Introduction to Full Ceramic Coating Die Market Dynamics
Full ceramic coating die technology represents a pivotal shift in manufacturing precision components, combining exceptional wear resistance with unparalleled thermal and chemical stability. By leveraging advanced ceramic formulations and state-of-the-art deposition techniques, producers achieve tooling surfaces that extend service life, reduce downtime, and maintain consistent dimensional tolerances under extreme conditions. These coatings not only safeguard high-value dies against abrasive wear and corrosive environments but also optimize heat transfer and frictional properties, unlocking new possibilities across sectors as varied as aerospace propulsion systems, automotive powertrains, and semiconductor wafer processing. As industries demand ever-greater efficiency, reliability, and sustainability, full ceramic coating die solutions have transitioned from niche applications to mainstream adoption.
The convergence of material science breakthroughs and innovative application methods is catalyzing rapid evolution in this field. Emerging demands for lighter, faster, and cleaner processes have elevated ceramics to the center of tooling strategies aimed at boosting throughput while minimizing energy consumption. This report presents an incisive overview of the current landscape, highlights critical inflection points influencing competitive dynamics, and lays the groundwork for informed decision-making by technical specialists and executive leaders.
Transformative Technological and Regulatory Shifts in the Landscape
In recent years, the full ceramic coating die market has undergone several transformative shifts driven by technological advancements and shifting end-user requirements. First, the refinement of sol-gel and chemical vapor deposition techniques has enabled the creation of ultra-thin, uniform ceramic layers that adhere more effectively to complex geometries. This precision has unlocked performance gains in tooling applications for semiconductor front-end and back-end wafer processing, where even microscopic irregularities can compromise yield.
Simultaneously, rising pressure to decarbonize manufacturing has spurred development of environmentally friendly thermal spray processes, such as high-velocity oxygen fuel (HVOF) and plasma spraying, which minimize volatile organic compound emissions. As a result, sectors like aerospace and defense are increasingly specifying ceramics with inherent thermal barrier properties to reduce engine temperatures and enhance fuel efficiency. Moreover, the integration of artificial intelligence-driven monitoring systems enables real-time feedback on coating integrity, predicting potential failures before they occur and shifting maintenance strategies from reactive to predictive.
Collectively, these advancements are reshaping competitive corridors. Companies that invest in multifunctional coating chemistries-combining hardness, corrosion resistance, and self-lubricating characteristics-are carving out leadership positions. The industry’s trajectory underscores an imperative to align research and development with evolving regulatory standards and customer performance benchmarks.
Cumulative Impact of United States Tariffs 2025
The imposition of United States tariffs in 2025 has introduced a complex layer of challenges for stakeholders in the full ceramic coating die market. Higher duties on imported raw ceramic powders and specialized equipment have led to upward pressure on input costs, compelling suppliers to reevaluate their sourcing strategies. In response, several major coating method providers have established localized manufacturing hubs within the Americas to mitigate tariff exposure and streamline supply chains.
These protective measures have, in turn, influenced procurement practices among automotive and power generation OEMs. Many are accelerating qualification of regional coating partners and exploring alternative materials that balance performance with cost efficiency. While short-term margin compression has tested the resilience of smaller players, larger integrated manufacturers with diversified geographical footprints have leveraged economies of scale to absorb a portion of the duty burden.
Beyond cost considerations, heightened trade barriers have stimulated strategic alliances aimed at technology transfer and joint ventures. Collaborative efforts between North American and European ceramic specialists are accelerating the deployment of advanced deposition processes, effectively bypassing tariff constraints. As businesses adapt, the collective impact of these measures underscores the need for agile operations, robust cross-border partnerships, and proactive policy engagement to sustain growth in a tariff-sensitive environment.
Key Segmentation Insights Across Materials, Applications, and Methods
A nuanced understanding of market segmentation offers critical insights into where growth and innovation are most pronounced. When categorized by material type, ceramic coating die solutions range from alumina through aluminum-based compounds and silicon carbide to zirconia, each delivering a tailored balance of hardness, thermal resistance, and chemical inertness for specific process requirements. Examining the application dimension reveals distinct performance demands in sectors such as aerospace and defense-where propulsion system components and structural parts must endure extreme thermal cycles-while automotive industry users prioritize brake system durability, engine component longevity, and exhaust system corrosion protection. Medical device manufacturers select diagnostic equipment and surgical instruments that benefit from biocompatible ceramic barriers, whereas oil and gas operators opt for coatings on drilling equipment and pipeline interiors to resist abrasion and chemical attack. In the power generation arena, both energy storage systems and turbine blades exploit ceramic die coatings for improved thermal management, and semiconductor manufacturers depend on backend and frontend wafer processing tools to uphold microscopic tolerances without particulate contamination.
Delving into coating method preferences, aerosol deposition offers cold-spray versatility, while chemical vapor deposition techniques-split between atomic layer deposition and plasma-enhanced CVD-provide unmatched uniformity. Physical vapor deposition variants like ion plating and magnetron sputtering excel at creating dense, adherent layers, and thermal spray methods, including high-velocity oxygen fuel spraying and plasma spraying, deliver thicker coatings at higher deposition rates. End-user industry segmentation spans automotive aftermarket and OEM manufacturer requirements, construction sector demands for abrasion-resistant tooling, defense and military specifications, consumer and industrial electronics, energy and power needs in oil, gas, and renewables, as well as healthcare applications covering dental and orthopedic devices. Further granularity emerges when considering form factor choices-bulk form ceramics, nanocoatings, powder feedstocks, layered thickness options, and thin films-as well as manufacturing techniques such as extrusion, injection molding, pressing and sintering, slip casting, and thickness-based classifications from sub-10 microns to layers exceeding 100 microns.
This comprehensive research report categorizes the Full Ceramic Coating Die market into clearly defined segments, providing a detailed analysis of emerging trends and precise revenue forecasts to support strategic decision-making.
- Material Type
- Application
- Coating Method
- End-User Industry
- Form Factor
- Manufacturing Technique
- Thickness
Key Regional Insights Highlighting Growth Hubs and Regulatory Drivers
Geographical analysis reveals that the Americas have consolidated a leadership position, largely driven by robust automotive and aerospace demand in North America, coupled with strategic investments in regional coating facilities to offset tariff impacts. Meanwhile, Latin American manufacturers are gradually adopting advanced quenching and spraying processes to service growing renewable energy and medical device markets.
In Europe, the Middle East & Africa region, stringent environmental regulations have accelerated adoption of low-emission coating methods, making Western European countries hotbeds for research into water-based ceramic slurries and solvent-free deposition. The Middle East’s focus on oil and gas infrastructure refurbishment and African energy initiatives demand abrasion-resistant ceramic layers for drilling and pipeline components, spurring localized partnerships.
Asia-Pacific continues to offer compelling growth opportunities, with China, Japan, South Korea, and India leading in semiconductor manufacturing tool upgrades and automotive production line expansions. Government programs supporting high-tech export readiness and green manufacturing have encouraged major coating equipment suppliers to establish joint ventures and training centers throughout the region. These regional dynamics underscore the necessity for market participants to calibrate strategies based on local regulatory frameworks, end-user end-market drivers, and supply chain configurations.
This comprehensive research report examines key regions that drive the evolution of the Full Ceramic Coating Die market, offering deep insights into regional trends, growth factors, and industry developments that are influencing market performance.
- Americas
- Asia-Pacific
- Europe, Middle East & Africa
Key Companies Insights and Competitive Differentiators
Competitive dynamics in the full ceramic coating die space are defined by innovation agility, service breadth, and regional footprint. Adams Polishes champions user-friendly aerosol formulations that streamline onsite application, while CarPro Global differentiates through proprietary nanocoating chemistries targeted at consumer and industrial segments. Ceramic Pro leads with a diversified portfolio that spans automotive brake system solutions and industrial equipment coatings. Feynlab’s focus on high-temperature stability and long-term corrosion protection sets it apart for aerospace and power generation clients. Gtechniq and GYEON Quartz excel in visual surface finishes and chemical resistance, attracting premium automotive detailers. IGL Coatings leverages eco-friendly, water-based processes, and Kamikaze Collection offers an end-to-end service model that includes technician training.
Nanoshine Group and Optimum Polymer Technologies, Inc. emphasize research collaborations on quantum-scale ceramic layers, while P&S Sales, Inc. and Pinnacle Black Label provide comprehensive distribution networks and application expertise. Shine Supply delivers turnkey aerosol spray kits, Sonax offers integrated cleaning and coating solutions, and The Detailed Image focuses on crafting bespoke coating formulations for high-end custom workshops. Together, these companies shape a marketplace where product differentiation, technical service capabilities, and supply chain resilience are key determinants of leadership.
This comprehensive research report delivers an in-depth overview of the principal market players in the Full Ceramic Coating Die market, evaluating their market share, strategic initiatives, and competitive positioning to illuminate the factors shaping the competitive landscape.
- Adam's Polishes
- CarPro Global
- Ceramic Pro
- Feynlab
- Gtechniq
- GYEON Quartz
- IGL Coatings
- Kamikaze Collection
- Nanoshine Group
- Optimum Polymer Technologies, Inc.
- P&S Sales, Inc.
- Pinnacle Black Label
- Shine Supply
- Sonax
- The Detailed Image
Actionable Recommendations for Industry Leaders to Secure Competitive Advantage
To capitalize on evolving market dynamics, industry leaders should prioritize targeted investments, strategic partnerships, and capability enhancements. First, establishing cross-functional research centers dedicated to multifunctional coatings will accelerate development of chemistries that integrate wear resistance, corrosion protection, and thermal barrier performance. Cultivating alliances with semiconductor equipment manufacturers and aerospace OEMs can secure early adoption pathways for next-generation deposition processes. Second, embedding advanced analytics and machine learning into production lines will optimize process controls, reduce waste, and enable real-time quality assurance. Third, expanding localized manufacturing and service facilities in high-growth regions-particularly within Asia-Pacific semiconductor clusters and EMEA energy refurbishment markets-will minimize tariff exposure and strengthen customer responsiveness. Fourth, enhancing technician training programs and certification pathways for coating application ensures consistent performance and drives higher contract retention. Finally, engaging proactively with regulatory bodies to shape environmental and trade policies will safeguard market access and reinforce corporate reputation for compliance and sustainability.
Explore AI-driven insights for the Full Ceramic Coating Die market with ResearchAI on our online platform, providing deeper, data-backed market analysis.
Ask ResearchAI anything
World's First Innovative Al for Market Research
Conclusion: Positioning for Long-Term Leadership and Innovation
As the full ceramic coating die market continues its rapid evolution, stakeholders who align research, operations, and market strategies with emerging performance requirements and regulatory imperatives will lead the next growth wave. Innovations in material science and deposition technologies are expanding the envelope of what’s possible across demanding applications, while shifting global trade dynamics underscore the value of localized resilience. By leveraging cross-sector partnerships and embedding data-driven process controls, companies can enhance reliability and drive cost efficiencies that translate into superior customer outcomes.
Moving forward, the ability to anticipate end-user challenges-whether in aerospace propulsion, automotive thermal management, or semiconductor yield optimization-will be the hallmark of market leaders. Those that cultivate a culture of continuous improvement, regulatory foresight, and agile execution will not only navigate current headwinds but also define future benchmarks for performance and sustainability.
This section provides a structured overview of the report, outlining key chapters and topics covered for easy reference in our Full Ceramic Coating Die market comprehensive research report.
- Preface
- Research Methodology
- Executive Summary
- Market Overview
- Market Dynamics
- Market Insights
- Cumulative Impact of United States Tariffs 2025
- Full Ceramic Coating Die Market, by Material Type
- Full Ceramic Coating Die Market, by Application
- Full Ceramic Coating Die Market, by Coating Method
- Full Ceramic Coating Die Market, by End-User Industry
- Full Ceramic Coating Die Market, by Form Factor
- Full Ceramic Coating Die Market, by Manufacturing Technique
- Full Ceramic Coating Die Market, by Thickness
- Americas Full Ceramic Coating Die Market
- Asia-Pacific Full Ceramic Coating Die Market
- Europe, Middle East & Africa Full Ceramic Coating Die Market
- Competitive Landscape
- ResearchAI
- ResearchStatistics
- ResearchContacts
- ResearchArticles
- Appendix
- List of Figures [Total: 30]
- List of Tables [Total: 913 ]
Call to Action: Engage with Ketan Rohom for In-Depth Market Intelligence
Ready to translate these insights into strategic action? Contact Ketan Rohom (Associate Director, Sales & Marketing) to explore comprehensive market intelligence and secure your competitive edge.
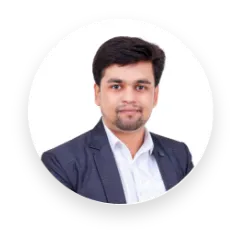
- When do I get the report?
- In what format does this report get delivered to me?
- How long has 360iResearch been around?
- What if I have a question about your reports?
- Can I share this report with my team?
- Can I use your research in my presentation?