Introduction to Glass Mat Reinforced Thermoplastics in Automotive Applications
Glass mat reinforced thermoplastics have emerged as a pivotal material innovation in automotive engineering, offering a balance of lightweight performance, design flexibility, and cost efficiency. By integrating random glass fiber mats into thermoplastic matrices, manufacturers achieve enhanced stiffness, impact resistance, and dimensional stability without the weight penalty associated with metal or traditional composites. This combination of properties supports rigorous safety standards, reduces fuel consumption through lighter vehicle mass, and streamlines production processes by leveraging thermoplastic recyclability and shorter cycle times.
In recent years, rapid advancements in fiber dispersion techniques, resin formulations, and molding processes have expanded the application scope of glass mat reinforced thermoplastics across both interior and exterior components. Stakeholders are now exploring these materials for structural elements, where traditionally only metals or continuous composites have dominated. Simultaneously, sustainability imperatives and circular economy goals are accelerating resin innovations, promoting bio‐based polymers and enhanced recyclability protocols. As the automotive industry transitions toward electrification and autonomous driving architectures, the demand for materials that deliver multifunctional performance and environmental credentials continues to intensify.
This executive summary distills the critical trends, regulatory influences, market segmentation insights, regional dynamics, and competitive landscape shaping the glass mat reinforced thermoplastics sector. It provides actionable guidance for decision-makers seeking to capitalize on transformative shifts and emerging opportunities in this evolving market.
Transformative Shifts Reshaping the Automotive Composite Landscape
Over the past five years, the glass mat reinforced thermoplastics landscape has undergone transformative shifts driven by material innovation, regulatory pressures, and evolving powertrain architectures. The surge in electric vehicle platforms has elevated the importance of weight reduction and thermal management, prompting extensive research into resin systems such as polyetheretherketone and polyamide that offer high temperature performance and dielectric stability.
Simultaneously, supply chain resilience has emerged as a strategic focus following raw material disruptions during the global pandemic. Manufacturers are diversifying resin sourcing, optimizing manufacturing footprints closer to end markets, and collaborating with resin and fiber suppliers to secure consistent quality and capacity. Meanwhile, automotive OEMs are increasingly adopting modular design principles, leveraging injection molding and compression molding techniques to integrate complex geometries and multifunctional elements in fewer build steps.
In parallel, sustainability mandates are reshaping value chains: recyclability targets and carbon footprint metrics now influence resin selection, process energy efficiency, and end-of-life management. Bio‐based polypropylene and polycarbonate blends are gaining traction as brands seek to align with stringent emission reduction goals. Together, these forces are redefining performance benchmarks, cost structures, and innovation pathways, presenting unprecedented opportunities for suppliers and OEMs poised to navigate this dynamic environment.
Assessing the Cumulative Impact of United States Tariffs in 2025
In 2025, the implementation of enhanced United States tariffs on imported glass fibers and certain thermoplastic resins has had a pronounced cumulative impact across the automotive supply chain. Tariff adjustments on fibers raised input costs by up to 10 percent, while duties on high-performance resins-particularly polyamide and polyetheretherketone grades-added an incremental 15 percent cost burden for key OEMs and tier suppliers.
These measures have prompted a reevaluation of sourcing strategies as companies seek to mitigate cost pressures. Several leading automakers have shifted production emphasis toward domestic fiber producers and resin compounds manufactured in North America. Concurrently, joint ventures and strategic partnerships between U.S. processors and foreign resin suppliers are accelerating to secure tariff-exempt supply routes through bonded warehouses and free trade zone operations.
On the manufacturing floor, suppliers are investing in process efficiencies-such as faster cycle injection molding machines and advanced fiber orientation controls-to offset raw material surcharges. Some component producers have begun localizing key feedstocks, including concentrated fiber mats, to buffer against future tariff volatility. Looking ahead, the tariff landscape is expected to remain a core consideration in market entry decisions, contract negotiations, and capital expenditure planning, reinforcing the need for agile supply chain architectures.
Key Segmentation Insights Across Material, Resin, Application, Process, End-User, and Functionality
A nuanced understanding of market segmentation reveals where glass mat reinforced thermoplastics create maximum value. Based on type, Continuous Fiber Reinforced Thermoplastics deliver superior mechanical performance for structural automotive parts, while Long Fiber Reinforced Thermoplastics offer a balance between strength and cost, and Short Fiber Reinforced Thermoplastics enable high-volume interior components with streamlined molding processes.
Resin type further delineates performance envelopes: Polyamide systems address under-the-hood durability and chemical resistance, Polycarbonate stands out for optical clarity and exterior trim applications, Polyetheretherketone serves demanding thermal and electrical insulation needs in next-generation EV battery housings, and Polypropylene acts as a cost-efficient, recyclable base for mass-market interior and exterior parts.
Application insights show that exterior components such as body panels, bumpers, and wheel covers benefit from dimensional stability and paint adherence, whereas interior parts like floors, instrument panels, and seat components leverage noise damping and aesthetic versatility. Structural parts integration, encompassing chassis components, front ends, and seat structures, exploits enhanced crash energy absorption and weight reduction.
Manufacturing process selection shapes production economics: Compression molding suits large, high-strength panels, injection molding excels at complex geometry for precision parts, and thermoforming addresses medium volume runs with moderate tooling commitments. End-user segmentation highlights divergent priorities: Commercial vehicle producers, split between heavy and light segments, demand extreme durability and load-bearing capacity, while passenger vehicle OEMs, including hatchbacks, sedans, and SUVs, prioritize fuel efficiency, cabin refinement, and sustainability messaging. Finally, functionality requirements across noise and vibration damping, structural reinforcement, and thermal insulation drive tailored material and process combinations to meet stringent automotive standards.
This comprehensive research report categorizes the Glass Mat Reinforced Thermoplastics for Automotive market into clearly defined segments, providing a detailed analysis of emerging trends and precise revenue forecasts to support strategic decision-making.
- Type
- Resin Type
- Application
- Manufacturing Process
- End-User
- Functionality
Regional Dynamics Driving Growth in the Glass Mat Reinforced Thermoplastics Market
Geographical dynamics are reshaping competitive positioning in the glass mat reinforced thermoplastics market. In the Americas, investment in lightweighting is propelled by stringent fuel economy regulations and the rapid ascent of EV production hubs in the United States and Mexico. Regional content requirements and domestic tariff policies are incentivizing local supply chain expansion and reshoring of critical fiber and resin manufacturing assets.
In Europe, Middle East & Africa, environmental directives such as the Euro 7 emission standards and the European Green Deal are accelerating adoption of recycled and bio-based polypropylene matrices. Automotive clusters in Germany, France, and Italy are spearheading pilot projects that integrate digital twin simulations and Industry 4.0 process controls to optimize fiber orientation and reduce scrap rates.
Across Asia-Pacific, growth is driven by expanding vehicle production in China, India, and Southeast Asia, where cost competitiveness and high-volume manufacturing favor long fiber reinforced systems in economy and mid-segment models. Meanwhile, Japan and South Korea supply advanced resin technologies and high-precision molding equipment, forming a hub for joint R&D initiatives focused on next-generation polymer composites. These regional dynamics reflect converging priorities: balancing cost, performance, and sustainability while responding to localized regulatory and consumer demands.
This comprehensive research report examines key regions that drive the evolution of the Glass Mat Reinforced Thermoplastics for Automotive market, offering deep insights into regional trends, growth factors, and industry developments that are influencing market performance.
- Americas
- Asia-Pacific
- Europe, Middle East & Africa
Leading Companies Shaping the Glass Mat Reinforced Thermoplastics Sector
Market leadership in glass mat reinforced thermoplastics is shared among global chemical majors, specialty composite processors, and automotive OEMs with in-house materials capabilities. BASF SE continues to expand its portfolio of engineered resins and coating solutions, while Borealis AG leverages its polyolefin expertise to develop high-recyclate content glass mat blends. Celanese Corporation is focusing on advanced thermoplastic formulations for EV battery enclosures, and DSM Engineering Materials targets structural reinforcement applications with high strength-to-weight composites.
DuPont de Nemours, Inc. and Solvay S.A. both intensify R&D investments in high-temperature polymers, whereas Groupe Renault is integrating glass mat reinforced parts in next-generation platform architectures to achieve up to 20 percent weight savings. Hanwha Solutions Corporation and LANXESS AG collaborate on bio-based resin systems, and LyondellBasell Industries N.V. drives circular economy initiatives through advanced recycling processes.
Mitsubishi Chemical Corporation and Teijin Limited supply premium fiber mats tailored for improved fiber distribution, while Toray Industries, Inc. and SGL Carbon SE push the boundaries of continuous fiber composites. Quadrant Plastics Composites and RTP Company excel in custom compound development, and Röchling Automotive and SABIC Innovative Plastics serve niche applications with specialized formulations. Victrex plc rounds out the competitive set with high-performance PEEK solutions for the most demanding automotive environments.
This comprehensive research report delivers an in-depth overview of the principal market players in the Glass Mat Reinforced Thermoplastics for Automotive market, evaluating their market share, strategic initiatives, and competitive positioning to illuminate the factors shaping the competitive landscape.
- BASF SE
- Borealis AG
- Celanese Corporation
- DSM Engineering Materials
- DuPont de Nemours, Inc.
- Groupe Renault
- Hanwha Solutions Corporation
- LANXESS AG
- LyondellBasell Industries N.V.
- Mitsubishi Chemical Corporation
- Quadrant Plastics Composites
- RTP Company
- Röchling Automotive
- SABIC
- SABIC Innovative Plastics
- SGL Carbon SE
- Solvay S.A.
- Teijin Limited
- Toray Industries, Inc.
- Victrex plc
Actionable Recommendations for Industry Leaders
To thrive in this rapidly evolving market, industry leaders should prioritize a dual focus on innovation and supply chain resilience. First, accelerating material development through strategic alliances with fiber and resin innovators will create tailored solutions that meet stringent performance and sustainability targets. Co-development programs for bio-based and high-recyclate content composites can differentiate product offerings and align with global decarbonization goals.
Second, optimizing manufacturing architectures by integrating advanced process controls-such as predictive maintenance, real-time fiber orientation monitoring, and energy recovery systems-will reduce cycle times, minimize waste, and lower total cost of ownership. Investing in flexible tooling platforms that support both injection molding and compression molding will enable rapid scaling across diverse vehicle programs.
Third, enhancing supply chain agility through multi-sourcing strategies and regional footprint rationalization will mitigate tariff risks and geopolitical uncertainties. Establishing bonded logistics hubs and leveraging free trade agreements can secure uninterrupted access to critical fibers and resins. Finally, embedding digital twin technologies and simulation tools into the design process will shorten development cycles and ensure component performance under real-world conditions.
Explore AI-driven insights for the Glass Mat Reinforced Thermoplastics for Automotive market with ResearchAI on our online platform, providing deeper, data-backed market analysis.
Ask ResearchAI anything
World's First Innovative Al for Market Research
Conclusion: Embracing Innovation and Sustainability
The glass mat reinforced thermoplastics market stands at the intersection of performance imperatives and sustainability mandates. By embracing advanced resin chemistries, process innovations, and collaborative supply chain models, stakeholders can unlock new avenues for lightweighting, cost reduction, and circularity. As EV adoption accelerates and regulatory frameworks tighten, the ability to deliver high‐temperature, high‐strength, and recyclable materials will determine competitive advantage.
Future success hinges on an integrated approach that aligns material science breakthroughs with digital manufacturing platforms and robust regional ecosystems. Companies that champion transparent lifecycle assessments and invest in closed‐loop recycling infrastructure will strengthen brand equity and meet escalating consumer expectations. Simultaneously, agile business models that balance regional optimization with global scale will enable rapid response to market shifts and tariff fluctuations.
In this dynamic landscape, continuous learning, cross‐sector partnerships, and data‐driven decision making will be essential. By fostering a culture of innovation and sustainability, industry participants can transform challenges into strategic growth opportunities and position glass mat reinforced thermoplastics at the forefront of the automotive materials revolution.
This section provides a structured overview of the report, outlining key chapters and topics covered for easy reference in our Glass Mat Reinforced Thermoplastics for Automotive market comprehensive research report.
- Preface
- Research Methodology
- Executive Summary
- Market Overview
- Market Dynamics
- Market Insights
- Cumulative Impact of United States Tariffs 2025
- Glass Mat Reinforced Thermoplastics for Automotive Market, by Type
- Glass Mat Reinforced Thermoplastics for Automotive Market, by Resin Type
- Glass Mat Reinforced Thermoplastics for Automotive Market, by Application
- Glass Mat Reinforced Thermoplastics for Automotive Market, by Manufacturing Process
- Glass Mat Reinforced Thermoplastics for Automotive Market, by End-User
- Glass Mat Reinforced Thermoplastics for Automotive Market, by Functionality
- Americas Glass Mat Reinforced Thermoplastics for Automotive Market
- Asia-Pacific Glass Mat Reinforced Thermoplastics for Automotive Market
- Europe, Middle East & Africa Glass Mat Reinforced Thermoplastics for Automotive Market
- Competitive Landscape
- ResearchAI
- ResearchStatistics
- ResearchContacts
- ResearchArticles
- Appendix
- List of Figures [Total: 28]
- List of Tables [Total: 505 ]
Next Steps: Secure Your Detailed Market Research Report
To gain comprehensive insights and detailed analysis on market drivers, regulatory impacts, and competitive strategies in the glass mat reinforced thermoplastics sector, contact Ketan Rohom (Associate Director, Sales & Marketing). Secure the full report to inform your decision-making and capitalize on emerging opportunities across this high-growth market segment.
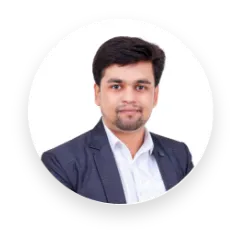
- When do I get the report?
- In what format does this report get delivered to me?
- How long has 360iResearch been around?
- What if I have a question about your reports?
- Can I share this report with my team?
- Can I use your research in my presentation?