The Formic Acid Vacuum Reflow Oven Market size was estimated at USD 1.54 billion in 2024 and expected to reach USD 1.63 billion in 2025, at a CAGR 5.95% to reach USD 2.18 billion by 2030.

Unveiling the Rise of Formic Acid Vacuum Reflow Oven Technology
Formic acid vacuum reflow ovens represent a breakthrough in soldering technology, enabling unparalleled precision in lead-free and high-reliability assemblies. These systems harness the chemical reactivity of formic acid vapors under controlled vacuum conditions to remove surface oxides and promote superior wetting, resulting in stronger solder joints with reduced risk of bridging and tombstoning. As electronic devices continue to shrink and incorporate complex multi-layer architectures, the demand for repeatable and defect-free soldering processes has never been higher. The vacuum environment not only eliminates entrapped gases but also supports the use of lower temperature profiles, minimizing thermal stress on sensitive components.
By integrating advanced vacuum pumps, infrared and convection heating modules, and real-time monitoring software, modern formic acid vacuum reflow ovens deliver consistent process control at scale. Manufacturers in automotive, aerospace, medical, and consumer electronics sectors are increasingly adopting these solutions to comply with stringent reliability standards and to improve yield rates. Transitioning from traditional convection-only reflow ovens, industry leaders are now investing in hybrid configurations that can seamlessly switch between formic acid reflow and vacuum reflow cycles, addressing both small-batch prototyping and high-volume production needs.
The growing trend toward Industry 4.0 has further accelerated the adoption of these ovens, as digital insights and closed-loop controls enable predictive maintenance and rapid recipe adjustments. With sustainability and safety protocols evolving, the use of formic acid requires robust off-gas treatment and compliant handling procedures, prompting manufacturers to partner closely with equipment suppliers who can ensure adherence to environmental regulations. The introduction of modular designs and scalable footprints has made it easier for mid-tier producers to leverage advanced reflow technologies, leveling the playing field and driving broader market penetration.
Navigating Transformative Shifts Reshaping the Reflow Oven Landscape
Over the past decade, the reflow oven landscape has undergone a radical transformation driven by the convergence of several key forces. Rapid advances in semiconductor packaging, including chip-scale packages and 3D stacking, have compelled equipment manufacturers to deliver ovens capable of exacting thermal profiles and vacuum levels. At the same time, the push for electric and autonomous vehicles has expanded the application base for high-reliability assemblies, prompting reflow oven designers to enhance throughput without compromising quality. Meanwhile, heightened focus on environmental stewardship has accelerated the deployment of gas abatement systems that capture and neutralize harmful off-gases, aligning process efficiency with corporate sustainability goals.
Digitalization has emerged as another pivotal shift, as cloud-based analytics and edge computing now drive real-time monitoring of temperature gradients, vacuum integrity, and formic acid concentration. This integration of smart sensors and machine learning algorithms empowers operators to detect anomalies early and implement process corrections on the fly, reducing downtime and scrap rates. Moreover, the ongoing consolidation among equipment suppliers and the formation of strategic alliances with chemical providers have optimized supply chains and expanded service networks. As a result, reflow oven offerings are no longer limited to hardware alone but encompass end-to-end solutions that blend equipment, consumables, and process expertise into a single turnkey ecosystem.
Furthermore, geopolitical shifts and evolving trade agreements have prompted manufacturers to reevaluate their production footprints, spurring innovation in portable and skid-mounted reflow ovens that can be deployed at regional hubs. As market participants seek to balance cost pressures with the need for agility, flexible lease and rental models for advanced reflow ovens are gaining traction, enabling faster technology adoption without large capital outlays. Collectively, these trends underscore a transformative period in the reflow oven sector, characterized by heightened specialization, digital integration, and a relentless drive toward higher yields and compliance.
Assessing the Cumulative Impact of 2025 US Tariffs
In early 2025, the imposition of additional tariffs on imported semiconductor assembly equipment in the United States has reshaped procurement strategies and cost structures across the industry. Equipment manufacturers supplying formic acid vacuum reflow ovens have encountered steep duty surcharges on components sourced from key manufacturing hubs, prompting many to reevaluate their global sourcing networks. These tariffs have increased landed costs for end users, compelling contract manufacturers and original equipment manufacturers alike to reassess long-term capital expenditure plans and explore alternative regions for equipment assembly.
The ripple effects extend beyond hardware acquisition. Raw material suppliers of formic acid and filtration media have also faced trade barriers, driving raw material costs upward and squeezing operational margins. In response, several leading equipment providers have accelerated the expansion of local assembly lines within North America, mitigating the impact of import duties and ensuring faster lead times. Meanwhile, end users are employing creative strategies such as forming purchasing consortia, negotiating long-term supply agreements to lock in favorable terms, and accepting incremental price premiums in exchange for prioritized delivery and extended warranty coverage.
Despite these challenges, the tariff environment has catalyzed a broader shift toward localized production and service ecosystems. By deepening partnerships with regional distributors and investing in domestic manufacturing capabilities, companies are rebuilding resilience into their supply chains. Over the coming years, this redistribution of production activities is expected to foster new centers of excellence in reflow technology and spur the development of complementary services, from on-site training to remote diagnostic support.
In-Depth Market Segmentation Revealing Hidden Growth Drivers
Analysis of the market reveals distinct performance characteristics and adoption rates based on a variety of segmentation parameters. When evaluating product type, for instance, manufacturers must decide between batch configurations, which offer flexible processing for prototype and small-lot requirements, and inline or continuous systems that deliver high throughput for large-scale production environments. The choice of technology further refines this decision, with some lines leveraging pure formic acid reflow to remove oxides at atmospheric pressure while others employ vacuum reflow augmented by formic acid vapor injection to achieve superior solder joint integrity and reduce voiding.
Process type also plays a critical role in shaping equipment requirements. Systems designed for post-soldering operations focus on reflow soldering inspection and defect reduction, whereas pre-soldering processes emphasize surface preparation through formic acid vapor conditioning. Integrated soldering processes manage the entire thermal profile from pre-bake through reflow to post-soldering cooling. Power source considerations introduce another layer of differentiation, as electric-powered ovens offer precise temperature control and cleaner operation, while gas-powered models can deliver higher ramp rates and reduced cycle times.
Oven capacity is a further determinant of application fit. Large-capacity units support multiple boards per cycle and accommodate oversized assemblies, whereas medium-capacity ovens strike a balance between footprint and throughput for midsize production runs. Small-capacity platforms cater to specialized applications and research labs, offering compact dimensions without sacrificing control capabilities. Distribution channels also influence market dynamics, with offline sales through established equipment distributors providing hands-on support and service contracts, while online channels enable digital procurement and rapid quote turnaround.
Finally, end-user requirements across applications drive specification sheets and process recipes. Aerospace and defense sectors demand traceable process validation and adherence to military standards. Automotive manufacturers prioritize high-yield, high-reliability assemblies capable of withstanding harsh environments. Consumer electronics producers value cycle time efficiency and cost-of-ownership metrics, and medical device fabricators require stringent contamination control and process repeatability. This multifaceted segmentation framework highlights the nuanced requirements that inform equipment selection and process optimization strategies in the formic acid vacuum reflow oven market.
This comprehensive research report categorizes the Formic Acid Vacuum Reflow Oven market into clearly defined segments, providing a detailed analysis of emerging trends and precise revenue forecasts to support strategic decision-making.
- Product Type
- Technology
- Process Type
- Power Source
- Oven Capacity
- Distribution Channel
- Application
Regional Dynamics Shaping Global Market Trajectories
Regional markets exhibit unique demand drivers and adoption patterns that reflect local manufacturing ecosystems and regulatory landscapes. In the Americas, leading automotive, aerospace, and medical device producers have embraced advanced reflow oven technologies to meet rigorous quality and reliability standards. The United States, in particular, has become a focal point for domestic production initiatives, leveraging incentives and reshoring programs to bolster supply chain security and reduce dependency on offshore manufacturing.
Across Europe, Middle East and Africa, the landscape is characterized by mature industrial bases and stringent environmental regulations. Western European nations have invested heavily in energy-efficient oven designs and comprehensive off-gas treatment systems to comply with carbon reduction commitments and chemical safety directives. Meanwhile, emerging economies in the Middle East and Africa are gradually adopting vacuum reflow capabilities, spurred by infrastructure development and rising demand for high-end electronics in telecommunications and defense sectors.
In the Asia-Pacific region, high-volume consumer electronics hubs and semiconductor manufacturing clusters have historically driven market expansion. China and South Korea continue to dominate in manufacturing scale, while Japan contributes deep expertise in precision engineering and process automation. More recently, India and Southeast Asian nations have emerged as alternative production centers, attracting investments in advanced assembly lines and diversified sourcing strategies. The interplay of local policies, labor dynamics, and technological partnerships across these regions underscores the global mosaic of opportunities for formic acid vacuum reflow oven suppliers.
This comprehensive research report examines key regions that drive the evolution of the Formic Acid Vacuum Reflow Oven market, offering deep insights into regional trends, growth factors, and industry developments that are influencing market performance.
- Americas
- Europe, Middle East & Africa
- Asia-Pacific
Competitive Analysis of Leading Industry Players
Leading equipment manufacturers have differentiated themselves through continuous innovation, strategic partnerships, and comprehensive service offerings. A prominent global systems supplier has solidified its position by introducing modular vacuum reflow platforms with upgradeable pump packages and smart recipe management software that seamlessly integrates into factory automation networks. Another key player has emphasized sustainability by developing energy-recovery heat exchangers and closed-loop off-gas abatement units compatible with formic acid vapor streams, reducing operational carbon footprints while maintaining throughput.
Some established companies have pursued growth through targeted acquisitions, expanding their footprints in emerging markets and bolstering after-sales support networks. These moves have enabled rapid deployment of field service teams and spare parts distribution centers, enhancing uptime guarantees and compliance training for end users. Specialized technology providers have carved out niches by optimizing reflow profiles for lead-free alloys and high-density interconnect boards, offering tailored processing solutions that address the unique requirements of consumer electronics and medical device applications.
Collaborative ventures between equipment OEMs and chemical suppliers have yielded co-developed formic acid formulations that balance oxide reduction efficiency with material compatibility, resulting in process chemistries that deliver consistent performance across diverse board finishes and solder alloys. These strategic integrations, coupled with remote monitoring platforms and predictive maintenance tools, have elevated the competitive landscape, compelling all market participants to align their roadmaps around digital transformation and sustainable manufacturing practices.
This comprehensive research report delivers an in-depth overview of the principal market players in the Formic Acid Vacuum Reflow Oven market, evaluating their market share, strategic initiatives, and competitive positioning to illuminate the factors shaping the competitive landscape.
- 3S Silicon Tech Inc.
- ATV Technologie GmbH
- BTU International
- Chengliankaida Technology.co.,LTD
- DKSH Holding Ltd.
- EIGHTECH TECTRON Co., Ltd.
- Heller Industries, Inc.
- HIRATA Corporation
- Invacu Ltd.
- ITW Electronics Assembly Equipment
- Kurtz Holding GmbH & Co Beteiligungs KG
- Origin Co., Ltd.
- Palomar Technologies
- PINK GmbH Thermosysteme
- Rehm Thermal Systems GmbH
- SANYOSEIKO CO., LTD.
- SEHO Systems GmbH
- Shinapex Co. Ltd.
- Sikama International, Inc.
- Tamura Corporation
- UniTemp GmbH
- Yield Engineering Systems
Strategic Recommendations to Secure Competitive Advantage
To maintain a leadership position in the evolving reflow oven arena, industry stakeholders should prioritize investments in digital control capabilities that enable adaptive process correction and real-time quality feedback. By integrating advanced analytics with machine learning models, manufacturers can reduce defect rates and optimize energy consumption across varied production campaigns. In parallel, diversifying supply chains through localized assembly and strategic partnerships with regional service providers will mitigate tariff risks and shorten equipment delivery cycles.
Sustainability must be embedded at the core of product development and operational strategies. Companies should broaden their portfolio of energy-efficient designs and closed-loop gas abatement solutions to align with global decarbonization commitments and end-user environmental targets. Collaborating with formic acid suppliers to co-engineer next-generation chemistries can further drive process consistency while lowering handling risks.
Workforce development represents another critical dimension. Establishing comprehensive training programs that educate technicians on best practices for vacuum sealing, vapor handling, and preventive maintenance will ensure that advanced systems deliver on their performance promises. Lastly, offering flexible financing models-including equipment-as-a-service and rental arrangements-can expand market reach among mid-tier manufacturers seeking the benefits of cutting-edge reflow technology without the burden of upfront capital investment.
Rigorous Methodology Underpinning Research Insights
This research initiative was designed to deliver a robust and transparent framework that informs strategic decision-making in the formic acid vacuum reflow oven sector. The methodology combined extensive secondary research, including peer-reviewed journals, industry white papers, and regulatory filings, with primary interviews conducted with equipment engineers, materials specialists, and senior procurement managers. Data triangulation techniques were employed to cross-verify findings across multiple sources, ensuring consistency and credibility.
Quantitative data on technology adoption rates and supply chain configurations were synthesized alongside qualitative insights into buyer preferences and service expectations. Market participants were surveyed to gauge satisfaction levels with existing equipment offerings, while in-depth discussions with process engineers provided clarity on emerging technical challenges and innovation drivers. All collected data underwent rigorous validation through expert panels and sensitivity analysis to identify potential biases and confirm the reliability of conclusions.
The resulting body of work offers a comprehensive view of the current market ecosystem, highlighting technological inflection points, competitive dynamics, and regulatory catalysts. This transparent approach enables stakeholders to trust the insights presented and to apply them with confidence in corporate strategy, product development, and investment planning.
Explore AI-driven insights for the Formic Acid Vacuum Reflow Oven market with ResearchAI on our online platform, providing deeper, data-backed market analysis.
Ask ResearchAI anything
World's First Innovative Al for Market Research
Key Takeaways and Future Outlook for Stakeholders
As the electronics and semiconductor assembly landscape continues to evolve, formic acid vacuum reflow ovens have emerged as a vital enabler of high-yield, high-reliability manufacturing. Their unique combination of chemical oxide removal and vacuum-assisted reflow addresses the stringent demands of today’s most critical applications, from automotive safety systems to life-saving medical devices. Despite headwinds posed by trade regulations and the need for stringent environmental controls, innovation in digitalization and modular design has ensured that these systems remain adaptable and efficient.
The market’s nuanced segmentation underscores the importance of tailoring oven configurations to specific production scenarios-whether that involves inline continuous processing for consumer electronics or small-batch prototyping for aerospace components. Regional dynamics, from localized reshoring initiatives in the Americas to energy efficiency drives in Europe and capacity expansions across Asia-Pacific, further accentuate the global nature of the opportunity. Competitive pressures have galvanized key players to advance service models, digital platforms, and collaborative chemistries, raising the bar for performance and sustainability.
Looking ahead, companies that embrace integrated solutions-combining hardware, software, and consumables-will be best positioned to navigate regulatory shifts and cost pressures. By aligning development roadmaps with end-user priorities, from reduced carbon footprints to improved throughput, equipment suppliers can capture long-term value and drive the next phase of growth in reflow oven technology.
This section provides a structured overview of the report, outlining key chapters and topics covered for easy reference in our Formic Acid Vacuum Reflow Oven market comprehensive research report.
- Preface
- Research Methodology
- Executive Summary
- Market Overview
- Market Dynamics
- Market Insights
- Cumulative Impact of United States Tariffs 2025
- Formic Acid Vacuum Reflow Oven Market, by Product Type
- Formic Acid Vacuum Reflow Oven Market, by Technology
- Formic Acid Vacuum Reflow Oven Market, by Process Type
- Formic Acid Vacuum Reflow Oven Market, by Power Source
- Formic Acid Vacuum Reflow Oven Market, by Oven Capacity
- Formic Acid Vacuum Reflow Oven Market, by Distribution Channel
- Formic Acid Vacuum Reflow Oven Market, by Application
- Americas Formic Acid Vacuum Reflow Oven Market
- Europe, Middle East & Africa Formic Acid Vacuum Reflow Oven Market
- Asia-Pacific Formic Acid Vacuum Reflow Oven Market
- Competitive Landscape
- ResearchAI
- ResearchStatistics
- ResearchContacts
- ResearchArticles
- Appendix
- List of Figures [Total: 30]
- List of Tables [Total: 323 ]
Secure Your Comprehensive Report with Expert Guidance from Ketan Rohom
For enterprises seeking an authoritative guide to formic acid vacuum reflow oven technology and market dynamics, this comprehensive report delivers actionable insights and strategic clarity. Our analysis synthesizes industry trends, competitive landscapes, and regulatory considerations to equip leaders with the information needed to make informed decisions. To obtain a full copy of the research, please reach out to Ketan Rohom, Associate Director, Sales & Marketing, who can provide detailed purchasing options and discuss how the findings align with your organizational objectives. Elevate your strategic planning and gain a competitive edge by securing this essential resource today.
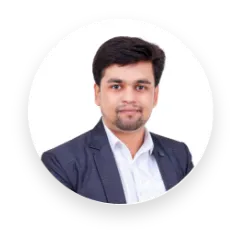
- How big is the Formic Acid Vacuum Reflow Oven Market?
- What is the Formic Acid Vacuum Reflow Oven Market growth?
- When do I get the report?
- In what format does this report get delivered to me?
- How long has 360iResearch been around?
- What if I have a question about your reports?
- Can I share this report with my team?
- Can I use your research in my presentation?