Section 1: Introduction to Field Assisted Sintering Technique Systems
Field Assisted Sintering Technique (FAST) systems represent a paradigm shift in advanced materials processing, enabling rapid densification and precision engineering of ceramics, composites, graphite, and metals. As industries strive for higher performance, lightweight construction, and complex geometries, FAST systems have emerged as a critical enabler for innovation across aerospace, automotive, defense, electronics, and medical applications. This executive summary provides a concise yet comprehensive overview of the dynamic forces shaping the FAST landscape, offering strategic insights for decision-makers and engineering leaders.
The introduction outlines the purpose and scope of this report, highlighting how the convergence of novel materials, legislative changes, and supply chain realignments has elevated the strategic importance of FAST. By examining key drivers, technological advances, tariff implications, segmentation, regional dynamics, and competitive positioning, this summary equips industry stakeholders with the knowledge needed to capitalize on emerging opportunities and mitigate potential risks.
Transitioning from traditional sintering techniques to field-assisted approaches, organizations can achieve significant reductions in processing time, energy consumption, and defect rates. This section establishes the context for the subsequent deep dives into transformative trends, regulatory impacts, market segmentation, regional variation, leading players, and actionable recommendations.
Section 2: Transformative Shifts Reshaping FAST Development
Over the past decade, several transformative shifts have redefined how manufacturers approach advanced materials densification. First, the rapid maturation of electric current–assisted sintering has accelerated adoption by reducing cycle times and enhancing microstructural control. Concurrently, the integration of real-time monitoring and closed-loop control has improved reproducibility, enabling consistent part quality even in complex geometries.
Second, the push for sustainable manufacturing has propelled pressure-assisted and microwave sintering into the spotlight. These technologies not only lower carbon footprints through reduced thermal budgets but also facilitate the use of non-oxide ceramics and metal matrix composites that were previously challenging to densify.
Third, materials innovation-including expanded graphite, polymer matrix composites, and advanced alloys-has created new performance benchmarks for thermal, mechanical, and electrical applications. These breakthroughs are driving cross-industry collaboration, as aerospace suppliers partner with electronics manufacturers to leverage FAST for multifunctional components.
Finally, digitalization and Industry 4.0 paradigms have accelerated the integration of FAST into flexible, scalable production lines. By combining cloud-based analytics with machine learning, manufacturers can predict process outcomes, optimize sintering profiles, and achieve higher throughput with lower scrap rates. These shifts collectively underscore the strategic imperative for organizations to invest in FAST capabilities to remain competitive in an era of rapid technological convergence.
Section 3: Cumulative Impact of United States Tariffs 2025
In 2025, the cumulative impact of newly instituted United States tariffs on imported sintering equipment and precursor materials has further complicated supply chain dynamics. Manufacturers relying on overseas components have faced elevated input costs, prompting an accelerated shift toward domestic equipment suppliers and vertically integrated production strategies. These tariffs have also incentivized OEMs to localize component fabrication, reducing exposure to international price fluctuations.
As a result, there has been a notable uptick in collaborative ventures between U.S.-based FAST system producers and end users in aerospace and defense. By shortening lead times and enhancing supply chain transparency, stakeholders have been able to partially offset tariff-driven cost increases. At the same time, some smaller producers have struggled to absorb the higher duties, leading to selective consolidation among equipment manufacturers.
Moreover, the tariffs have spurred investments in alternative sintering materials, particularly metal matrix composites and polymer matrix systems sourced from tariff-exempt regions. This strategic diversification has mitigated risk and supported innovation, but it has also introduced complexity in quality control and process standardization. Consequently, many organizations are prioritizing robust supplier qualification programs and lean inventory strategies to balance cost efficiency with performance reliability.
Section 4: Key Segmentation Insights Across Applications, Materials, Industries, and Technologies
Key segmentation insights reveal nuanced adoption patterns across application, material, end-user industry, and technology dimensions. Based on application, aerospace applications such as heat shields, structural components, and turbine blades are driving demand for FAST systems with high-temperature ceramic and composite capabilities, while automotive manufacturers emphasize cylinder heads, fuel injectors, powertrain components, and turbochargers for efficiency gains. Defense procurement focuses on armored vehicles and weapons components requiring rapid prototyping, whereas electronics makers leverage FAST for chip components, conductive materials, and microelectronics that demand precise grain structures. In medical sectors, dental implants, orthopedic implants, and surgical tools benefit from the technique’s ability to produce biocompatible ceramics and metal alloys.
From a material perspective, non-oxide and oxide ceramics lead the ceramics segment, whereas metal matrix and polymer matrix composites underpin composite applications. Expanded and mesophase graphite serve thermal management needs, and the metals spectrum encompasses high-performance alloys, ferrous metals for structural strength, and non-ferrous metals such as titanium and aluminum for weight-sensitive parts.
End-user industries exhibit distinct drivers: construction stakeholders seek infrastructure-grade components, energy enterprises in nuclear, oil & gas, and renewable energy prioritize corrosion resistance and thermal stability, consumer goods and industrial machinery manufacturers demand scalable production, and automotive producers focus on cutting-edge manufacturing integration.
Technologically, electric current–assisted sintering-including field-activated and spark plasma variants-dominates early-stage adoption, while microwave sintering at high or low frequencies offers rapid heating profiles. Pressure-assisted methods, utilizing hot isostatic pressure or uniaxial pressure, provide unparalleled density control for critical components. Together, these segmentation insights paint a comprehensive picture of where and how FAST systems are being deployed across diverse markets.
This comprehensive research report categorizes the Field Assisted Sintering Technique System market into clearly defined segments, providing a detailed analysis of emerging trends and precise revenue forecasts to support strategic decision-making.
- Application
- Material
- End-User Industry
- Technology
Section 5: Key Regional Insights Driving FAST Adoption
Regional dynamics play a crucial role in determining strategic priorities and investment flows. In the Americas, a robust aerospace and defense ecosystem drives demand for FAST systems that can handle high-performance alloys and ceramics, supported by government incentives for onshore manufacturing and defense procurement. Meanwhile, automotive OEMs in North America are rapidly integrating FAST into powertrain and emissions control component production to meet stringent regulatory standards.
Across Europe, the Middle East & Africa, strong academic–industry partnerships fuel research into non-oxide ceramics and metal matrix composites, particularly for renewable energy and high-speed rail applications. Collaborative initiatives within the European Union have accelerated standardization efforts, enabling cross-border deployment of advanced sintering systems.
In the Asia-Pacific region, a broad manufacturing base spans consumer electronics, energy infrastructure, and medical device production. High-frequency microwave sintering and cost-effective pressure-assisted methods have gained traction in emerging markets, where capacity expansion and digitalization are top priorities. Government-led innovation programs in Japan and South Korea further reinforce the region’s leadership in field-activated sintering technologies.
This comprehensive research report examines key regions that drive the evolution of the Field Assisted Sintering Technique System market, offering deep insights into regional trends, growth factors, and industry developments that are influencing market performance.
- Americas
- Asia-Pacific
- Europe, Middle East & Africa
Section 6: Key Companies Shaping the FAST Ecosystem
The competitive landscape is defined by a blend of specialized equipment manufacturers and diversified industrial players. ARES Advanced Equipment Systems has distinguished itself with customizable electric current–assisted furnaces, while Carbolite Gero Limited excels in modular microwave sintering platforms. Centorr Vacuum Industries, Inc. and CM Furnaces, Inc. offer versatile hot isostatic pressing solutions, and CH Instruments, Inc. has introduced innovative pulsed DC sintering modules.
Dr. Fritsch Sondermaschinen GmbH and FCT Systeme GmbH provide turnkey FAST lines with integrated process monitoring, whereas Höganäs AB and IDONIAL Technology Group leverage their metallurgical expertise to deliver application-specific sintering protocols. Keppeler Teknologi AS and Kurimoto Ltd. focus on high-pressure sintering for critical aerospace components, and Linn High Therm GmbH and Materials Research Furnaces, LLC are recognized for scalable research-to-production systems.
MTI Corporation and Nabertherm GmbH serve specialized niches in graphite and ceramic sintering, respectively, while Sinter Land Inc. and Sintex a/s have carved out market share in electric current–assisted solutions. Sumitomo Coal Mining Co., Ltd. and Thermal Technology LLC round out the competitive field with a mix of established industrial heritage and emerging technology offerings. Together, these companies shape the innovation trajectory and set performance benchmarks for the FAST ecosystem.
This comprehensive research report delivers an in-depth overview of the principal market players in the Field Assisted Sintering Technique System market, evaluating their market share, strategic initiatives, and competitive positioning to illuminate the factors shaping the competitive landscape.
- ARES Advanced Equipment Systems
- Carbolite Gero Limited
- Centorr Vacuum Industries, Inc.
- CH Instruments, Inc.
- CM Furnaces, Inc.
- Dr. Fritsch Sondermaschinen GmbH
- FCT Systeme GmbH
- Höganäs AB
- IDONIAL Technology Group
- Keppeler Teknologi AS
- Kurimoto Ltd.
- Linn High Therm GmbH
- Materials Research Furnaces, LLC
- MTI Corporation
- Nabertherm GmbH
- Sinter Land Inc.
- Sintex a/s
- Sumitomo Coal Mining Co., Ltd.
- Thermal Technology LLC
Section 7: Actionable Recommendations for Industry Leaders
To capitalize on the evolving FAST landscape, industry leaders should pursue a multi-faceted strategy. First, investments in modular, scalable equipment platforms will enable rapid response to shifting application requirements, whether in aerospace heat shields or medical implants. Second, forging strategic alliances with material suppliers and in-house research centers can accelerate the qualification of advanced ceramics, composites, and alloys, ensuring swift commercialization of next-generation components.
Third, organizations must optimize supply chain resilience by diversifying sourcing of critical consumables and leveraging tariff-exempt regions for alternative materials. Implementing lean inventory management paired with predictive analytics will reduce exposure to cost volatility while maintaining production agility.
Fourth, adopting digital twins and cloud-based process controls will facilitate real-time monitoring, predictive maintenance, and continuous process improvement. By integrating machine learning algorithms, manufacturers can refine sintering profiles to achieve consistent microstructures and mechanical properties at scale.
Finally, upskilling the workforce through targeted training programs in FAST techniques, process simulation, and quality assurance will ensure that teams can fully exploit the technology’s potential. Cross-functional knowledge-sharing initiatives between engineering, operations, and quality departments will further strengthen organizational capabilities.
Explore AI-driven insights for the Field Assisted Sintering Technique System market with ResearchAI on our online platform, providing deeper, data-backed market analysis.
Ask ResearchAI anything
World's First Innovative Al for Market Research
Section 8: Conclusion on Strategic Implications and Future Outlook
The field assisted sintering landscape is characterized by rapid technological evolution, shifting regulatory frameworks, and dynamic competitive forces. By understanding transformative shifts in sintering methodologies, assessing the effects of tariff policies, and leveraging segmentation and regional insights, organizations can position themselves at the forefront of advanced materials innovation.
Collaboration among equipment suppliers, material producers, and end users will be critical to overcoming technical challenges and accelerating time to market. As FAST systems become increasingly integrated into production lines, digitalization and data-driven process control will differentiate market leaders from followers.
Ultimately, success in the FAST arena will hinge on the ability to align technological investments with strategic objectives-whether that means enhancing component performance, reducing production costs, or meeting sustainability goals. This executive summary provides the framework to inform those decisions, equipping stakeholders with an authoritative perspective on the drivers, opportunities, and best practices that will define the future of advanced sintering processes.
This section provides a structured overview of the report, outlining key chapters and topics covered for easy reference in our Field Assisted Sintering Technique System market comprehensive research report.
- Preface
- Research Methodology
- Executive Summary
- Market Overview
- Market Dynamics
- Market Insights
- Cumulative Impact of United States Tariffs 2025
- Field Assisted Sintering Technique System Market, by Application
- Field Assisted Sintering Technique System Market, by Material
- Field Assisted Sintering Technique System Market, by End-User Industry
- Field Assisted Sintering Technique System Market, by Technology
- Americas Field Assisted Sintering Technique System Market
- Asia-Pacific Field Assisted Sintering Technique System Market
- Europe, Middle East & Africa Field Assisted Sintering Technique System Market
- Competitive Landscape
- ResearchAI
- ResearchStatistics
- ResearchContacts
- ResearchArticles
- Appendix
- List of Figures [Total: 24]
- List of Tables [Total: 904 ]
Section 9: Call-To-Action: Secure the Comprehensive FAST Market Research Report
To explore the full depth of analysis, detailed segmentation data, and proprietary insights, reach out to Ketan Rohom, Associate Director of Sales & Marketing, to secure your copy of the comprehensive FAST market research report. Prime your organization for success by gaining immediate access to the strategic intelligence needed to make informed decisions in this rapidly evolving field.
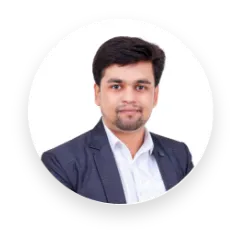
- When do I get the report?
- In what format does this report get delivered to me?
- How long has 360iResearch been around?
- What if I have a question about your reports?
- Can I share this report with my team?
- Can I use your research in my presentation?