Introduction to Glass Grinding Electric Spindle Market
The glass grinding electric spindle market stands at the intersection of precision engineering and advanced material processing, defining new benchmarks in manufacturing excellence. Demand for high-accuracy, high-speed spindles has intensified as sectors like aerospace, automotive and electronics seek tighter tolerances and faster cycle times. Technological advances such as direct-drive motor integration, enhanced bearing systems and sophisticated control architectures have fueled innovation, enabling manufacturers to address increasingly complex glass components om windshield glass to intricate display panels. As players navigate supply chain constraints and evolving regulatory dynamics, a clear understanding of market drivers and competitive forces becomes essential for informed decision-making and sustainable growth.
Transformative Shifts Reshaping the Glass Grinding Electric Spindle Landscape
Over the past five years, the landscape of glass grinding electric spindles has undergone transformative shifts driven by Industry 4.0 integration, rising automation demands and a relentless pursuit of precision. Manufacturers have leveraged digital twin technology to simulate spindle performance under varying loads, reducing design cycles and accelerating time to market. Meanwhile, the proliferation of smart sensors and IoT connectivity has elevated condition monitoring from reactive maintenance to predictive analytics, cutting downtime and extending spindle life. In parallel, demand for multi-axis machining capabilities has grown, prompting suppliers to develop dedicated spindles optimized for 5-axis glass grinding. These dynamic forces have reshaped value chains, with strategic partnerships emerging between spindle OEMs, control system providers and material science specialists.
Cumulative Impact of 2025 U.S. Tariffs on Market Dynamics
In 2025, the introduction of tightened U.S. tariffs on imported glass grinding electric spindles has reshaped procurement strategies and pricing structures. Original equipment manufacturers responded by localizing production of key components and qualifying domestic suppliers to mitigate cost spikes. Tier-1 automotive and aerospace firms initiated dual-sourcing programs to diversify risk, ensuring continuity in precision spindle supply. Simultaneously, aftermarket services gained prominence as companies extended maintenance contracts to optimize total cost of ownership. Despite initial margin compression, these adaptations have reinforced supply-chain resilience and driven incremental investment in automation lines within North America.
Key Segmentation Insights Driving Diverse Market Needs
A nuanced segmentation framework reveals diverse application requirements and performance expectations across the glass grinding electric spindle market. When examining product type, offerings range from customized grinding spindles tailored for specialized geometries to cylindrical, external, internal and surface grinding spindles optimized for standard glass profiles. Material type differentiation captures the transition from ceramic and composite spindles to metal variants-aluminum, stainless steel and titanium-alongside polymeric spindles designed for corrosion resistance and weight reduction. Speed range classifications encompass high-speed spindles operating above 10,000 RPM, medium-speed options between 5,000 and 10,000 RPM and low-speed spindles below 5,000 RPM, aligning power delivery with precision demands. Application-driven segmentation spans aerospace engine parts and structural components, automotive engine and transmission components, electronics assembly and machine tools. From an industry perspective, end users include aerospace & defense sectors-commercial and military aviation-automotive & transportation, electronics & semiconductor manufacturing, and both mass production and prototype development in manufacturing. Technology adoption covers CNC controlled spindles with retrofittable features, conventional spindles for basic operations and direct drive spindles for high-torque scenarios. Mounting styles vary among end-on mount, flange mount and through-hole configurations, while machine compatibility extends across horizontal, universal and vertical platforms. Finally, power output distinctions fall into below 10 KW, 10–50 KW and above 50 KW categories, providing a spectrum of performance profiles.
This comprehensive research report categorizes the Glass Grinding Electric Spindle market into clearly defined segments, providing a detailed analysis of emerging trends and precise revenue forecasts to support strategic decision-making.
- Product Type
- Material Type
- Speed Range
- Application
- End-User Industry
- Technology
- Mounting Style
- Machine Compatibility
- Power Output
Regional Dynamics and Growth Patterns
Regional variations underscore the strategic importance of geographical positioning and localized expertise. In the Americas, a robust automotive base and growing aerospace manufacturing hubs have spurred investments in high-precision spindles, supported by regional initiatives to reshore critical supply chains. Europe, Middle East & Africa benefit from stringent quality regulations and long-standing machine tool heritage, which drive demand for advanced direct-drive and CNC-controlled spindles. Manufacturers in this region emphasize sustainable production practices and energy-efficient designs. In the Asia-Pacific region, rapid expansion of electronics and semiconductor fabrication facilities coupled with aggressive infrastructure spending has fueled adoption of versatile grinding spindles, with local OEMs aggressively pursuing technology partnerships to close the innovation gap.
This comprehensive research report examines key regions that drive the evolution of the Glass Grinding Electric Spindle market, offering deep insights into regional trends, growth factors, and industry developments that are influencing market performance.
- Americas
- Asia-Pacific
- Europe, Middle East & Africa
Competitive Landscape: Leading Companies and Innovations
The competitive landscape is anchored by established spindle manufacturers and precision tooling specialists. Alfred Jäger GmbH leads with modular spindle architectures and integrated real-time monitoring solutions. Colonial Tool Group Inc. focuses on turnkey grinding systems endorsed by advanced spindle designs. Fischer Precise and its regional arm, Fischer USA, have carved a niche in high-speed spindle assemblies for microgrinding applications. GMN Paul Müller Industrie GmbH & Co. KG distinguishes itself through ultra-precision spindles with ceramic bearings. HEIDENHAIN Corporation combines servo control expertise with spindle innovation. Heinz Fiege GmbH and HSD SpA push boundaries in power-dense direct-drive spindles. IBAG North America and Nakanishi Inc. offer compact, high-frequency spindles ideal for tight-tolerance glass components. Posa Machinery Co., Ltd. and Shenzhen Sufeng Tool Co., Ltd. serve fast-growing Asian markets with cost-effective solutions. Swiss firm Step-Tec AG excels in customized multi-axis spindle systems, while SycoTec GmbH & Co. KG and WEISS Spindeltechnologie GmbH drive integration of smart sensors and advanced lubrication methods.
This comprehensive research report delivers an in-depth overview of the principal market players in the Glass Grinding Electric Spindle market, evaluating their market share, strategic initiatives, and competitive positioning to illuminate the factors shaping the competitive landscape.
- Alfred Jäger GmbH
- Colonial Tool Group Inc.
- Fischer Precise
- Fischer USA
- GMN Paul Müller Industrie GmbH & Co. KG
- HEIDENHAIN Corporation
- Heinz Fiege GmbH
- HSD SpA
- IBAG North America
- Nakanishi Inc.
- Posa Machinery Co., Ltd.
- Shenzhen Sufeng Tool Co., Ltd.
- Step-Tec AG
- SycoTec GmbH & Co. KG
- WEISS Spindeltechnologie GmbH
Actionable Recommendations for Industry Leaders
Industry leaders must act decisively to capitalize on evolving market conditions and technological breakthroughs. First, invest in modular spindle platforms that support rapid customization and reduce time-to-market for novel glass geometries. Second, develop in-house predictive maintenance capabilities by embedding sensor arrays and analytics software to enhance uptime and lower lifecycle costs. Third, foster strategic alliances with material suppliers to co-develop next-generation composite and ceramic spindle solutions that boost speed and wear resistance. Fourth, build regional service hubs in key markets to deliver localized support and expedite retrofit programs under changing tariff environments. Finally, adopt sustainable design practices-including energy-efficient motors and recyclable components-to align with global decarbonization mandates and differentiate offerings.
Explore AI-driven insights for the Glass Grinding Electric Spindle market with ResearchAI on our online platform, providing deeper, data-backed market analysis.
Ask ResearchAI anything
World's First Innovative Al for Market Research
Conclusion and Strategic Imperatives
The glass grinding electric spindle market is at a pivotal juncture, where innovation, resilience and strategic foresight will determine long-term success. Ongoing digital transformation, coupled with evolving trade policies and material advancements, mandates a proactive approach to R&D and supply-chain optimization. Companies that harmonize technological excellence with regional agility and customer-centric services will secure leadership positions. By leveraging predictive analytics, modular architectures and green engineering, stakeholders can drive efficiency improvements and unlock new application frontiers.
This section provides a structured overview of the report, outlining key chapters and topics covered for easy reference in our Glass Grinding Electric Spindle market comprehensive research report.
- Preface
- Research Methodology
- Executive Summary
- Market Overview
- Market Dynamics
- Market Insights
- Cumulative Impact of United States Tariffs 2025
- Glass Grinding Electric Spindle Market, by Product Type
- Glass Grinding Electric Spindle Market, by Material Type
- Glass Grinding Electric Spindle Market, by Speed Range
- Glass Grinding Electric Spindle Market, by Application
- Glass Grinding Electric Spindle Market, by End-User Industry
- Glass Grinding Electric Spindle Market, by Technology
- Glass Grinding Electric Spindle Market, by Mounting Style
- Glass Grinding Electric Spindle Market, by Machine Compatibility
- Glass Grinding Electric Spindle Market, by Power Output
- Americas Glass Grinding Electric Spindle Market
- Asia-Pacific Glass Grinding Electric Spindle Market
- Europe, Middle East & Africa Glass Grinding Electric Spindle Market
- Competitive Landscape
- ResearchAI
- ResearchStatistics
- ResearchContacts
- ResearchArticles
- Appendix
- List of Figures [Total: 34]
- List of Tables [Total: 814 ]
Connect with Ketan Rohom to Access the Full Report
Secure unparalleled competitive advantage by accessing the comprehensive market research report. Contact Ketan Rohom, Associate Director, Sales & Marketing, to purchase the full analysis and gain exclusive insights into the glass grinding electric spindle market.
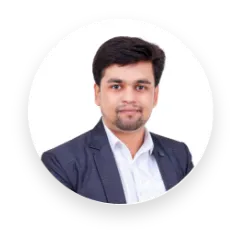
- When do I get the report?
- In what format does this report get delivered to me?
- How long has 360iResearch been around?
- What if I have a question about your reports?
- Can I share this report with my team?
- Can I use your research in my presentation?