Introduction to the Monoblock Machine Market Landscape
The filling and capping monoblock machine market lies at the heart of modern packaging operations, driven by the need for efficiency, precision, and flexibility. As product lifecycles shorten and consumer expectations heighten, manufacturers demand equipment that can seamlessly integrate multiple operations into a single footprint. Monoblock machines, which combine filling, capping, and sometimes additional processes such as sterilization or labeling, represent the apex of this evolution, streamlining production lines and reducing downtime.
In this executive summary, we explore the forces reshaping this landscape-from technological breakthroughs and shifting trade policies to granular insights into how industry players segment their offerings. By synthesizing the latest industry developments without resorting to raw forecasts or numerical estimates, this overview equips decision-makers with the context they need to navigate a dynamic environment and seize emerging opportunities.
Transformative Shifts Shaping Packaging Automation
The packaging industry overhauled conventional workflows by embracing smart automation, collaborative robotics, and data-driven controls. Fully automated monoblock systems now incorporate advanced sensors and machine-learning algorithms, enabling real-time adjustments to fill levels and torque settings. At the same time, modular designs have allowed manufacturers to retrofit legacy lines with sensor-driven capping heads and robotic loading arms.
Connectivity has emerged as a cornerstone: machines equipped with IoT gateways transmit performance metrics to centralized dashboards, facilitating predictive maintenance and minimizing unplanned stops. Sustainability concerns have also spurred product innovation, driving the adoption of low-waste processing technologies and energy-efficient drives.
Moreover, human-machine interfaces have evolved beyond simple touchscreens. Intuitive graphical controls and augmented reality support tools help operators perform changeovers faster and troubleshoot more effectively. Collectively, these transformative shifts are redefining what monoblock machines can deliver: not just throughput gains, but a holistic upgrade in line agility and operational intelligence.
Cumulative Impact of United States Tariffs in 2025
Trade tensions and the subsequent tariff adjustments in 2025 have imposed a notable burden on equipment sourcing and component procurement. Inbound duties on key subassemblies-including servo motors, precision sensors, and specialty stainless-steel fittings-have elevated landed costs for both full-sized monoblock machines and retrofit modules.
Domestic assemblers have partially offset these impacts by forging strategic alliances with local component suppliers and by repurposing existing assembly lines to reduce reliance on imports. Meanwhile, certain service providers have introduced ‘tariff mitigation’ programs, structuring equipment as service contracts to sidestep capital expenditure duties.
Although no specific forecasts are presented here, the aggregate effect has been to accelerate the shift toward regional manufacturing hubs. By favoring supply chains within the United States and neighboring markets, original equipment manufacturers have sought to insulate themselves from further trade fluctuations. As a result, buyer negotiations now routinely factor in duty-planning strategies alongside traditional considerations such as cycle speed and OEE (Overall Equipment Effectiveness).
Key Segmentation Insights Across Multiple Dimensions
The monoblock machine market can be deconstructed across multiple dimensions to reveal where innovation and investment are most concentrated. In terms of production mechanisms, solutions extend from fully automatic systems featuring robotic integration and sensor-driven controls, down to manual, lever-operated units and semi-automatic models that pair electric-assisted actuation with pneumatic-assisted modules.
When examining packaging materials, manufacturers accommodate glass containers spanning borosilicate and soda lime compositions, metal containers crafted from aluminum and tin plate, as well as plastic containers molded from high-density polyethylene and poly-ethylene terephthalate. Industry applications further refine this picture: specialized monoblocks address the precise fill tolerances demanded by injectable formulations, oral liquids, and topical drugs in the pharmaceutical sector, while separate configurations manage haircare and skincare products, or handle bottled water, carbonated drinks, dairy products and juices with tailored hygiene protocols.
Operational capacity is another key axis, distinguishing large-scale continuous plants from mid-sized batch operations and small-scale artisanal lines. Design complexity ranges from standard fixed-cam designs to advanced control architectures driven by programmable logic, and further to smart integration platforms leveraging artificial intelligence and IoT connectivity. Process efficiency metrics break down by high-speed operation, low-waste processing and precision filling standards, while automation levels traverse fully automated cells with robotic assistance and sensor-driven orchestration, as well as systems under manual control or semi-automated frameworks. Material choices-from composite and high-grade plastics to stainless steel-underscore durability and contamination control, and cap and closure modules cover crown caps, flip tops with child-resistant or tamper-evident features, and classic screw caps.
This comprehensive research report categorizes the Filling & Capping Monoblock Machine market into clearly defined segments, providing a detailed analysis of emerging trends and precise revenue forecasts to support strategic decision-making.
- Production Mechanism
- Packaging Material
- Industry Application
- Operational Capacity
- Design Complexity
- Process Efficiency
- Automation Level
- System Material
- Cap And Closure Type
Key Regional Insights Driving Deployment Trends
Regional dynamics have become increasingly pivotal in both sourcing and sales strategies. In the Americas, strong demand for beverage and pharmaceutical packaging has driven continuous line expansions in the United States and Brazil, with a particular focus on local manufacturing to reduce exposure to import duties. In Europe, Middle East & Africa, regulatory harmonization and sustainability targets have prompted manufacturers to adopt low-waste fill systems and energy-recovery drives, with the European Union emerging as a trailblazer in chemical-resistant machine enclosures.
The Asia-Pacific region continues to exhibit robust growth fueled by fast-moving consumer goods, with India and Southeast Asia investing heavily in semi-automatic lines to meet growing domestic demand. Collaborative agreements between major OEMs and regional integrators have lowered barriers to entry, accelerating technology transfer and supporting localized service networks. Across all regions, after-sales support and spare-parts availability remain critical differentiators, influencing procurement decisions more heavily than ever.
This comprehensive research report examines key regions that drive the evolution of the Filling & Capping Monoblock Machine market, offering deep insights into regional trends, growth factors, and industry developments that are influencing market performance.
- Americas
- Asia-Pacific
- Europe, Middle East & Africa
Key Company Insights and Competitive Positioning
A diverse landscape of original equipment manufacturers competes on both innovation and service excellence. Alpha Packaging Solutions and Apex Packaging are often cited for their end-to-end turnkey offerings, while Beta Industrial Machines and Chi Packaging Engineering excel in customized monoblocks tailored for niche pharmaceutical lines. Delta Machinery Inc. alongside Epsilon Packaging Technologies have gained traction with modular platforms that simplify capacity scaling, and Eta Robotics and Frontier Automation lead in robotics integration.
Gamma Manufacturing and Iota Industrial stand out for precision filling expertise, just as Kappa Automation and Lambda Equipment Ltd. deliver robust semi-automatic cells. Mu Packaging Technologies and Nu Industrial Solutions focus on sustainability upgrades, whereas Omega Packaging Enterprises, Omicron Packaging Corp., and Phi Manufacturing Solutions emphasize comprehensive after-sales support. Pi Machinery and Pioneer Pack Solutions have built reputations for hygienic design in beverage applications, and Psi Machinery Corp. together with Rho Solutions Inc. deliver specialized clean-in-place assemblies. Sigma Package Systems, Summit Machine Works, Tau Automation, Theta Packaging Group, Upsilon Engineering, Vertex Industrial, Xi Process Engineering, Zenith Packaging Tech, and Zeta Systems Engineering collectively cover segments ranging from advanced sensor platforms to low-cost manual units, ensuring that buyers can access a precise fit for their operational needs.
This comprehensive research report delivers an in-depth overview of the principal market players in the Filling & Capping Monoblock Machine market, evaluating their market share, strategic initiatives, and competitive positioning to illuminate the factors shaping the competitive landscape.
- Alpha Packaging Solutions
- Apex Packaging
- Beta Industrial Machines
- Chi Packaging Engineering
- Delta Machinery Inc.
- Epsilon Packaging Technologies
- Eta Robotics
- Frontier Automation
- Gamma Manufacturing
- Iota Industrial
- Kappa Automation
- Lambda Equipment Ltd.
- Mu Packaging Technologies
- Nu Industrial Solutions
- Omega Packaging Enterprises
- Omicron Packaging Corp.
- Phi Manufacturing Solutions
- Pi Machinery
- Pioneer Pack Solutions
- Psi Machinery Corp.
- Rho Solutions Inc.
- Sigma Package Systems
- Summit Machine Works
- Tau Automation
- Theta Packaging Group
- Upsilon Engineering
- Vertex Industrial
- Xi Process Engineering
- Zenith Packaging Tech
- Zeta Systems Engineering
Actionable Recommendations for Industry Leaders
Industry leaders should prioritize modularity and digital integration as cornerstones of their monoblock strategies. Retrofitting legacy lines with sensor-driven monitoring towers can deliver immediate OEE improvements without requiring full equipment replacement. Investing in augmented-reality-enabled maintenance platforms can also reduce mean time to repair and bolster uptime metrics, positioning service offerings as value accelerators rather than cost centers.
Strategic partnerships with regional component suppliers can mitigate tariff risk while shortening lead times and inventory buffers. Collaborative R&D efforts, particularly around AI-driven fill algorithms and low-waste nozzle designs, offer competitive differentiation and can be codified through co-branding or joint-IP agreements. Meanwhile, establishing flexible financing models-such as equipment-as-a-service contracts-allows customers to align capital outlays with production volumes, smoothing procurement cycles.
Finally, embedding sustainability at both product design and operational levels is no longer optional. Adoption of low-energy drives, solvent-free cleaning cycles, and recyclable material constructions can secure preferential treatment under evolving environmental regulations, and also resonate strongly with end-users who increasingly demand green credentials from their suppliers.
Explore AI-driven insights for the Filling & Capping Monoblock Machine market with ResearchAI on our online platform, providing deeper, data-backed market analysis.
Ask ResearchAI anything
World's First Innovative Al for Market Research
Conclusion: Positioning for Sustainable Competitive Advantage
The evolution of filling and capping monoblock machines underscores a broader shift toward integrated, intelligent manufacturing. As traceability, speed, and sustainability become business imperatives, organizations that embrace modular architectures, data-driven controls, and collaborative service models will capture the most value. The current landscape demands a balance: leverage rapid digital upgrades to elevate existing assets while pacing new capital investments to regional market realities.
In this context, success hinges on orchestrating partnerships-whether in sourcing, R&D, or service delivery-that extend an OEM’s capabilities without diluting focus. By aligning strategic initiatives with customer priorities, and by transparently quantifying performance gains, packaging equipment providers can solidify long-term relationships and secure recurring revenue streams due to service contracts and consumable sales.
This section provides a structured overview of the report, outlining key chapters and topics covered for easy reference in our Filling & Capping Monoblock Machine market comprehensive research report.
- Preface
- Research Methodology
- Executive Summary
- Market Overview
- Market Dynamics
- Market Insights
- Cumulative Impact of United States Tariffs 2025
- Filling & Capping Monoblock Machine Market, by Production Mechanism
- Filling & Capping Monoblock Machine Market, by Packaging Material
- Filling & Capping Monoblock Machine Market, by Industry Application
- Filling & Capping Monoblock Machine Market, by Operational Capacity
- Filling & Capping Monoblock Machine Market, by Design Complexity
- Filling & Capping Monoblock Machine Market, by Process Efficiency
- Filling & Capping Monoblock Machine Market, by Automation Level
- Filling & Capping Monoblock Machine Market, by System Material
- Filling & Capping Monoblock Machine Market, by Cap And Closure Type
- Americas Filling & Capping Monoblock Machine Market
- Asia-Pacific Filling & Capping Monoblock Machine Market
- Europe, Middle East & Africa Filling & Capping Monoblock Machine Market
- Competitive Landscape
- ResearchAI
- ResearchStatistics
- ResearchContacts
- ResearchArticles
- Appendix
- List of Figures [Total: 34]
- List of Tables [Total: 989 ]
Contact Ketan Rohom for the Full Market Research Report
To delve deeper into this comprehensive market research and unlock tailored strategies for your organization, reach out to Ketan Rohom, Associate Director of Sales & Marketing. He can provide detailed insights and guide you through the options available to align your packaging operations with the latest industry innovations. Contact Ketan today to ensure you stay ahead of the competition and maximize your equipment investments.
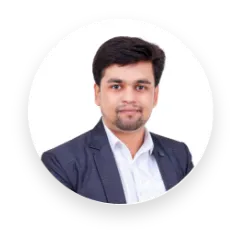
- When do I get the report?
- In what format does this report get delivered to me?
- How long has 360iResearch been around?
- What if I have a question about your reports?
- Can I share this report with my team?
- Can I use your research in my presentation?