaging environment, organizations should prioritize investments in scalable automation technologies that can adapt to evolving product mixes. Conducting modular pilot programs accelerates risk mitigation and enables rapid validation of return on investment, paving the way for broader system rollouts. Additionally, forging strategic alliances with material suppliers can secure preferential access to innovative substrates and support co-development initiatives aimed at optimizing end-to-end performance.
Beyond technology, companies must cultivate cross-functional teams that unite operations, procurement, sustainability, and IT stakeholders. This integrated governance model fosters a holistic view of packaging programs, driving data-driven decision making and ensuring alignment with corporate objectives. Moreover, establishing continuous improvement processes-anchored by real-time analytics and predictive maintenance-can reduce unplanned downtime and enhance overall equipment effectiveness.
Finally, industry leaders should adopt regionally tailored strategies that account for local regulations, infrastructure maturity, and workforce capabilities. By aligning capital expenditure plans with market-specific opportunities-such as circular economy incentives in Europe or automation grants in North America-organizations can optimize resource allocation and maximize returns on deployment. Embracing these recommendations will position companies to navigate uncertainty and capitalize on emerging trends in end-of-line packaging.
Detailing Rigorous Research Methodology Leveraging Primary Secondary Data and Multivariate Analysis for Robust Market Insights
This analysis draws upon a robust research methodology designed to deliver actionable insights with clarity and precision. Primary data collection included in-depth interviews with packaging engineers, operations managers, and sustainability leaders across diverse industry verticals. These firsthand perspectives were complemented by a comprehensive review of regulatory filings, patent disclosures, and technology roadmaps to validate emerging trends and innovation trajectories.
Secondary research encompassed an exhaustive examination of industry publications, white papers, and academic journals, as well as the consolidation of best practices gleaned from leading manufacturing and consumer goods organizations. Quantitative analysis techniques-such as cross-segment correlation studies and regional demand modeling-were applied to refine segmentation assumptions and ensure the reliability of findings. Throughout the study, data integrity was maintained through triangulation methods and rigorous peer review, establishing a foundation of credibility that supports strategic decision making.
Explore AI-driven insights for the End-of-line Packaging market with ResearchAI on our online platform, providing deeper, data-backed market analysis.
Ask ResearchAI anything
World's First Innovative Al for Market Research
Synthesis of Core Findings and Strategic Considerations to Guide Decision Makers Toward Successful Packaging Transformations
The convergence of automation, material innovation, and regulatory influences has created a pivotal moment for end-of-line packaging. By synthesizing segmentation insights with regional dynamics, decision makers can craft strategies that balance efficiency, sustainability, and cost-effectiveness. The competitive landscape underscores the importance of strategic partnerships, integrated solution design, and continuous adaptation to maintain a leadership edge.
Ultimately, organizations that systematically apply the actionable recommendations outlined in this summary will be better positioned to navigate tariff fluctuations, capitalize on regional growth opportunities, and drive transformative improvements in their packaging operations. As market conditions evolve, maintaining a forward-looking posture-rooted in data-driven analysis and cross-sector collaboration-will be essential for sustaining momentum and achieving long-term success.
This section provides a structured overview of the report, outlining key chapters and topics covered for easy reference in our End-of-line Packaging market comprehensive research report.
- Preface
- Research Methodology
- Executive Summary
- Market Overview
- Market Dynamics
- Market Insights
- Cumulative Impact of United States Tariffs 2025
- End-of-line Packaging Market, by Packaging Type
- End-of-line Packaging Market, by End User Industry
- End-of-line Packaging Market, by Material
- End-of-line Packaging Market, by Automation Level
- Americas End-of-line Packaging Market
- Europe, Middle East & Africa End-of-line Packaging Market
- Asia-Pacific End-of-line Packaging Market
- Competitive Landscape
- ResearchAI
- ResearchStatistics
- ResearchContacts
- ResearchArticles
- Appendix
- List of Figures [Total: 26]
- List of Tables [Total: 2950 ]
Engage with Ketan Rohom to Access Advanced Packaging Intelligence That Accelerates Your Operational Excellence and Strategic Growth
For organizations poised to capitalize on the latest insights in end-of-line packaging, the next step is simple yet transformative. Reach out to Ketan Rohom, Associate Director of Sales & Marketing, to gain immediate access to the full report and unlock detailed strategies for automation, regional expansion, and material innovation. Engaging with this comprehensive analysis ensures your leadership team is equipped with data-driven recommendations and actionable intelligence that drive efficiency and competitiveness.
Act now to schedule a customized briefing and explore tailored solutions that address your unique operational challenges. By partnering with Ketan, you gain direct guidance on implementing best practices, navigating tariff impacts, and leveraging segmentation insights to refine your roadmap. Secure your copy today to stay ahead of emerging trends and lead the industry with confidence.
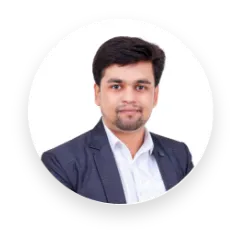
- How big is the End-of-line Packaging Market?
- What is the End-of-line Packaging Market growth?
- When do I get the report?
- In what format does this report get delivered to me?
- How long has 360iResearch been around?
- What if I have a question about your reports?
- Can I share this report with my team?
- Can I use your research in my presentation?