Introduction: Establishing the Context of Grinding Media in Mining
Grinding media comprises metallic or ceramic objects used in mills to grind ore and other materials for critical mineral extraction. These components represent a substantial share of overall milling costs, driving ongoing advancements in material engineering, design and manufacturing processes. Over the past decade, high‐chrome cast steel formulations have delivered enhanced wear resistance, while zirconia‐based ceramic beads have provided exceptional hardness and reduced contamination. Concurrently, sustainability imperatives and rising energy costs have steered the industry toward total cost of ownership models and life‐cycle analyses. Moreover, digital integration-such as real‐time wear monitoring and predictive maintenance algorithms-has begun to redefine performance benchmarks and operational reliability. This executive summary synthesizes the transformative shifts underway, examines the cascading effects of recent United States tariffs, and delivers granular insights across material type, shape, application and production technology segments. It further explores regional demand dynamics and profiles leading manufacturers, offering actionable recommendations to optimize supply chains, mitigate risk and capture untapped value. By drawing these threads together, decision-makers will gain a clear line of sight into the evolving grinding media landscape, empowering them to drive efficiency, reduce downtime and enhance overall profitability.
Transformative Shifts Reshaping the Grinding Media Ecosystem
The grinding media ecosystem is undergoing a wave of innovation shaped by material advancements, digital transformation and sustainability mandates. First, material science breakthroughs are expanding the palette of options beyond traditional high‐chrome steel. Alumina and zirconia ceramics now offer ultra‐low wear rates for specialized applications, while forged alloy and carbon steels provide a balance of toughness and cost efficiency. In parallel, the integration of sensors and Internet of Things platforms enables real‐time monitoring of media wear, mill vibration and process variables, allowing maintenance teams to transition from reactive to predictive strategies. Furthermore, remote monitoring tools and advanced analytics are accelerating decision cycles, optimizing media replacement schedules and improving throughput consistency. Sustainability considerations are also reshaping procurement criteria: recycling programs for spent media, lower‐energy production methods and closed‐loop supply chains are becoming industry imperatives. As ore grades decline in many legacy operations, the need for more efficient grinding media has intensified, driving investment in high‐performance formulations. Together, these transformative shifts are redefining the competitive landscape, compelling manufacturers and end users alike to adopt more agile, data-driven and environmentally responsible approaches to stay ahead in a rapidly evolving market.
Cumulative Impact of United States Tariffs in 2025
The United States’ imposition of additional tariffs on imported steel and ceramic grinding media in 2025 has introduced new complexity to global supply chains and cost structures. Manufacturers that previously relied on competitively priced imports now face duty surcharges of up to 25 percent, elevating landed costs and squeezing margins. As a result, domestic steel‐based producers have gained a strategic edge, attracting demand from mills seeking to avoid tariff penalties and inventory disruptions. Conversely, suppliers outside North America are exploring alternative distribution channels and local partnerships to circumvent the duties, increasing regional competitiveness and supply diversity. In addition, buyers are reevaluating procurement strategies, shifting from just‐in-time purchasing to forward contracting and safety‐stock buildup to mitigate price volatility. This tariff environment also underscores the importance of production technology: casting operations in duty‐free jurisdictions have become more attractive, while closed‐die forging operations in tariff‐exposed regions are reevaluating their cost models. Ultimately, the cumulative impact of these measures extends beyond immediate price hikes, influencing long-term investment decisions, encouraging nearshoring of critical manufacturing assets and accelerating the adoption of cost-efficient, low‐tariff material alternatives.
Key Segmentation Insights Across Material, Shape, Application, End-User and Production Technology
A detailed examination of market segments reveals nuanced performance patterns and evolving preferences. Based on material type, cast steel remains the volume leader, with high‐chrome grades preferred for their superior abrasion resistance and low‐chrome grades chosen for cost‐sensitive applications. The ceramic segment, particularly alumina products, is gaining traction where contamination control is critical, while zirconia beads are carving out specialized niches in fine mineral processing. Forged steel variants balance toughness and wear life, with alloy formulations serving heavy‐duty grinding and carbon steel catering to general‐purpose milling. In terms of shape, cylindrical forms-both cylpebs and rods-dominate applications requiring targeted grinding action, whereas irregular segments excel in crushing media applications and mill lining wear replacement. Spherical media, whether ceramic balls or traditional steel balls, continue to underpin fine and ultra‐fine grinding circuits due to their uniform contact mechanics. Application-driven demand varies significantly: open-pit chrome ore operations drive high‐chrome cast steel usage, strip‐mined copper projects prioritize durable forged steel, hydraulic gold mining favors abrasion‐resistant ceramics and underground iron ore extraction relies on a blend of spherical and irregular steel media. End‐user industries further influence purchase decisions; for example, the paints and coatings sector in the chemical industry selects alumina-based beads to minimize contamination, while aggregate producers in construction opt for cost-effective forged steel. Base and precious metal mining both push for premium wear media to handle increasingly hard ores, and thermal power plants demand high-capacity media to support ash processing and boiler feed applications. Finally, production technology diverges into sand casting for complex geometries and closed‐die forging for high-strength profiles, each offering distinct advantages in terms of mechanical properties and unit economics.
This comprehensive research report categorizes the Grinding Media for Mining market into clearly defined segments, providing a detailed analysis of emerging trends and precise revenue forecasts to support strategic decision-making.
- Material Type
- Shape
- Application
- End-User Industry
- Production Technology
Regional Dynamics and Opportunities in Key Markets
Regional dynamics shape both demand profiles and competitive positioning. In the Americas, a robust mining sector-particularly in North America and Brazil-fuels steady consumption of steel‐based grinding media, and domestic producers capitalize on reduced logistical lead times. Rigorous environmental regulations in Canada and the United States also favor recycled and energy-efficient media production. Europe, Middle East & Africa present a diverse tapestry of end‐user requirements: European steel mills and mining operations lean toward high‐performance ceramic and high‐chrome steel, while Middle East construction booms drive demand for cost-effective forged shapes. African projects, ranging from gold extraction in South Africa to phosphate processing in North Africa, create pockets of specialized media requirements. Meanwhile, Asia-Pacific stands as the largest regional market, led by China and India, where rapid mining expansion and infrastructure investments underpin insatiable demand for both steel and ceramic grinding media. In this region, local manufacturers scale up sand casting and closed‐die forging capacities to meet surging requirements, while multinational players forge joint ventures and technology licensing agreements to gain market share. Across all regions, digital supply chain platforms and aftermarket services are emerging as key differentiators, enabling faster order fulfillment and predictive maintenance support.
This comprehensive research report examines key regions that drive the evolution of the Grinding Media for Mining market, offering deep insights into regional trends, growth factors, and industry developments that are influencing market performance.
- Americas
- Asia-Pacific
- Europe, Middle East & Africa
Competitive Landscape: Top Players Driving Innovation and Growth
A competitive landscape populated by diversified technology leaders and regional specialists is driving continuous innovation. AIA Engineering Ltd. and Molycop maintain dominance in high‐chrome steel production, leveraging expansive global footprints to supply major mining conglomerates. Donhad Pty Ltd and Sino Grinding International Pty Ltd have solidified their positions in spherical steel ball manufacturing, focusing on cost efficiency and rapid delivery to regional mills. European firms such as Magotteaux SA, ME Elecmetal and Metso Outotec lead in proprietary ceramic formulations and integrated mill optimization services. In South America, Sigdo Koppers S.A. – SK Sabo and Gerdau Group capitalize on local ore processing projects, offering turnkey grinding media solutions. Asian suppliers-including Fengxing Wear Resistant Material Co., Ltd., Ningguo Nanfang Wear-Resistant Materials Co., Qingzhou Huahong Grinding Ball Co., Shandong Huamin Steel Ball Joint-stock Co. and Toyo Grinding Ball Co., Ltd.-compete on both price and product breadth, pushing the envelope in alloy design and production automation. Union Process Inc. distinguishes itself with laboratory milling equipment and custom media development, serving niche applications in mineral research and specialty chemicals. Collectively, these companies emphasize R&D investment, digital monitoring platforms and circular economy initiatives to strengthen their value propositions and capture incremental market share in a highly fragmented industry.
This comprehensive research report delivers an in-depth overview of the principal market players in the Grinding Media for Mining market, evaluating their market share, strategic initiatives, and competitive positioning to illuminate the factors shaping the competitive landscape.
- AIA Engineering Ltd.
- Donhad Pty Ltd
- Fengxing Wear Resistant Material Co., Ltd.
- Gerdau Group
- Magotteaux SA
- ME Elecmetal
- Metso Outotec
- Molycop
- Ningguo Nanfang Wear-Resistant Materials Co., Ltd
- Qingzhou Huahong Grinding Ball Co., Ltd.
- Shandong Huamin Steel Ball Joint-stock Co., Ltd
- Sigdo Koppers S.A. – SK Sabo
- Sino Grinding International Pty Ltd
- Toyo Grinding Ball Co., Ltd.
- Union Process Inc.
Actionable Recommendations for Industry Leaders
Industry leaders should adopt a multi-pronged strategy to thrive amid evolving market conditions. First, diversify material portfolios by expanding research into advanced ceramics and specialty steel alloys, ensuring product lines align with the rising demand for low-wear, high-hardness media. Second, integrate digital wear-monitoring sensors and predictive analytics into standard product offerings, delivering value-added services that reduce downtime and optimize replacement cycles for end users. Third, strategically localize production assets in tariff-exposed regions or form partnerships to mitigate the impact of trade barriers and limit logistical bottlenecks. Fourth, develop closed-loop recycling programs that reclaim spent media, reduce raw material consumption and appeal to customers pursuing sustainability goals. Fifth, leverage modular casting and forging capacities to scale rapidly in high-growth markets, maintaining flexibility to shift production based on geographies and ore type. Sixth, enhance aftermarket capabilities by providing technical training, application audits and performance guarantees, thereby deepening customer relationships and creating recurring revenue streams. By executing these initiatives, manufacturers and mining operators can secure competitive advantage, drive operational efficiency and cushion their businesses against regulatory and market uncertainties.
Explore AI-driven insights for the Grinding Media for Mining market with ResearchAI on our online platform, providing deeper, data-backed market analysis.
Ask ResearchAI anything
World's First Innovative Al for Market Research
Conclusion: Reinforcing Strategic Priorities for Sustainable Growth
The grinding media market stands at a pivotal juncture, shaped by material innovations, digital transformation and geopolitical forces. Emerging tariffs have reconfigured cost structures and supply chains, catalyzing domestic production in key regions while pressuring import-reliant operations to adapt. Technological evolution-from high‐performance ceramics to sensor‐enabled wear monitoring-continues to raise performance benchmarks and unlock new efficiency gains. Regionally, demand patterns vary widely across the Americas, EMEA and Asia-Pacific, underscoring the importance of localized strategies and flexible manufacturing footprints. Against this backdrop, the major players profiled herein are investing aggressively in R&D, service models and circular economy initiatives to capture growth and mitigate risk. For decision-makers, the path forward hinges on balanced portfolios, integrated digital solutions, agile supply chains and sustainable practices. By aligning investments with these strategic priorities, industry stakeholders can navigate volatility, meet evolving customer expectations and secure long‐term profitability in an increasingly competitive grinding media ecosystem.
This section provides a structured overview of the report, outlining key chapters and topics covered for easy reference in our Grinding Media for Mining market comprehensive research report.
- Preface
- Research Methodology
- Executive Summary
- Market Overview
- Market Dynamics
- Market Insights
- Cumulative Impact of United States Tariffs 2025
- Grinding Media for Mining Market, by Material Type
- Grinding Media for Mining Market, by Shape
- Grinding Media for Mining Market, by Application
- Grinding Media for Mining Market, by End-User Industry
- Grinding Media for Mining Market, by Production Technology
- Americas Grinding Media for Mining Market
- Asia-Pacific Grinding Media for Mining Market
- Europe, Middle East & Africa Grinding Media for Mining Market
- Competitive Landscape
- ResearchAI
- ResearchStatistics
- ResearchContacts
- ResearchArticles
- Appendix
- List of Figures [Total: 26]
- List of Tables [Total: 931 ]
Next Steps: Engage with Ketan Rohom to Access the Full Report
To unlock the full depth of analysis, detailed data and proprietary insights presented in this executive summary, reach out to Ketan Rohom, Associate Director, Sales & Marketing. His expertise will guide you through report features, customization options and licensing terms, ensuring you access the precise market intelligence needed to inform your strategic decisions. Engage now to secure your copy of the comprehensive research report and position your organization for success in the dynamic grinding media landscape.
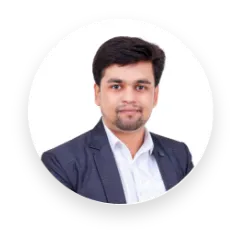
- When do I get the report?
- In what format does this report get delivered to me?
- How long has 360iResearch been around?
- What if I have a question about your reports?
- Can I share this report with my team?
- Can I use your research in my presentation?