Introduction to Explosion-Proof Palletizing Technology
Explosion-proof palletizing robots have emerged as a pivotal solution for industries operating in hazardous environments where combustible dust, flammable gases, and volatile vapors pose persistent safety risks. By integrating robust hardware enclosures, intrinsic safety protocols, and compliance with stringent certification standards, these specialized robots enable manufacturers to automate repetitive palletizing tasks without compromising on operational safety. With the maturation of robotics technology, explosion-proof models now offer performance levels on par with their standard counterparts, allowing for precise handling, consistent throughput, and seamless integration into existing production lines.
As industrial facilities increasingly prioritize uptime and risk mitigation, adopting explosion-proof palletizing robots not only enhances workplace safety but also drives efficiency gains. These systems excel in environments such as chemical processing plants, oil and gas terminals, mining operations, and pharmaceutical manufacturing, where the cost of unplanned downtime or an incident can be exceptionally high. Furthermore, the rise of Industry 4.0 initiatives has spurred demand for intelligent robotic solutions that can communicate with enterprise management platforms, enabling real-time monitoring, predictive maintenance, and data-driven optimization.
In this context, explosion-proof palletizing robots represent more than a niche automation trend-they embody a fundamental shift in how businesses balance productivity with safety compliance. This executive summary outlines the transformative market forces shaping this segment, highlights critical segmentation and regional insights, profiles key players, and offers strategic guidance for leaders seeking to leverage these advanced solutions.
Key Trends Reshaping the Explosion-Proof Palletizing Market
The explosion-proof palletizing robot market is undergoing transformative shifts driven by a convergence of regulatory, technological, and operational factors. First, evolving safety regulations across North America, Europe, and Asia-Pacific are tightening certification requirements for automated equipment in hazardous zones. As a result, suppliers are advancing their product portfolios with modular designs that simplify compliance while reducing lead times.
Second, digitalization is reshaping how companies deploy and manage their fleets. The integration of digital twins, edge computing, and cloud-based analytics enables remote monitoring of explosion-proof robots, accelerating fault detection and minimizing unplanned downtime. Meanwhile, artificial intelligence–powered vision systems and machine learning algorithms are improving pick-and-place accuracy, enabling robots to handle irregular pallet loads with minimal human intervention.
Third, sustainability imperatives are prompting manufacturers to optimize energy consumption. Explosion-proof models now feature regenerative braking, variable-speed motors, and intelligent power management to reduce carbon footprints without sacrificing throughput. Additionally, the adoption of collaborative robotic arms in non-classified zones adjacent to hazardous areas is creating hybrid workflows that balance human dexterity with machine endurance.
Through these converging trends, the explosion-proof palletizing landscape is being reshaped from one of rigid, single-purpose machinery to a flexible, data-driven ecosystem-positioning early adopters to gain significant competitive advantage.
Assessing the Cumulative Impact of U.S. Tariffs in 2025
The announcement of new tariffs on automation equipment components in the United States beginning in 2025 has introduced additional complexity for suppliers and end users of explosion-proof palletizing robots. Components imported under specific tariff codes-ranging from specialized motors and drives to certified enclosures-face increased duties that elevate landed costs. Consequently, original equipment manufacturers (OEMs) are recalibrating their supply chains to source compliant components domestically or from tariff-exempt regions.
At the same time, some companies are preemptively adjusting procurement strategies by leveraging bonded warehouses and foreign-trade zones to defer duties, while others are renegotiating long-term contracts to include tariff-adjustment clauses. On the demand side, higher component costs are exerting pressure on capital expenditure budgets, prompting buyers to extend asset lifecycles through enhanced maintenance services and software upgrades rather than opting for full system replacements.
However, the cumulative impact of these tariffs has also galvanized investment in localized assembly and modular design architectures. By shifting final assembly operations closer to key end markets, manufacturers can preserve margin levels and offer more competitive pricing. This localization trend aligns with broader nearshoring initiatives, which aim to reduce lead times and increase supply chain resilience. As a result, participants who proactively adapt to the new tariff landscape are poised to outpace competitors relying on traditional global sourcing models.
In-Depth Segmentation Insights Driving Market Dynamics
A comprehensive understanding of market segmentation reveals critical drivers of explosion-proof palletizing robot demand. When examined by end-user industry, chemical processing facilities lead deployment, followed closely by manufacturing operations that handle flammable solvents. Mining and metallurgy plants, where explosive dust hazards are prevalent, represent a fast-growing segment, while oil and gas refineries and pharmaceutical production sites maintain strong, steady uptake due to regulatory compliance imperatives.
Payload capacity insights shed light on operational applications: robots rated for loads up to 100 kg cater to high-speed packaging and component assembly lines, whereas units in the 101 kg to 500 kg range dominate general material handling. Systems engineered for 501 kg to 1000 kg loads address bulk pallet stacking tasks, and those above 1000 kg serve large-format container transfers in heavy-duty environments.
Exploring application segmentation clarifies that assembly processes benefit from precise, programmable movements, material handling tasks leverage robotic endurance for continuous throughput, packaging operations demand rapid, repetitive accuracy, and transport functions require coordinated multi-axis motion to navigate complex layouts. In terms of robot type, articulated arms deliver unmatched flexibility, Cartesian models excel in linear pick-and-place operations, collaborative robots enable safe human-robot interactions outside classified zones, and SCARA platforms provide high-speed, four-axis precision for compact cell designs.
Finally, component segmentation underscores the importance of robust hardware as the foundation, specialized software to orchestrate multi-robot workflows and ensure compliance, and comprehensive services-including installation, certification support, and lifecycle management-to maximize return on investment.
This comprehensive research report categorizes the Explosion-Proof Palletizing Robot market into clearly defined segments, providing a detailed analysis of emerging trends and precise revenue forecasts to support strategic decision-making.
- End-User Industry
- Payload Capacity
- Application
- Robot Type
- Component
Regional Dynamics Shaping Global Adoption Patterns
Regional analysis highlights diverse growth trajectories across three major markets. In the Americas, the combination of stringent Occupational Safety and Health Administration standards and robust investment in petrochemical infrastructure underpins strong demand for explosion-proof palletizing solutions. Supply chain reconfiguration in response to tariff pressures has further stimulated domestic assembly operations.
Within Europe, the Middle East, and Africa, harmonization of ATEX and IECEx directives across multiple jurisdictions creates a unified regulatory framework that supports cross-border trade of certified robotic systems. Growth in the Middle East is particularly driven by large-scale oil and gas projects, while Africa’s expanding mining sector presents emerging opportunities for automated pallet handling.
Asia-Pacific remains the fastest-growing region, fueled by industrial modernization initiatives in China, Southeast Asia, and India. Government incentives aimed at reducing industrial accidents and improving productivity have incentivized both state-owned and private enterprises to deploy explosion-proof automation. Additionally, Japan and South Korea continue to pioneer advanced robotics integration, setting performance benchmarks that influence regional adoption patterns.
This comprehensive research report examines key regions that drive the evolution of the Explosion-Proof Palletizing Robot market, offering deep insights into regional trends, growth factors, and industry developments that are influencing market performance.
- Americas
- Asia-Pacific
- Europe, Middle East & Africa
Leading Players Steering Innovation and Growth
The competitive landscape features a mix of established industrial automation leaders and specialized robotics innovators. ABB Ltd. offers a comprehensive portfolio of explosion-proof models that integrate seamlessly with its wider industrial ecosystem. Omron Corporation, following its acquisition of Adept Technology, delivers highly intelligent systems with advanced vision-guided capabilities. Bastian Robotics, a division of Bastian Solutions, focuses on tailored warehouse automation solutions, while Comau S.p.A. leverages its automotive heritage to supply robust, high-speed palletizing cells.
Dürr Systems AG differentiates through its global service network and modular hardware designs that streamline installation across disparate sites. Epson Robots (Seiko Epson Corporation) brings precision-driven, space-efficient Cartesian and SCARA platforms to packaging applications. FANUC Corporation maintains leadership in reliability and uptime, complemented by Festo SE & Co. KG’s pneumatic expertise for integrated process automation. Kawasaki Heavy Industries, Ltd. and KUKA AG both excel in heavy-payload articulated solutions, supported by OTC Daihen Inc.’s deep welding integration knowledge.
Panasonic Corporation combines electronics assembly prowess with explosion-proof technologies, while Staubli International AG focuses on quick-change tooling systems for rapid reconfiguration. Universal Robots A/S continues to expand collaborative robot deployments in peripheral zones, and Yaskawa Electric Corporation drives innovation in motion control and predictive maintenance frameworks. Together, these companies shape a dynamic market ecosystem characterized by continuous product enhancements and strategic partnerships.
This comprehensive research report delivers an in-depth overview of the principal market players in the Explosion-Proof Palletizing Robot market, evaluating their market share, strategic initiatives, and competitive positioning to illuminate the factors shaping the competitive landscape.
- ABB Ltd.
- Adept Technology, Inc. (Omron Corporation)
- Bastian Robotics, a division of Bastian Solutions, LLC
- Comau S.p.A.
- Dürr Systems AG
- Epson Robots (Seiko Epson Corporation)
- FANUC Corporation
- Festo SE & Co. KG
- Kawasaki Heavy Industries, Ltd.
- KUKA AG
- OTC Daihen Inc.
- Panasonic Corporation
- Staubli International AG
- Universal Robots A/S
- Yaskawa Electric Corporation
Strategic Recommendations for Industry Leadership
Industry leaders can capitalize on current momentum by adopting several strategic actions. First, prioritize modular architectures that allow rapid reconfiguration and simplified certification updates, reducing time-to-deployment for new sites. Second, invest in digital twin technology and edge analytics to enable predictive maintenance and real-time performance optimization, thereby minimizing unplanned downtime and extending asset lifecycles.
Third, forge partnerships with regional integrators and local component suppliers to mitigate tariff exposure and enhance supply chain resilience. Fourth, expand service portfolios to include remote commissioning, virtual training, and subscription-based maintenance plans that lock in recurring revenue while delivering continuous value to end users. Fifth, standardize on open communication protocols to ensure seamless interoperability with enterprise resource planning and warehouse management systems, facilitating holistic visibility across the automation ecosystem.
Finally, develop targeted workforce upskilling programs that equip operators and maintenance technicians with the skills to manage explosion-proof robotic cells safely and efficiently. By combining these actions, organizations can not only navigate current market complexities but also position themselves as preferred partners for customers seeking high-performance, compliant automation in hazardous environments.
Explore AI-driven insights for the Explosion-Proof Palletizing Robot market with ResearchAI on our online platform, providing deeper, data-backed market analysis.
Ask ResearchAI anything
World's First Innovative Al for Market Research
Concluding Perspectives on Future Opportunities
Explosion-proof palletizing robots represent a critical inflection point for automation in hazardous environments, balancing safety imperatives with productivity gains. As regulatory frameworks continue to tighten and tariff landscapes evolve, organizations that invest in adaptable, data-driven solutions will secure both operational resilience and competitive differentiation. The synergy of advanced hardware, intelligent software, and comprehensive services is reshaping end-user expectations, driving demand for systems that deliver consistent throughput, precise handling, and minimal downtime.
Looking ahead, continuous innovation in areas such as collaborative human-robot workflows, energy-efficient designs, and integrated safety sensors will further elevate the role of explosion-proof automation across diverse industries. Companies that embed these capabilities within scalable, standardized platforms will not only meet current compliance requirements but also anticipate the next wave of performance and safety benchmarks. In doing so, they will unlock new value streams-ranging from reduced operational risk to enhanced sustainability-solidifying their position at the forefront of industrial innovation.
This section provides a structured overview of the report, outlining key chapters and topics covered for easy reference in our Explosion-Proof Palletizing Robot market comprehensive research report.
- Preface
- Research Methodology
- Executive Summary
- Market Overview
- Market Dynamics
- Market Insights
- Cumulative Impact of United States Tariffs 2025
- Explosion-Proof Palletizing Robot Market, by End-User Industry
- Explosion-Proof Palletizing Robot Market, by Payload Capacity
- Explosion-Proof Palletizing Robot Market, by Application
- Explosion-Proof Palletizing Robot Market, by Robot Type
- Explosion-Proof Palletizing Robot Market, by Component
- Americas Explosion-Proof Palletizing Robot Market
- Asia-Pacific Explosion-Proof Palletizing Robot Market
- Europe, Middle East & Africa Explosion-Proof Palletizing Robot Market
- Competitive Landscape
- ResearchAI
- ResearchStatistics
- ResearchContacts
- ResearchArticles
- Appendix
- List of Figures [Total: 26]
- List of Tables [Total: 241 ]
Contact Ketan Rohom for the Full Market Research Report
To gain comprehensive insights and actionable data on explosion-proof palletizing robots, reach out to Ketan Rohom, Associate Director, Sales & Marketing, to secure your copy of the full market research report. Unlock the strategic intelligence you need to drive growth, optimize safety, and stay ahead of emerging industry trends.
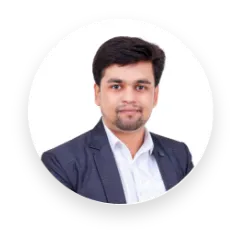
- When do I get the report?
- In what format does this report get delivered to me?
- How long has 360iResearch been around?
- What if I have a question about your reports?
- Can I share this report with my team?
- Can I use your research in my presentation?