Introduction to the Form-in-Place Gasket Material Market
Over the past decade, the form-in-place gasket (FIPG) sector has emerged as a critical enabler of efficient, high-performance sealing solutions across industrial and commercial applications. By dispensing liquid or two-component materials directly onto mating surfaces, FIPG delivers custom-fit seals that streamline assembly processes, cut cycle times, and reduce inventory complexity. Recent advances in automated dispensing systems and robotic integration have further propelled adoption as manufacturers pursue higher throughput, repeatable precision, and minimal waste. At the same time, tightening environmental regulations and heightened safety standards have driven accelerated innovation in silicone, urethane, and acrylic chemistries. High-temperature cures, low-odour formulations, and rapid-set systems now coexist with engineered polymers designed for chemical resistance and dynamic stress. As a result, design teams are reevaluating traditional pre-cut gasket inventories in favor of inline application strategies that lower total cost of ownership while enhancing performance reliability. This executive summary equips decision-makers with a clear, concise view of the FIPG landscape, spotlighting strategic drivers, material breakthroughs, and market dynamics set to influence sourcing and engineering choices in the year ahead.
Transformative Shifts Redefining the Form-in-Place Gasket Material Landscape
Manufacturing automation has reshaped FIPG deployment, elevating precision through CNC-controlled dispensing equipment and collaborative robotics. Concurrently, demand for lightweight, fuel-efficient designs in transportation has spurred interest in low-mass silicone and urethane gaskets, offering both sealing integrity and mass reduction. Sustainability imperatives have also gained traction: water-based acrylics and solvent-free silicones minimize volatile organic compound (VOC) emissions while addressing lifecycle assessments.
Digitalization is another transformative force. Real-time process monitoring, predictive maintenance algorithms, and closed-loop quality systems now enable proactive defect detection and tighter tolerances. Material suppliers leverage data analytics to tailor formulations for specific cure profiles and application methods, bridging the gap between lab development and shop-floor performance.
Meanwhile, cross-industry convergence is widening FIPG usage. Automotive OEMs, once the dominant adopters, now share the stage with electronics manufacturers seeking dust-proof enclosures and food & beverage processors requiring hygienic, FDA-compliant seals. In this evolving environment, agility and material versatility have become core competitive advantages.
Evaluating the Cumulative Impact of U.S. Tariffs in 2025
In early 2025, the United States implemented a new tranche of tariffs affecting imported raw materials and components used in FIPG formulations. Key feedstocks such as specialty silicones and advanced urethane precursors saw duty hikes that directly impacted input costs. Suppliers have navigated these increases by renegotiating procurement contracts, localizing certain production activities, and accelerating development of alternative chemistries sourced from tariff-exempt regions.
The cumulative effect of these measures has varied across the supply chain. Large global producers with integrated manufacturing networks have absorbed a significant portion of cost inflation by optimizing yield and leveraging scale. At the same time, smaller compounders face margin pressure, prompting them to pass through higher unit costs or reformulate products using domestic or allied-country raw materials. End-users in highly competitive industries, like consumer electronics, are particularly sensitive to these price shifts and are exploring hybrid material strategies that blend tariff-exempt acrylics with minimal quantities of imported silicone.
Overall, the 2025 tariff landscape has catalyzed a strategic shift toward supply-chain resilience, with stakeholders prioritizing local sourcing, greater inventory buffers, and multi-supplier engagement to mitigate further trade-related disruptions.
Key Segmentation Insights Driving Material and Application Choices
Insight into segment performance reveals that material choice remains at the core of FIPG strategy. Acrylic chemistries, including epoxy acrylates and polyurethane acrylates, continue to dominate applications requiring rapid cure and low-temperature flex. Silicone formulations-whether liquid or solid-excel where thermal stability and chemical inertness are paramount, and urethane variants, from single-component to two-component systems, meet demands for abrasion resistance and high mechanical strength. Understanding the nuances between these sub-groups empowers specification teams to align seal properties precisely with operating environments.
Application methods further differentiate market dynamics. Automated dispensing via CNC machines, precision dispensers, and robotic applicators offers unmatched repeatability in high-volume production lines, while manual techniques using brushes or hand guns remain indispensable for prototyping, repair, and low-volume assemblies. Each method requires tailored rheology, cure kinetics, and adhesion profiles to ensure process efficiency and bond integrity.
Industry verticals drive unique performance criteria. Aerospace applications bifurcate into commercial and defense segments, each governed by stringent certification and traceability standards. Automotive sectors leverage FIPG in engine and transmission systems to reduce leak rates and enable lightweight housings. In electronics, consumer devices demand dust-proof and moisture-resistant seals, whereas industrial electronics focus on extended durability under harsh conditions. Meanwhile, food & beverage processors select FDA-compliant resin systems for both food processing machinery and packaging equipment, balancing hygiene with clean-room compatibility.
Gasket types carve out distinct use cases: high-temperature cures and room-temperature cures for cured-in-place gaskets address different assembly schedules and heating constraints, moisture-cure and room-temperature-vulcanizing variants of liquid applied gaskets offer flexible on-demand sealing solutions, and closed-cell or open-cell pre-formed foam gaskets provide rapid assembly with predictable compression set. Finally, end-user environments dictate chemical resistance, thermal range, and weathering performance: from acid and alkali resistant systems to seals rated for cryogenic applications, high-temperature service above 250°C, or UV and moisture resistance outdoors. Aligning these segmentation layers enables optimized material selection, streamlined inventory, and targeted performance outcomes.
This comprehensive research report categorizes the Form in Place Gasket Material market into clearly defined segments, providing a detailed analysis of emerging trends and precise revenue forecasts to support strategic decision-making.
- Material Type
- Application Method
- Industry Vertical
- Gasket Type
- End-User Environment
Regional Dynamics Shaping the Global Form-in-Place Gasket Market
North and South America remain pivotal markets, fueled by strong automotive, aerospace, and electronics manufacturing bases that prioritize local sourcing and integrated supply chains. In contrast, Europe, the Middle East & Africa exhibit fragmented demand patterns: European Tier 1 OEMs adopt advanced automation faster, the Middle Eastern energy sector specifies high-performance seals for extreme temperatures, and African infrastructure projects drive basic gasket needs in construction and utilities.
Asia-Pacific commands significant growth potential, with China and India investing heavily in domestic manufacturing and automation. Japanese and South Korean producers continue to push boundaries in semiconductor packaging and consumer electronics, demanding ultra-low-contamination silicone systems. Meanwhile, Southeast Asian contract manufacturers offer attractive cost structures for manual application markets serving regional clientele. Recognizing these regional nuances allows global players to tailor distribution networks, adjust product portfolios, and localize technical support to capture the full spectrum of opportunity.
This comprehensive research report examines key regions that drive the evolution of the Form in Place Gasket Material market, offering deep insights into regional trends, growth factors, and industry developments that are influencing market performance.
- Americas
- Asia-Pacific
- Europe, Middle East & Africa
Competitive Overview: Leading Players in the Gasket Material Sector
The competitive arena features both diversified conglomerates and specialized sealant manufacturers. 3M Company leverages its global research infrastructure to advance novel adhesives and dispense systems, while Dow Inc. focuses on scalable silicone and urethane platforms with integrated supply networks. ElringKlinger AG and Freudenberg Sealing Technologies deliver engineered gasket tapes and in-house application machinery, combining hardware and chemistry for turnkey solutions.
Henkel AG & Co. KGaA applies strength in high-performance acrylics and epoxy acrylates to serve automotive and industrial electronics, whereas Hernon Manufacturing, Inc. and J-B Weld Company target niche repair and aftermarket segments with easy-use kits. Mitsubishi Chemical Corporation and Wacker Chemie AG push polymer innovation in liquid silicone rubbers and moisture-cure systems, driving next-generation thermal stability and chemical resistance.
Parker Hannifin Corporation and Permatex, Inc. integrate fluid and gas sealing expertise, offering both pre-formed and in-place gasket solutions. Saint-Gobain Performance Plastics specializes in foam gaskets and high-temperature elastomers designed for aerospace and defense. Trelleborg AB and Victor Reinz – Dana Incorporated round out the field with heavy-duty cured-in-place systems optimized for engine and transmission assemblies. Collectively, these companies illustrate a market defined by vertical integration, material science leadership, and the strategic pairing of dispensing technology with advanced resin formulations.
This comprehensive research report delivers an in-depth overview of the principal market players in the Form in Place Gasket Material market, evaluating their market share, strategic initiatives, and competitive positioning to illuminate the factors shaping the competitive landscape.
- 3M Company
- Dow Inc.
- ElringKlinger AG
- Freudenberg Sealing Technologies
- Henkel AG & Co. KGaA
- Hernon Manufacturing, Inc.
- J-B Weld Company
- Mitsubishi Chemical Corporation
- Parker Hannifin Corporation
- Permatex, Inc.
- Saint-Gobain Performance Plastics
- Trelleborg AB
- Victor Reinz - Dana Incorporated
- Wacker Chemie AG
Actionable Recommendations for Industry Leaders
First, prioritize investment in advanced dispensing automation. By integrating CNC machines, precision dispensers, and collaborative robots, manufacturers can achieve tighter tolerances, reduce material waste, and scale production with consistent quality. Second, develop modular material portfolios that address specific end-user environments; for example, offer dedicated acid-resistant silicone grades for chemical processing and cryogenic-rated urethanes for cold-storage applications.
Third, reinforce supply-chain resilience by diversifying raw material sources and expanding regional production footprints. Engaging with multiple suppliers of key monomers and catalysts will mitigate exposure to trade policy shifts. Fourth, collaborate with end-user engineering teams to co-develop rapid-cure formulations that align with lean manufacturing initiatives, reducing cure cycle times and accelerating time to market.
Fifth, leverage digital quality platforms to monitor dispensing parameters in real time, enabling proactive adjustments and defect prevention. Finally, invest in comprehensive training programs for application technicians, ensuring proper handling of both manual and automated systems to maximize seal integrity and process efficiency.
Explore AI-driven insights for the Form in Place Gasket Material market with ResearchAI on our online platform, providing deeper, data-backed market analysis.
Ask ResearchAI anything
World's First Innovative Al for Market Research
Conclusion: Charting the Path Forward in Gasket Material Innovation
The form-in-place gasket market stands at an inflection point where material innovation, automation, and supply-chain agility intersect to redefine sealing strategies across industries. Companies that master the integration of advanced chemistries with precise dispensing technologies will secure competitive advantages in performance, cost, and responsiveness. Moreover, a deep understanding of segmentation layers-from material types and application methods to industry-specific requirements-enables targeted product development and optimized inventory management.
As regional dynamics evolve and trade policies fluctuate, proactive risk management and localized production will become essential to maintain margin stability. Finally, forging strategic partnerships between material suppliers, OEMs, and equipment manufacturers will fuel the next wave of breakthroughs in high-temperature, low-VOC, and rapid-cure formulations. By aligning these elements within a cohesive roadmap, businesses can chart a course toward sustainable growth and enduring market leadership.
This section provides a structured overview of the report, outlining key chapters and topics covered for easy reference in our Form in Place Gasket Material market comprehensive research report.
- Preface
- Research Methodology
- Executive Summary
- Market Overview
- Market Dynamics
- Market Insights
- Cumulative Impact of United States Tariffs 2025
- Form in Place Gasket Material Market, by Material Type
- Form in Place Gasket Material Market, by Application Method
- Form in Place Gasket Material Market, by Industry Vertical
- Form in Place Gasket Material Market, by Gasket Type
- Form in Place Gasket Material Market, by End-User Environment
- Americas Form in Place Gasket Material Market
- Asia-Pacific Form in Place Gasket Material Market
- Europe, Middle East & Africa Form in Place Gasket Material Market
- Competitive Landscape
- ResearchAI
- ResearchStatistics
- ResearchContacts
- ResearchArticles
- Appendix
- List of Figures [Total: 26]
- List of Tables [Total: 942 ]
Take the Next Step: Engage for In-Depth Market Intelligence
To explore these insights in greater depth and secure a competitive edge, reach out to Ketan Rohom (Associate Director, Sales & Marketing at 360iResearch). Engage with an expert who can tailor the full market research report to your strategic priorities, deliver detailed technical appendices, and provide personalized guidance on material selection, supply-chain optimization, and automation integration. Take the next step toward informed decision-making-contact Ketan today to unlock the comprehensive analysis your organization needs.
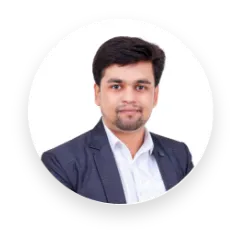
- When do I get the report?
- In what format does this report get delivered to me?
- How long has 360iResearch been around?
- What if I have a question about your reports?
- Can I share this report with my team?
- Can I use your research in my presentation?