Introduction to the Fast Linear Servo Tool Holder System
In advanced manufacturing, the fast linear servo tool holder system has emerged as a critical enabler of high-precision and responsive machining. By combining linear servo drives with robust tool holding mechanisms, this technology delivers rapid tool changes, instantaneous positioning, and consistent clamping force under heavy loads. These attributes translate into reduced cycle times, improved surface finishes, and heightened throughput in operations ranging from aerospace component production to precision mold making.
As production landscapes evolve toward greater automation, the demand for systems that seamlessly integrate with CNC machines, robotic cells, and smart factory platforms has grown exponentially. Fast linear servo tool holders offer a bridge between mechanical rigidity and digital control, enabling real-time feedback loops and closed-loop position corrections that drive productivity gains. Equally important, they support predictive maintenance protocols by tracking torque signatures and wear indicators through embedded sensors.
This executive summary explores the transformative shifts shaping this market, analyzes the cumulative impact of U.S. tariffs slated for 2025, presents segmentation and regional insights, highlights key industry players, and offers actionable recommendations for decision-makers seeking to maintain a competitive edge in an era of rapid innovation.
Transformative Shifts in the Manufacturing Landscape
Manufacturing is undergoing a paradigm shift driven by the convergence of digitalization, advanced materials, and autonomous operations. The integration of fast linear servo tool holders into Industry 4.0 ecosystems exemplifies this transformation, as these systems enable seamless data exchange between tool, machine and enterprise resource planning platforms. High-speed operation and precision control have become non-negotiable requirements in sectors such as electronics assembly, medical device fabrication and automotive powertrain machining.
Simultaneously, the proliferation of collaborative robots alongside traditional CNC cells is redefining workload distribution and programming methodologies. Tool holders capable of rapid dynamic adjustments and predictive self-calibration are unlocking new levels of flexibility across mixed-model production lines. Additive manufacturing processes are also intersecting with subtractive techniques, with hybrid systems demanding tool holders that can withstand both high thermal loads and the inertial forces of high-velocity machining.
Advances in thermal performance, enabled by innovative materials such as ceramic components and composite alloys, are extending service intervals and reducing energy consumption. Meanwhile, the rise of edge computing and digital twin simulations allows engineers to optimize tool path strategies, ensure regulatory compliance and anticipate maintenance requirements before a machine ever turns a spindle.
Cumulative Impact of United States Tariffs 2025
The introduction of additional duties on imported machine components and high-tensile alloys scheduled for 2025 has prompted strategic realignments across the supply chain. Manufacturers reliant on offshore production of linear servo modules are evaluating the cost ramifications as maintenance costs and production expenses rise in tandem with tariff-induced surcharges. Some have accelerated initiatives to qualify domestic suppliers of stainless steel and titanium alloys, while others are investing in localized multi-axis machining capabilities to offset potential investment returns erosion.
Beyond direct component pricing, the tariffs have had a cascading effect on operational efficiency. Tooling systems that historically depended on precision bearings and proprietary electronic drives from targeted regions must now account for longer lead times and alternative sourcing strategies. This ripple effect has elevated the importance of partnership models that emphasize co-development and joint risk sharing, ensuring that critical material compositions and performance attributes remain accessible.
Despite these headwinds, the industry is leveraging the disruption to foster resilience. Companies are conducting scenario analyses across regulatory impact scenarios, deploying additive manufacturing techniques for rapid prototyping of tool holders, and exploring composite materials that circumvent tariff classifications. In doing so, they are not only mitigating cost structure pressures but also uncovering fresh opportunities for differentiation.
Critical Segmentation Highlights for Strategic Decision-Making
A holistic understanding of this market requires examining multiple dimensions. Based on market dynamics, stakeholders encounter regulatory impact challenges, while being propelled by drivers such as automation trends and opportunities in digital integration, all set against evolving technology trends. From the lens of application categories, fast linear servo tool holders serve industrial automation and precision manufacturing, extend into robotic integration with both autonomous and collaborative robots, and fortify tooling systems in high-speed machining centers.
Performance attributes reveal a balance between durability and load capacity, enhanced by speed and accuracy that bifurcate into high-speed operation and precision control, and supported by robust thermal performance for extended run times. Material composition analysis highlights the use of ceramic components and composite materials, alongside versatile thermoplastic composites and high-tensile alloys differentiated into stainless steel and titanium variants.
Manufacturing processes range from 3D printing and additive manufacturing to laser cutting, with computer numeric control machining further refined through multi-axis machining techniques. Cost structure considerations encompass investment returns, maintenance costs, operational efficiency and production expenses. Finally, end user profiles span automation service providers and industrial enterprises, include original equipment manufacturers in aerospace, automotive and electronics, and address the unique demands of small and medium enterprises.
This comprehensive research report categorizes the Fast Linear Servo Tool Holder System market into clearly defined segments, providing a detailed analysis of emerging trends and precise revenue forecasts to support strategic decision-making.
- Market Dynamics
- Application Categories
- Performance Attributes
- Material Composition
- Manufacturing Processes
- Cost Structure
- End User Profiles
Regional Dynamics Shaping Fast Linear Servo Tool Holder Deployment
North America continues to lead adoption, driven by a robust industrial automation ecosystem and stringent regulatory standards for precision and safety. Advanced research institutions and strategic public-private partnerships bolster capabilities in the Americas, where manufacturers prioritize operational efficiency and direct supplier relationships to navigate tariff complexities.
In Europe, Middle East & Africa, mature manufacturing hubs in Germany, Italy and France capitalize on sophisticated tooling systems and performance attributes optimized for lean production. Meanwhile, emerging economies in the Middle East invest in smart factory projects to diversify their industrial bases, and African markets show growing interest in localized additive manufacturing solutions to reduce reliance on imported high-tensile alloys.
The Asia-Pacific region exhibits the fastest acceleration in deployment, anchored by large-scale electronics and automotive production in China, Japan and South Korea. Investments in multi-axis machining and collaborative robots are particularly pronounced, ensuring that manufacturers across this region can meet stringent export quality requirements while advancing digital twin simulations and edge analytics to maintain competitive unit costs.
This comprehensive research report examines key regions that drive the evolution of the Fast Linear Servo Tool Holder System market, offering deep insights into regional trends, growth factors, and industry developments that are influencing market performance.
- Americas
- Asia-Pacific
- Europe, Middle East & Africa
Competitive Landscape and Leading Players
The competitive landscape is defined by an array of global leaders and innovative challengers. ABB Ltd. and Fanuc Corporation drive robotics integration, while Bosch Rexroth AG, Siemens AG and Schneider Electric SE emphasize closed-loop control and digitalization. Traditional machine tool providers such as DMG Mori AG, Makino Milling Machine Co., Ltd. and Mazak Corporation maintain a strong presence through multi-axis machining expertise, as do Haas Automation, Inc. and Hurco Companies, Inc. with versatile CNC platforms.
Manufacturers like Amada Co., Ltd. and TRUMPF GmbH + Co. KG lead in laser cutting and hybrid processing, whereas Bystronic Machine Tools Inc. and Sodick Co., Ltd. focus on precision manufacturing for electronics applications. KUKA Robotics GmbH, Yaskawa Electric Corporation and Doosan Machine Tools Co., Ltd. deliver advanced robotic cells empowered by high-speed operation and precision control. Companies such as Emerson Electric Co. and Parker Hannifin Corporation support hydraulic and pneumatic tool clamping systems, while Fidex Machines Incorporated and GF Machining Solutions GmbH innovate around additive manufacturing and thermal performance.
Okuma Corporation, Mitsubishi Electric Corporation and Komatsu Ltd. continue to expand service networks and predictive maintenance offerings, and smaller firms like Perske Machinery Inc. and Tornos SA differentiate through specialized tool holding solutions for niche industries.
This comprehensive research report delivers an in-depth overview of the principal market players in the Fast Linear Servo Tool Holder System market, evaluating their market share, strategic initiatives, and competitive positioning to illuminate the factors shaping the competitive landscape.
- ABB Ltd.
- Amada Co., Ltd.
- Bosch Rexroth AG
- Brother Industries, Ltd.
- Bystronic Machine Tools Inc.
- DMG Mori AG
- Doosan Machine Tools Co., Ltd.
- Emerson Electric Co.
- Fanuc Corporation
- Festo AG & Co. KG
- Fidex Machines Incorporated
- GF Machining Solutions GmbH
- Haas Automation, Inc.
- Hurco Companies, Inc.
- Komatsu Ltd.
- KUKA Robotics GmbH
- Makino Milling Machine Co., Ltd.
- Matsuura Machinery Corp.
- Mazak Corporation
- Mitsubishi Electric Corporation
- Okuma Corporation
- Parker Hannifin Corporation
- Perske Machinery Inc.
- Rockwell Automation, Inc.
- Schneider Electric SE
- Siemens AG
- Sodick Co., Ltd.
- Tornos SA
- TRUMPF GmbH + Co. KG
- Yaskawa Electric Corporation
Strategic Actions to Lead in the Fast Linear Servo Tool Holder Space
Invest in materials and digital integration: Evaluate emerging ceramic and composite alloys while embedding IoT-enabled sensors for real-time performance monitoring. Build strategic alliances with autonomous and collaborative robot manufacturers to ensure seamless tool holder interoperability. Diversify supply chains by qualifying local stainless steel and titanium suppliers and by leveraging additive manufacturing for rapid prototyping to reduce dependency on tariff-exposed imports. Enhance R&D capabilities: Establish multi-axis machining test beds and digital twin simulations to accelerate development cycles and optimize thermal and load-capacity attributes under realistic operating conditions. Implement predictive maintenance frameworks that utilize torque and vibration analytics to extend service intervals and minimize unplanned downtime. Tailor solutions for varied end users: Offer modular tool holder platforms that address the specific requirements of aerospace, automotive and electronics OEMs, as well as adaptable packages for small and medium enterprises seeking cost-effective entry points. Advance training and support: Develop comprehensive digital training modules that guide process engineers and technicians through calibration, diagnostics and safety protocols, ensuring rapid adoption and sustained performance gains.
Explore AI-driven insights for the Fast Linear Servo Tool Holder System market with ResearchAI on our online platform, providing deeper, data-backed market analysis.
Ask ResearchAI anything
World's First Innovative Al for Market Research
Conclusion: Charting the Path Forward
The fast linear servo tool holder system stands at the crossroads of innovation and industrial necessity. By aligning development roadmaps with the transformative shifts in automation, additive manufacturing and materials science, organizations can secure differentiated positions in both mature and emerging markets. Navigating the financial and logistical challenges posed by 2025 tariffs requires agile supply chain strategies and investments in domestic sourcing and rapid prototyping.
Key segmentation insights underscore the importance of tailoring solutions across market dynamics, application categories, performance attributes, material compositions, manufacturing processes, cost structures and end user profiles. Regional nuances, from the Americas’ technology leadership to Asia-Pacific’s scale advantages, demand targeted go-to-market approaches. Meanwhile, collaboration with leading companies drives ecosystem synergies that accelerate innovation and ensure interoperability.
By embracing these principles, industry leaders can not only mitigate risks from regulatory shifts but also capitalize on emerging opportunities in smart manufacturing, predictive maintenance and hybrid machining environments to fuel sustainable growth.
This section provides a structured overview of the report, outlining key chapters and topics covered for easy reference in our Fast Linear Servo Tool Holder System market comprehensive research report.
- Preface
- Research Methodology
- Executive Summary
- Market Overview
- Market Dynamics
- Market Insights
- Cumulative Impact of United States Tariffs 2025
- Fast Linear Servo Tool Holder System Market, by Market Dynamics
- Fast Linear Servo Tool Holder System Market, by Application Categories
- Fast Linear Servo Tool Holder System Market, by Performance Attributes
- Fast Linear Servo Tool Holder System Market, by Material Composition
- Fast Linear Servo Tool Holder System Market, by Manufacturing Processes
- Fast Linear Servo Tool Holder System Market, by Cost Structure
- Fast Linear Servo Tool Holder System Market, by End User Profiles
- Americas Fast Linear Servo Tool Holder System Market
- Asia-Pacific Fast Linear Servo Tool Holder System Market
- Europe, Middle East & Africa Fast Linear Servo Tool Holder System Market
- Competitive Landscape
- ResearchAI
- ResearchStatistics
- ResearchContacts
- ResearchArticles
- Appendix
- List of Figures [Total: 30]
- List of Tables [Total: 596 ]
Contact for In-Depth Research Insights
For a comprehensive exploration of these insights and to gain a competitive edge in the fast linear servo tool holder domain, reach out to Ketan Rohom, Associate Director of Sales & Marketing. Ketan can provide full access to the in-depth research report, detailed data analyses and tailored consultation to support your strategic initiatives. Contact him today to unlock the actionable intelligence your organization needs.
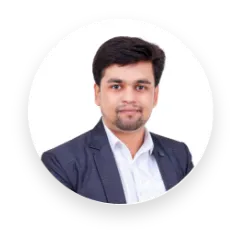
- When do I get the report?
- In what format does this report get delivered to me?
- How long has 360iResearch been around?
- What if I have a question about your reports?
- Can I share this report with my team?
- Can I use your research in my presentation?