The Fiber Reinforced Composites Market size was estimated at USD 236.51 billion in 2024 and expected to reach USD 257.86 billion in 2025, at a CAGR 8.61% to reach USD 388.34 billion by 2030.

Setting the Stage for Fiber Reinforced Innovations
Fiber reinforced composites have become indispensable in modern engineering, offering a remarkable combination of high strength, low weight, and design flexibility that traditional materials cannot match. As industries from aerospace to automotive and wind energy seek to optimize performance and efficiency, these advanced materials deliver critical benefits such as improved fuel economy, enhanced corrosion resistance, and reduced lifecycle costs. The growing emphasis on carbon footprint reduction and product durability has further accelerated their adoption across diverse sectors.
Technological advances in fiber production and resin formulation have enabled manufacturers to fine-tune composite properties to exacting specifications. These innovations support the development of next-generation structures capable of withstanding extreme environments and dynamic loads. Simultaneously, evolving manufacturing techniques are driving down cycle times and material waste, making composites more accessible to volume applications.
A complex global supply chain underpins this market, linking raw material suppliers, processing technology providers, and end-use manufacturers. Regional policies and trade regulations continuously reshape sourcing strategies, while increasing collaboration between material scientists and OEMs fuels ongoing product evolution. Against this dynamic backdrop, stakeholders must remain vigilant to emerging trends and disruptive forces that will define the future of fiber reinforced composites.
Emerging Forces Shaping the Composite Materials Arena
The fiber reinforced composite landscape is undergoing a profound transformation driven by innovations in material science and digital manufacturing. Advanced formulations incorporating nanoscale reinforcements are enhancing mechanical performance while reducing overall weight. At the same time, the integration of automation and robotics in layup and curing processes is boosting production speed and consistency, opening new possibilities for high-volume applications.
Sustainability imperatives are reshaping raw material choices and lifecycle strategies. Manufacturers are increasingly exploring bio-based resins, recycled fibers, and closed-loop manufacturing systems to minimize environmental impact. Circular economy principles are not only gaining traction in research laboratories but are also finding practical implementation in pilot production lines.
End-use markets are equally dynamic. In aerospace, next-generation aircraft frames rely on composites to achieve unprecedented range and efficiency. The automotive sector is accelerating the deployment of lightweight structures for electric vehicles, while the wind energy industry is designing longer blades with optimized lay-up architectures. Across these shifts, strategic partnerships between material suppliers, technology firms, and OEMs are becoming the norm, enabling accelerated product development and faster time-to-market.
Unraveling the Impact of 2025 U.S. Tariff Measures
The introduction of new U.S. tariffs in 2025 has introduced significant complexities into global composite supply chains. Levies on key precursors such as carbon fiber and specialty resins have increased landed costs for imported materials, compelling many manufacturers to reassess sourcing strategies. This adjustment has triggered a measurable uptick in domestic fiber production capacity as regional suppliers expand to capture shifted demand.
Cost pressures are rippling through the value chain, prompting OEMs to explore alternative fiber sources and resin systems. Some have accelerated qualification of locally produced materials, while others have negotiated long-term supply agreements to hedge against further tariff escalations. Logistics routes have also diversified, with increased direct shipping from Asia-Pacific hubs to avoid intermediate transshipments that would incur additional duties.
Despite these challenges, the tariff landscape has galvanized investment in regional processing infrastructure. New composite manufacturing facilities are emerging in the Americas, often in proximity to end-use customers, to reduce lead times and transportation costs. This reshaping of production footprints underscores a broader trend toward supply chain resilience and near-market manufacturing.
Deep Dive into Composite Market Segmentation
When examining the market by fiber type, aramid fiber has established itself as a critical choice for applications requiring exceptional damage tolerance and thermal stability. Within this category, meta-aramid and para-aramid variants address needs ranging from ballistic protection to high-stress structural components. Carbon fiber, segmented into high modulus, intermediate modulus, standard modulus, and ultra-high modulus grades, supports a spectrum of stiffness and strength requirements across aerospace and transportation sectors. Glass fiber remains a cost-effective option for large-volume applications where structural performance and affordability must balance.
Resin type further differentiates the market between thermoplastics and thermosets. High-performance thermoplastics such as polyamide, polyether ether ketone, polyphenylene sulfide, and polypropylene offer recyclability and rapid cycle times, appealing to automotive and consumer goods manufacturers. Thermoset resins including epoxy, phenolic, polyester, and vinyl ester continue to dominate in sectors demanding superior chemical resistance and thermal stability, such as electrical insulation and marine structures.
Manufacturing processes define another axis of specialization. Autoclave molding, compression molding, filament winding, and hand layup remain essential for high-precision, load-bearing parts in aerospace and defense. In parallel, injection molding, pultrusion, and resin transfer molding are gaining share through automation and cost efficiency, enabling widespread adoption in wind energy components and structural automotive parts.
Application segmentation reveals a diverse landscape. Aerospace and defense persist as the largest consumers of advanced composites, while automotive and transportation increasingly leverage lightweight structures for electric vehicles. Construction and infrastructure applications are adopting prefabricated composite panels for durability and rapid assembly, even as electrical and electronics industries explore composite housings to meet miniaturization and heat management challenges. Marine, sports and leisure, and wind energy segments each pursue tailored composite solutions to overcome performance hurdles and meet sustainability targets.
Reinforcement form also influences material selection. Continuous fiber formats-multiaxial, unidirectional, and woven-provide high structural integrity for critical load-bearing parts. Discontinuous fiber forms such as chopped strand mat, needled mat, and nonwoven textiles offer design flexibility and simplified processing for composite panels and molded components. These reinforcement choices allow engineers to optimize lay-up strategies for cost, performance, and manufacturability.
This comprehensive research report categorizes the Fiber Reinforced Composites market into clearly defined segments, providing a detailed analysis of emerging trends and precise revenue forecasts to support strategic decision-making.
- Fiber Type
- Resin Type
- Manufacturing Process
- Application
- Reinforcement Form
Regional Dynamics Driving Composite Demand
In the Americas, investment in domestic fiber production and processing capacity has accelerated as a response to shifting trade policies. Major automotive OEMs and aerospace primes are re-engineering their supply chains to reduce dependence on imported materials, resulting in the establishment of new composite fabrication facilities near key manufacturing hubs. Public and private partnerships are also fostering R&D programs aimed at advancing sustainable resin systems and next-generation fiber architectures.
Across Europe, the Middle East, and Africa, regulatory frameworks and sustainability goals are driving composite adoption in wind energy and construction markets. Offshore wind developers are commissioning longer, lighter blades that demand precise material performance, while infrastructure authorities are piloting composite bridge components for corrosion resistance and rapid deployment. Collaboration among governments, research institutes, and industry leaders is fostering innovation clusters that accelerate product development and certification processes.
The Asia-Pacific region remains a hotbed of manufacturing growth, driven by expanding automotive production and renewable energy investments. Manufacturers are scaling up filament winding and pultrusion lines to serve the wind market, while automotive tier suppliers are integrating advanced composites into electric vehicle platforms. Government incentives in several markets support technology transfer and localization of high-performance fiber production, creating a more balanced global supply ecosystem.
This comprehensive research report examines key regions that drive the evolution of the Fiber Reinforced Composites market, offering deep insights into regional trends, growth factors, and industry developments that are influencing market performance.
- Americas
- Europe, Middle East & Africa
- Asia-Pacific
Leading Players Steering Industry Trajectories
Leading composite material suppliers have pursued strategic partnerships and joint ventures to broaden their global footprints and secure critical raw material access. Investments in capacity expansion have targeted both fiber extrusion facilities and resin synthesis plants, ensuring a more resilient supply base. Simultaneously, technology providers have intensified their focus on digitalization, offering process-monitoring platforms and predictive analytics to optimize curing cycles and reduce production scrap.
Some enterprises have differentiated themselves through vertically integrated models, combining fiber, resin, and component manufacturing under one roof to streamline timelines and lower total cost of ownership. Others have carved out niches by specializing in high-end applications such as aerospace structural elements or high-performance sports equipment. These specialized players often maintain close collaborations with research universities and defense agencies to maintain a pipeline of cutting-edge innovations.
Mergers and acquisitions remain common as companies seek to expand product portfolios and geographic reach. Targeted acquisitions of automation technology firms and software providers are enabling more integrated offerings, from material formulation to final part inspection. In parallel, leading composite manufacturers are entering aftermarket services, offering repair and maintenance solutions that extend component life cycles and reinforce customer relationships.
This comprehensive research report delivers an in-depth overview of the principal market players in the Fiber Reinforced Composites market, evaluating their market share, strategic initiatives, and competitive positioning to illuminate the factors shaping the competitive landscape.
- Owens Corning
- Toray Industries, Inc.
- Teijin Limited
- SGL Carbon SE
- Hexcel Corporation
- Solvay SA
- Mitsubishi Chemical Holdings Corporation
- Johns Manville Corporation
- Jushi Group Co., Ltd.
- Gurit Holding AG
Strategic Imperatives for Industry Trailblazers
To thrive in this evolving market, industry leaders should prioritize the diversification of their supply chains by qualifying multiple fiber and resin sources across different regions. This approach will mitigate tariff and logistics risks while enabling faster response to end-user demands. At the same time, investments in digital process control and real-time quality monitoring will reduce cycle times and improve yield, underpinning cost competitiveness in high-volume segments.
Companies that embed sustainability at the core of their product development will gain a strategic advantage. Exploring bio-based resins, recycled reinforcement forms, and closed-loop manufacturing systems will position organizations as preferred partners for customers with ambitious environmental targets. Collaborative innovation programs involving OEMs, research institutes, and policy bodies can accelerate certification of new materials and shorten time to market.
Finally, organizations should evaluate entry opportunities in emerging end-use markets such as electric mobility and distributed renewable energy. Establishing early pilot programs with marquee customers will generate valuable performance data and foster co-development partnerships. By combining a robust supply chain, digital manufacturing capabilities, and sustainability leadership, companies can capture growth and build long-term resilience.
Robust Methodology Underpinning Our Analysis
This analysis draws upon a rigorous blend of secondary and primary research. The secondary phase involved an exhaustive review of industry publications, technical papers, trade association data, and regulatory filings to establish a comprehensive understanding of technological trends and policy impacts. Publicly available company reports and patent databases provided insights into competitive strategies and emerging material innovations.
Primary research included in-depth interviews with senior executives, materials scientists, design engineers, and procurement heads across the composite value chain. These conversations offered first-hand perspectives on market dynamics, capacity planning, cost pressures, and innovation roadmaps. Responses were validated through cross-referencing supply-side data and end-use demand metrics to ensure consistency.
Data triangulation techniques were employed to reconcile discrepancies between sources, while qualitative insights were synthesized to contextualize quantitative findings. All information was subjected to multiple quality checks, with an emphasis on eliminating bias and ensuring that the analysis reflects the most recent developments. The methodology consciously avoided speculative forecasting, focusing instead on fact-based evaluation of structural shifts and current market realities.
Explore AI-driven insights for the Fiber Reinforced Composites market with ResearchAI on our online platform, providing deeper, data-backed market analysis.
Ask ResearchAI anything
World's First Innovative Al for Market Research
Synthesizing Insights for Strategic Clarity
Fiber reinforced composites stand at the forefront of material innovation, offering unmatched performance and design versatility that spans multiple industries. The market is being reshaped by transformative technologies, shifting trade policies, and evolving end-use requirements, underscoring the need for strategic agility. Detailed segmentation analysis reveals the nuanced preferences across fiber types, resin systems, manufacturing processes, and applications, while regional studies highlight how local policies and infrastructure investments drive demand.
Key players have responded with capacity expansions, vertical integration, and digital process enhancements to navigate supply chain complexities and cost pressures. Their actions illustrate both the challenges and opportunities inherent in a market increasingly defined by sustainability mandates and near-market manufacturing strategies. The tactical recommendations outlined herein offer a roadmap for companies seeking to fortify their positions and capture value in this dynamic landscape.
In sum, a clear understanding of segmentation drivers, regional dynamics, and competitive responses is essential for informed decision-making. Organizations that integrate supply chain resilience, digital innovation, and sustainability leadership will be best placed to leverage the full potential of fiber reinforced composites and achieve lasting competitive advantage.
This section provides a structured overview of the report, outlining key chapters and topics covered for easy reference in our Fiber Reinforced Composites market comprehensive research report.
- Preface
- Research Methodology
- Executive Summary
- Market Overview
- Market Dynamics
- Market Insights
- Cumulative Impact of United States Tariffs 2025
- Fiber Reinforced Composites Market, by Fiber Type
- Fiber Reinforced Composites Market, by Resin Type
- Fiber Reinforced Composites Market, by Manufacturing Process
- Fiber Reinforced Composites Market, by Application
- Fiber Reinforced Composites Market, by Reinforcement Form
- Americas Fiber Reinforced Composites Market
- Europe, Middle East & Africa Fiber Reinforced Composites Market
- Asia-Pacific Fiber Reinforced Composites Market
- Competitive Landscape
- ResearchAI
- ResearchStatistics
- ResearchContacts
- ResearchArticles
- Appendix
- List of Figures [Total: 26]
- List of Tables [Total: 514 ]
Connect with Ketan Rohom to Secure Your Market Report
To explore the full breadth of these insights and access detailed data, reach out to Ketan Rohom, Associate Director, Sales & Marketing at 360iResearch. He can guide you through tailored solutions that align with your strategic goals and facilitate an informed decision on acquiring the complete market research report. Engage with him to unlock competitive intelligence and position your organization at the forefront of the fiber reinforced composite industry.
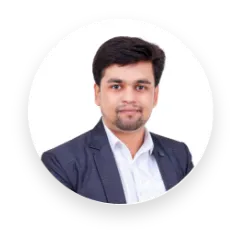
- How big is the Fiber Reinforced Composites Market?
- What is the Fiber Reinforced Composites Market growth?
- When do I get the report?
- In what format does this report get delivered to me?
- How long has 360iResearch been around?
- What if I have a question about your reports?
- Can I share this report with my team?
- Can I use your research in my presentation?