Introduction to Fiberglass Reinforced Thermoplastics
Thermoplastic composites reinforced with fiberglass have emerged as pivotal materials in industries ranging from automotive to aerospace, offering an exceptional balance of strength, weight reduction, and design flexibility. As global manufacturers push to meet stringent performance and sustainability criteria, fiberglass lies at the heart of advanced thermoplastic solutions, unlocking unprecedented opportunities for product innovation and cost optimization. This executive summary delves into the evolving dynamics of the fiberglass reinforcement market, spotlighting technological advancements, regulatory influences, and strategic imperatives that will shape competitive positioning over the coming years.
By exploring transformative shifts, tariff impacts, segmentation nuances, regional trends, and key players’ strategies, this report equips decision-makers with a clear understanding of the factors driving adoption and the actions required to capitalize on growth avenues. Whether evaluating new material formulations or refining supply chain strategies, readers will gain a comprehensive perspective on how fiberglass reinforcement can reinforce both product performance and bottom-line outcomes.
Transformative Shifts Reshaping Thermoplastic Composites
The landscape of thermoplastic composites has undergone a profound transformation driven by advances in fiber treatments, processing methods, and sustainability mandates. Surface functionalization techniques now enable stronger interfacial bonding between glass fibers and polymer matrices, resulting in composites that rival traditional metals in tensile strength while delivering superior corrosion resistance and cyclic durability. Concurrently, the rise of hybrid composites-combining fiberglass with carbon or natural fibers-has introduced tailored solutions that optimize cost-performance balance for specific applications.
On the manufacturing front, automated deposition systems and real-time quality monitoring have reduced production variability and enhanced throughput. Additive manufacturing platforms are beginning to integrate fiberglass preforms directly into printable thermoplastic filaments, opening doors to complex geometries and rapid prototyping. At the same time, sustainability considerations-spurred by circular economy regulations-have accelerated demand for high-recyclability fiber options and process-efficient resin systems. Together, these shifts are redefining design paradigms and compelling original equipment manufacturers to adopt more agile material strategies.
Analyzing the 2025 United States Tariffs Impact
The United States’ imposition of elevated tariffs on imported fiberglass materials has generated immediate cost pressures across supply chains, prompting buyers to reevaluate sourcing strategies. With duty rates scheduled to rise further in 2025, many downstream fabricators have accelerated local supplier qualification, fostering growth in domestic capacity. However, this localization trend carries its own challenges: raw glass feedstock availability is constrained, and U.S. production must scale rapidly to meet quality and volume demands without compromising consistency.
Meanwhile, buyers are exploring tariff engineering solutions, such as blending lower-duty fiberglass with premium batches or leveraging Free Trade Agreement provisions where eligible. Collaborative partnerships with regional fiber manufacturers have also emerged as a tactical response, offering co-investment models in processing infrastructure and shared risk in product development. In sum, the tariff landscape is catalyzing a reconfiguration of global supply networks, driving a cautious but decisive shift toward diversified and regionally balanced procurement.
Key Segmentation Insights in Thermoplastic Reinforcement
In dissecting market segmentation, several core dimensions reveal where fiberglass reinforcement will deliver the most value. Product type breakdown underscores that chopped strands, with their cost-effectiveness and adaptability to injection molding, dominate high-volume applications, particularly when available in both standard and high-performance fiber lengths. Mats and felts continue to serve compression molding sectors where uniform fiber distribution and surface finish are critical, while milled fibers-ranging from coarse to fine-enable precise viscosity control in extrusion and pultrusion processes. Roving remains essential for filament winding tasks where continuous fiber orientation dictates strength characteristics.
Reinforcement form choices further illustrate the balance between continuous profiles, prized for directional mechanical properties, and discontinuous formats, which encompass non-woven flow style mediums for automotive interiors and random orientation alignments suited to injection molding versatility. Examining manufacturing processes, injection molding retains a firm foothold in high-volume production-now supported by short-run capabilities for rapid product iterations-while compression molding and extrusion deliver economical solutions for thicker cross-sections. Filament winding and pultrusion maintain niche leadership in pressure vessels, pipes, and structural profiles that demand consistent fiber continuity.
Fiber type segmentation reveals that E-Glass remains the workhorse thanks to its low cost and electrical insulation, with subvariants tailored for high-temperature resistance or low dielectric properties. C-Glass applications focus on chemical resistance, whereas S-Glass fibers, offering high strength and reduced density, address weight-sensitive aerospace components. Application-focused analysis highlights aerospace adoption for fuselage components and wing panels where fatigue resistance is mandatory; automotive uptake in chassis, engine blocks, and interior elements where crashworthiness and aesthetics converge; construction uses in architectural composites and reinforced rebar aimed at extending service life; and electrical & electronics deployments in circuit boards and insulation where dielectric integrity is non-negotiable.
Thermoplastic resin selection exerts a profound effect on composite performance. Polyamide formulations-spanning Nylon 6 and Nylon 6/6-provide a balance of toughness and chemical resistance; polycarbonate supports transparency and impact resilience; polypropylene, available as copolymer or homopolymer grades, enables economical exterior trims and consumer goods. End-user industries from consumer furniture and sporting goods through medical devices, rehabilitation equipment, and machinery components reflect the versatile nature of fiberglass-reinforced thermoplastics. Finally, recycling potential stratifies products into high-recyclability loops for closed-cycle applications, while low-recyclability components-those incorporating non-degradable binders or restricted additives-demand novel reclaiming strategies to meet sustainability goals.
This comprehensive research report categorizes the Fiberglass for Thermoplastics Reinforcement market into clearly defined segments, providing a detailed analysis of emerging trends and precise revenue forecasts to support strategic decision-making.
- Product Type
- Reinforcement Form
- Manufacturing Process
- Fiber Type
- Application
- Thermoplastic Resin Type
- End-User Industry
- Recycling Potential
Regional Dynamics Driving Market Adoption
Regional adoption of fiberglass-reinforced thermoplastics exhibits notable distinctions across the Americas, EMEA, and Asia-Pacific. In the Americas, strong automotive and aerospace footprints underpin steady demand, with investments directed toward localizing chopped strand and roving production to mitigate import tariff exposure. Infrastructure spending in construction, combined with consumer appetite for lightweight sporting goods and furniture, further propels market expansion.
Within Europe, the Middle East, and Africa, regulatory frameworks emphasizing recyclability and carbon footprint reduction drive interest in advanced composites, particularly in high-value transportation and electrical applications. Collaborative research clusters in Western Europe are pioneering S-Glass variants for next-generation aircraft, while Middle Eastern petrochemical hubs leverage local resources to boost C-Glass manufacturing. Africa’s nascent industrialization efforts hint at emerging opportunities in construction and energy sectors.
Asia-Pacific commands the largest share of global fiberglass output, with China, Japan, and India leading production of E-Glass and high-temperature E-Glass subtypes. Rapid urbanization and automotive electrification in the region fuel robust demand for high-strength, electrically insulating composites. Southeast Asian economies are evolving into specialized extrusion and pultrusion service centers, benefiting from lower labor costs and improving logistics infrastructure.
This comprehensive research report examines key regions that drive the evolution of the Fiberglass for Thermoplastics Reinforcement market, offering deep insights into regional trends, growth factors, and industry developments that are influencing market performance.
- Americas
- Asia-Pacific
- Europe, Middle East & Africa
Competitive Landscape: Leading Fiberglass Providers
The competitive landscape is defined by both global champions and specialized regional players, each investing in fiber innovation, process optimization, and partnership ecosystems. 3B Fibreglass and Chongqing Polycomp International Corporation have built vertically integrated platforms that streamline raw glass to finished fiber conversion, while Owens Corning and Johns Manville leverage extensive distribution networks to offer tailored reinforcement solutions worldwide. AGY Holding Corp. focuses on high-performance S-Glass fibers for aerospace and defense applications, whereas Jushi Group and China Fiberglass Co., Ltd. emphasize cost leadership in E-Glass roving and chopped strands.
In Japan, Nippon Electric Glass and Asahi Fiber Glass Company Ltd. drive advancements in low-dielectric fiberglass formulations, targeting electronics markets that demand ultra-thin circuit substrates. Saint-Gobain Vetrotex and PFG Fiber Glass Corporation reinforce their positions through strategic partnerships with resin compounders, enhancing end-to-end composite offerings. Taishan Fiberglass Inc. and Vetrotex India Private Limited anchor regional growth by investing in local capacity expansions and service support hubs, ensuring rapid response to evolving customer requirements.
This comprehensive research report delivers an in-depth overview of the principal market players in the Fiberglass for Thermoplastics Reinforcement market, evaluating their market share, strategic initiatives, and competitive positioning to illuminate the factors shaping the competitive landscape.
- 3B Fibreglass
- AGY Holding Corp.
- Ahlstrom-Munksjö
- Asahi Fiber Glass Company Ltd.
- China Fiberglass Co., Ltd.
- Chongqing Polycomp International Corporation (CPIC)
- Johns Manville
- Jushi Group Co., Ltd.
- Nippon Electric Glass Co., Ltd.
- Owens Corning
- PFG Fiber Glass Corporation
- Saint-Gobain Vetrotex
- Taishan Fiberglass Inc.
- Vetrotex India Private Limited
Strategic Recommendations for Industry Leaders
To navigate evolving market complexities, industry leaders must prioritize five strategic imperatives. First, diversifying supply chains across multiple geographies will alleviate tariff-related cost volatility and strengthen resilience against raw material disruptions. Second, investing in advanced fiber surface treatments and hybrid composite development will address stringent performance and sustainability demands, differentiating product portfolios.
Third, establishing co-innovation partnerships with key OEMs can accelerate validation cycles and reduce time to market for application-specific solutions, particularly in high-growth sectors like electric vehicles and renewable energy infrastructure. Fourth, implementing digital twin and real-time quality assurance systems in manufacturing operations will enhance consistency, minimize scrap rates, and optimize resource utilization. Finally, embedding circular economy principles-such as designing for disassembly and closing material loops through chemical recycling-will align offerings with regulatory requirements and corporate sustainability commitments, amplifying both environmental and financial performance.
Explore AI-driven insights for the Fiberglass for Thermoplastics Reinforcement market with ResearchAI on our online platform, providing deeper, data-backed market analysis.
Ask ResearchAI anything
World's First Innovative Al for Market Research
Conclusion: Harnessing Fiberglass for Future Growth
Fiberglass reinforcement continues to redefine the boundaries of thermoplastic composite performance, offering unmatched combinations of strength, durability, and design freedom. As tariff structures, sustainability mandates, and technological innovations reshape competitive dynamics, the capacity to adapt swiftly and collaboratively will separate market leaders from laggards. By integrating segmentation insights with regional intelligence and strategic partnerships, organizations can unlock new growth vectors while managing risk in an increasingly complex supply environment.
This section provides a structured overview of the report, outlining key chapters and topics covered for easy reference in our Fiberglass for Thermoplastics Reinforcement market comprehensive research report.
- Preface
- Research Methodology
- Executive Summary
- Market Overview
- Market Dynamics
- Market Insights
- Cumulative Impact of United States Tariffs 2025
- Fiberglass for Thermoplastics Reinforcement Market, by Product Type
- Fiberglass for Thermoplastics Reinforcement Market, by Reinforcement Form
- Fiberglass for Thermoplastics Reinforcement Market, by Manufacturing Process
- Fiberglass for Thermoplastics Reinforcement Market, by Fiber Type
- Fiberglass for Thermoplastics Reinforcement Market, by Application
- Fiberglass for Thermoplastics Reinforcement Market, by Thermoplastic Resin Type
- Fiberglass for Thermoplastics Reinforcement Market, by End-User Industry
- Fiberglass for Thermoplastics Reinforcement Market, by Recycling Potential
- Americas Fiberglass for Thermoplastics Reinforcement Market
- Asia-Pacific Fiberglass for Thermoplastics Reinforcement Market
- Europe, Middle East & Africa Fiberglass for Thermoplastics Reinforcement Market
- Competitive Landscape
- ResearchAI
- ResearchStatistics
- ResearchContacts
- ResearchArticles
- Appendix
- List of Figures [Total: 32]
- List of Tables [Total: 1078 ]
Next Steps: Engage Ketan Rohom for In-Depth Analysis
To access comprehensive data, in-depth analysis, and customized strategic guidance on fibreglass reinforcement for thermoplastic applications, contact Ketan Rohom, Associate Director, Sales & Marketing, to purchase the full market research report and elevate your competitive advantage today.
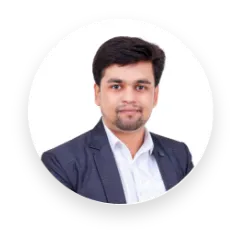
- When do I get the report?
- In what format does this report get delivered to me?
- How long has 360iResearch been around?
- What if I have a question about your reports?
- Can I share this report with my team?
- Can I use your research in my presentation?