Introduction to the Dynamic Foam Cutting Machine Landscape
The foam cutting machine market has evolved into a cornerstone of modern manufacturing, powering applications across automotive seating, construction insulation, furniture cushioning, and sophisticated packaging solutions. As industries demand ever-greater precision, customization, and throughput, manufacturers are compelled to adopt technologies that deliver repeatable accuracy, reduced material waste, and rapid changeovers. This report delves into the dynamic environment shaping foam cutting equipment, tracing the drivers behind innovation, the influence of global trade policies, and the nuanced ways in which customer requirements are steering product development. By examining technological breakthroughs, tariff impacts, and strategic segment analysis, readers will gain a holistic understanding of current market forces. In the following sections, we explore transformative shifts, quantify the ripple effects of 2025 U.S. tariffs, dissect core market segments, and highlight regional and competitive landscapes. Finally, we present actionable strategies to guide industry leaders in capitalizing on emerging opportunities and navigating potential pitfalls.
Key Technological and Market Shifts Redefining Foam Cutting
Rapid advancements in digital control and growing emphasis on Industry 4.0 integration have rewritten the rules for foam cutting. Computer Numerical Control (CNC) platforms are no longer confined to high-end aerospace or automotive boutiques; they’re increasingly applied to midsize furniture manufacturers seeking consistent cushion and mattress profiles. Simultaneously, laser technology has transitioned from a niche high-precision tool into a versatile asset for intricate packaging designs.
Automation has emerged as a key differentiator. Fully automated systems that link Programmable Logic Controllers with real-time analytics reduce downtime and energy consumption, while hybrid semi-automatic machines strike a balance between human oversight and machine-led accuracy. Ultrasonic cutters and water jet setups are gaining traction in markets where tool wear and material stress must be minimized, such as medical device foams and sensitive insulation products.
Beyond equipment, a shift toward on-demand manufacturing and mass customization is reshaping supply chains. Companies are investing in modular platforms that can swiftly pivot between cutting capacity tiers-lightweight for prototyping or heavyweight for bulk output-without sacrificing throughput. Environmental considerations also drive innovation: biodegradable polymer foams and closed-loop waste recovery influence both material selection and cutter design. As these technological and market shifts converge, the foam cutting landscape is more competitive and opportunity-rich than ever.
Assessing the 2025 U.S. Tariffs’ Effects on Foam Cutting Equipment
The introduction of new U.S. tariffs in 2025 marks a pivotal moment for foam cutting machine suppliers and end users. With higher duties imposed on imported equipment and replacement parts, original equipment manufacturers face increased cost pressure, prompting many to reevaluate their sourcing strategies. Domestic production lines are expanding as companies seek tariff relief, yet capacity constraints and lead-time challenges persist.
End users, from automotive seat fabricators to packaging houses, are absorbing incremental price increases, which in turn impacts capital expenditure cycles. Some buyers are delaying upgrades or shifting toward semi-automatic solutions that carry lower duty liabilities. Others are recalibrating maintenance schedules to extend the service life of existing CNC, hot wire, and laser cutters.
On a strategic level, this tariff environment accelerates regionalization of supply chains. North American component suppliers are forging partnerships with domestic machine builders to localize critical subsystems, while overseas manufacturers explore assembly hubs in Mexico or Canada to maintain access to U.S. markets. Anticipating potential retaliatory measures, global players are hedging by diversifying footprints across multiple free trade zones.
Ultimately, these tariffs underscore the importance of supply chain resilience. Companies that proactively restructure sourcing, optimize inventory buffers, and leverage automation to offset cost increases will be best positioned to maintain margins and meet evolving customer demands.
Core Segment Analysis Driving Foam Cutting Machine Adoption
A comprehensive segmentation of the foam cutting machine market reveals distinct growth vectors and technology preferences. Based on Technology Type, demand for CNC Technology is surging in applications requiring micron-level tolerances, while Hot Wire Technology retains its stronghold in insulation and construction markets due to its cost efficiency. Laser Technology is carving out specialized niches in high-end packaging, and Ultrasonic Technology achieves consistent, burr-free edges ideal for medical foams. Water Jet Technology continues to appeal to manufacturers handling composite materials or those prioritizing minimal thermal impact.
When considering Machine Type, Automatic Machines-comprising both Fully Automated Systems and those driven by Programmable Logic Controllers-capture attention for large-scale operations seeking minimal human intervention and maximum throughput. Manual Machines remain relevant for low-volume runs or prototype work, whereas Semi-Automatic Machines, whether Hybrid Systems blending manual setup with automated cutting or Push Button Controls offering user-friendly operation, serve mid-tier facilities balancing flexibility and cost.
Analyzing Application end points, the Automotive sector’s appetite for Seating Foams and Soundproofing Foams drives high-precision cutter investments, whereas Construction applications focus on Concrete Fillers and Insulation Materials, prioritizing speed and low material waste. The Furniture segment emphasizes Cushion Foam and Mattresses, favoring machines that handle variable foam densities, while Packaging requirements-spanning Consumer Goods, Food, and Industrial Packaging-demand machines capable of complex die-less cuts and agile changeovers.
From an End-User Industry perspective, Aerospace Industry adopters mandate the strictest tolerances and traceability, Automotive Industry leaders require scalable solutions, the Construction Industry prioritizes rugged reliability, Furniture Manufacturing favors quick changeovers, and the Packaging Industry seeks high-mix, low-downtime capabilities. Material Type segmentation shows Polyurethane Foams leading overall consumption, with Polyethylene and Polypropylene Foams significant in packaging, and Polystyrene Foams preferred where rigidity and thermal insulation are key.
Cutting Capacity tiers reveal Lightweight Capacity machines dominating prototyping and small-batch production, Mid-Weight Capacity solutions serving general manufacturing, and Heavyweight Capacity systems tailored to continuous high-volume operations. Finally, Sales Channel analysis indicates strong direct sales relationships in enterprise accounts, while Distributors, Online Platforms, and Retail Outlets facilitate broader access for small- and medium-sized businesses.
This comprehensive research report categorizes the Foam Cutting Machine market into clearly defined segments, providing a detailed analysis of emerging trends and precise revenue forecasts to support strategic decision-making.
- Technology Type
- Machine Type
- Application
- End-User Industry
- Material Type
- Cutting Capacity
- Sales Channel
Regional Dynamics Shaping the Global Foam Cutting Market
Regional dynamics exert significant influence on technology adoption, regulatory compliance, and competitive positioning. In the Americas, established automotive clusters and robust packaging sectors stimulate continuous demand for both high-precision CNC units and cost-effective hot wire systems. Manufacturers here often emphasize after-sales service, retrofit options, and leasing models to optimize capital utilization.
Across Europe, the Middle East & Africa, stringent environmental regulations and energy efficiency standards are steering investment toward laser and ultrasonic cutters that reduce material waste and power consumption. The region’s strong aerospace and construction industries also drive demand for heavy-duty systems capable of handling advanced insulation materials and high-grade composites.
In the Asia-Pacific, rapid urbanization and expanding furniture manufacturing hubs are fueling growth in semi-automatic and fully automated machines designed for flexibility and speed. Cost-sensitive markets in China, India, and Southeast Asia increasingly adopt water jet and hybrid systems to balance precision with lower upfront investment. Government initiatives aimed at modernizing manufacturing infrastructure further support accelerated technology uptake.
This comprehensive research report examines key regions that drive the evolution of the Foam Cutting Machine market, offering deep insights into regional trends, growth factors, and industry developments that are influencing market performance.
- Americas
- Asia-Pacific
- Europe, Middle East & Africa
Competitive Landscape: Leading Foam Cutting Equipment Suppliers
The competitive landscape for foam cutting equipment features a blend of legacy OEMs and agile innovators. Albrecht Bäumer GmbH & Co. KG distinguishes itself with integrated CNC and hot wire platforms engineered for automotive and technical foam applications, while Croma Foamcutting Technology advances laser and ultrasonic solutions tailored to packaging and medical sectors. Eastman Machine Company leverages decades of experience to supply high-throughput automatic and semi-automatic machines, and Fecken-Kirfel GmbH & Co. KG is renowned for heavy-duty systems designed for continuous industrial operations.
Foamlinx LLC focuses on lightweight capacity machines optimized for prototyping and small-batch production, whereas Graphic Systems Services, Inc. offers customized maintenance and retrofit services that extend the lifespan of existing cutter fleets. Horia Corporation’s water jet and hybrid cutting systems attract customers requiring minimal thermal impact and complex geometries, and Magma Technologies Pvt. Ltd. excels in PLC-driven automation for mid-tier manufacturers.
OMAX Corporation leads the water jet segment with unparalleled precision, while Sunkist Chemical Machinery Ltd. continues to innovate in hot wire technology for insulation markets. Thermwood Corporation integrates CAD/CAM and robotic automation into large-format CNC routers, and Wintech Engineering supplies versatile push button control units favored by small-scale furniture makers. Together, these companies shape the market through differentiated technology portfolios, global service networks, and ongoing R&D investments.
This comprehensive research report delivers an in-depth overview of the principal market players in the Foam Cutting Machine market, evaluating their market share, strategic initiatives, and competitive positioning to illuminate the factors shaping the competitive landscape.
- Albrecht Bäumer GmbH & Co. KG
- Croma Foamcutting Technology
- Eastman Machine Company
- Fecken-Kirfel GmbH & Co. KG
- Foamlinx LLC
- Graphic Systems Services, Inc.
- Horia Corporation
- Magma Technologies Pvt. Ltd.
- OMAX Corporation
- Sunkist Chemical Machinery Ltd.
- Thermwood Corporation
- Wintech Engineering
Strategic Recommendations for Industry Leadership and Growth
First, industry leaders should invest in advanced digital control and IoT-enabled monitoring to optimize machine uptime and enable predictive maintenance, reducing unplanned downtime and operational costs. Next, diversifying the supplier base and exploring nearshore manufacturing hubs can mitigate exposure to tariff fluctuations and shipping delays while enhancing supply chain resilience. Moreover, allocating R&D resources to laser and water jet technologies will position companies to address high-precision market segments and environmental regulations. Additionally, developing comprehensive retrofit and upgrade programs can capture revenue from installed bases seeking to extend equipment lifecycles. Finally, leveraging data analytics to understand customer usage patterns and integrate feedback loops into product development will drive continuous innovation and deepen client relationships.
Explore AI-driven insights for the Foam Cutting Machine market with ResearchAI on our online platform, providing deeper, data-backed market analysis.
Ask ResearchAI anything
World's First Innovative Al for Market Research
Conclusion: Navigating the Future of Foam Cutting Technology
As technology innovations, tariff considerations, and evolving customer requirements converge, foam cutting machine providers must adopt a multifaceted strategy that balances efficiency with agility. By aligning product portfolios with core segments, tailoring solutions to regional dynamics, and leveraging data-driven insights, companies can navigate market complexities and capture emerging growth opportunities. The ability to adapt-through automation, supply chain flexibility, and targeted R&D-will define the next wave of competitive advantage in this rapidly changing industry.
This section provides a structured overview of the report, outlining key chapters and topics covered for easy reference in our Foam Cutting Machine market comprehensive research report.
- Preface
- Research Methodology
- Executive Summary
- Market Overview
- Market Dynamics
- Market Insights
- Cumulative Impact of United States Tariffs 2025
- Foam Cutting Machine Market, by Technology Type
- Foam Cutting Machine Market, by Machine Type
- Foam Cutting Machine Market, by Application
- Foam Cutting Machine Market, by End-User Industry
- Foam Cutting Machine Market, by Material Type
- Foam Cutting Machine Market, by Cutting Capacity
- Foam Cutting Machine Market, by Sales Channel
- Americas Foam Cutting Machine Market
- Asia-Pacific Foam Cutting Machine Market
- Europe, Middle East & Africa Foam Cutting Machine Market
- Competitive Landscape
- ResearchAI
- ResearchStatistics
- ResearchContacts
- ResearchArticles
- Appendix
- List of Figures [Total: 30]
- List of Tables [Total: 598 ]
Reach Out to Ketan Rohom for the Full Foam Cutting Market Report
To access a detailed marketplace analysis, proprietary insights across segments and regions, and a comprehensive competitive matrix, contact Ketan Rohom, Associate Director, Sales & Marketing. Engage with him to secure the full foam cutting machine market research report and equip your organization with the strategic intelligence needed to make informed investment and operational decisions.
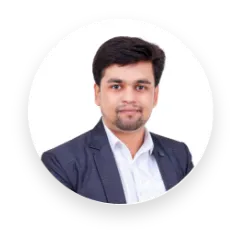
- When do I get the report?
- In what format does this report get delivered to me?
- How long has 360iResearch been around?
- What if I have a question about your reports?
- Can I share this report with my team?
- Can I use your research in my presentation?