Introduction to Epoxy Resin in Electrical Insulation
Epoxy resins have emerged as indispensable materials in electrical insulation, combining exceptional mechanical strength with outstanding dielectric properties. As electronic systems become increasingly complex and power-dense, the need for reliable insulation solutions has never been greater. In this context, epoxy resin formulations designed for electrical applications deliver critical performance benefits, including high thermal stability, low moisture absorption, and resistance to corona discharge. These characteristics ensure long-term reliability in motors, transformers, circuit breakers, and cable systems.
Innovations in resin chemistry have further enhanced performance, with tailored molecular structures that offer improved adhesion, reduced cure temperatures, and tunable viscosity profiles. Such advancements enable manufacturers to optimize processing workflows, minimize defects, and achieve thinner insulation layers without sacrificing durability. Moreover, regulatory pressures on energy efficiency and safety standards are driving wider adoption of epoxy-based insulation systems, particularly in high-voltage and renewable energy sectors.
Against this backdrop, this executive summary provides an in-depth exploration of the transformative shifts influencing the epoxy resin market for electrical insulation. It examines the ripple effects of new trade policies, dissects key segmentation trends, highlights regional dynamics, and profiles leading companies. Finally, it delivers actionable guidance for decision-makers seeking to capitalize on emerging opportunities and navigate potential disruptions.
Transformative Shifts Reshaping the Epoxy Resin Landscape
The landscape of epoxy resin for electrical insulation is undergoing profound transformation, fueled by rapid technological advancements and shifting end-use requirements. Advances in formulation science now enable the development of flexible epoxies that resist UV degradation and impact damage, alongside rigid systems optimized for potting and encapsulation applications requiring thermally conductive and electrically insulative properties. These material breakthroughs are redefining performance benchmarks, enabling thinner, lighter, and more efficient insulation architectures.
Furthermore, the advent of high-voltage renewable energy infrastructure and electric mobility has accelerated demand for epoxy solutions with enhanced thermal management capabilities. In response, manufacturers are leveraging nanotechnology and specialized fillers to achieve superior heat dissipation without compromising dielectric strength. At the same time, digitalization of production lines is enhancing quality control-real-time monitoring of viscosity, cure kinetics, and temperature profiling ensures consistent batch-to-batch performance.
In addition, sustainability considerations are reshaping raw material selection, with growing emphasis on bio-based epoxies and recycled components. This shift toward greener chemistries not only supports corporate environmental goals but also aligns with tightening regulations on hazardous substances. As a result, the market is witnessing the emergence of hybrid systems that balance performance, cost, and eco-credentials.
Cumulative Impact of United States Tariffs in 2025 on Supply Chains
In 2025, the United States implemented a series of tariffs targeting critical raw materials and chemical intermediates used in epoxy resin production. These measures, aiming to protect domestic manufacturers, have had a cascading effect throughout global supply chains. Import costs for bisphenol-A derivatives, epichlorohydrin, and specialty fillers have risen significantly, prompting resin producers to reassess sourcing strategies and revise procurement calendars.
As a consequence, many manufacturers have accelerated efforts to localize production, forging partnerships with regional suppliers in North America and exploring backward integration. While these initiatives reduce exposure to import duties, they require substantial capital investment and lead times for capacity expansion. In parallel, resin formulators are adapting by reformulating products to incorporate alternative feedstocks, including bio-based epoxides and non-traditional curing agents. This material substitution strategy mitigates cost pressures while maintaining key performance attributes.
Moreover, the tariff-induced volatility has underscored the importance of supply chain resilience. Industry leaders are implementing dual-sourcing frameworks, investing in safety stock, and leveraging digital procurement platforms to monitor global price fluctuations in real time. Ultimately, these adaptive strategies highlight the sector’s agility in navigating policy-driven disruptions, while underscoring the imperative for continuous innovation and risk management.
Key Segmentation Insights into Type, Application, and End-Use Industries
The epoxy resin market for electrical insulation can be understood through a multilayered segmentation framework that illuminates critical growth drivers. When examined by resin type, the portfolio spans potting and encapsulation systems, flexible epoxies, liquid variants, and solid formulations. Potting and encapsulation systems further bifurcate into electrically insulative grades and thermally conductive grades, each engineered for specific thermal and dielectric requirements. Flexible epoxies break down into impact resistant and UV resistant formulations, ensuring durability in dynamic environments. Liquid epoxies are differentiated by viscosity-high, medium, and low-to match processing techniques ranging from automated dispensing to manual potting. Solid epoxies likewise vary by molecular weight, with high, medium, and low molecular weight grades tailored for curing speed, crosslink density, and mechanical flexibility.
In terms of application, the market addresses cables and wires, circuit breakers, motors and generators, and transformers. Cables and wires are sub-segmented into high, medium, and low tension categories, each demanding unique dielectric thickness and thermal performance. Circuit breakers are classified into high, medium, and low voltage types, with epoxy resins delivering arc quenching and insulation integrity. Motors and generators encompass electric vehicle motors, industrial motors, and wind turbine generators, where insulation systems must withstand thermal cycling and mechanical stress. Transformer insulation spans distribution, instrument, and power transformers, requiring formulations with high thermal conductivity and minimal shrinkage.
Evaluating end-use industries reveals four primary sectors: automotive, construction, electronics and electricals, and energy and power. Automotive applications include electric vehicles and traditional internal combustion engine vehicles, where epoxy resins protect stators and power electronics. Construction segments consist of commercial, infrastructure, and residential projects, leveraging encapsulation solutions for building automation and safety systems. Electronics and electricals cover computers and peripherals, consumer electronics, and industrial electronics, each with distinct thermal management and miniaturization demands. Finally, the energy and power sector comprises hydropower, solar power, and wind power installations, where high-performance insulation materials ensure long-term reliability under harsh environmental conditions.
This comprehensive research report categorizes the Epoxy Resin for Electrical Insulation market into clearly defined segments, providing a detailed analysis of emerging trends and precise revenue forecasts to support strategic decision-making.
- Type
- Application
- End-Use Industry
Key Regional Insights across the Americas, EMEA, and Asia-Pacific
Regional dynamics play a pivotal role in shaping competitive landscapes and investment priorities. In the Americas, growth drivers include expanding renewable energy projects and the resurgence of domestic manufacturing, with North American producers ramping up capacity for potting compounds and thermally conductive resins. Latin America, while smaller in absolute volume, shows promise in cable infrastructure upgrades and electrification initiatives.
Turning to Europe, Middle East & Africa, stringent regulatory frameworks on sustainability and chemical safety are accelerating the adoption of bio-based and low-VOC epoxy solutions. Western Europe leads in high-performance formulations for automotive and industrial electronics, while the Middle East focuses on large-scale power generation and distribution infrastructure. In Africa, emerging markets are gradually increasing demand for affordable insulation materials to support rural electrification and telecom network expansions.
In the Asia-Pacific region, rapid industrialization and the surge in electric vehicle production are primary catalysts. China remains the largest manufacturing hub for epoxy resins, investing heavily in advanced curing technologies and nanocomposite resins for thermal management. Japan and South Korea concentrate on highly specialized applications, including semiconductor packaging and aerospace-grade insulation. Southeast Asian economies, meanwhile, are experiencing steady uptake in power distribution and motor manufacturing, creating opportunities for both global incumbents and local producers.
This comprehensive research report examines key regions that drive the evolution of the Epoxy Resin for Electrical Insulation market, offering deep insights into regional trends, growth factors, and industry developments that are influencing market performance.
- Americas
- Asia-Pacific
- Europe, Middle East & Africa
Key Companies Driving Innovation and Market Leadership
Innovation and market leadership are driven by a diverse set of established and emerging players. 3M Company has strengthened its position through specialty adhesives and encapsulants with integrated thermal pathways. Aditya Birla Chemicals (Thailand) Ltd. leverages vertically integrated feedstock capabilities to offer cost-optimized resin systems. BASF SE’s global research network has delivered high-performance liquid epoxies with tailored viscosity profiles. Chang Chun Group focuses on bio-based epoxy precursors, establishing early footholds in sustainable formulations. CIECH GROUP has expanded its thermal conductive epoxy portfolio to meet growing demands in power electronics.
Dow Chemical Company continues to refine cure accelerators and tougheners for flexible insulations, while Elekeiroz S.A. emphasizes high-voltage potting compounds for transformer applications. Guangdong Longhua Technology Group Co., Ltd. invests in automated processing platforms, enhancing consistency in low-viscosity systems. Gurit Holdings AG specializes in high-performance composites and epoxy adhesives, catering to aerospace and wind energy sectors. Hexion Inc. offers a broad array of solid and liquid epoxy resins, supported by a global technical service network. Huntsman Corporation has introduced novel resin blends that improve adhesion to metallic substrates.
Jiangsu Sanmu Group Corporation excels in large-volume resin production, whereas KUKDO Chemical Co., Ltd. develops precision-controlled molecular weight epoxies. Mitsubishi Chemical Corporation applies advanced catalyst systems for rapid curing, and Momentive Performance Materials Inc. pioneers silane-modified epoxies for enhanced moisture resistance. Nippon Steel Chemical & Material Co., Ltd. integrates steel manufacturing expertise to deliver epoxy powders for coil coating. Olin Corporation offers a comprehensive suite of curing agents, while Sumitomo Bakelite Co., Ltd. focuses on specialty thermosetting molding compounds. Westlake Chemical Corporation rounds out the landscape with competitively priced resins and a growing presence in North America.
This comprehensive research report delivers an in-depth overview of the principal market players in the Epoxy Resin for Electrical Insulation market, evaluating their market share, strategic initiatives, and competitive positioning to illuminate the factors shaping the competitive landscape.
- 3M Company
- Aditya Birla Chemicals (Thailand) Ltd.
- BASF SE
- Chang Chun Group
- CIECH GROUP
- Dow Chemical Company
- Elekeiroz S.A.
- Guangdong Longhua Technology Group Co., Ltd.
- Gurit Holdings AG
- Hexion Inc.
- Huntsman Corporation
- Jiangsu Sanmu Group Corporation
- KUKDO Chemical Co., Ltd.
- Mitsubishi Chemical Corporation
- Momentive Performance Materials Inc.
- Nippon Steel Chemical & Material Co., Ltd.
- Olin Corporation
- Sumitomo Bakelite Co., Ltd.
- Westlake Chemical Corporation
Actionable Recommendations for Industry Leaders to Navigate Challenges
Industry leaders must adopt strategic imperatives to seize emerging opportunities and mitigate risks. First, investing in sustainable resin chemistries-such as bio-based epoxides and recycled filler integrations-will address tightening environmental regulations and corporate responsibility targets. Second, enhancing supply chain agility through dual sourcing and nearshoring raw material procurement can buffer against future tariff volatility and geopolitical tensions.
Third, accelerating digital transformation within manufacturing operations-by deploying real-time monitoring of cure kinetics, viscosity trends, and temperature profiles-will improve yield consistency and reduce scrap rates. Fourth, forging collaborative partnerships with end-users in the automotive, renewable energy, and electronics sectors can drive co-development of customized formulations, ensuring optimal performance in targeted applications. Fifth, expanding technical service capabilities-through virtual training modules and on-site support teams-will deepen customer relationships and accelerate adoption of advanced resin systems.
Finally, fortifying intellectual property portfolios and pursuing strategic acquisitions of niche technology providers will strengthen competitive positioning. By aligning R&D roadmaps with market demand signals and emerging regulatory frameworks, companies can maintain momentum in a rapidly evolving environment.
Explore AI-driven insights for the Epoxy Resin for Electrical Insulation market with ResearchAI on our online platform, providing deeper, data-backed market analysis.
Ask ResearchAI anything
World's First Innovative Al for Market Research
Conclusion: Harnessing Opportunities in Epoxy Resin for Electrical Insulation
In conclusion, the epoxy resin sector for electrical insulation stands at a crossroads defined by innovation imperatives, regulatory shifts, and trade policy dynamics. The ability to craft advanced material solutions-spanning high-performance potting compounds, flexible insulations, and thermally conductive resins-will determine competitive success. Adapting to 2025 tariff impacts has highlighted the need for resilient supply chains and agile sourcing strategies, while the segmentation landscape underscores the diversity of end-use requirements across type, application, and industry.
Regional variations further emphasize the importance of tailored market approaches, whether addressing renewable energy deployments in the Americas, regulatory-driven green chemistry in EMEA, or electrification and industrial scaling in Asia-Pacific. Meanwhile, leading companies continue to innovate through sustainable chemistries, process digitization, and strategic partnerships. By executing on these fronts, manufacturers and suppliers can unlock growth avenues and reinforce the reliability of critical electrical infrastructure worldwide.
This section provides a structured overview of the report, outlining key chapters and topics covered for easy reference in our Epoxy Resin for Electrical Insulation market comprehensive research report.
- Preface
- Research Methodology
- Executive Summary
- Market Overview
- Market Dynamics
- Market Insights
- Cumulative Impact of United States Tariffs 2025
- Epoxy Resin for Electrical Insulation Market, by Type
- Epoxy Resin for Electrical Insulation Market, by Application
- Epoxy Resin for Electrical Insulation Market, by End-Use Industry
- Americas Epoxy Resin for Electrical Insulation Market
- Asia-Pacific Epoxy Resin for Electrical Insulation Market
- Europe, Middle East & Africa Epoxy Resin for Electrical Insulation Market
- Competitive Landscape
- ResearchAI
- ResearchStatistics
- ResearchContacts
- ResearchArticles
- Appendix
- List of Figures [Total: 22]
- List of Tables [Total: 686 ]
Take the Next Step: Connect with Ketan Rohom to Unlock In-Depth Insights
Ready to gain comprehensive, data-delivered insights and strategic guidance on the epoxy resin market for electrical insulation? Contact Ketan Rohom, Associate Director, Sales & Marketing, to secure your copy of the detailed market research report. Empower your organization with actionable intelligence and stay ahead in this dynamic, high-growth segment.
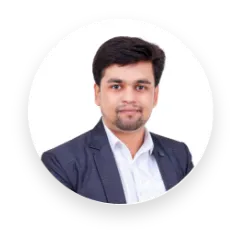
- When do I get the report?
- In what format does this report get delivered to me?
- How long has 360iResearch been around?
- What if I have a question about your reports?
- Can I share this report with my team?
- Can I use your research in my presentation?