Executive Overview of Green Silicon Carbide’s Role in Modern Grinding
Green silicon carbide has emerged as a cornerstone abrasive material, offering unmatched hardness and thermal conductivity that drive efficiency in high-precision grinding processes. Its unique microstructure delivers exceptional performance on both ferrous and non-ferrous substrates, making it an indispensable component in sectors ranging from automotive to semiconductors. By resisting fracturing under heavy load and maintaining sharp cutting edges longer than traditional abrasives, green silicon carbide optimizes throughput while reducing downtime associated with wheel dressing and replacement. Moreover, ongoing innovations in manufacturing processes have enhanced particle uniformity and enabled custom formulations that address specific application needs. As industry demands evolve toward finer finishes and tighter tolerances, green silicon carbide’s role is transitioning from a niche solution to a default choice for critical grinding tasks. This introduction sets the stage for a deep dive into the market forces, regulatory shifts, and strategic imperatives shaping its future.
Transformative Shifts Redefining the Abrasive Sector
The grinding landscape has undergone transformative shifts driven by rising quality standards, automation, and sustainability mandates. Advanced manufacturing technologies now require abrasives that deliver consistent performance across a spectrum of operating conditions. As CNC machining centers proliferate, users demand abrasives capable of supporting higher feed rates without sacrificing surface integrity. In parallel, electric vehicle and renewable energy components have triggered surge requirements for semiconductors and engineering ceramics, amplifying pressure on abrasive supply chains. Environmental regulations have further accelerated the transition to eco-friendlier processes, pressuring producers to adopt closed-loop recycling of spent wheels and less energy-intensive synthesis routes. Meanwhile, digitization initiatives are enabling real-time monitoring of abrasive wear, ushering in predictive maintenance models that optimize tool life. Taken together, these trends are redefining value propositions for abrasives, elevating the importance of materials that combine performance, adaptability, and environmental stewardship.
Cumulative Impact of United States Tariffs in 2025
The imposition of new United States tariffs in 2025 has significantly reshaped trade dynamics for green silicon carbide suppliers and end users. Import duties on raw material and finished abrasive imports have increased input costs, prompting domestic manufacturers to reevaluate sourcing strategies. While some players have absorbed these duties through efficiency gains in furnace or sublimation processes, others have redirected procurement toward non-tariffed markets in Asia-Pacific and Europe. The higher cost basis has accelerated investments in onshore production capacity, particularly for high-purity grades used in semiconductor polishing. At the same time, end users are optimizing inventory management and adopting just-in-time purchasing models to mitigate cash flow constraints. In response, suppliers are offering flexible contracting terms and value-added services such as in-house diagnostics to preserve customer loyalty. Collectively, these adjustments underscore how tariff policy can catalyze supply-chain diversification and spur innovation in production economics.
Comprehensive Segmentation Insights Across Multiple Dimensions
Segmentation analysis reveals nuanced opportunities and risk profiles across application, product type, end user, manufacturing process, grade, shape, density, size, and packaging. In terms of application, abrasive tools dominate demand, encompassing cutting tools, grinding wheels, polishing discs, and sandpaper, while engineering ceramics underpin foundry and wear parts manufacturing. Homemade use applications such as abrasion-resistant surfaces and kitchen knife sharpeners address niche consumer markets, whereas refractories include heating elements and kiln furniture. In the semiconductor sector, power semiconductors drive ultra-fine abrasive requirements. On the product type front, macrogrits spanning 120–150 and 180–220 grit sizes deliver robust material removal rates, while microgrits in the 36–120 grit ranges enable precision finishes. End users span aerospace components manufacturers and maintenance providers, automotive parts suppliers and carmakers, building materials and infrastructure developers, consumer and industrial electronics producers, as well as machinery builders and tool manufacturers. Manufacturing processes vary between closed and open furnace routes or sublimation techniques like nitrogen doping and physical vapor transport. Material grade distinctions between high-purity (99%) and medium-purity (95–97%) define critical performance thresholds. Shapes range from blocks to powders and slurries, densities segment into high and low categories, sizes into granules and particles, and packaging into bulk containers or small packs. This multi-dimensional segmentation framework equips stakeholders to tailor offerings precisely and capture growth pockets within each sub-segment.
This comprehensive research report categorizes the Green Silicon Carbide for Grinding market into clearly defined segments, providing a detailed analysis of emerging trends and precise revenue forecasts to support strategic decision-making.
- Application
- Product Type
- End User
- Manufacturing Process
- Grade
- Shape
- Density
- Size
- Packaging
Key Regional Dynamics Shaping Market Growth
Regionally, the Americas benefit from well-established supply chains and proximity to major aerospace and automotive hubs. Investment in local production is rising as tariff impacts spur onshore capacity expansion and reduce logistical complexities. Europe, Middle East & Africa leverage advanced manufacturing clusters, particularly in Germany and the UAE, driving demand for premium high-purity grades in semiconductor and engineering ceramics applications. Sustainability goals across EMEA are accelerating adoption of green manufacturing practices and regulatory compliance services. Asia-Pacific remains the largest consumption center, propelled by China’s growing infrastructure projects, Japan’s electronics sector, and India’s rapidly expanding industrial manufacturing base. Suppliers in APAC are scaling production of both macro- and microgrits, focusing on cost competitiveness while upgrading quality to meet global standards. Across all regions, collaborative partnerships between material producers and end users are forging integrated service models that deliver technical support, just-in-time delivery, and lifecycle management solutions.
This comprehensive research report examines key regions that drive the evolution of the Green Silicon Carbide for Grinding market, offering deep insights into regional trends, growth factors, and industry developments that are influencing market performance.
- Americas
- Asia-Pacific
- Europe, Middle East & Africa
Competitive Landscape and Leading Company Strategies
Leading firms are intensifying efforts to differentiate through proprietary process technologies, customer co-development initiatives, and expanded service portfolios. Established conglomerates 3M Company and Saint-Gobain S.A. continue to leverage their scale and R&D capabilities to introduce customized abrasive composites. Cumi Murugappa Group and VSM Abrasives Corporation are enhancing furnace process efficiencies to reduce per-unit energy consumption, while ESK-SIC GmbH and Fujimi Incorporated focus on ultra-high-purity grades tailored for next-generation semiconductors. Smaller specialized players such as Electro Abrasives, LLC and Washington Mills Electro Minerals Corp. are carving niches in slurries and microgrit applications. Fiven ASA and Henan Si&C Co., Ltd. are expanding into Asia-Pacific through joint ventures and technology licensing, and Toshiba Corporation is exploring in-house grinding solutions for its electronics division. Meanwhile, Imerys Fused Minerals, K.C. Abrasive Company LLC, Norton Abrasives, Tyrolit Group, and other regionally strong entities are forging strategic partnerships to deliver end-to-end abrasive ecosystem services, from material selection to post-process waste recycling.
This comprehensive research report delivers an in-depth overview of the principal market players in the Green Silicon Carbide for Grinding market, evaluating their market share, strategic initiatives, and competitive positioning to illuminate the factors shaping the competitive landscape.
- 3M Company
- Cumi Murugappa Group
- Electro Abrasives, LLC
- ESK-SIC GmbH
- Fiven ASA
- Fujimi Incorporated
- Henan Si&C Co., Ltd.
- Imerys Fused Minerals
- K.C. Abrasive Company LLC
- Norton Abrasives (a brand of Saint-Gobain),
- Saint-Gobain S.A.
- Toshiba Corporation
- Tyrolit Group
- VSM Abrasives Corporation
- Washington Mills Electro Minerals Corp.
Actionable Recommendations for Industry Leaders
Industry leaders should align their strategies with evolving market dynamics by focusing on three key imperatives. First, invest in advanced manufacturing platforms that support process diversification, enabling seamless switching between furnace and sublimation methods to optimize cost and quality under shifting regulatory environments. Second, deepen customer engagement through integrated digital services that monitor tool health and predict maintenance needs, transforming transactional relationships into long-term partnerships. Third, pursue regional diversification by balancing capacity expansion in high-growth Asia-Pacific markets with resilient onshore operations in the Americas and EMEA to mitigate tariff and logistics risks. Supplements to these core strategies include forging alliances for sustainable material recycling, adopting high-density and specialized packaging solutions to reduce waste, and co-developing tailored abrasive forms-such as microgrit powders and slurry systems-for cutting-edge semiconductor and aerospace applications.
Explore AI-driven insights for the Green Silicon Carbide for Grinding market with ResearchAI on our online platform, providing deeper, data-backed market analysis.
Ask ResearchAI anything
World's First Innovative Al for Market Research
Conclusion: Navigating the Future of Abrasive Excellence
Green silicon carbide’s trajectory is defined by its ability to meet increasingly stringent performance and sustainability criteria. As tariffs and regional dynamics reshape supply chains, material innovators and end users must embrace adaptable manufacturing, deeper digital integration, and collaborative development models. Segmentation insights highlight white spaces in niche applications such as kitchen knife sharpeners and refractory kiln furniture, while macro- and microgrit product extensions open doors to precision polishing and heavy-duty stock removal alike. Regional analysis underscores the importance of a balanced global footprint, with Asia-Pacific’s scale, EMEA’s premium markets, and the Americas’ logistical advantages each playing critical roles. Competitive pressures will intensify, favoring entrants and incumbents that can leverage process know-how, technical support, and sustainability credentials. By acting on these insights, stakeholders can secure long-term value creation and maintain a competitive edge in a rapidly evolving terrain.
This section provides a structured overview of the report, outlining key chapters and topics covered for easy reference in our Green Silicon Carbide for Grinding market comprehensive research report.
- Preface
- Research Methodology
- Executive Summary
- Market Overview
- Market Dynamics
- Market Insights
- Cumulative Impact of United States Tariffs 2025
- Green Silicon Carbide for Grinding Market, by Application
- Green Silicon Carbide for Grinding Market, by Product Type
- Green Silicon Carbide for Grinding Market, by End User
- Green Silicon Carbide for Grinding Market, by Manufacturing Process
- Green Silicon Carbide for Grinding Market, by Grade
- Green Silicon Carbide for Grinding Market, by Shape
- Green Silicon Carbide for Grinding Market, by Density
- Green Silicon Carbide for Grinding Market, by Size
- Green Silicon Carbide for Grinding Market, by Packaging
- Americas Green Silicon Carbide for Grinding Market
- Asia-Pacific Green Silicon Carbide for Grinding Market
- Europe, Middle East & Africa Green Silicon Carbide for Grinding Market
- Competitive Landscape
- ResearchAI
- ResearchStatistics
- ResearchContacts
- ResearchArticles
- Appendix
- List of Figures [Total: 34]
- List of Tables [Total: 1119 ]
Take Action: Engage with Our Sales & Marketing Lead to Access the Full Report
To explore comprehensive data, strategic analysis, and tailored recommendations for leveraging green silicon carbide’s potential, connect directly with Ketan Rohom, Associate Director, Sales & Marketing. Secure your advanced insights and actionable roadmap by requesting the full market research report today.
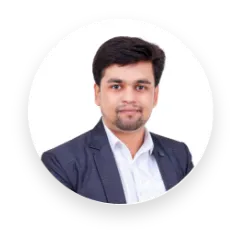
- When do I get the report?
- In what format does this report get delivered to me?
- How long has 360iResearch been around?
- What if I have a question about your reports?
- Can I share this report with my team?
- Can I use your research in my presentation?