Introduction to Forging Technology Simulation Software Market Dynamics
The forging industry stands at the cusp of a digital revolution driven by advanced simulation software that replicates complex metal forming processes with unprecedented fidelity. As manufacturers pursue greater efficiency, quality, and sustainability, simulation platforms have emerged as indispensable tools for predicting material behavior, optimizing die designs, and reducing costly trial-and-error. Recent innovations in computational power, algorithmic accuracy, and integration with artificial intelligence have accelerated adoption across aerospace structures, automotive powertrains, and beyond. Leading engineers now simulate thermo-mechanical interactions, strain distribution, and tool wear in virtual environments, enabling data-driven decisions that minimize scrap rates and energy consumption.
In this introduction, we explore the pivotal role of forging technology simulation software in shaping future operations. We examine how simulation-driven workflows streamline collaboration among design, production, and quality assurance teams, fostering shorter development cycles and heightened responsiveness to shifting specifications. With Industry 4.0 principles as a guiding framework, this section underscores why forging simulation is not just an enhancement but a strategic imperative for organizations seeking to remain competitive amid rising material costs and stringent regulatory requirements.
Emerging Paradigms Transforming Forging Simulation Workflows
The landscape of forging technology simulation is undergoing transformative shifts characterized by heightened user expectations and technological breakthroughs. Cloud-based deployment models have expanded access to high-performance computing resources, allowing small and medium enterprises to leverage the same simulation capabilities once reserved for large corporations. At the same time, machine learning algorithms are being embedded within finite element analysis modules, automatically calibrating material models and predicting defects with growing precision.
Moreover, user interface and experience enhancements have reduced the learning curve, enabling engineers in consumer goods, electronics, and oil and gas sectors to adopt simulation tools swiftly. Collaboration features now support real-time design reviews, fostering cross-functional synergy between R&D and production teams. Concurrently, integration with product lifecycle management systems ensures that simulation results feed seamlessly into downstream quality checks and supply chain planning. These converging innovations are reshaping forging workflows, delivering faster time-to-market and driving continuous process improvements.
Assessing the 2025 US Tariff Effects on Simulation Adoption
The cumulative impact of United States tariffs in 2025 has reshaped cost structures and procurement strategies in forging simulation software. Elevated levies on imported steel and aluminum spurred manufacturers to intensify virtual testing to mitigate material waste and control expenses. As tariffs propelled raw material prices upward, simulation solutions became vital for modeling alternative alloys and process parameters before committing to physical trials.
Additionally, retaliatory tariffs imposed by key trading partners disrupted the global supply of tooling components, prompting forging shops to simulate alternative die materials and lubrication regimes. This increased reliance on simulation drove a surge in demand for data management modules, as engineers sought to track variant performance across different trade zones. Consequently, vendors invested heavily in enhancing retrieval systems and storage solutions to support expansive material libraries and cross-border collaboration. These dynamics underscore how geopolitical measures in 2025 have elevated simulation software from a cost-saving accessory to a core risk-management instrument.
Key Segmentation Insights Across Applications, Solutions, and Users
A nuanced segmentation analysis reveals that forging simulation software must cater to a broad spectrum of industry needs and technological preferences. When examined by application, sectors range from Aerospace and Defense-where virtual trials of aircraft frame assembly, defense equipment components, landing gear, and propulsion systems demand ultra-precise modeling-to Automotive and Transportation, which covers chassis manufacturing, engine components, and suspension systems. Consumer Goods manufacturers deploy simulation to refine household equipment, personal care appliances, and sports equipment, while Electronics producers rely on virtual testing of circuitry cases, connectors, and equipment housings. Industrial Machinery applications extend to agricultural machinery, construction machinery parts, and mining equipment, just as the Oil and Gas segment emphasizes drill bits, pipelines, and valves and fittings.
Turning to software type, platforms are divided into data management, drafting and design, simulation and analysis, and user interface and experience categories. Data management systems incorporate retrieval capabilities, security features, and storage solutions. Drafting and design modules support both 2D and 3D modeling workflows. Simulation and analysis suites offer finite element analysis and thermal analysis tools, whereas user interface enhancements focus on customization options and usability testing protocols.
End users span educational institutions-where research universities and technical colleges integrate simulation into curricula-to large enterprises such as conglomerates and multinational corporations that deploy comprehensive enterprise licenses. Small and medium enterprises, including independent manufacturers and startups, leverage modular or cloud-based offerings to scale computational resources on demand.
Integration technology preferences further delineate the market between artificial intelligence–driven automated processes and machine learning enhancements, cloud-based systems spanning hybrid, private, and public clouds, and on-premise solutions hosted on dedicated infrastructure or local servers. Finally, industry vertical applications concentrate on automobile manufacturing at both OEM and parts supplier levels, electronics and semiconductors encompassing integrated device manufacturers and foundries, and utilities and energy segments from conventional to renewable sources. These intersecting segmentation dimensions define a market in which tailored solution bundles and modular architectures deliver optimal return on investment.
This comprehensive research report categorizes the Forging Technology Simulation Software market into clearly defined segments, providing a detailed analysis of emerging trends and precise revenue forecasts to support strategic decision-making.
- Application
- Software Type
- End User
- Technology Integration
- Industry Vertical
Regional Trends Shaping Simulation Software Growth Trajectories
Regional dynamics significantly influence the adoption and development of forging simulation software. In the Americas, the push for nearshoring and advanced manufacturing tax incentives has spurred investment in high-fidelity simulation platforms to shorten supply chains and enhance domestic production capabilities. North American aerospace primes and automotive OEMs lead in early adoption of cloud-based and AI-integrated solutions, leveraging robust computational infrastructure and skilled engineering talent.
In Europe, Middle East & Africa, stringent emissions regulations and sustainability mandates have elevated the role of thermal analysis and material optimization features. Established forging clusters in Germany, Italy, and the UK combine on-premise solutions with localized support networks, while emerging markets in the Middle East explore hybrid cloud deployments to build agile manufacturing ecosystems.
The Asia-Pacific region is characterized by rapid capacity expansion among forging shops in China, India, Japan, and South Korea. Competitive pricing pressures and supply chain diversification efforts drive uptake of cost-effective cloud-based simulation suites. Government-led smart manufacturing initiatives emphasize standardized training programs at technical colleges, accelerating software penetration in both large state-owned enterprises and independent SMEs.
This comprehensive research report examines key regions that drive the evolution of the Forging Technology Simulation Software market, offering deep insights into regional trends, growth factors, and industry developments that are influencing market performance.
- Americas
- Asia-Pacific
- Europe, Middle East & Africa
Key Company Profiles and Strategic Positioning in the Market
The competitive landscape features a mix of specialized vendors and diversified software powerhouses, each advancing unique strategies to capture market share. Altair Engineering Inc. emphasizes open-architecture platforms that integrate AI-driven process optimization, while Ansys Inc. continues to invest in comprehensive multiphysics solvers and cloud collaboration tools. AutoForm Engineering GmbH focuses on sheet metal forming excellence, and Crescent Technologies leverages proprietary algorithms for defect prediction.
Dassault Systèmes differentiates through unified 3DEXPERIENCE environments, offering end-to-end product lifecycle integration, whereas DEFORM (Scientific Forming Technologies Corporation) remains a leader in forging-specific finite element analysis. FEMFAT (Magna Powertrain) tailors its fatigue analysis capabilities for powertrain components, and Forming Technologies Inc. (FTI) emphasizes user-centric interfaces for accelerated die validation.
Matchware Technologies and MSC Software (Hexagon) cater to both simulation novices and advanced users with scalable licensing models, while Northeastern Forge combines software with hardware test beds to validate process innovations. Quintus Technologies provides high-pressure forming simulation for specialized industries, and Simufact Engineering targets aerospace and automotive sectors with detailed material libraries. Transvalor rounds out the roster with focused solutions for forging and heat treatment, enabling seamless transitions from design to production.
This comprehensive research report delivers an in-depth overview of the principal market players in the Forging Technology Simulation Software market, evaluating their market share, strategic initiatives, and competitive positioning to illuminate the factors shaping the competitive landscape.
- Altair Engineering Inc.
- Ansys Inc.
- AutoForm Engineering GmbH
- Crescent Technologies
- Dassault Systemes
- DEFORM (Scientific Forming Technologies Corporation)
- FEMFAT (Magna Powertrain)
- Forming Technologies Inc. (FTI)
- Matchware Technologies
- MSC Software (Hexagon)
- Northeastern Forge
- Quintus Technologies
- Simufact Engineering
- Transvalor
Actionable Recommendations for Industry Leaders to Drive ROI
To capitalize on the evolving simulation software landscape, industry leaders should prioritize the following strategies:
- Align Simulation Investments with Sustainability Goals: Integrate thermal and material optimization modules to reduce energy consumption and scrap rates, enhancing both environmental performance and cost savings.
- Adopt Hybrid Deployment Models: Balance cloud-based scalability with on-premise control to meet data security requirements while leveraging elastic computing power for peak workloads.
- Cultivate Cross-Functional Collaboration: Establish shared simulation platforms and data repositories across R&D, production, and quality assurance teams to accelerate decision-making and drive continuous process improvements.
- Leverage AI and Machine Learning: Incorporate automated model calibration and defect prediction algorithms to shorten validation cycles and anticipate material behavior under extreme conditions.
- Expand Training and Support Ecosystems: Partner with educational institutions to develop certification programs and on-the-job training initiatives, ensuring a skilled workforce capable of extracting maximum value from advanced simulation tools.
By implementing these recommendations, forging operations can enhance agility, drive innovation, and secure a competitive edge in increasingly complex manufacturing environments.
Explore AI-driven insights for the Forging Technology Simulation Software market with ResearchAI on our online platform, providing deeper, data-backed market analysis.
Ask ResearchAI anything
World's First Innovative Al for Market Research
Conclusion: Elevating Forging Excellence with Integrated Simulation
As forging technology simulation software continues to mature, its role shifts from an auxiliary validation tool to a central pillar of digital transformation. Companies that embed simulation early in their product development lifecycles reap benefits in reduced prototyping costs, accelerated time-to-market, and improved quality consistency. The convergence of AI, cloud computing, and intuitive user interfaces further democratizes access, empowering organizations of all sizes to harness advanced modeling capabilities.
Looking ahead, the ability to integrate real-time production data with virtual simulations will enable closed-loop feedback systems that continuously refine process parameters and respond dynamically to material variability. Organizations that embrace these trends will not only optimize existing operations but also pioneer new forging techniques, materials, and component designs. Ultimately, the strategic deployment of simulation software will underpin the next wave of manufacturing innovation and ensure long-term competitiveness in a rapidly evolving industrial landscape.
This section provides a structured overview of the report, outlining key chapters and topics covered for easy reference in our Forging Technology Simulation Software market comprehensive research report.
- Preface
- Research Methodology
- Executive Summary
- Market Overview
- Market Dynamics
- Market Insights
- Cumulative Impact of United States Tariffs 2025
- Forging Technology Simulation Software Market, by Application
- Forging Technology Simulation Software Market, by Software Type
- Forging Technology Simulation Software Market, by End User
- Forging Technology Simulation Software Market, by Technology Integration
- Forging Technology Simulation Software Market, by Industry Vertical
- Americas Forging Technology Simulation Software Market
- Asia-Pacific Forging Technology Simulation Software Market
- Europe, Middle East & Africa Forging Technology Simulation Software Market
- Competitive Landscape
- ResearchAI
- ResearchStatistics
- ResearchContacts
- ResearchArticles
- Appendix
- List of Figures [Total: 26]
- List of Tables [Total: 1085 ]
Next Steps: Engage with Ketan Rohom to Access the Full Market Report
Ready to deepen your understanding of the forging technology simulation software market? Contact Ketan Rohom, Associate Director, Sales & Marketing, to secure your comprehensive market research report. Gain exclusive insights into emerging trends, competitive strategies, and technology roadmaps that will inform your next strategic move. Reach out today to explore tailored licensing options and unlock the full potential of simulation-driven forging processes.
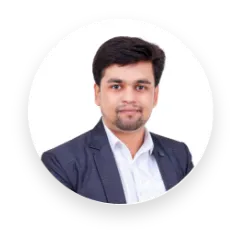
- When do I get the report?
- In what format does this report get delivered to me?
- How long has 360iResearch been around?
- What if I have a question about your reports?
- Can I share this report with my team?
- Can I use your research in my presentation?