The Foundry Binder Market size was estimated at USD 3.89 billion in 2024 and expected to reach USD 4.10 billion in 2025, at a CAGR 5.18% to reach USD 5.28 billion by 2030.

Navigating the Next Era of Technological Convergence
As the pace of technological innovation accelerates, industry stakeholders face an intricate mosaic of opportunities and challenges. Grounded in an era defined by digital transformation and converging IT infrastructures, the market is witnessing an unprecedented demand for integrated solutions that can deliver agility, resilience and scalability. Emerging trends in cloud computing, edge deployment and advanced analytics are reshaping enterprise priorities, compelling organizations to reevaluate their technology roadmaps.
Against this backdrop, decision-makers must navigate a complex interplay of hardware, software and services. Hardware platforms are evolving to support next-generation networking, high-density storage and modular server architectures. Simultaneously, software ecosystems are expanding to encompass hybrid cloud orchestration, AI-driven analytics and robust security frameworks. Professional service offerings-from strategic consulting to hands-on implementation and ongoing support-play a pivotal role in ensuring seamless adoption and optimization of these technologies.
This report delivers a concise yet comprehensive overview of the forces driving this dynamic landscape. It synthesizes the latest market data, examines regulatory influences such as trade policies and tariffs, and highlights the competitive moves that will define the industry’s trajectory. With these insights, industry leaders can craft informed strategies that harness innovation and mitigate emerging risks.
Unveiling Transformative Shifts Reshaping the Industry Landscape
The market landscape is undergoing transformative shifts driven by the convergence of cloud-native architectures, edge computing and intelligent automation. Cloud adoption has transcended basic infrastructure migration, catalyzing the widespread deployment of hybrid models that blend public, private and on-premises environments. This hybrid paradigm is enabling organizations to optimize cost, compliance and performance, while also supporting latency-sensitive use cases at the network edge.
Concurrently, the rise of artificial intelligence and machine learning has elevated data management and analytics from back-office utilities to core strategic assets. Enterprises are embedding predictive insights across customer experience platforms, supply chain systems and security operations, thereby unlocking new avenues for differentiation. Networking equipment is becoming more programmable and software-defined, fostering resilient architectures that can adapt to fluctuating workloads and evolving threat landscapes.
At the same time, increasing regulatory scrutiny around data sovereignty and cybersecurity is prompting a shift toward platforms with built-in compliance controls and transparent governance mechanisms. These regulatory imperatives are accelerating investments in identity and access management, threat detection and integrated risk management solutions. As a result, industry participants must recalibrate their offerings to align with both technological imperatives and evolving compliance frameworks.
Assessing the Cumulative Impact of US Tariffs in 2025
In 2025, the cumulative impact of United States tariffs has reverberated across global supply chains, prompting a reassessment of sourcing strategies and cost structures. Hardware vendors have faced elevated input costs for critical components such as semiconductors and networking switches, compelling many to negotiate alternative procurement channels or adjust their pricing models. This pressure has, in turn, influenced enterprise purchasing decisions, with a segment of buyers accelerating digital transformation investments before additional tariff escalations.
Software and services providers have not remained immune. The necessity to localize data centers and deploy regionally compliant solutions has gained traction as organizations seek to mitigate exposure to cross-border trade restrictions. Consulting and implementation partners have observed an uptick in demand for advisory services centered on tariff risk assessment and supply chain diversification. Support and maintenance contracts are likewise being revisited to incorporate flexible terms that address potential cost fluctuations.
Looking forward, the enduring effect of these trade policies is expected to spur greater vertical integration among hardware manufacturers, increased partnerships with domestic suppliers and a renewed emphasis on software-driven differentiation. Organizations that proactively adapt their sourcing and deployment strategies will be best positioned to navigate volatility and maintain competitive agility in a tariff-sensitive environment.
Revealing Critical Insights Across Key Market Segments
Critical insights emerge when examining key market segments across component, deployment model, application, end user and service type dimensions. Within the component sphere, hardware maintains a foundational role, with networking equipment encompassing routers and switches, servers spanning blade, rack-mounted and tower formats, and storage solutions that include NAS and SAN configurations. Complementing this, the services domain extends from consulting to implementation, support and training responsibilities, while software components bifurcate into cloud and on-premises platforms, with hybrid, private and public cloud variants enabling tailored deployment strategies.
By deployment model, the binary of cloud versus on-premises persists, yet hybrid configurations have garnered pronounced market momentum. Organizations are strategically balancing performance and compliance requirements by blending public and private cloud footprints, ensuring optimal workload placement. In the application segment, enterprise resource planning, customer relationship management and marketing automation continue to anchor core operations, whereas advanced data management-encompassing analytics, governance and integration-fuels data-driven decision-making. Security imperatives such as identity and access management and threat detection and prevention have become indispensable components of every enterprise technology stack.
End-user adoption patterns reveal diverse sectoral dynamics. Financial services, public sector agencies and healthcare institutions are prioritizing resilience and regulatory compliance, while IT and telecom providers drive network modernization. Manufacturing sub-verticals such as automotive, electronics, food and beverages and medical devices are digitalizing production lines with IoT-enabled platforms. Retail and consumer goods enterprises are optimizing omnichannel experiences through integrated software and analytics solutions. Service type segmentation underscores the enduring importance of advisory and implementation expertise, alongside ongoing support and specialized training to maximize solution value.
This comprehensive research report categorizes the Foundry Binder market into clearly defined segments, providing a detailed analysis of emerging trends and precise revenue forecasts to support strategic decision-making.
- Component
- Deployment Model
- Application
- End User
- Service Type
Decoding Regional Dynamics Driving Global Market Growth
Regional dynamics are exerting a profound influence on market trajectories and investment patterns. In the Americas, digital transformation initiatives are flourishing across both established enterprises and emerging disruptors. North American firms are accelerating cloud migrations, driven by competitive pressures to streamline operations and enhance customer engagement. Latin American markets demonstrate growing interest in software-defined networking and security solutions, catalyzed by expanding digital economies and government modernization programs.
Meanwhile, Europe, the Middle East and Africa present a tapestry of regulatory complexity and innovation hubs. Western European organizations are prioritizing sustainability and data sovereignty, prompting investments in green data centers and privacy-centric architectures. In the Middle East, sovereign wealth funds and public-private partnerships are channeling capital into smart city deployments and next-generation telecom infrastructure. African markets, though at varying stages of digital maturity, are witnessing rapid adoption of mobile-first applications and cloud-based services, often leapfrogging legacy constraints.
Asia-Pacific remains a hotbed of technological innovation, with leading economies embracing AI-driven platforms and 5G rollouts. China’s government-backed initiatives continue to drive domestic semiconductor production and cloud expansion. Southeast Asian nations are forging regional alliances to bolster digital trade corridors and cross-border data flows. Australia and New Zealand focus on enhancing cybersecurity resilience and regulatory frameworks to support enterprise-grade cloud adoption. These varied regional dynamics underscore the importance of localized strategies that align with market-specific drivers and policy landscapes.
This comprehensive research report examines key regions that drive the evolution of the Foundry Binder market, offering deep insights into regional trends, growth factors, and industry developments that are influencing market performance.
- Americas
- Europe, Middle East & Africa
- Asia-Pacific
Profiling Leading Companies Innovating the Market Frontier
The competitive arena is shaped by a dynamic mix of established technology providers and emerging challengers. Market leaders have leveraged expansive product portfolios encompassing hardware, software and services to deliver end-to-end solutions. Their strategic investments in research and development, vertical integration and ecosystem partnerships have reinforced their market positions while fostering innovation in areas such as network automation and AI-powered security.
Simultaneously, niche players are gaining traction by focusing on specialized offerings that address discrete customer pain points. Companies with strengths in data governance and integration tools are capturing demand from enterprises seeking to operationalize big data initiatives. Other firms have built reputations around advanced identity and access management solutions, bolstering enterprise security postures in an era of escalating cyber threats. Cloud-native specialists continue to expand their footprints by delivering containerized and microservices-based platforms that cater to agile development practices.
Collaborations between technology vendors and consulting partners have become instrumental in accelerating time-to-value for complex deployments. Strategic alliances are forming around co-innovation labs, joint go-to-market programs and integrated support networks. As consolidation waves sweep through the industry, companies that demonstrate agility, domain expertise and customer-centric innovation will be best positioned to capture incremental market share.
This comprehensive research report delivers an in-depth overview of the principal market players in the Foundry Binder market, evaluating their market share, strategic initiatives, and competitive positioning to illuminate the factors shaping the competitive landscape.
- Hexion Inc.
- SI Group, Inc.
- BASF SE
- Ingevity Corporation
- Sumitomo Bakelite Co., Ltd.
- Evonik Industries AG
- DIC Corporation
- Arkema S.A.
- Chiyoda Chemical Co., Ltd.
- Olin Corporation
Strategic Actions to Seize Emerging Opportunities
To capitalize on emerging opportunities, industry leaders must adopt a multi-faceted approach. First, organizations should prioritize platform interoperability by investing in open standards and API-driven architectures that facilitate seamless integration across diverse environments. This will accelerate time-to-market for new services and reduce vendor lock-in risks. Next, enterprises need to strengthen their security and compliance frameworks by embedding identity-centric controls and AI-augmented threat detection into every layer of the technology stack, ensuring resilience against evolving cyber threats.
Furthermore, executives should cultivate strategic supplier and partner ecosystems that enhance supply chain flexibility. By diversifying procurement channels and co-innovating with local hardware and software specialists, companies can mitigate tariff volatility and accelerate localized deployments. Simultaneously, organizations must champion a data-first culture, investing in analytics and governance capabilities that drive actionable insights and operational efficiency. Workforce upskilling is also critical: training programs should focus on emerging disciplines such as DevSecOps, cloud orchestration and data science to maintain a competitive talent pipeline.
Finally, leaders should engage in scenario planning exercises that evaluate potential regulatory changes, technological disruptions and macroeconomic shifts. By stress-testing strategic roadmaps against multiple futures, organizations can build the agility required to pivot quickly and seize advantages in an ever-evolving market environment.
Ensuring Rigor Through a Robust Research Methodology
This research is anchored in a rigorous, multi-stage methodology designed to ensure accuracy and relevance. Primary data was obtained through in-depth interviews with senior executives, industry analysts and technology architects, providing firsthand perspectives on market dynamics. Secondary sources, including government publications, regulatory filings and reputable industry journals, were systematically reviewed to corroborate and enhance these insights.
Quantitative analysis involved evaluating historical trends and cross-segment performance metrics, with a focus on component adoption rates, deployment model preferences and application use cases. Supply chain impacts, including the effects of tariffs and trade policies, were modeled using established economic frameworks. Regional market assessments drew upon proprietary databases and validated third-party intelligence to account for localized variances in regulation, infrastructure maturity and investment patterns.
Finally, all findings underwent peer review by subject-matter experts to validate assumptions and interpretive frameworks. This comprehensive approach ensures that the report’s conclusions and recommendations rest on a solid foundation of empirical evidence and critical analysis, equipping decision-makers with actionable insights grounded in the latest industry realities.
Explore AI-driven insights for the Foundry Binder market with ResearchAI on our online platform, providing deeper, data-backed market analysis.
Ask ResearchAI anything
World's First Innovative Al for Market Research
Synthesis of Findings and Strategic Implications
The synthesis of this research underscores a market at the crossroads of innovation, regulation and shifting geopolitical dynamics. The integration of hybrid cloud models, AI-driven analytics and programmable networking is redefining enterprise architectures, while tariff pressures and supply chain complexities continue to shape sourcing strategies. As market segmentation reveals distinct dynamics across components, deployment models, applications and end users, it becomes clear that a one-size-fits-all approach is no longer tenable.
Regional nuances further complicate the competitive landscape, with the Americas, EMEA and Asia-Pacific each exhibiting unique growth drivers and regulatory hurdles. Leading companies are differentiating through open ecosystems, specialized security offerings and strategic partnerships, even as emerging challengers carve out niches in data management and identity solutions. Actionable recommendations emphasize interoperability, supply chain resilience, data-centric cultures and continuous workforce development as key enablers of sustained market leadership.
In conclusion, organizations that embrace an integrated strategy-balancing technological innovation with agile risk management and localized execution-will be best positioned to thrive. The market’s evolution demands both visionary leadership and meticulous operational discipline, ensuring that enterprises can harness growth opportunities while navigating the complexities of this dynamic environment.
This section provides a structured overview of the report, outlining key chapters and topics covered for easy reference in our Foundry Binder market comprehensive research report.
- Preface
- Research Methodology
- Executive Summary
- Market Overview
- Market Dynamics
- Market Insights
- Cumulative Impact of United States Tariffs 2025
- Foundry Binder Market, by Component
- Foundry Binder Market, by Deployment Model
- Foundry Binder Market, by Application
- Foundry Binder Market, by End User
- Foundry Binder Market, by Service Type
- Americas Foundry Binder Market
- Europe, Middle East & Africa Foundry Binder Market
- Asia-Pacific Foundry Binder Market
- Competitive Landscape
- ResearchAI
- ResearchStatistics
- ResearchContacts
- ResearchArticles
- Appendix
- List of Figures [Total: 26]
- List of Tables [Total: 734 ]
Engage with Ketan Rohom to Secure the Full Market Report
Thank you for exploring this comprehensive market research summary. To gain access to the full suite of in-depth analysis, proprietary data and strategic recommendations, we invite you to connect with Ketan Rohom, Associate Director of Sales & Marketing. Engaging with Ketan will ensure you receive tailored guidance on how this report can empower your organization’s decision-making and shape your competitive advantage. Reach out today to secure your copy and accelerate your strategic initiatives in this rapidly evolving market landscape.
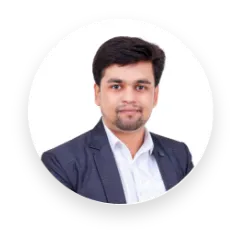
- How big is the Foundry Binder Market?
- What is the Foundry Binder Market growth?
- When do I get the report?
- In what format does this report get delivered to me?
- How long has 360iResearch been around?
- What if I have a question about your reports?
- Can I share this report with my team?
- Can I use your research in my presentation?