Introduction to the Strategic Importance of Gear Forgings
The executive summary opens with an overview of the strategic significance of gear forgings in today’s industrial ecosystem. Heavy reliance on precision-forged gears underpins the performance and reliability of critical systems across aerospace, automotive, and heavy machinery sectors. These components endure extreme mechanical stresses, demanding superior material properties and manufacturing integrity. As industries pursue greater efficiency, lightweight designs, and enhanced performance, demand for advanced gear forgings continues to accelerate. Recent technological breakthroughs in forging processes and material science are redefining traditional manufacturing paradigms, enabling production of complex geometries with tighter tolerances and higher throughput. Stakeholders must navigate an intricate web of supply chain dynamics, regulatory pressures, and shifting end-use requirements. Understanding these factors is essential for manufacturers, OEMs, and investors aiming to capitalize on emerging opportunities. This introduction sets the stage for an in-depth exploration of transformative trends, trade impacts, segmentation insights, regional dynamics, and strategic priorities shaping the gear forgings landscape.
Transformative Shifts Redefining the Gear Forgings Landscape
The gear forgings sector is undergoing transformative shifts driven by rapid technological innovation and evolving market demands. Digital twins and advanced simulation tools are enabling engineers to optimize forging parameters before production begins, reducing waste and accelerating time-to-market. Robotics and automation are increasing throughput while maintaining consistent quality, empowering producers to meet stringent aerospace and automotive specifications. Sustainability has emerged as a core driver, prompting investments in energy-efficient furnaces, closed-loop hydraulic systems, and scrap recycling initiatives that minimize environmental footprints.
At the same time, Industry 4.0 integration is fostering real-time data analytics, condition monitoring, and predictive maintenance, enhancing operational resilience. Materials science breakthroughs are introducing lightweight super alloys that offer exceptional strength-to-weight ratios, addressing the performance needs of electric vehicles and next-generation aircraft. As the competitive landscape intensifies, manufacturers are forging strategic partnerships with material suppliers, technology providers, and end-users to co-innovate and streamline workflows. This confluence of digitalization, sustainability, and advanced materials is redefining value chains, creating new benchmarks for efficiency and quality in gear forging.
Cumulative Impact of United States Tariffs on Gear Forgings
The cumulative impact of recently imposed United States tariffs is reshaping sourcing strategies and cost structures in the gear forgings market. Higher import duties on a range of forged components and raw materials have driven OEMs and Tier-1 suppliers to re-evaluate global supply chains, accelerating nearshoring trends and domestic capacity expansions. As a result, forging facilities in North America are experiencing increased demand, prompting capital investments in new forging presses and finishing lines.
However, input cost inflation remains a challenge, with material suppliers absorbing part of the tariff burden while negotiating long-term contracts to stabilize pricing. End-users are implementing value-engineering initiatives to mitigate cost pressures, revising component designs for material efficiency and exploring alternative materials that offer comparable performance at lower cost. Trade partnerships with non-tariffed countries are growing, as companies seek diversified suppliers across Europe and Asia-Pacific to balance risk and maintain continuity.
Looking ahead, agile supply chain management, transparent cost modeling, and proactive stakeholder engagement will be essential to navigate the evolving tariff landscape. Companies that adapt quickly by aligning production footprints with demand patterns will gain competitive advantages in both domestic and export markets.
Key Segmentation Insights Across Material, Product, Industry, Process, and Application
Analyzing the market through a segmentation lens reveals critical insights into demand drivers and competitive dynamics. Based on material type, demand is distributed across non-ferrous metals, steel alloys, and super alloys, each with specialized subcategories. Within non-ferrous metals, aluminum dominates lightweight applications while copper and titanium address high-corrosion and high-strength requirements respectively. Steel alloys encompass alloy steel for high-strength components, carbon steel for cost-effective designs, and stainless steel where corrosion resistance is paramount. Super alloys subdivide into cobalt-based, iron-based, and nickel-based compositions, supporting demanding aerospace and power generation applications.
From a product type standpoint, closed die forgings-comprising fittings, flanges, and valves-lead high-volume, precision applications, whereas open die forgings such as blocks, discs, and rings serve heavy equipment and wind turbine shafts. Seamless rolled rings, including bearing rings, flanges, and gear rings, cater to applications requiring uniform microstructure and minimal material waste.
End-use segmentation highlights the aerospace industry’s growth in commercial aviation, helicopters, and military aviation, contrasted with the automotive sector’s expansion across commercial vehicles, electric vehicles, and passenger cars. Railway and marine segments further diversify with locomotives, ships, and submarines. Process segmentation underscores cold forging’s precision through impression die and precision forging, hot forging’s versatility via hammer and press operations, and warm forging’s balanced characteristics through roll and upset forging. Finally, application segmentation spotlights construction equipment such as excavators and loaders, drivetrain components including bearings, gears, and shafts, and engine components like connecting rods, crankshafts, and pistons.
This comprehensive research report categorizes the Gear Forgings market into clearly defined segments, providing a detailed analysis of emerging trends and precise revenue forecasts to support strategic decision-making.
- Material Type
- Product Type
- End-Use Industry
- Process
- Application
Key Regional Insights Shaping the Global Gear Forgings Market
Regional dynamics underscore how geographical factors influence supply chains, technological adoption, and regulatory environments. In the Americas, a robust manufacturing base and proximity to key automotive and aerospace OEMs support growing demand for domestically forged gears. Investments in modernization and supportive trade policies are further bolstering capacity expansions across the United States, Canada, and Mexico.
Europe, Middle East & Africa present a diverse landscape. Europe’s stringent quality standards and sustainability mandates are driving adoption of green forging technologies, while Middle Eastern investments in infrastructure projects are creating new growth avenues for heavy-equipment forgings. In Africa, emerging rail and energy sectors are gradually increasing demand, albeit from a smaller base.
Asia-Pacific remains a powerhouse of production and consumption. Rapid industrialization in China and India fuels substantial demand for automotive and railway forgings, while Japan and South Korea lead in advanced materials and precision processes for aerospace and high-performance applications. Supply chain integration and cost competitiveness position the region as both a major exporter and collaborator for global forging leaders.
This comprehensive research report examines key regions that drive the evolution of the Gear Forgings market, offering deep insights into regional trends, growth factors, and industry developments that are influencing market performance.
- Americas
- Asia-Pacific
- Europe, Middle East & Africa
Key Company Insights and Strategic Positioning in the Forgings Industry
Examining leading companies reveals varied strategies in capacity, specialization, and innovation. Alcoa Corp. leverages its expertise in aluminum forgings to serve aerospace and electric vehicle markets, while ATI (Allegheny Technologies) focuses on super alloys and high-temperature applications for power generation and defense. Aubert & Duval has carved a niche in high-end aerospace components through proprietary metallurgical processes.
In India, Bharat Forge Ltd. stands out as a vertically integrated powerhouse for automotive and industrial forgings, complemented by CEi Forge’s focus on closed die and ring products. The Ellwood Group Inc. and Farinia Group, including its Setforge division, emphasize global expansion, offering turnkey forging solutions and aftermarket services. Mettis Aerospace specializes in critical engine components, leveraging US-based facilities and JVs.
Rothe Erde GmbH brings decades of expertise in forging rings for turbines, while Scot Forge Company is renowned for large open die forgings servicing heavy machinery sectors. Siempelkamp Giesserei GmbH integrates casting and forging capabilities, differentiating through full-service solutions. Collectively, these players are driving industry consolidation, innovation partnerships, and market segmentation strategies.
This comprehensive research report delivers an in-depth overview of the principal market players in the Gear Forgings market, evaluating their market share, strategic initiatives, and competitive positioning to illuminate the factors shaping the competitive landscape.
- Alcoa Corp.
- ATI (Allegheny Technologies Incorporated)
- Aubert & Duval
- Bharat Forge Ltd.
- CEi Forge
- Ellwood Group Inc.
- Farinia Group
- Farinia Group - Setforge
- Mettis Aerospace
- Rothe Erde GmbH
- Scot Forge Company
- Siempelkamp Giesserei GmbH
Actionable Recommendations for Industry Leaders to Drive Growth and Resilience
To navigate the complex gear forgings landscape, industry leaders should prioritize a multi-pronged strategy. First, invest in digital manufacturing platforms that integrate AI-driven process optimization and real-time quality monitoring, reducing scrap rates and enhancing throughput. Second, develop strategic partnerships with material science institutions and technology providers to co-innovate lightweight alloys and advanced coatings.
Third, diversify supply chains by establishing dual-sourcing arrangements across tariff-resilient regions, ensuring production continuity and cost stability. Fourth, implement sustainability roadmaps targeting energy efficiency, carbon reduction, and circular economy principles, addressing both regulatory requirements and customer expectations. Fifth, expand workforce capabilities through targeted training programs in advanced forging techniques, data analytics, and automation maintenance.
Finally, adopt agile product development cycles to respond swiftly to emerging end-use trends in electric mobility, aerospace electrification, and renewable energy infrastructure. By executing these actionable steps, forging companies can enhance resilience, differentiate through innovation, and capture growth opportunities across evolving market segments.
Explore AI-driven insights for the Gear Forgings market with ResearchAI on our online platform, providing deeper, data-backed market analysis.
Ask ResearchAI anything
World's First Innovative Al for Market Research
Conclusion: Capitalizing on Innovation and Strategic Agility in Gear Forgings
In conclusion, the gear forgings sector stands at a pivotal juncture, defined by rapid technological advancements, evolving trade policies, and diverse end-use demands. Stakeholders must embrace digitalization and sustainability while balancing cost pressures from tariffs and raw material volatility. Detailed segmentation analysis reveals opportunities across specialized materials, precision processes, and value-add applications, underscoring the importance of tailored strategies.
Regional insights highlight the need to align production footprints with demand centers and regulatory landscapes, while competitive analysis illustrates how leading companies leverage innovation, integration, and global networks. By adopting the recommended strategic imperatives-digital transformation, supply chain diversification, sustainability roadmaps, and workforce development-industry participants can fortify their market positions and achieve long-term success.
This section provides a structured overview of the report, outlining key chapters and topics covered for easy reference in our Gear Forgings market comprehensive research report.
- Preface
- Research Methodology
- Executive Summary
- Market Overview
- Market Dynamics
- Market Insights
- Cumulative Impact of United States Tariffs 2025
- Gear Forgings Market, by Material Type
- Gear Forgings Market, by Product Type
- Gear Forgings Market, by End-Use Industry
- Gear Forgings Market, by Process
- Gear Forgings Market, by Application
- Americas Gear Forgings Market
- Asia-Pacific Gear Forgings Market
- Europe, Middle East & Africa Gear Forgings Market
- Competitive Landscape
- ResearchAI
- ResearchStatistics
- ResearchContacts
- ResearchArticles
- Appendix
- List of Figures [Total: 26]
- List of Tables [Total: 907 ]
Call-To-Action: Engage with Ketan Rohom to Unlock the Full Market Research Report
To gain deeper insights and actionable intelligence, contact Ketan Rohom, Associate Director, Sales & Marketing, for a personalized consultation. He will guide you through our comprehensive research report, tailored to your strategic priorities and operational challenges. Reach out today to secure the full market analysis and position your organization at the forefront of the gear forgings industry’s next chapter.
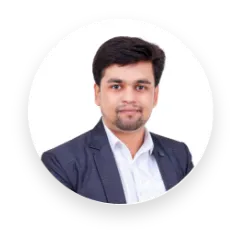
- When do I get the report?
- In what format does this report get delivered to me?
- How long has 360iResearch been around?
- What if I have a question about your reports?
- Can I share this report with my team?
- Can I use your research in my presentation?