Introduction to High-Density Interconnect PCBs in Aerospace & Defense
The aerospace and defense sector demands relentless innovation in electronic interconnects to achieve greater reliability, performance, and miniaturization. High-Density Interconnect (HDI) printed circuit boards have emerged as a cornerstone technology, enabling advanced avionics, satellite communications, radar systems, and secure military platforms. As mission profiles grow more complex and electromagnetic environments become more challenging, HDI PCBs deliver the signal integrity, thermal management, and mechanical robustness required to sustain critical operations. This executive summary explores the driving forces behind HDI adoption, highlights transformative shifts reshaping the landscape, and offers in-depth insights into segmentation, regional dynamics, and competitive positioning. Leaders and decision-makers will find actionable guidance to navigate tariff impacts, optimize supply chains, and leverage cutting-edge materials and processes. By understanding emerging trends, regulatory pressures, and technology trajectories, organizations can confidently align their product roadmaps, forge strategic partnerships, and sustain a competitive edge in the high-stakes arena of aerospace and defense electronics.
Transformative Shifts Redefining HDI PCB Development
The HDI PCB landscape is undergoing seismic shifts driven by miniaturization imperatives, the push for higher signal densities, and the proliferation of digital payloads. Advances in additive and semi-additive manufacturing processes now enable finer line widths and lower via aspect ratios, obviating traditional subtractive constraints and accelerating design cycles. Simultaneously, materials innovations such as ceramic and glass-fiber reinforced substrates deliver superior thermal conductivity and dielectric stability at high frequencies. Regulatory changes around export controls and cybersecurity have redirected development toward domestically sourced components and trusted foundries, fostering resilience amid global supply chain disruptions. Moreover, the rise of composite architectures-combining flexible PCBs with rigid-flex layers-facilitates three-dimensional routing and shock-resistant assemblies for unmanned aerial vehicles, hypersonic platforms, and next-generation radar. These transformative dynamics underscore the criticality of integrated design-to-manufacture frameworks, collaborative ecosystems, and continuous process optimization to meet evolving defense and aerospace requirements.
Assessing the Cumulative Impact of U.S. Tariffs Through 2025
The implementation of cumulative U.S. tariffs through 2025 has materially influenced cost structures and sourcing strategies across the HDI PCB value chain. While levies on imported laminates and copper foils increased procurement costs, they simultaneously incentivized near-shoring of key manufacturing steps and greater vertical integration among domestic suppliers. As a result, several electronics fabricators have diversified their supplier base, adopting dual-sourcing models that blend Tier 1 domestic capacity with selected Asia-Pacific partnerships optimized for advanced process nodes. This tariff environment accelerated investments in additive and semi-additive processes to reduce material waste and offset duty impacts. In parallel, companies expanded inventory buffers and instituted dynamic pricing mechanisms to maintain margin stability. Although duties introduced near-term inflationary pressures, they also catalyzed improved supply chain visibility, risk management frameworks, and long-term capital commitments toward localized HDI PCB production.
Key Segmentation Insights Across Material, Process, and Application
A granular segmentation analysis reveals distinct performance drivers and technology priorities across multiple dimensions. Based on material type, flexible PCBs-encompassing single layer, double layer, multi layer, and unimount constructions-dominate applications requiring conformable interconnects, while rigid-flex PCBs integrate high frequency, multi layer, and single layer variants for hybrid avionics modules. Hard PCBs, differentiated into single and multi layer forms, remain integral to robust control systems. When evaluating component density, the advanced high density segment emphasizes sub-millimeter microvias for next-generation phased-array radars, whereas standard density solutions persist in legacy communications equipment and ultra high density layouts support satellite payload miniaturization. The manufacturing process spectrum spans cluster deposition and laser patterning within additive processes, microwave hybrid circuits and non-conductive thermal heat dissipation in semi-additive workflows, as well as chemical milling and etching in subtractive approaches, each offering trade-offs in throughput and precision. End use applications branch into communication systems-with distinct requirements for commercial aviation links and secure military networks-navigation systems ranging from space-based platforms to tactical guidance units, and radar systems including airborne and shipboard variants. Technology node preferences split between CMOS at 14nm and below or 28nm and above, and GaAs architectures featuring chipsets and monolithic microwave integrated circuits. Substrate materials differentiate ceramic PCBs-utilizing aluminum nitride or beryllium oxide for high thermal dissipation-from glass-fiber reinforced PCBs in both flame retardant and non-flame retardant formulations. Signal layer configurations vary from single signal paths to dual and multi-signal arrangements, while component mount types traverse surface-mount and through-hole technologies to address mechanical and reparability considerations.
This comprehensive research report categorizes the HDI PCB for Aerospace & Defense market into clearly defined segments, providing a detailed analysis of emerging trends and precise revenue forecasts to support strategic decision-making.
- Material Type
- Component Density
- Manufacturing Process
- End Use Application
- Technology Node
- Substrate Material
- Signal Layer
- Component Mount Type
Key Regional Insights Shaping HDI PCB Markets
Regional dynamics underscore varied growth trajectories and strategic imperatives. In the Americas, defense modernization programs and commercial aerospace expansions drive sustained demand for high-reliability HDI PCBs, prompting investments in localized manufacturing clusters and digital quality assurance systems. In Europe, the Middle East & Africa, stringent regulatory frameworks around export licensing and environmental compliance coexist with major radar and satellite projects, encouraging collaborative R&D consortia among OEMs and tier-one suppliers. Asia-Pacific remains the largest production hub, leveraging high-volume capacity in China, Taiwan, and South Korea for both cost-effective standard density boards and premium advanced high density solutions. However, escalating labor costs and geopolitical considerations have spurred regional governments to incentivize domestic innovation, advanced materials development, and workforce upskilling to balance export-oriented growth with sovereign supply chain resilience.
This comprehensive research report examines key regions that drive the evolution of the HDI PCB for Aerospace & Defense market, offering deep insights into regional trends, growth factors, and industry developments that are influencing market performance.
- Americas
- Asia-Pacific
- Europe, Middle East & Africa
Key Company Insights and Strategic Positioning
Competitive landscapes reveal diversified strategies among leading HDI PCB fabricators. Advanced Circuits, Inc. focuses on rapid prototyping and agile turnaround times to serve design validation cycles. AT&S Austria Technologie & Systemtechnik Aktiengesellschaft leverages deep expertise in high-end HDI substrates and rigid-flex integration for premium aerospace platforms. Compeq Manufacturing Co., Ltd. and Meiko Electronics Co., Ltd. emphasize broad in-house capacity and vertical integration to manage cost volatility. HannStar Board Corporation and Shennan Circuits Co., Ltd. (SCC) have prioritized additive process capabilities to achieve finer trace resolution. Multek, a subsidiary of Flex Ltd., and TTM Technologies, Inc. maintain global footprints offering end-to-end assembly services. Nanya PCB Corp. and Nippon Mektron, Ltd. deliver specialized materials development in ceramic substrates. Samsung Electro-Mechanics Co., Ltd. and Shenzhen Kinwong Electronic Co., Ltd. focus on ultra high density and next-generation CMOS process nodes. Tripod Technology Corporation, Unimicron Technology Corp., and Zhen Ding Technology Holding Limited advance their competitive positioning through strategic partnerships and targeted capital investments in advanced thermal management and signal-integrity solutions.
This comprehensive research report delivers an in-depth overview of the principal market players in the HDI PCB for Aerospace & Defense market, evaluating their market share, strategic initiatives, and competitive positioning to illuminate the factors shaping the competitive landscape.
- Advanced Circuits, Inc.
- AT&S Austria Technologie & Systemtechnik Aktiengesellschaft
- Compeq Manufacturing Co., Ltd.
- HannStar Board Corporation
- Meiko Electronics Co., Ltd.
- Multek, a subsidiary of Flex Ltd.
- Nanya PCB Corp.
- Nippon Mektron, Ltd.
- Samsung Electro-Mechanics Co., Ltd.
- Shennan Circuits Co., Ltd. (SCC)
- Shenzhen Kinwong Electronic Co., Ltd.
- Tripod Technology Corporation
- TTM Technologies, Inc.
- Unimicron Technology Corp.
- Zhen Ding Technology Holding Limited
Actionable Recommendations for Industry Leaders
Industry leaders should bolster resilience by diversifying their material supply base and incorporating advanced thermal substrates such as aluminum nitride ceramics alongside next-generation glass-fiber composites. Investing in additive and semi-additive manufacturing capabilities will yield finer feature sizes, reduce material waste, and shorten prototyping cycles. Collaborative engagement with defense primes, avionics integrators, and regulatory bodies can accelerate standards development for high-frequency interconnects and ensure compliance with evolving export and cybersecurity mandates. Companies should also adopt data-driven quality assurance platforms and real-time supply chain visibility tools to mitigate tariff impacts and inventory disruptions. Finally, forging cross-sector alliances with chipmakers and system integrators will unlock opportunities for co-optimized design frameworks, accelerating the adoption of HDI solutions in next-generation satellite, radar, and unmanned systems.
Explore AI-driven insights for the HDI PCB for Aerospace & Defense market with ResearchAI on our online platform, providing deeper, data-backed market analysis.
Ask ResearchAI anything
World's First Innovative Al for Market Research
Conclusion: Navigating the Future of HDI PCBs in Aerospace & Defense
High-density interconnect PCBs stand at the forefront of aerospace and defense electronics innovation, delivering the miniaturization, signal integrity, and thermal performance that underpin advanced systems. Transformative shifts in manufacturing processes, materials science, and regulatory environments are reshaping competitive dynamics. A comprehensive segmentation analysis has illuminated specific growth pathways across material types, density classes, process technologies, and end-use applications. Regional insights reveal the strategic imperatives in the Americas, Europe, Middle East & Africa, and Asia-Pacific markets, while leading companies showcase diverse approaches to capacity, materials development, and process optimization. By embracing actionable recommendations-from diversifying supply chains to advancing additive processes-organizations can navigate tariff headwinds, regulatory complexities, and technology transitions with confidence. The insights presented here equip decision-makers with a robust framework to align investments, partnerships, and innovation roadmaps for sustained leadership in the high-stakes realm of aerospace and defense electronics.
This section provides a structured overview of the report, outlining key chapters and topics covered for easy reference in our HDI PCB for Aerospace & Defense market comprehensive research report.
- Preface
- Research Methodology
- Executive Summary
- Market Overview
- Market Dynamics
- Market Insights
- Cumulative Impact of United States Tariffs 2025
- HDI PCB for Aerospace & Defense Market, by Material Type
- HDI PCB for Aerospace & Defense Market, by Component Density
- HDI PCB for Aerospace & Defense Market, by Manufacturing Process
- HDI PCB for Aerospace & Defense Market, by End Use Application
- HDI PCB for Aerospace & Defense Market, by Technology Node
- HDI PCB for Aerospace & Defense Market, by Substrate Material
- HDI PCB for Aerospace & Defense Market, by Signal Layer
- HDI PCB for Aerospace & Defense Market, by Component Mount Type
- Americas HDI PCB for Aerospace & Defense Market
- Asia-Pacific HDI PCB for Aerospace & Defense Market
- Europe, Middle East & Africa HDI PCB for Aerospace & Defense Market
- Competitive Landscape
- ResearchAI
- ResearchStatistics
- ResearchContacts
- ResearchArticles
- Appendix
- List of Figures [Total: 32]
- List of Tables [Total: 943 ]
Call-To-Action: Connect with Ketan Rohom for the Full HDI PCB Market Research Report
To explore these insights in greater depth and secure a competitive advantage, contact Ketan Rohom, Associate Director, Sales & Marketing, for access to the full market research report. This comprehensive analysis offers detailed data, expert forecasts, and strategic guidance tailored to the needs of aerospace and defense stakeholders seeking to capitalize on the latest HDI PCB trends and opportunities.
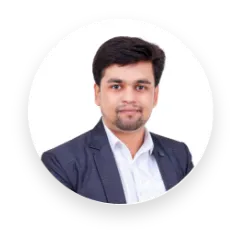
- When do I get the report?
- In what format does this report get delivered to me?
- How long has 360iResearch been around?
- What if I have a question about your reports?
- Can I share this report with my team?
- Can I use your research in my presentation?