Introduction: Contextualizing the Evolution of Gear Measurement
The gear measurement sector stands at a critical juncture where precision, efficiency, and innovation converge to redefine manufacturing standards. In an era marked by rapid technological advancements and increasing regulatory scrutiny, stakeholders require a clear overview of driving forces that shape future competitiveness. This executive summary provides a concise yet thorough exploration of emerging trends, policy shifts, and strategic opportunities that influence the adoption of measurement solutions across industries. By examining recent disruptions and established practices, this introduction sets the stage for an in-depth discussion of key transformations, tariff impacts, segmentation patterns, regional dynamics, leading players, and actionable strategies. The goal is to equip decision-makers with a cohesive narrative that bridges technical sophistication and practical implementation, ensuring that readers can anticipate change, optimize processes, and maintain a decisive edge in an increasingly quality-driven marketplace.
Transformative Shifts in the Gear Measurement Landscape
The gear measurement landscape has undergone several transformative shifts driven by automation, digital integration, and heightened quality standards. Initially dominated by manual inspection and discrete mechanical gauges, the industry progressively embraced coordinate measuring machines equipped with advanced probes. This transition to automated metrology unlocked unprecedented dimensional accuracy, laying the groundwork for real-time data analytics and closed-loop feedback.
Simultaneously, additive manufacturing and complex gear geometries prompted the development of optical digitizers and 3D scanning platforms. As a result, engineers can now capture intricate surface profiles and internal structures without physical contact. Furthermore, the rise of artificial intelligence and machine learning algorithms has accelerated defect detection, enabling predictive maintenance and process improvement far beyond traditional tolerances.
Moreover, regulatory frameworks in aerospace, automotive, and medical sectors are driving compliance requirements that demand traceability and digital records. Combined with global supply-chain complexity, these factors compel manufacturers to adopt integrated measurement ecosystems that seamlessly connect hardware, software, and data insights. Consequently, the industry is transitioning from standalone instruments to interconnected metrology platforms that support scalability, remote collaboration, and continuous optimization.
Cumulative Impact of United States Tariffs 2025 on Supply Chains
In 2025, the United States implemented new tariffs aimed at protecting domestic manufacturing while encouraging onshore production of precision components. These levies particularly target imported measurement equipment and key raw materials, such as specialized alloys used in high-precision probes and sensor housings. The immediate effect has been a notable increase in procurement costs for non-domestic devices, prompting manufacturers to reassess supplier portfolios and consider nearshoring strategies.
As a consequence, some firms have accelerated partnerships with local system integrators and begun evaluating alternative technologies that offer similar performance at lower duty exposure. In addition, the tariffs have spurred investment in modular retrofit kits to upgrade existing coordinate measuring machines, circumventing the need for full equipment replacement. Nonetheless, higher upfront expenses for new hardware have strained capital budgets, requiring more rigorous return-on-investment analyses and phased deployment plans.
Despite these challenges, the policy environment has also stimulated innovation within domestic metrology firms. Increased R&D funding and grant opportunities have led to prototypes of vision-based inspection systems and next-generation surface measurement tools. In effect, the tariffs have acted as both a catalyst for reshoring advanced equipment production and a force driving end users to optimize asset utilization and extend the lifecycle of current metrology assets.
Key Segmentation Insights Across Technologies, Industries, and Applications
The gear measurement market is dissected through multiple segmentation lenses, revealing nuanced adoption patterns. Based on technology type, stakeholders evaluate Coordinate Measuring Machines alongside Form Measuring Machines, Optical Digitizers And Scanners, Surface Measuring Machines, and Vision Measuring Machines; within CMMs, Bridge CMMs, Cantilever CMMs, Gantry CMMs, and Horizontal Arm CMMs each address different workpiece dimensions, while Length Measurement Machines and Roundness And Cylindricity Testers offer focused form analysis; Optical Digitizers encompass 3D Laser Scanners, Laser Trackers, and White Light Scanners to tackle free-form and complex geometries; Surface Measuring Machines break down into Contour Measuring Machines and Surface Roughness Testers for profile and finish quantification; Vision Measuring Machines incorporate Manual Vision Systems, Non-Contact Inspection Systems, and Optical Probing Systems for rapid, multi-feature inspection workflows.
Shifting to end-user industry segmentation, manufacturers in Aerospace And Defense leverage Commercial Aviation, Military Aviation, and Space Exploration applications that demand ultra-tight tolerances, while Automotive relies on Aftermarket, Component Suppliers, and OEM Manufacturers to balance volume throughput with quality consistency; Electronics And Electrical segments into Consumer Electronics, Semiconductor Manufacturing, and Smart Devices, each requiring miniaturized metrology solutions; Medical divides into Dental Applications, Medical Devices, and Orthopedic Implants, all governed by stringent regulatory validation; Oil And Gas spans Downstream Refining, Midstream Services, and Upstream Exploration, using robust measurement instruments to ensure equipment integrity under harsh conditions.
Application-wise, gear measurement supports Dimensional Inspection through Initial Inspection and Routine Inspection regimes, Manufacturing via Machine Fabrication and Tool Making processes, Prototyping in Functional Prototyping and Rapid Prototyping stages, Quality Control inclusive of In-Line Quality Control and Metrological Verification, and Reverse Engineering across Assembly Level Reverse Engineering and Component Level Reverse Engineering to reproduce intricate designs or update legacy parts.
Finally, product type segmentation comprises Accessories such as Calibration Tools, Fixtures And Stands, and Styli And Probe Heads; Hardware including Controllers, Probes, and Sensors; and Software embracing CAD/CAM Integration Software, Custom Metrology Software, and Quality Management Software that coordinate data capture, analysis, and reporting.
This comprehensive research report categorizes the Gear Measurement Center market into clearly defined segments, providing a detailed analysis of emerging trends and precise revenue forecasts to support strategic decision-making.
- Technology Type
- End User Industry
- Application
- Product Type
Key Regional Insights Influencing Gear Measurement Strategies
Regional dynamics play a pivotal role in shaping gear measurement adoption and innovation cycles. In the Americas, a combination of advanced manufacturing hubs and significant aerospace, automotive, and defense sectors drives demand for high-precision equipment, while tariff considerations reinforce opportunities for domestic suppliers and retrofit services. Europe, Middle East & Africa showcases a diversified landscape where stringent automotive emissions regulations, burgeoning medical device centers, and established oil and gas infrastructure foster investment in multi-functional measurement platforms appropriate for both mass production and specialized applications. In the Asia-Pacific region, rapid industrial expansion, aggressive automation initiatives, and emerging quality control standards in electronics and semiconductor clusters stimulate widespread adoption of optical digitizers and high-throughput vision systems. Cross-regional partnerships, joint ventures, and localized service networks further influence how manufacturers prioritize capital investments and after-sales support strategies.
This comprehensive research report examines key regions that drive the evolution of the Gear Measurement Center market, offering deep insights into regional trends, growth factors, and industry developments that are influencing market performance.
- Americas
- Asia-Pacific
- Europe, Middle East & Africa
Key Companies Shaping the Future of Gear Measurement
Major players in the gear measurement industry are refining portfolios and forging alliances to capture growth. Brodie Global Gear Measurement Systems is known for bespoke gear inspection cells that cater to large-scale, automotive driveline production. Gleason Corporation maintains its leadership through gear testing solutions embedded within end-to-end manufacturing cells. Hexagon Manufacturing Intelligence leverages its extensive software suite to deliver seamless integration between measurement hardware and enterprise resource planning systems. KAPP NILES focuses on high-precision cylindrical gear inspection and grinding verification, often partnering with turbine and heavy equipment producers. Klingelnberg Group differentiates itself through hybrid measuring centers that combine form, profile, and pitch analysis. Marposs S.p.A. integrates sensor-based solutions into grinding machines, enabling closed-loop control. Mitutoyo America Corporation excels in portable and stationary coordinate measurement technologies supported by broad calibration services. Tokyo Seimitsu Co., Ltd. brings vision-based inspection systems to electronics and semiconductor applications. Wenzel Group GmbH & Co. KG emphasizes modular hardware designs compatible with diverse work cell configurations. Zeiss Industrial Metrology emphasizes multi-axis, multi-sensor platforms that unify tactile and optical measurement in a single setup.
This comprehensive research report delivers an in-depth overview of the principal market players in the Gear Measurement Center market, evaluating their market share, strategic initiatives, and competitive positioning to illuminate the factors shaping the competitive landscape.
- Brodie Global Gear Measurement Systems
- Gleason Corporation
- Hexagon Manufacturing Intelligence
- KAPP NILES
- Klingelnberg Group
- Marposs S.p.A.
- Mitutoyo America Corporation
- Tokyo Seimitsu Co., Ltd.
- Wenzel Group GmbH & Co. KG
- Zeiss Industrial Metrology
Actionable Recommendations for Industry Leaders to Secure Competitive Advantage
To navigate the evolving gear measurement landscape, industry leaders should adopt a strategic framework focused on technological agility, supply-chain resilience, and value-driven partnerships. First, investing in modular metrology architectures enables seamless upgrades as new sensors, software modules, or AI-powered analytics become available. Second, diversifying supplier networks-especially by combining domestic and international sources-mitigates tariff risks and ensures continuity of critical components. Third, integrating measurement data into digital twin initiatives fosters real-time process monitoring and predictive maintenance, reducing downtime and scrap rates.
Moreover, forging collaborations with software developers and systems integrators accelerates deployment of tailored solutions without extensive in-house development. In addition, implementing comprehensive training programs for metrology technicians and engineers ensures optimal utilization of advanced systems, while structured feedback loops between operations and R&D departments drive continuous improvement. Finally, evaluating total cost of ownership over equipment lifecycle-factoring in calibration intervals, consumables, service contracts, and software licensing-allows organizations to prioritize investments that yield the highest long-term returns.
Explore AI-driven insights for the Gear Measurement Center market with ResearchAI on our online platform, providing deeper, data-backed market analysis.
Ask ResearchAI anything
World's First Innovative Al for Market Research
Conclusion: Synthesizing Insights for Future-Ready Metrology Practices
As the gear measurement sector continues to evolve, companies that remain adaptive, collaborative, and data-driven will maintain a distinct edge. By aligning technology roadmaps with customer requirements, leveraging cross-functional teams to streamline workflows, and embracing advanced analytics for process optimization, organizations can elevate precision standards and accelerate time to market. Furthermore, proactive engagement with policy developments and industry consortia ensures that regulatory shifts are anticipated, not merely responded to. Ultimately, those who marry technical excellence with strategic foresight will shape the next generation of metrology solutions, driving sustainable growth and reinforcing quality as a core competitive differentiator.
This section provides a structured overview of the report, outlining key chapters and topics covered for easy reference in our Gear Measurement Center market comprehensive research report.
- Preface
- Research Methodology
- Executive Summary
- Market Overview
- Market Dynamics
- Market Insights
- Cumulative Impact of United States Tariffs 2025
- Gear Measurement Center Market, by Technology Type
- Gear Measurement Center Market, by End User Industry
- Gear Measurement Center Market, by Application
- Gear Measurement Center Market, by Product Type
- Americas Gear Measurement Center Market
- Asia-Pacific Gear Measurement Center Market
- Europe, Middle East & Africa Gear Measurement Center Market
- Competitive Landscape
- ResearchAI
- ResearchStatistics
- ResearchContacts
- ResearchArticles
- Appendix
- List of Figures [Total: 24]
- List of Tables [Total: 1001 ]
Call-To-Action: Connect with Ketan Rohom for the Detailed Research Report
For a comprehensive exploration of these insights and to devise a tailored roadmap that aligns with your organization’s strategic objectives, reach out to Ketan Rohom, Associate Director, Sales & Marketing. Engage directly with an experienced industry advisor to secure proprietary analysis, detailed technology assessments, and implementation guidance. Take the next step toward optimizing your gear measurement operations and ensuring your organization remains at the forefront of precision engineering excellence.
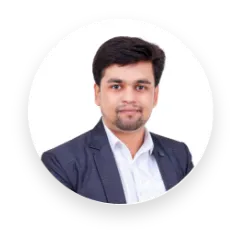
- When do I get the report?
- In what format does this report get delivered to me?
- How long has 360iResearch been around?
- What if I have a question about your reports?
- Can I share this report with my team?
- Can I use your research in my presentation?