Introduction to the EVA Glass Laminating Machine Market
Efficient lamination of glass has become indispensable in modern architecture, automotive design, and aerospace engineering. Ethylene vinyl acetate (EVA) glass laminating machines serve as the backbone of multilayer glass assemblies, delivering improved safety, energy efficiency, and aesthetic versatility. Recent years have witnessed accelerated adoption of lamination equipment that can apply precise temperature control and uniform pressure, enabling high throughput while meeting stringent quality standards. As the global building envelope relies increasingly on insulated, laminated, or decorative glass, the demand for advanced EVA lamination solutions continues to climb. This summary explores the transformative shifts, regulatory headwinds, segmentation dynamics, regional trends, and competitive landscape shaping the evolution of this sector. By synthesizing strategic insights, industry stakeholders can navigate emerging challenges and seize opportunities to optimize production efficiency, enhance product performance, and drive sustainable growth.
Moreover, the proliferation of electric vehicle adoption and the integration of smart glass functionalities have redefined performance benchmarks. OEMs across automotive and aerospace sectors now require laminate assemblies with enhanced mechanical resilience, acoustic insulation, and compatibility with conductive interlayers for embedded sensors. Similarly, growth in commercial and residential construction is fueling the specification of laminated safety and security glass, catalyzing investments in high-precision, automated laminating lines. Culminating in robust pipeline projects and retrofit applications that necessitate customization at scale.
In parallel, ongoing research into advanced film chemistries and process automation-leveraging AI-driven quality control and predictive maintenance-has established new operational paradigms. This dynamic interplay among technological innovation, end-user requirements, and regulatory frameworks sets the stage for a comprehensive examination of the EVA glass laminating machine market’s future trajectory.
Transformative Technological and Market Shifts Shaping the Industry
Digitalization has redefined how manufacturers monitor and optimize lamination lines in real time. Integrated sensors, IoT-enabled control systems, and machine learning algorithms now ensure consistent temperature profiles across heated rollers, detect anomalies in film application, and minimize scrap rates through adaptive process adjustments. Concurrently, rising regulatory emphasis on environmental stewardship has accelerated the transition from solvent-based cleaning and adhesive systems toward greener formulations that reduce VOC emissions and energy consumption. This shift has spurred adoption of hybrid laminating systems that combine liquid-based and thermal-assisted roll configurations, balancing speed with eco-friendly operation.
In addition, the proliferation of multi-layer glass architectures has expanded application scopes from conventional safety and decorative panels to advanced energy-harvesting modules and interactive façades. Architects and OEMs are increasingly specifying laminated assemblies that integrate photovoltaic cells or electrochromic layers, which demand specialized EVA films and precision vacuum-assist laminating processes. This trend has elevated the strategic importance of machines capable of handling both cold and hot lamination cycles within a single production cell.
Furthermore, global supply chain realignments are reshaping vendor relationships, with suppliers investing in localized manufacturing hubs to mitigate lead times and tariff exposures. Strategic partnerships between equipment manufacturers and film chemists have become critical for co-developing next-generation interlayers that enhance UV resistance, acoustic damping, and impact performance. As the market embraces these transformative shifts, stakeholders must continuously adapt to sustain competitiveness in a rapidly evolving landscape.
Assessing the 2025 United States Tariffs and Their Cumulative Industry Impact
In early 2025, the United States implemented a series of additional tariffs on imported EVA films, glass laminating machinery components, and ancillary equipment related to multilayer glass production. These measures, aimed at protecting domestic manufacturers and curbing perceived unfair trade practices, have introduced a cumulative duty burden of up to 15% on key inputs. As a result, original equipment manufacturers (OEMs) and laminator end-users are grappling with higher procurement costs, which have eroded margin structures and prompted a reassessment of sourcing strategies.
The impact extends beyond direct equipment purchases. Upstream suppliers of hot laminating rollers, pressure calibration systems, and vacuum pumps have faced escalated costs that have been passed through the value chain, driving up capital expenditures for new line installations. Operationally, some producers have deferred planned expansions, while others have accelerated investments in domestic automation lines to sidestep import levies. These strategic shifts have led to pilot projects for localized manufacturing clusters in the Southern United States and partnerships with North American component vendors.
Moreover, the tariff package has had a knock-on effect on commodity markets. EVA, PVB, and PVC film imports from traditional low-cost regions now attract heavier duties, incentivizing end users to consider alternative interlayer chemistries or to repurpose existing lamination assets. However, material substitution brings technical challenges, including compatibility with established curing profiles and compliance with safety standards. Navigating this complex tariff landscape requires proactive supply chain mapping, cost modeling, and engagement with policy stakeholders to shape future trade negotiations.
Key Segmentation Insights Across Industries, Technologies, Applications, Machinery and Raw Materials
Analysis by end-user industry reveals diverse demand drivers. In aerospace, demand for laminated glass spans commercial aircraft cabins, defense cockpit canopies, and unmanned aerial vehicle sensors. Automotive sector growth is underpinned by lamination for commercial trucks, assembly lines in electric vehicle compacts, and enhanced safety glazing for passenger cars. Commercial and residential construction specify laminated façades for high-rise towers and energy-efficient residential windows. Electronics applications include decorative consumer displays, telecommunication device screens, and wearable sensors. In the energy sector, laminated modules serve in solar panel encapsulation and wind turbine blade windows.
Technology segmentation highlights distinct preferences. Cold laminating technologies-liquid-based and pressure-sensitive systems-offer gentle film handling ideal for heat-sensitive substrates, while hot laminating solutions such as infrared and vacuum-assisted ovens deliver rapid curing cycles. Hybrid laminating systems leverage liquid hybrid processes and thermal-assist roll configurations to balance throughput with process flexibility.
Application segmentation underscores market heterogeneity. Decorative glass encompasses printed and tinted variants favored in architectural accents. Safety glass includes bulletproof and shatterproof solutions mandated by regulatory codes. Sound insulation glass, deployed as façade panels or internal wall partitions, addresses acoustic control in urban developments. Structural glass, featuring heat-strengthened and tempered formats, meets load-bearing and safety requirements.
Machinery type analysis shows that batch-type machines-manual and semi-automatic models-continue to serve low-volume or customized runs, whereas continuous production lines-fully automatic and inline processing-dominate high-volume manufacturing. Finally, raw material segmentation indicates that EVA films, in clear and colored formats, lead the market, complemented by PVB films designed for acoustic dampening or enhanced safety, and PVC films tailored for decorative or privacy applications. Together, these segmentation insights provide a granular view of market opportunities and challenges across diverse use cases.
This comprehensive research report categorizes the EVA Glass Laminating Machine market into clearly defined segments, providing a detailed analysis of emerging trends and precise revenue forecasts to support strategic decision-making.
- End-User Industry
- Technology Type
- Application
- Machinery Type
- Raw Material
Regional Market Dynamics and Growth Drivers
Regional analysis reveals differentiated growth trajectories. In the Americas, robust investment in commercial construction projects and accelerating adoption of laminated safety glass in automotive assembly plants have driven demand. Manufacturers in North and South America are leveraging free trade agreements to optimize their supply networks, while Latin American markets exhibit rising interest in energy-efficient glazing solutions for solar installations.
Transitioning to the Europe, Middle East & Africa region, stringent building codes and sustainability targets bolster demand for laminated façades and advanced interlayers, with key markets in Western Europe pushing for energy-harvesting glass and the Middle East investing in high-durability glazing for harsh climates. Meanwhile, Africa’s infrastructure expansions are gradually incorporating laminated solutions to meet safety and sound insulation requirements.
In Asia-Pacific, rapid urbanization, coupled with large-scale infrastructure development in China, India, and Southeast Asia, underpins strong demand for both batch and continuous laminating systems. Regional equipment suppliers are expanding local service capabilities to support OEMs and retrofit projects, while government incentives for solar energy installations further stimulate the use of laminated modules in the renewable energy sector.
This comprehensive research report examines key regions that drive the evolution of the EVA Glass Laminating Machine market, offering deep insights into regional trends, growth factors, and industry developments that are influencing market performance.
- Americas
- Asia-Pacific
- Europe, Middle East & Africa
Leading Manufacturers and Competitive Positioning
Competition in the EVA laminating equipment space features a mix of established global players and specialized innovators. H&H Glass Machinery Inc. and Morntech are renowned for their robust continuous laminating lines with integrated quality control modules, while HUBAY Eveson Ltd. and North Glass focus on fully automatic solutions that cater to high-volume glass processors. Ldge Glass and Ory & Co. Pvt. Ltd. differentiate themselves through customizable batch-type machines tailored for niche applications, and Pujol 1920 leverages a century of craftsmanship to deliver semi-automatic laminating presses with precise temperature regulation.
On the material handling front, Qinhuandao Wellking Glass New Technology Co., Ltd. and SGO Innovations have made strides in hybrid laminating systems that combine liquid dispersion with thermal-assist rolling for enhanced process efficiency. Vaspar Engineering Co. Ltd. rounds out the competitive landscape with pressure-sensitive cold laminators that appeal to electronics and wearable device manufacturers. Through strategic alliances, continuous product upgrades, and regional expansion initiatives, these companies are vying for market share by aligning their portfolios with evolving end-user requirements and regulatory trends.
This comprehensive research report delivers an in-depth overview of the principal market players in the EVA Glass Laminating Machine market, evaluating their market share, strategic initiatives, and competitive positioning to illuminate the factors shaping the competitive landscape.
- H&H Glass Machinery Inc.
- HUBAY Eveson Ltd.
- Ldge Glass
- Morntech
- North Glass
- Ory & Co. Pvt. Ltd.
- Pujol 1920
- Qinhuandao Wellking Glass New Technology Co., Ltd.
- SGO Innovations
- Vaspar Engineering Co. Ltd.
Actionable Recommendations for Industry Leaders
Based on these insights, industry leaders should prioritize several strategic actions. First, diversifying the supplier base for EVA, PVB, and PVC films will mitigate tariff risks and ensure access to critical interlayers. Second, investing in modular, hybrid laminating systems that can switch seamlessly between cold and hot cycles will enhance production flexibility and accommodate evolving application demands. Third, forging R&D partnerships with film chemists and digital control vendors can accelerate the development of next-generation laminates that deliver improved UV stability, acoustic performance, and embedded functionalities. Fourth, expanding service networks and spare parts inventory in key regions will reduce downtime and strengthen customer relationships. Finally, aligning capital investment plans with regional incentive schemes-particularly those promoting energy-efficient construction and renewable energy installations-can unlock cost advantages and position manufacturers ahead of regulatory mandates. By executing these recommendations, equipment suppliers and end users will reinforce their competitive positioning and drive sustainable growth in a complex market environment.
Explore AI-driven insights for the EVA Glass Laminating Machine market with ResearchAI on our online platform, providing deeper, data-backed market analysis.
Ask ResearchAI anything
World's First Innovative Al for Market Research
Conclusion: Seizing Opportunities in a Complex Landscape
As the EVA glass laminating machine market navigates a landscape marked by technological leaps, regulatory shifts, and shifting trade dynamics, stakeholders must remain agile and forward-looking. The confluence of digitalization, sustainability imperatives, and rising demand across automotive, construction, electronics, aerospace, and energy sectors underscores the need for versatile, high-precision equipment. By leveraging segmentation insights, regional trends, and competitive benchmarks, market participants can target investments, streamline operations, and tailor product portfolios to emerging customer requirements. Sustained collaboration between equipment manufacturers, raw material suppliers, and end users will be crucial for co-creating innovative solutions that enhance safety, energy efficiency, and design flexibility. Ultimately, the companies that integrate strategic foresight with operational excellence will capture the greatest value as the industry evolves toward more integrated and intelligent lamination processes.
This section provides a structured overview of the report, outlining key chapters and topics covered for easy reference in our EVA Glass Laminating Machine market comprehensive research report.
- Preface
- Research Methodology
- Executive Summary
- Market Overview
- Market Dynamics
- Market Insights
- Cumulative Impact of United States Tariffs 2025
- EVA Glass Laminating Machine Market, by End-User Industry
- EVA Glass Laminating Machine Market, by Technology Type
- EVA Glass Laminating Machine Market, by Application
- EVA Glass Laminating Machine Market, by Machinery Type
- EVA Glass Laminating Machine Market, by Raw Material
- Americas EVA Glass Laminating Machine Market
- Asia-Pacific EVA Glass Laminating Machine Market
- Europe, Middle East & Africa EVA Glass Laminating Machine Market
- Competitive Landscape
- ResearchAI
- ResearchStatistics
- ResearchContacts
- ResearchArticles
- Appendix
- List of Figures [Total: 26]
- List of Tables [Total: 989 ]
Next Steps to Access In-Depth Market Intelligence
To gain access to comprehensive data, detailed analysis, and actionable insights on the EVA glass laminating machine market, reach out to Ketan Rohom (Associate Director, Sales & Marketing). He can guide you through the full report, which delves into emerging trends, competitive dynamics, and strategic opportunities. This comprehensive report covers company profiles, regulatory mapping, adoption case studies, and technology evaluations that equip decision-makers with the evidence base required to optimize production strategies and capital allocation. Whether you are evaluating a retrofit of an existing line or planning a greenfield installation, this intelligence will help you anticipate challenges, capitalize on emerging segments, and deliver superior laminated solutions to your customers. Contact him today to secure executive-level intelligence that will inform your investment decisions, technology roadmaps, and market expansion plans.
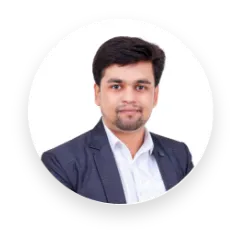
- When do I get the report?
- In what format does this report get delivered to me?
- How long has 360iResearch been around?
- What if I have a question about your reports?
- Can I share this report with my team?
- Can I use your research in my presentation?