The Extrusion Coatings Market size was estimated at USD 6.21 billion in 2024 and expected to reach USD 6.58 billion in 2025, at a CAGR 5.76% to reach USD 8.70 billion by 2030.

Charting the Evolution of Extrusion Coatings
Extrusion coatings represent a cornerstone of modern packaging and industrial applications, marrying polymer technology with precision processing to deliver functional and protective layers across a broad range of substrates. This executive summary unpacks the complexities of this dynamic market segment, tracing its evolution from basic thermoplastic overlays to advanced copolymers and metallocene-based solutions engineered for performance, sustainability, and cost efficiency.
As demand for lightweight, high-barrier packaging intensifies and sectors such as medical devices, automotive, and construction seek specialized surface properties, extrusion coating stands at the intersection of innovation and practicality. Industry leaders are leveraging breakthroughs in resin chemistry and processing technologies to optimize adhesion, enhance barrier characteristics, and streamline production workflows. Consequently, a nuanced understanding of market drivers, segmentation, regional patterns, and competitive strategies becomes essential for stakeholders aiming to unlock value and maintain a competitive edge.
Unfolding Shifts Redefining Coating Dynamics
The extrusion coatings landscape has undergone profound transformations driven by shifting consumer priorities, regulatory mandates, and technological breakthroughs. Sustainability has emerged as a central theme, pushing formulators to reduce volatile organic compounds and transition to water-based or solventless systems without compromising performance. Concurrently, the rise of monomaterial packaging has prompted the development of tailored coatings that facilitate recyclability while maintaining barrier integrity.
Digitalization is another transformative force, enabling real-time process controls, predictive maintenance, and remote monitoring that enhance operational efficiency and minimize waste. Additive manufacturing and nanotechnology are also carving new pathways for functionality, with opportunities to embed active properties such as antimicrobial barriers or oxygen scavengers directly into coating layers.
In parallel, end users are demanding faster changeover times and greater customization, prompting equipment suppliers to introduce modular dies and precision coatings heads. These incremental yet impactful shifts underscore a broader trend toward agile, data-driven operations that align product formulation with end-use specifications and environmental objectives.
Anticipating the Ripple Effects of Upcoming Tariffs
The introduction of additional United States tariffs slated for 2025 is poised to exert a cumulative impact on raw material sourcing, supply chain configurations, and pricing strategies. Many resin suppliers are recalibrating their global footprints, repatriating production lines or forging new partnerships with domestic petrochemical producers to mitigate increased import duties and currency volatility.
As resin costs adjust upward in response to tariff pressures, converters and brand owners are exploring contract structures that share risk across the value chain. Longer-term supply agreements, index-linked pricing clauses, and collaborative inventory management initiatives are becoming commonplace as stakeholders seek to stabilize input costs. Meanwhile, nearshoring trends are gaining traction, with North American facilities expanding capacity to serve the packaging and industrial segments more efficiently.
Regulatory scrutiny is also on the rise, as trade authorities assess tariff impacts on downstream industries and consider exemptions for critical medical and food-grade barrier materials. In this fluid environment, proactive engagement with policy makers and supply chain partners will be essential for companies aiming to secure uninterrupted access to key polymers and maintain competitive pricing.
Deep Dive into Market Segmentation Nuances
Understanding the extrusion coatings market requires a granular view of how applications, technologies, substrates, end use industries, and coating types intersect to shape demand patterns. Application analysis reveals that adhesives engineered for pressure sensitive and water activated bonding coexist alongside barrier coatings tailored to food packaging and medical packaging protections, while heat seal overlays optimized for high temperature or low temperature operations extend the functional envelope. Lamination plays a pivotal role as well, with film lamination, flexible packaging lamination, and paperboard lamination each addressing specific performance requirements.
On the technology front, copolymer resins, ethylene vinyl acetate formulations, metallocene-based polymers, plastomers, and polyurethane blends offer a spectrum of mechanical and barrier properties that converters leverage to meet customer specifications. Substrate preferences further refine market opportunities, as folding carton board and solid bleached board find favor in rigid packaging, while film substrates such as BOPP, PE, PET, and PP deliver clarity and flexibility. Coated paper and kraft paper remain staples for specialty labeling and ecofriendly solutions.
End use industries stretch from agriculture and automotive interiors and exteriors to construction applications in insulation and roofing, as well as device packaging and pharmaceutical packaging in the medical sector, capped by beverage packaging and food packaging in commercial distribution. Finally, the choice between powder coating, solvent based aliphatic and aromatic systems, solventless lines, and water based acrylic and polyurethane formulas underscores the imperative to balance environmental compliance with end-use performance.
This comprehensive research report categorizes the Extrusion Coatings market into clearly defined segments, providing a detailed analysis of emerging trends and precise revenue forecasts to support strategic decision-making.
- Application
- Technology
- Substrate
- End Use Industry
- Coating Type
Regional Patterns Shaping Demand Dynamics
Regional insights highlight the unique drivers and challenges shaping extrusion coating demand across the Americas, Europe Middle East and Africa, and Asia-Pacific. In the Americas, robust growth in e-commerce packaging and demand for recyclable solutions fuel investments in advanced barrier coatings and lamination technologies. Converters in this region are also early adopters of solventless systems to meet stringent VOC regulations and address sustainability pledges from major retailers.
Across Europe, the Middle East and Africa, regulatory frameworks such as the European Green Deal and local content requirements in the Gulf Cooperation Council are accelerating the shift toward water based and high-performance copolymer coatings. Medical and pharmaceutical packaging demand remains strong, prompting regional players to enhance cleanroom capacities and invest in precision coating lines.
Asia-Pacific stands out for its cost-competitive manufacturing base and rapid expansion of end use sectors, particularly in automotive lightweighting and consumer electronics. China and India are witnessing heightened demand for white goods and medical packaging, while Southeast Asian markets are increasingly sourcing flexible packaging lamination solutions to serve rising food and beverage consumption. Cross-border supply chains remain complex, with import tariffs, currency fluctuations, and evolving environmental regulations shaping investment decisions.
This comprehensive research report examines key regions that drive the evolution of the Extrusion Coatings market, offering deep insights into regional trends, growth factors, and industry developments that are influencing market performance.
- Americas
- Europe, Middle East & Africa
- Asia-Pacific
Competitive Landscape and Leading Innovators
The competitive landscape is dominated by globally diversified chemical majors and specialized resin producers that continuously invest in R&D to enhance functionality and sustainability. Leading polymer manufacturers leverage extensive application laboratories to co-develop custom formulations with converters, thereby deepening customer relationships and accelerating time to market. Collaboration between resin suppliers and equipment vendors is also intensifying, resulting in integrated solutions that streamline coating line performance and reduce waste.
Specialty chemical companies differentiate through targeted acquisitions and strategic partnerships aimed at broadening their technology portfolios and geographic reach. Some have established regional innovation centers to adapt formulations to local substrate preferences and regulatory requirements. Meanwhile, niche players capitalize on agility, offering rapid prototyping capabilities and pilot-scale runs to support emerging packaging formats and novel end use cases.
Investments in digital platforms and data analytics further distinguish market leaders, enabling real-time quality control, predictive maintenance, and supply chain transparency. These capabilities not only drive operational efficiencies but also underpin value-added services such as shelf-life prediction and sustainability reporting, reinforcing supplier differentiation in a maturing market.
This comprehensive research report delivers an in-depth overview of the principal market players in the Extrusion Coatings market, evaluating their market share, strategic initiatives, and competitive positioning to illuminate the factors shaping the competitive landscape.
- Dow Inc.
- BASF SE
- Arkema S.A.
- Evonik Industries AG
- Eastman Chemical Company
- Henkel AG & Co. KGaA
- Wacker Chemie AG
- 3M Company
- PPG Industries, Inc.
- H.B. Fuller Company
Strategic Imperatives for Market Leadership
Industry leaders should prioritize a multifaceted strategy to navigate market complexities and capture growth. First, diversifying raw material sourcing through geographic or supplier expansion can mitigate tariff impacts and stabilize input costs. Concurrently, accelerating the development of sustainable coatings-such as water based and solventless systems-will align product portfolios with tightening environmental regulations and customer sustainability goals.
Second, investment in digital process controls and predictive analytics will unlock efficiencies across the production lifecycle. By integrating sensors, machine learning, and cloud-based monitoring, operations teams can reduce downtime, optimize formulation parameters, and enhance product consistency. Third, building deeper partnerships with end users-especially in fast-growing segments like medical packaging and flexible e-commerce fulfillment-can drive co-innovation and secure long-term commitments.
Finally, companies should continuously evaluate end use and substrate trends to refine their segmentation strategies. Targeted efforts in emerging applications, from antimicrobial barrier coatings to recyclable monomaterial packaging, will position businesses for sustainable growth while reinforcing their reputation as market innovators.
Robust Methodological Framework Underpinning Insights
This analysis is grounded in a robust methodology that combines extensive secondary research with primary interviews and data triangulation. Industry publications, regulatory reports, and corporate filings provided foundational insights into market trends, regulatory developments, and technological advances. These desk-based findings were augmented by in-depth interviews with resin manufacturers, coating line operators, equipment suppliers, and end users to validate assumptions and uncover real-world challenges.
Quantitative data points were cross-checked against proprietary databases and market intelligence platforms to ensure accuracy and consistency. Regional market dynamics were analyzed using trade statistics, import-export records, and environmental policy reviews. The segmentation framework was developed iteratively, reflecting feedback from industry experts and aligning with prevailing commercial practices.
Quality assurance measures included peer reviews of key findings, sensitivity analyses on tariff scenarios, and scenario planning workshops that tested strategic recommendations under varying market conditions. This comprehensive approach ensures that the conclusions and guidance presented here are both credible and actionable for decision makers.
Explore AI-driven insights for the Extrusion Coatings market with ResearchAI on our online platform, providing deeper, data-backed market analysis.
Ask ResearchAI anything
World's First Innovative Al for Market Research
Synthesizing Key Takeaways for Decision Makers
As this executive summary has shown, the extrusion coatings market is at a pivotal juncture, shaped by sustainability imperatives, technological innovation, and evolving trade dynamics. Companies that align their portfolios with environmental regulations, harness digital capabilities, and forge strategic partnerships will be best positioned to capture growth across diverse applications and regions.
Anticipating the cumulative effects of upcoming tariffs, stakeholders must adopt agile supply chain strategies and foster transparent collaborations that spread risk and stabilize pricing. In parallel, a deep understanding of segmentation nuances-from substrate preferences to end use industry requirements-will inform targeted investments in R&D and capacity expansion.
Ultimately, the most successful players will be those that integrate rigorous market intelligence with decisive action, harnessing insights to optimize product development, streamline operations, and deliver sustainable value to customers.
This section provides a structured overview of the report, outlining key chapters and topics covered for easy reference in our Extrusion Coatings market comprehensive research report.
- Preface
- Research Methodology
- Executive Summary
- Market Overview
- Market Dynamics
- Market Insights
- Cumulative Impact of United States Tariffs 2025
- Extrusion Coatings Market, by Application
- Extrusion Coatings Market, by Technology
- Extrusion Coatings Market, by Substrate
- Extrusion Coatings Market, by End Use Industry
- Extrusion Coatings Market, by Coating Type
- Americas Extrusion Coatings Market
- Europe, Middle East & Africa Extrusion Coatings Market
- Asia-Pacific Extrusion Coatings Market
- Competitive Landscape
- ResearchAI
- ResearchStatistics
- ResearchContacts
- ResearchArticles
- Appendix
- List of Figures [Total: 26]
- List of Tables [Total: 819 ]
Engage with Our Lead Expert to Unlock Full Insights
I invite you to connect with Ketan Rohom, Associate Director of Sales and Marketing, to gain full access to this comprehensive market research report and empower your strategic planning. Ketan brings deep expertise in extrusion coatings and stands ready to guide you through tailored insights, ensuring your organization capitalizes on emerging trends and navigates regulatory shifts with confidence. Reach out today to discuss customization options, secure premier access, and position your business at the forefront of the extrusion coatings landscape.
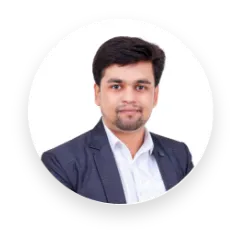
- How big is the Extrusion Coatings Market?
- What is the Extrusion Coatings Market growth?
- When do I get the report?
- In what format does this report get delivered to me?
- How long has 360iResearch been around?
- What if I have a question about your reports?
- Can I share this report with my team?
- Can I use your research in my presentation?