The Fab Management Software Market size was estimated at USD 1.08 billion in 2024 and expected to reach USD 1.18 billion in 2025, at a CAGR 8.80% to reach USD 1.79 billion by 2030.

Unveiling the Evolution of Fab Management Software
Over the past decade, fabrication management software has transcended its traditional role as a simple production scheduler to become a pivotal element in modern supply chain optimization. As manufacturing operations grow in complexity, the demand for integrated digital solutions that bridge design, execution, and analytics has never been greater. The convergence of cloud computing, real-time data access, and advanced analytics is reshaping the way factories operate, elevating efficiency and enabling near-zero downtime in production lines.
In response to intensifying global competition and stringent regulatory standards, organizations are seeking software that can deliver end-to-end visibility and traceability across all stages of fabrication. The pressure to reduce costs, accelerate time-to-market, and maintain consistent quality has propelled a shift towards platforms that offer modular scalability and cross-functional collaboration. These systems are designed to align disparate workflows, from procurement and maintenance to quality assurance and compliance, thereby reducing manual handoffs and minimizing the risk of errors.
This executive summary provides a comprehensive overview of the current state of fabrication management software, highlighting key technological shifts, the influence of trade policies, and actionable insights for industry stakeholders. By examining market segmentation, regional adoption patterns, and leading solution providers, this report equips decision-makers with the strategic guidance needed to navigate a dynamic landscape and capitalize on emerging opportunities.
Embracing a New Era of Digital Fabrication Management
Building on the evolving landscape, three transformative forces are driving the next wave of innovation in fabrication management. First, the maturation of cloud-native architectures has unlocked unparalleled scalability, enabling manufacturers to deploy solutions across multiple facilities with minimal upfront investment. Second, the proliferation of edge computing devices is facilitating real-time monitoring of critical production metrics, empowering teams to detect anomalies before they escalate into costly disruptions. Third, the emergence of digital thread frameworks is fostering seamless data continuity, stitching together design specifications, material sourcing, and operational performance into a cohesive narrative.
Automation and artificial intelligence are no longer optional add-ons but foundational components of high-performance fabrication ecosystems. Machine learning algorithms are optimizing production schedules by dynamically reallocating resources based on machine health, inventory levels, and order deadlines. Meanwhile, robotic process automation is streamlining repetitive tasks such as data entry and report generation, allowing engineers to focus on value-added activities. Cognitive analytics platforms are also surfacing predictive insights, forecasting maintenance needs and quality deviations to ensure that every batch meets exacting standards.
Interoperability across legacy systems and emerging digital twins is becoming a standard expectation rather than a competitive differentiator. Open API configurations and standardized data schemas are facilitating plug-and-play integration across CAD tools, ERP platforms, and warehouse management systems. This new modularity enables rapid deployment of targeted upgrades without requiring a complete overhaul of existing infrastructure, reducing both implementation risk and total cost of ownership. As a result, organizations can continuously refine their operations by adopting best-in-class capabilities at a pace that aligns with their strategic objectives.
Assessing the 2025 US Tariffs Impact on Supply Chains
The scheduled implementation of modified United States tariffs in 2025 is poised to reshape the economics of raw material procurement and component sourcing across fabrication industries. With levies targeted at key import categories, organizations reliant on cross-border supply chains are reassessing vendor portfolios to mitigate cost volatility. Materials such as specialized alloys and precision machining parts may see price surges that ripple through production planning and margin projections.
Manufacturers are pursuing a dual strategy of nearshoring and supplier diversification to reduce tariff exposure. Nearshoring initiatives enable closer geographic proximity to end markets, lowering transit times and reducing the impact of import duties. Concurrently, strategic partnerships with alternative suppliers in regions unaffected by the new tariffs are gaining prominence. This pivot not only safeguards operations against sudden tariff escalations but also fosters resilience by building multi-tiered supply networks.
The interplay between tariff adjustments and currency fluctuations adds another dimension to procurement risk. Organizations that previously hedged solely on currency rates are now layering in tariff sensitivity analyses to their financial modeling. Advanced procurement tools are integrating tariff schedules directly into cost estimation engines, allowing purchasing managers to simulate “what-if” scenarios in real time. By leveraging these capabilities, fabrication leaders can optimize contract terms, align purchase orders with favorable duty structures, and uphold production continuity despite an increasingly complex regulatory environment.
Decoding Market Segmentation for Targeted Growth
A nuanced understanding of market segmentation provides clarity on where growth opportunities lie and how solution providers can tailor their offerings. By deployment mode, cloud-based platforms are witnessing accelerated uptake due to their lower upfront costs, seamless updates, and remote accessibility. On-premises installations continue to appeal to organizations with stringent data sovereignty requirements or legacy infrastructure commitments, yet the balance is clearly tipping towards cloud deployments as cybersecurity frameworks mature and hybrid architectures gain traction. This shift is prompting vendors to offer flexible subscription models that blend cloud agility with localized control.
Organizational size further delineates distinct adoption patterns. Large enterprises leverage expansive budgets and centralized IT governance to roll out enterprise-wide systems that unify fabrication across multiple sites, while small and medium enterprises prioritize rapid implementation cycles and modular functionalities that address specific pain points. In practice, mid-sized manufacturers often start with core modules such as maintenance management or quality assurance before scaling into full-suite solutions, thereby preserving capital and demonstrating return on investment in incremental stages.
Diverse end users shape requirement profiles and customization needs in distinct ways. Contract manufacturers across electronics and pharmaceuticals rely on rigorous compliance features and end-to-end traceability, while original equipment manufacturers tailor deployments to their tier status: Tier One suppliers prioritize advanced scheduling modules to meet just-in-time delivery demands, and Tier Two suppliers emphasize capacity planning tools that flex with fluctuating order volumes. Industry vertical nuances further refine feature sets. Commercial and passenger vehicle plants have unique cycle time imperatives, consumer electronics fabs demand rapid changeovers, and both discrete and process manufacturing operations require specialized integration solutions encompassing API connections and robust data migration. Across all segments, investments gravitate towards design tools, integration platforms, maintenance management, production planning, and quality assurance modules that collectively drive operational excellence.
This comprehensive research report categorizes the Fab Management Software market into clearly defined segments, providing a detailed analysis of emerging trends and precise revenue forecasts to support strategic decision-making.
- Deployment Mode
- Organization Size
- End User
- Industry Vertical
- Component
Mapping Regional Dynamics in Fab Software Adoption
Regional dynamics in the adoption of fabrication management software vary significantly across global markets. In the Americas, strategic emphasis on nearshoring and digital supply chain optimization has accelerated investment in cloud-native platforms that enable end-to-end visibility. Adoption among North American manufacturers is propelled by incentives for localization and resilient sourcing, while Latin American players are leveraging flexible subscription models to overcome infrastructure constraints and budgetary limitations.
Meanwhile, Europe, the Middle East, and Africa present a tapestry of regulatory regimes and industrial maturity levels. Western European countries lead in deploying advanced analytics and AI-driven predictive maintenance due to stringent regulatory standards and high labor costs. During this rollout, regional harmonization efforts are encouraging unified data protocols, facilitating cross-border operations. In contrast, the Middle East is rapidly modernizing fabrication hubs with greenfield investments, integrating IoT connectivity from inception. African markets, though nascent, are showing early signs of uptake in discrete manufacturing hubs that prioritize modular and cost-effective solutions.
In Asia-Pacific, heterogeneous market maturity spans from highly automated fabrication centers in Japan and South Korea to emerging economies in Southeast Asia pursuing lean manufacturing initiatives. China continues to dominate adoption volumes, investing heavily in smart factory upgrades to support its strategic manufacturing roadmap. Meanwhile, India’s growth is driven by digital skill development programs and public–private partnerships that aim to modernize legacy plants. Across the region, a growing focus on sustainability and circular economy principles is influencing the selection of quality management and maintenance modules that minimize waste and extend asset lifecycles.
This comprehensive research report examines key regions that drive the evolution of the Fab Management Software market, offering deep insights into regional trends, growth factors, and industry developments that are influencing market performance.
- Americas
- Europe, Middle East & Africa
- Asia-Pacific
Spotlight on Leading Innovators in Fab Management
Leading solution providers have intensified their efforts to differentiate through modular architectures and industry-specific capabilities. Some innovators focus on seamless integration with enterprise resource planning systems, offering prebuilt connectors that reduce deployment timelines. Others are investing in user-centric interfaces and mobile-first designs to empower shop-floor personnel with real-time insights and intuitive controls. Strategic alliances between software vendors and hardware manufacturers are also gaining traction, enabling turnkey solutions that include IoT sensors, edge computing gateways, and advanced analytics packages.
Competitive differentiation is further fueled by investment in specialized vertical modules. Vendors offering deep domain expertise in sectors such as aerospace or pharmaceuticals deliver enhanced compliance features and domain-specific automation sequences. This verticalization strategy enhances value propositions by aligning system workflows with industry standards, regulatory requirements, and best practices. Meanwhile, partnerships with academic institutions and research consortia are accelerating the development of next-generation capabilities, including digital twin frameworks and adaptive scheduling engines that learn from historical production data.
The strategic roadmaps of market leaders underscore a commitment to open ecosystems. By embracing open API standards and developer-friendly toolkits, these companies foster thriving partner networks that extend core functionality through third-party applications. This approach not only broadens the solution portfolio but also accelerates innovation cycles, as community-driven extensions address niche requirements and emerging use cases. Ultimately, the confluence of modular design, vertical specialization, and ecosystem collaboration is setting the stage for the next generation of fabrication management platforms.
This comprehensive research report delivers an in-depth overview of the principal market players in the Fab Management Software market, evaluating their market share, strategic initiatives, and competitive positioning to illuminate the factors shaping the competitive landscape.
- Siemens Digital Industries Software GmbH
- Applied Materials, Inc.
- KLA Corporation
- Brooks Automation, Inc.
- Cimetrix, Inc.
- Schneider Electric SE
- Emerson Electric Co.
Strategic Roadmap for Fab Software Leadership
To capitalize on the trends shaping the fabrication management landscape, industry leaders must adopt a strategic roadmap that balances technological innovation with organizational agility. Primary among these actions is the establishment of a cloud-first mindset, migrating core fabrication functions to scalable platforms that support continuous updates and minimize capital expenditure. By treating cloud deployment as the default option, organizations can rapidly pilot new features, enforce consistent security policies, and streamline cross-site collaboration.
Simultaneously, firms should diversify their supplier bases and implement flexible sourcing strategies to mitigate the impact of evolving trade policies. This includes qualifying alternative vendors in emerging markets, negotiating multi-year contracts with built-in tariff adjustment clauses, and leveraging real-time procurement analytics to anticipate cost fluctuations. By embedding tariff schedules and currency sensitivity analyses within procurement workflows, purchasing managers can proactively adjust order volumes and timing to optimize landed costs.
Investing in advanced analytics and digital twin capabilities is also critical. Organizations can unlock predictive insights by creating virtual replicas of production lines, simulating what-if scenarios, and stress-testing process changes before execution. This forward-looking approach reduces the risk of downtime, enhances capacity planning accuracy, and underpins a culture of continuous improvement.
Finally, cultivating a digital-ready workforce through targeted training programs and cross-functional collaboration initiatives will ensure that technological investments translate into sustainable operational gains. By equipping employees with data literacy skills and fostering a mindset of experimentation, companies can accelerate adoption rates and drive measurable performance improvements.
Methodological Framework Underpinning Market Insights
This research is underpinned by a rigorous methodological framework designed to ensure the validity and reliability of the insights presented. The analysis began with an extensive secondary research phase that incorporated peer-reviewed journals, industry white papers, and regulatory filings. Publicly available financial disclosures and trade databases were also examined to map historical trends and benchmark cost structures across key markets.
Primary research was conducted through in-depth interviews with C-level executives, factory managers, and IT directors across multiple manufacturing sectors. These conversations provided firsthand perspectives on adoption drivers, integration challenges, and strategic priorities. In addition, a series of panel discussions with software vendors and supply chain experts enriched the qualitative data set, helping to validate emerging hypotheses and uncover niche use cases.
Quantitative data was triangulated using robust analytical tools, including regression analysis and scenario modeling, to test correlations between technology investments and performance outcomes. The research team also applied a thematic coding approach to open-ended responses, identifying recurring patterns and priority areas. Together, these methods deliver a comprehensive, data-driven view of the fab management software market, ensuring that recommendations and insights are anchored in empirical evidence.
Explore AI-driven insights for the Fab Management Software market with ResearchAI on our online platform, providing deeper, data-backed market analysis.
Ask ResearchAI anything
World's First Innovative Al for Market Research
Future Outlook for Fab Management Software
The evolution of fabrication management software represents a cornerstone in the modern manufacturing revolution. From the integration of cloud-native architectures to the advancement of digital twin frameworks, the industry stands at an inflection point where digital solutions are no longer supportive tools but strategic enablers of competitive advantage.
The upcoming shifts in trade policy, particularly the 2025 tariff adjustments, underscore the importance of agility and resilience in procurement and supply chain strategies. Firms that proactively realign sourcing practices and embed tariff sensitivity into their decision-making processes will be better positioned to sustain margins and maintain uninterrupted operations.
By leveraging segmentation insights, regional adoption patterns, and the strategies of leading solution providers, stakeholders can craft informed roadmaps that align with both short-term objectives and long-term transformation goals. The convergence of technology, policy, and organizational readiness will dictate the pace of digital adoption and shape the future of fabrication management for years to come.
This section provides a structured overview of the report, outlining key chapters and topics covered for easy reference in our Fab Management Software market comprehensive research report.
- Preface
- Research Methodology
- Executive Summary
- Market Overview
- Market Dynamics
- Market Insights
- Cumulative Impact of United States Tariffs 2025
- Fab Management Software Market, by Deployment Mode
- Fab Management Software Market, by Organization Size
- Fab Management Software Market, by End User
- Fab Management Software Market, by Industry Vertical
- Fab Management Software Market, by Component
- Americas Fab Management Software Market
- Europe, Middle East & Africa Fab Management Software Market
- Asia-Pacific Fab Management Software Market
- Competitive Landscape
- ResearchAI
- ResearchStatistics
- ResearchContacts
- ResearchArticles
- Appendix
- List of Figures [Total: 26]
- List of Tables [Total: 547 ]
Connect with Ketan Rohom for Exclusive Market Insights
To secure comprehensive market intelligence and actionable strategies, we invite you to connect with Ketan Rohom, Associate Director of Sales & Marketing. Engage directly to explore customized insights, discuss your specific business challenges, and unlock the full potential of the fab management software landscape.
Reach out today to obtain the detailed market research report and equip your leadership team with the data, analysis, and strategic recommendations needed to thrive in an increasingly complex manufacturing environment. Partnering with our expert team ensures you stay ahead of emerging trends and make data-driven decisions with confidence.
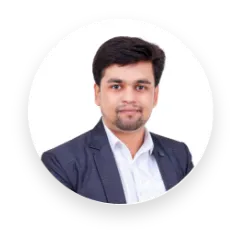
- How big is the Fab Management Software Market?
- What is the Fab Management Software Market growth?
- When do I get the report?
- In what format does this report get delivered to me?
- How long has 360iResearch been around?
- What if I have a question about your reports?
- Can I share this report with my team?
- Can I use your research in my presentation?