Introduction to the Evolving Forklift Aftermarket Services Landscape
The aftermarket services segment for forklifts has become an indispensable component of material handling operations, ensuring uptime, operational efficiency, and cost optimization for businesses across diverse industries. As fleets age and utilization intensifies, organizations are prioritizing comprehensive maintenance and repair solutions to extend equipment lifecycles and reduce unplanned downtime. This evolution has transformed the aftermarket landscape into a strategic arena where service providers compete on innovation, responsiveness, and value-added offerings. In this context, stakeholders-from fleet managers to third-party workshops-must navigate complex service portfolios, regulatory pressures, and changing end-user demands. Against this backdrop, a concise understanding of the current state of the forklift aftermarket, coupled with emerging trends and disruptive forces, is critical for executives seeking to refine their service strategies and capitalize on growth opportunities.
Transformative Shifts Rewriting Service Delivery Paradigms
Digital transformation and sustainability imperatives have ushered in transformative shifts across the forklift aftermarket. Advanced telematics and IoT-enabled sensors now collect real-time performance data, empowering predictive analytics engines to forecast component wear and schedule corrective maintenance before failures occur. This shift from reactive to predictive maintenance not only curtails unplanned downtime but also optimizes spare-parts inventory by aligning replacement cycles with actual usage patterns.
Simultaneously, a growing emphasis on environmental compliance has accelerated adoption of electric powertrains and eco-friendly lubricants within maintenance programs. Service providers are retooling their offerings to encompass battery health diagnostics and regenerative braking calibrations, catering to fleets migrating toward zero-emission operations. In parallel, additive manufacturing is emerging as a disruptive force; on-site 3D printing of complex parts reduces lead times and logistical bottlenecks, challenging traditional distribution models.
These technological and regulatory drivers are converging to reshape service delivery: fleet operators demand digital service portals for seamless scheduling and billing, while aftermarket specialists integrate remote troubleshooting capabilities to minimize truck idle time. Consequently, market participants who leverage data-driven insights and sustainable service designs are poised to secure competitive advantage in an increasingly dynamic environment.
Cumulative Impact of 2025 US Tariffs on Aftermarket Services
The introduction of new cumulative tariffs in 2025 has added a layer of complexity to the US forklift aftermarket by inflating the cost of imported components and subassemblies. Tariff adjustments on battery components, engine parts, transmission systems and sensors have triggered a reassessment of global sourcing strategies among both OEMs and third-party suppliers. Organizations reliant on cross-border supply chains are now grappling with higher landed costs, prompting many to explore domestic manufacturing alternatives or nearshore partnerships to mitigate the impact.
Consequently, service providers are recalibrating maintenance packages to reflect increased input costs. Preventive and predictive maintenance contracts have been restructured with tiered pricing that accounts for escalated component expenses. Some large fleet operators are opting to expand in-house servicing capabilities for hydraulic and mechanical repairs, aiming to bypass third-party markups exacerbated by tariffs. Conversely, independent workshops are renegotiating supplier agreements and investing in regional distribution hubs to consolidate buying power and secure volume discounts.
Overall, the tariff landscape has accelerated the shift toward localized supply networks, reinforcing the strategic importance of agile inventory management. Market participants that successfully balance cost pressures with service excellence will emerge as leaders in a post-tariff marketplace.
Key Segmentation Insights Underpinning Service Strategies
A granular view of service type segmentation reveals a trifurcated ecosystem of maintenance, parts replacement, and repairs. Within maintenance, corrective protocols address unexpected breakdowns, predictive approaches use sensor data to anticipate failures, and preventive schedules maintain optimal performance. Parts replacement is anchored by battery components vital to electric fleets, engine parts for internal combustion trucks, and transmission parts that govern power delivery. Repair services are subdivided into electrical diagnostics and wiring restorations, hydraulic leak remediation, and mechanical overhauls for drive trains and lift assemblies.
Examining service provider segmentation, in-house teams range from dedicated large fleet maintenance divisions to smaller scale operations managing compact fleets; OEM service centers extend both multiple brand and single brand support; third-party workshops operate through franchised networks with standardized processes alongside independent shops offering specialized, bespoke solutions.
An end-user segmentation lens highlights logistics and warehousing operators, spanning distribution center managers to third-party logistics providers. Manufacturing industries include automotive assembly lines, food and beverage processing plants, and heavy machinery production facilities. Retail and e-commerce clients cover traditional brick-and-mortar storefronts as well as rapidly expanding online retail platforms.
Forklift types command distinct aftermarket demands: electric and internal combustion counterbalance models require unique maintenance protocols; manual versus powered pallet stackers differ in wear patterns and service intervals; moving mast and tilting mast reach trucks present specialized hydraulic and control system needs.
Purchase mode segmentation differentiates customers securing equipment through authorized dealers or direct OEM purchase, those on long- or short-term leases, and users preferring daily or monthly rental contracts. Finally, component type segmentation underscores electrical systems such as motors and sensors, engine components including air filters and spark plugs, and transmission systems featuring gearboxes and torque converters, each demanding tailored diagnostics and replacement procedures.
This comprehensive research report categorizes the Forklift Aftermarket Services market into clearly defined segments, providing a detailed analysis of emerging trends and precise revenue forecasts to support strategic decision-making.
- Service Type
- Service Provider
- End User
- Forklift Type
- Purchase Mode
- Component Type
Key Regional Dynamics Shaping Aftermarket Growth
Regionally, the Americas aftermarket is characterized by mature maintenance frameworks in North America, where fleet operators prioritize predictive maintenance and digital service management. Procurement shifts toward authorized dealer networks respond to risk mitigation goals, while independent workshops in Latin America are investing in capacity expansions to meet rising demand from growing logistics hubs.
In Europe, Middle East & Africa, stringent emissions regulations in the European Union drive accelerated uptake of electric forklifts and corresponding battery health services. Manufacturers in the Middle East integrate automated warehousing solutions, fueling demand for specialized electrical repairs. Across Africa, infrastructure investments in ports and distribution centers are catalyzing growth in on-site corrective and mechanical repair offerings.
The Asia-Pacific region remains the fastest-growing aftermarket, propelled by rapid e-commerce expansion in China and India. Local OEMs and third-party providers are forging franchise networks to standardize preventive maintenance across sprawling logistics parks. In Japan and South Korea, advanced sensor-based diagnostics and remote monitoring services are becoming mainstream, reflecting a shift toward Industry 4.0-driven service delivery.
This comprehensive research report examines key regions that drive the evolution of the Forklift Aftermarket Services market, offering deep insights into regional trends, growth factors, and industry developments that are influencing market performance.
- Americas
- Asia-Pacific
- Europe, Middle East & Africa
Competitive Company Insights into Aftermarket Leadership
Leading aftermarket portfolios reflect diverse strategic priorities among top players. Toyota Material Handling, Crown Equipment Corporation and Jungheinrich AG are strengthening integrated service networks with digital portals that streamline maintenance scheduling and parts ordering. Clark Material Handling Company and Komatsu Forklift USA, LLC emphasize localized support centers and mobile service units to ensure rapid response times.
Doosan Industrial Vehicle America Corp. and Hyster-Yale Group, Inc. have entered strategic alliances with franchise networks, enabling independent workshops to deliver standardized OEM-approved repairs. Hangcha Group Co., Ltd. and Hyundai Material Handling are investing heavily in battery diagnostics and regenerative braking calibrations to service the electric counterbalance segment in Asia. KION North America Corporation and Linde Material Handling prioritize predictive analytics capabilities, deploying advanced telematics for real-time fleet health monitoring.
Mitsubishi Caterpillar Forklift America Inc. and Raymond Corporation integrate 3D printing for rapid component fabrication, reducing dependency on external suppliers. STILL GmbH and UniCarriers Americas Corporation expand leasing and rental offerings to accommodate fluctuating end-user capital expenditures. Yale Materials Handling Corporation is enhancing training programs for technicians, ensuring proficiency in emerging hydraulic and electrical system diagnostics.
This comprehensive research report delivers an in-depth overview of the principal market players in the Forklift Aftermarket Services market, evaluating their market share, strategic initiatives, and competitive positioning to illuminate the factors shaping the competitive landscape.
- Clark Material Handling Company
- Crown Equipment Corporation
- Doosan Industrial Vehicle America Corp.
- Hangcha Group Co., Ltd.
- Hyster-Yale Group, Inc.
- Hyundai Material Handling
- Jungheinrich AG
- KION North America Corporation
- Komatsu Forklift USA, LLC
- Linde Material Handling
- Mitsubishi Caterpillar Forklift America Inc. (MCFA)
- Raymond Corporation
- STILL GmbH
- Toyota Material Handling, U.S.A. Inc.
- UniCarriers Americas Corporation
- UNICARRIERS Systems Solutions
- Yale Materials Handling Corporation
Actionable Recommendations for Industry Leaders
Invest in robust predictive maintenance platforms that leverage IoT and machine learning to minimize downtime and optimize parts inventory. Foster partnerships with local component manufacturers and nearshore suppliers to reduce exposure to tariff-induced cost volatility. Expand multi-channel service networks by integrating franchised workshops alongside in-house and OEM centers, ensuring geographic and operational coverage. Customize service agreements by end-user vertical, offering specialized packages for logistics, manufacturing, and retail applications. Develop flexible pricing models across direct purchase, leasing, and rental modalities to align with customer capital strategies. Enhance technician training in advanced hydraulic, electrical and additive manufacturing techniques to maintain service quality amid evolving equipment complexities.
Explore AI-driven insights for the Forklift Aftermarket Services market with ResearchAI on our online platform, providing deeper, data-backed market analysis.
Ask ResearchAI anything
World's First Innovative Al for Market Research
Conclusion: Navigating Tomorrow’s Aftermarket with Agility and Insight
The forklift aftermarket services sector stands at the cusp of a data-driven revolution, propelled by digital maintenance tools, sustainability requirements, and shifting trade policies. Service providers who adapt to predictive maintenance paradigms, cultivate resilient supply chains in response to tariffs, and tailor solutions to nuanced segmentation insights will secure long-term competitive advantage. Regional nuances and the strategic initiatives of leading companies offer valuable blueprints for success. By embracing technology, fostering strategic partnerships, and remaining responsive to end-user priorities, market participants can navigate the complexities of the aftermarket landscape and drive sustained growth.
This section provides a structured overview of the report, outlining key chapters and topics covered for easy reference in our Forklift Aftermarket Services market comprehensive research report.
- Preface
- Research Methodology
- Executive Summary
- Market Overview
- Market Dynamics
- Market Insights
- Cumulative Impact of United States Tariffs 2025
- Forklift Aftermarket Services Market, by Service Type
- Forklift Aftermarket Services Market, by Service Provider
- Forklift Aftermarket Services Market, by End User
- Forklift Aftermarket Services Market, by Forklift Type
- Forklift Aftermarket Services Market, by Purchase Mode
- Forklift Aftermarket Services Market, by Component Type
- Americas Forklift Aftermarket Services Market
- Asia-Pacific Forklift Aftermarket Services Market
- Europe, Middle East & Africa Forklift Aftermarket Services Market
- Competitive Landscape
- ResearchAI
- ResearchStatistics
- ResearchContacts
- ResearchArticles
- Appendix
- List of Figures [Total: 28]
- List of Tables [Total: 1077 ]
Call to Action: Connect with Ketan Rohom for the Complete Report
Ready to elevate your aftermarket strategy? Contact Ketan Rohom, Associate Director, Sales & Marketing, to secure your comprehensive market research report and gain the insights you need to outpace the competition.
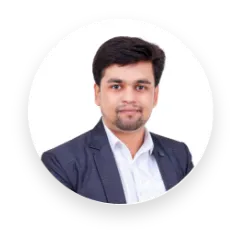
- When do I get the report?
- In what format does this report get delivered to me?
- How long has 360iResearch been around?
- What if I have a question about your reports?
- Can I share this report with my team?
- Can I use your research in my presentation?