Unraveling the Significance and Performance Advantages of Gas-Filled Shock Absorbers in Heavy Vehicle Operations Under Emerging Industry Demands and Expectations
The performance and durability of heavy vehicles hinge upon the precision and resilience of their shock absorption systems. Gas-filled shock absorbers have emerged as a critical component for buses, trailers, and a wide range of trucks, delivering enhanced ride comfort, improved handling under heavy loads, and reduced maintenance costs over the vehicle lifecycle. As fleet operators seek to balance total cost of ownership with stringent safety and emissions standards, gas-filled technology offers a compelling solution, leveraging pressurized gas chambers to maintain consistent damping characteristics under fluctuating operational stresses.
In recent years, advances in materials science, valve design, and manufacturing processes have propelled gas-filled absorbers into the spotlight, enabling more responsive suspension tuning and greater adaptability across diverse vehicle types. At the same time, industry stakeholders including OEMs, aftermarket suppliers, and regulatory bodies are collaborating to set performance benchmarks, driving standardization of testing protocols and certification schemes. This alignment underscores the market’s maturation, as technology providers shift from offering commodity dampers toward comprehensive ride-control systems that integrate gas-filled struts with electronic sensors and predictive maintenance capabilities.
Looking ahead, the convergence of digitalization, sustainability goals, and evolving end-user requirements will shape the trajectory of shock absorber innovation. Understanding the underlying mechanical principles, key performance differentiators, and broader operational benefits of gas-filled designs lays the groundwork for informed strategic decisions across product development, procurement, and fleet optimization.
Analyzing the Transformational Shifts Reshaping Heavy Vehicle Shock Absorber Technologies Driven by Digital Integration Sustainability and Regulatory Pressure
The landscape of heavy vehicle suspension technology is undergoing a profound transformation, driven by the intersection of digital integration, environmental mandates, and heightened focus on lifecycle costs. Traditional hydraulic dampers are increasingly complemented-or replaced-by gas-filled variants that deliver greater damping stability under high payloads. However, their refinement is only part of the story. Industry leaders are now embedding sensors, leveraging real-time telematics, and employing advanced analytics to achieve predictive maintenance, reducing downtime and optimizing vehicle uptime.
Simultaneously, stringent emissions regulations and sustainability targets are compelling materials and component manufacturers to reduce their carbon footprint through the adoption of lightweight alloys, recycled composites, and lower-energy production methods. These shifts are leading to a new generation of gas-filled shock absorbers that not only improve vehicle performance but also align with corporate environmental, social, and governance (ESG) objectives. Consequently, OEMs and aftermarket providers are partnering with tier-one suppliers to co-innovate on high-strength, low-mass damper architectures that support electrified powertrains and alternative fuels.
Furthermore, the globalization of supply chains has precipitated an increased emphasis on regional manufacturing hubs, near-shoring strategies, and diversified supplier bases to mitigate the risk of disruption. As a result, market participants are reevaluating sourcing strategies for high-precision components, including gas seals and nitrogen-charging units, to maintain service continuity in the face of logistical challenges and geopolitical uncertainties.
Examining How United States Section 232 Tariffs Imposed in 2025 Are Redefining Sourcing Strategies and Supply Chain Dynamics for Gas-Filled Shock Absorbers
The introduction of new tariffs on automotive components has added complexity to procurement and pricing strategies for gas-filled shock absorbers. In early 2025, the United States significantly increased duties on imported suspension parts under Section 232, citing both national security considerations and the need to bolster domestic manufacturing. These measures, applying up to 25 percent tariff rates on select gas-filled shock absorber assemblies and subcomponents, have prompted manufacturers to reassess their global sourcing footprints.
To mitigate cost escalation, major suppliers have accelerated localization efforts, expanding capacity at U.S.-based plants while entering into joint ventures with domestic partners. This strategic pivot addresses tariff pressures but also aligns with the broader trend toward reshoring advanced manufacturing capabilities. Meanwhile, aftermarket distributors are recalibrating inventory strategies to absorb tariff volatility, incorporating dynamic pricing models and multi-tiered stocking approaches.
The cumulative impact of these tariffs extends beyond direct cost increases. Supply chain delays have intensified as importers navigate complex customs procedures and compliance requirements. Consequently, lead times for gas-filled shock absorbers have grown, incentivizing end users to explore total solution providers that offer integrated maintenance packages and performance guarantees. As tariff scenarios remain fluid, agility in procurement and adaptive contract structures will be critical for manufacturers and fleet operators alike.
Highlighting Critical Segmentation Criteria That Define Performance Requirements and Competitive Dynamics Across Gas-Filled Shock Absorber Market Subsegments
Gas-filled shock absorber manufacturers segment their offerings by vehicle type, tailoring damper characteristics to the unique demands of buses, trailers, and trucks. Within the truck category, heavy-duty models require high-pressure nitrogen charging and reinforced piston assemblies to withstand extreme loads, while medium-duty and light-duty applications balance performance with cost efficiencies. Trailer suspensions emphasize consistent damping across variable cargo weights, whereas bus applications demand elevated ride comfort and passenger safety, spurring innovations in multi-stage valve technologies.
Through distribution channels, the market bifurcates into OEM supply and aftermarket sales. OEM partnerships prioritize rigorous validation processes, ensuring dampers integrate seamlessly into assembly lines and meet brand-specific performance criteria. Aftermarket operators, served through both retailers and wholesalers, offer a diverse range of replacement components, capitalizing on demand for rapid delivery and competitive pricing. Retail outlets emphasize brand visibility and value-added services, while wholesalers leverage volume purchasing to serve a broad network of workshops and fleet maintenance providers.
The choice of gas medium further differentiates product lines, with nitrogen prized for its inert properties and consistent damping over temperature variations. Argon-filled absorbers find niche applications where heavier gas molecules enhance low-speed performance, and mixed gas formulations allow fine-tuning of spring rates and responsiveness. Finally, applications in load bearing and vibration isolation define end-use requirements, with load-bearing solutions engineered for structural stability under static loads and vibration isolation products optimized to attenuate high-frequency oscillations in both on- and off-road environments.
End user industries such as agriculture, construction, mining, and transportation and logistics impose distinct operational profiles. Agricultural tractors operate in unstructured terrains that demand robust seal integrity, whereas construction vehicles require absorbers resistant to high shock loads. Mining equipment benefits from thermal stability and corrosion resistance in harsh conditions, and transportation fleets seek extended service intervals and predictable performance to minimize downtime.
This comprehensive research report categorizes the Heavy Vehicle Gas-filled Shock Absorber market into clearly defined segments, providing a detailed analysis of emerging trends and precise revenue forecasts to support strategic decision-making.
- Vehicle Type
- Distribution Channel
- Gas Type
- Application
- End User Industry
Revealing Region-Specific Dynamics Driving Adoption and Innovation in Gas-Filled Shock Absorbers Across Key Global Markets
Geographically, the Americas region remains a linchpin for heavy vehicle shock absorber demand, driven by robust freight and long-haul trucking activity across North America and significant bus and commercial vehicle fleets in Latin America. U.S. infrastructure spending has spurred investment in road maintenance and fleet modernization, supporting aftermarket growth even as OEM sales experience cyclicality. Meanwhile, Canada’s focus on sustainability has accelerated uptake of advanced damping solutions for both traditional and electric heavy vehicles.
In Europe, the Middle East, and Africa, regulatory harmonization around vehicle safety and emissions releases is encouraging regional suppliers to innovate in gas-filled damper design. European OEMs, in particular, are integrating absorbers with active chassis control systems, while Middle East markets lean on reliable aftermarket networks to maintain aging bus and truck fleets. Africa’s emerging commercial transport corridors present long-term growth potential, despite shorter replacement cycles and cost sensitivities in certain markets.
The Asia-Pacific region continues to be a powerhouse for production and consumption, anchored by substantial domestic manufacturing in China, India, and Southeast Asia. Rapid urbanization and rising demand for public transit have boosted bus suspension requirements, and the expansion of e-commerce logistics has fueled trailer and light-duty truck applications. Localized R&D centers are collaborating with global tier-one suppliers to develop gas-filled absorbers suited to diverse climatic conditions, from monsoon-affected routes to high-altitude transport in South Asia.
This comprehensive research report examines key regions that drive the evolution of the Heavy Vehicle Gas-filled Shock Absorber market, offering deep insights into regional trends, growth factors, and industry developments that are influencing market performance.
- Americas
- Europe, Middle East & Africa
- Asia-Pacific
Mapping the Competitive Terrain of Gas-Filled Shock Absorber Providers and Uncovering Strategies That Differentiate Leaders from Niche Innovators
The competitive landscape of gas-filled shock absorbers is marked by established automotive component specialists and emergent technology innovators. Leading incumbents leverage decades of manufacturing expertise and extensive distribution networks to serve both OEM and aftermarket channels. These firms are investing heavily in R&D to refine gas-sealing techniques, develop multi-chamber configurations, and enhance thermal performance under heavy loads.
Strategic alliances between suspension system manufacturers and electronic component providers are giving rise to integrated damping solutions, combining gas-filled absorbers with adaptive valve assemblies and onboard diagnostics. Such collaborations enable predictive health monitoring, unlocking new service-based revenue streams and differentiating offerings in competitive tender processes. Moreover, smaller niche players, focused on custom and retrofit solutions, are capitalizing on demand from specialized segments such as off-road mining and high-performance coach applications.
As supply chain resilience becomes paramount, many top companies are expanding localized production footprints, establishing assembly lines closer to key markets, and engaging in vertical integration of critical subcomponents. This trend not only reduces exposure to raw material price volatility but also shortens lead times, improving responsiveness to end-user requirements. The convergence of mechanical excellence with digital connectivity is setting a new benchmark for value creation across the industry.
This comprehensive research report delivers an in-depth overview of the principal market players in the Heavy Vehicle Gas-filled Shock Absorber market, evaluating their market share, strategic initiatives, and competitive positioning to illuminate the factors shaping the competitive landscape.
- Tenneco Inc.
- KYB Corporation
- ZF Friedrichshafen AG
- Showa Corporation
- Mando Corporation
- Bilstein GmbH & Co. KG
- Hitachi Astemo Ltd.
- Öhlins Racing AB
- Fox Factory Inc.
- Gabriel India Limited
Proposing Strategic Alliances Operational Adjustments and Sustainable Practices to Propel Market Leadership and Long-Term Value Creation
To capitalize on the evolving dynamics of heavy vehicle suspension, industry leaders should pursue strategic partnerships that bridge mechanical engineering expertise with digital technology capabilities. By collaborating with sensor and telematics providers, manufacturers can offer holistic ride-control solutions that deliver predictive maintenance insights, enhancing fleet uptime and reducing total cost of ownership. Such alliances also facilitate entry into performance-based contracting models, generating recurring revenue and strengthening customer relationships.
Further, companies must optimize their global sourcing strategies to mitigate tariff impacts and supply chain disruptions. Establishing or expanding regional manufacturing facilities in key markets will not only lower landed costs but also enable faster time to market for new absorber designs. Incorporating modular assembly approaches and flexible production lines will allow rapid configuration of damper variants for diverse vehicle types without significant retooling.
Lastly, investing in sustainable materials and production processes is no longer optional. Adopting recycled alloys, low-energy forging techniques, and eco-friendly coatings can support ESG goals while meeting customer expectations for environmentally responsible products. Communicating these commitments transparently through certifications and third-party validations will enhance brand reputation and open doors to procurement contracts with governments and large fleet operators.
Detailing a Multi-Tiered Research Approach Employing Primary Interviews Secondary Data Triangulation and Patent Analysis to Ensure Insight Validity
This comprehensive analysis of the heavy vehicle gas-filled shock absorber market is grounded in a robust research framework that integrates primary and secondary methodologies. Primary insights were obtained through in-depth interviews with senior executives from leading suspension system manufacturers, OEM procurement managers, and aftermarket distributors across North America, Europe, and Asia-Pacific. These conversations provided nuanced perspectives on technology roadmaps, supply chain challenges, and evolving end-user requirements.
Secondary research encompassed a thorough review of industry association publications, regulatory filings, patent databases, and technical papers on damper design and manufacturing processes. Trade journals and financial filings were analyzed to track strategic initiatives, capacity expansions, and partnership announcements among major market participants. In addition, historical tariff schedules and customs data were examined to quantify the impact of trade policies on import costs and sourcing strategies.
Data triangulation ensured the validation of market trends and competitive dynamics. Quantitative data points were cross-verified against multiple sources to identify discrepancies, while qualitative inputs from subject-matter experts lent context to emerging themes. All findings were synthesized into thematic matrices and scenario analyses to support actionable recommendations and strategic decision-making for stakeholders across the value chain.
Explore AI-driven insights for the Heavy Vehicle Gas-filled Shock Absorber market with ResearchAI on our online platform, providing deeper, data-backed market analysis.
Ask ResearchAI anything
World's First Innovative Al for Market Research
Synthesizing Market Dynamics Segmentation Drivers and Regional Trends to Illuminate the Path Forward for Industry Stakeholders
The maturation of gas-filled shock absorber technology for heavy vehicles presents both opportunities and challenges for manufacturers, OEMs, and fleet operators. The integration of digital monitoring systems, alongside advancements in materials and valve design, positions gas-filled damping solutions as a cornerstone of modern ride-control strategies. At the same time, external forces such as new tariff regimes, supply chain realignment, and stringent environmental regulations demand agility and foresight from industry participants.
Segmentation insights reveal that vehicle type, distribution channel, gas medium, application focus, and end-user industry each exert distinct influences on product requirements and competitive positioning. Regional analyses underscore divergent adoption patterns, shaped by infrastructure investment, regulatory landscapes, and local manufacturing capabilities. Key companies are vying for market share through strategic collaborations, localized production, and value-added service offerings, signaling a shift toward performance-oriented business models.
To thrive in this evolving market, stakeholders must balance the imperatives of innovation, cost efficiency, and regulatory compliance. By leveraging the insights outlined in this report, decision-makers can chart a course toward sustainable growth, enhanced operational resilience, and long-term competitive advantage.
This section provides a structured overview of the report, outlining key chapters and topics covered for easy reference in our Heavy Vehicle Gas-filled Shock Absorber market comprehensive research report.
- Preface
- Research Methodology
- Executive Summary
- Market Overview
- Market Dynamics
- Market Insights
- Cumulative Impact of United States Tariffs 2025
- Heavy Vehicle Gas-filled Shock Absorber Market, by Vehicle Type
- Heavy Vehicle Gas-filled Shock Absorber Market, by Distribution Channel
- Heavy Vehicle Gas-filled Shock Absorber Market, by Gas Type
- Heavy Vehicle Gas-filled Shock Absorber Market, by Application
- Heavy Vehicle Gas-filled Shock Absorber Market, by End User Industry
- Americas Heavy Vehicle Gas-filled Shock Absorber Market
- Europe, Middle East & Africa Heavy Vehicle Gas-filled Shock Absorber Market
- Asia-Pacific Heavy Vehicle Gas-filled Shock Absorber Market
- Competitive Landscape
- ResearchAI
- ResearchStatistics
- ResearchContacts
- ResearchArticles
- Appendix
- List of Figures [Total: 28]
- List of Tables [Total: 644 ]
Take decisive action today by partnering with Ketan Rohom to access unparalleled market insights and transform your growth strategy
If you are ready to gain an in-depth understanding of the heavy vehicle gas-filled shock absorber market’s most pivotal trends, challenges, and opportunities, now is the time to act. Reach out directly to Ketan Rohom, Associate Director of Sales & Marketing, to secure your copy of the comprehensive market research report. This report will empower your organization with actionable insights, strategic frameworks, and the competitive intelligence needed to navigate evolving regulations, supply chain complexities, and emerging technologies.
Don’t miss the opportunity to leverage detailed segmentation analyses, tariff impact assessments, and region-specific overviews that will inform your next strategic moves. Contact Ketan today to discuss customized licensing options, enterprise-wide engagement, and consultation services designed to accelerate your market leadership. Your path to superior decision-making starts with a single conversation.
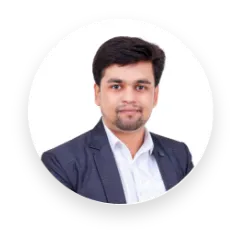
- When do I get the report?
- In what format does this report get delivered to me?
- How long has 360iResearch been around?
- What if I have a question about your reports?
- Can I share this report with my team?
- Can I use your research in my presentation?