Introduction to the High Accuracy Die Bonder Market
The high accuracy die bonder has emerged as an indispensable asset for semiconductor and advanced electronics manufacturers seeking unparalleled precision in chip assembly. This technology enables exact placement of semiconductor dies onto substrates, ensuring consistent electrical performance and long-term reliability. Driven by the relentless push for miniaturization and higher circuit densities, die bonders that deliver sub-micron accuracy are crucial for supporting advanced packaging strategies such as system-in-package (SiP), 3D integration, and fan-out wafer-level packaging (FOWLP).
Innovation in die bonding technology aligns with the evolving demands of automotive electronics, consumer gadgets, healthcare devices, and aerospace systems. As manufacturers integrate more functions into smaller footprints, even minor misalignments can lead to yield loss or thermal inefficiencies. Consequently, die bonders equipped with vision-guided alignment, closed-loop motion control, and adaptive pressure regulation are reshaping production lines.
With digital transformation fueling Industry 4.0 initiatives, these machines are increasingly networked, offering real-time process monitoring, predictive maintenance alerts, and seamless integration with manufacturing execution systems (MES). In this landscape, stakeholders-from equipment OEMs to end-users-must understand the technological advances, market drivers, and potential challenges that define the high accuracy die bonder arena.
Transformative Shifts Redefining Die Bonder Technology
Over the past five years, the high accuracy die bonder landscape has undergone transformative shifts in response to technological breakthroughs and market pressures. First, industry-wide adoption of automation platforms has accelerated, enabling manufacturers to achieve higher throughput without compromising placement precision. Concurrently, advanced vision systems-powered by machine learning algorithms-now perform real-time defect detection and alignment corrections, reducing scrap and elevating yields.
Second, the emergence of 3D packaging architectures has driven demand for sub-micron accuracy as multiple active dies stack within a single package. This trend has prompted die bonder vendors to integrate ultraviolet (UV) curing modules and micro-dispensing capabilities, allowing simultaneous bonding and adhesive control.
Third, collaborations between die bonder suppliers and semiconductor foundries have intensified, with joint development agreements ensuring equipment aligns with next-generation node requirements. As a result, research and development investments have surged, with notable progress in thermal compression and thermosonic bonding techniques for eutectic applications.
These shifts are not isolated; they reflect an industry where precision, speed, and adaptability converge to meet the escalating demands of electronics innovation.
Cumulative Impact of U.S. Tariffs on Die Bonder Supply Chains in 2025
In 2025, the cumulative impact of United States tariffs on imported electronic assembly equipment has reverberated across the high accuracy die bonder market. Import duties imposed on key components-such as precision motion stages and vision sensors-have increased production costs for equipment manufacturers, who face the dilemma of absorbing tariffs or passing costs to customers.
As a result, several die bonder OEMs have reevaluated their supply chains, relocating critical assembly operations to tariff-exempt countries or sourcing components from domestic suppliers when feasible. While these measures mitigate financial burdens, they require significant capital investment and requalification of equipment to comply with regulatory standards.
Meanwhile, end-users in automotive electronics and defense sectors contend with extended lead times as manufacturers adjust to new logistics networks. Some companies have strategically increased onshore inventory and forged partnerships with local distributors to buffer against future tariff fluctuations.
Despite these challenges, the market remains resilient. Strategic alliances, adaptive sourcing strategies, and a focus on high-value applications are helping industry participants navigate the tariff landscape while preserving innovation momentum.
Key Segmentation Insights across Technology, Material, Application, and Functionality
A nuanced view of market segmentation reveals how demand varies across technology type, bonding material, application, end-user industry, machine type, and functionality. By technology type, epoxy die bonders remain prevalent due to their versatility, with fully automatic, semi-automatic, and manual epoxy platforms serving both high-volume and low-volume producers. Flip chip die bonders-available in fully automated, semi-automatic, and manual configurations-cater to applications requiring minimal form factors, while thermal compression and thermosonic gold eutectic bonders address premium segments such as aerospace and advanced computing.
Examining bonding materials, conductive adhesives-carbon-based and silver-based-are gaining traction in applications that demand moderate electrical performance with simplified process flows. Non-conductive adhesives, whether acrylic-based or epoxy-based, are increasingly used for die attach in memory modules and power electronics. Solder paste variants, including lead-free and tin-lead formulations, remain indispensable for high-reliability joint formation.
Application-based segmentation highlights the critical role of automotive electronics, especially in advanced driver assistance systems (ADAS) and in-vehicle infotainment, where robust thermal management and reliability are non-negotiable. Consumer electronics, spanning smartphones, tablets, and wearable devices, drive demand for compact, high-speed bonders. Industrial manufacturing, encompassing control systems and robotics, demands flexible platforms capable of handling diverse substrates.
End-user industries such as defense & aerospace leverage avionics and satellite communication equipment, while healthcare deploys die bonders for medical imaging and wearable healthcare devices. Telecommunications modules and networking devices also rely on precision placement to maintain signal integrity.
Machine type differentiation shows a clear bifurcation between entry-level manual and automated solutions versus high-speed, high-precision fully automatic and semi-automatic systems. Finally, packaging functionality spans substrate level packaging (BGA, QFP), system level packaging (3D SiP, MCM), and wafer level packaging (CSP, FOWLP), each driving unique equipment specifications.
This comprehensive research report categorizes the High Accuracy Die Bonder market into clearly defined segments, providing a detailed analysis of emerging trends and precise revenue forecasts to support strategic decision-making.
- Technology Type
- Bonding Material
- Application
- End-User Industry
- Machine Type
- Functionality
Key Regional Insights Shaping Market Trajectories
Regional dynamics shape strategic priorities and investment flows within the high accuracy die bonder market. In the Americas, strong demand for automotive electronics and telecommunications infrastructure has translated into significant capital expenditure on precision assembly equipment. North American manufacturers benefit from robust R&D ecosystems and government incentives for domestic semiconductor production.
In Europe, Middle East & Africa, a well-established industrial base supports advanced manufacturing in aerospace, defense, and healthcare sectors. European die bonder vendors emphasize customization, often collaborating with research institutes to develop bespoke solutions. Meanwhile, the Middle East is progressively investing in electronics manufacturing clusters to diversify economies, presenting new opportunities for equipment suppliers.
Asia-Pacific remains the most dynamic region, driven by high-volume consumer electronics production in East Asia and rapid expansion of automotive electronics in Southeast Asia. State-backed initiatives in countries like China, South Korea, and Taiwan continue to bolster semiconductor fabrication and packaging capacity. This has spurred local OEMs to ramp up production of high accuracy die bonders, often incorporating cutting-edge features to serve both domestic and export markets.
This comprehensive research report examines key regions that drive the evolution of the High Accuracy Die Bonder market, offering deep insights into regional trends, growth factors, and industry developments that are influencing market performance.
- Americas
- Asia-Pacific
- Europe, Middle East & Africa
Key Company Insights and Competitive Differentiators
Competitive intensity in the high accuracy die bonder market is anchored by a blend of established OEMs and specialized technology providers. ASM Pacific Technology Ltd. has secured a leading position through continuous innovation in automated die attach and wafer transfer solutions. Besi (BE Semiconductor Industries N.V.) has differentiated itself by enhancing throughput for flip chip and advanced packaging applications. Fasford Technology Co., Ltd. focuses on cost-effective, compact systems tailored for regional electronics manufacturers.
Hesse GmbH is recognized for its high-precision thermal compression bonders that serve premium segments in automotive and aerospace. Kulicke and Soffa Industries, Inc. combines system integration expertise with legacy experience in semiconductor assembly, offering turnkey production lines. Palomar Technologies, Inc. leverages advanced vision alignment to address the needs of ultra-fine pitch applications.
Panasonic Corporation and SHINKAWA Ltd. continue to broaden their portfolios with hybrid die bonding platforms that integrate adhesive dispensing and curing. TEL NEXX, Inc. emphasizes modularity and scalability, enabling quick configuration changes on the production floor. Toray Engineering Co., Ltd. offers comprehensive support services, reinforcing long-term collaborations with end-users in defense and medical device manufacturing.
This comprehensive research report delivers an in-depth overview of the principal market players in the High Accuracy Die Bonder market, evaluating their market share, strategic initiatives, and competitive positioning to illuminate the factors shaping the competitive landscape.
- ASM Pacific Technology Ltd.
- Besi (BE Semiconductor Industries N.V.)
- Fasford Technology Co., Ltd.
- Hesse GmbH
- Kulicke and Soffa Industries, Inc.
- Palomar Technologies, Inc.
- Panasonic Corporation
- SHINKAWA Ltd.
- TEL NEXX, Inc.
- Toray Engineering Co., Ltd.
Actionable Recommendations for Industry Leaders
Industry leaders can capitalize on emerging opportunities by adopting a focused set of strategic actions. First, prioritize modular automation: investing in scalable platforms that accommodate future functionality expansions reduces total cost of ownership and minimizes downtime during product transitions. Second, strengthen supply chain resilience by diversifying component sourcing and qualifying dual suppliers for critical subsystems such as motion stages and optical sensors.
Third, forge deeper partnerships with semiconductor foundries and integrated device manufacturers (IDMs) to co-develop die bonding processes optimized for next-generation packaging architectures. These collaborative efforts can accelerate time-to-market and ensure equipment readiness for advanced node requirements.
Fourth, integrate data analytics and predictive maintenance capabilities to drive continuous process improvement and maximize equipment uptime. Fifth, target high-growth verticals-such as electric vehicle electronics and wearable medical devices-with tailored marketing and service offerings that address regulatory and reliability benchmarks.
Finally, embed sustainability principles by optimizing energy consumption, reducing adhesive waste, and pursuing circular economy initiatives for retired equipment. Such green credentials will resonate with environmentally conscious customers and support compliance with evolving ESG frameworks.
Explore AI-driven insights for the High Accuracy Die Bonder market with ResearchAI on our online platform, providing deeper, data-backed market analysis.
Ask ResearchAI anything
World's First Innovative Al for Market Research
Conclusion: Navigating the Future of Precision Die Bonding
The high accuracy die bonder market is at a pivotal juncture, shaped by technological innovation, dynamic regional trends, and evolving regulatory landscapes. Companies that harness advanced automation, forge collaborative partnerships, and implement resilient supply chain strategies will stand out in this competitive environment. Moreover, focusing on energy efficiency and sustainability can unlock new value propositions, enhancing brand reputation and customer loyalty.
As applications become more complex and precision requirements tighten, the ability to deliver modular, scalable, and data-driven solutions will determine market leadership. By aligning R&D investments with the demands of automotive, aerospace, healthcare, and consumer electronics segments, equipment providers can capture emerging opportunities and drive long-term growth.
This section provides a structured overview of the report, outlining key chapters and topics covered for easy reference in our High Accuracy Die Bonder market comprehensive research report.
- Preface
- Research Methodology
- Executive Summary
- Market Overview
- Market Dynamics
- Market Insights
- Cumulative Impact of United States Tariffs 2025
- High Accuracy Die Bonder Market, by Technology Type
- High Accuracy Die Bonder Market, by Bonding Material
- High Accuracy Die Bonder Market, by Application
- High Accuracy Die Bonder Market, by End-User Industry
- High Accuracy Die Bonder Market, by Machine Type
- High Accuracy Die Bonder Market, by Functionality
- Americas High Accuracy Die Bonder Market
- Asia-Pacific High Accuracy Die Bonder Market
- Europe, Middle East & Africa High Accuracy Die Bonder Market
- Competitive Landscape
- ResearchAI
- ResearchStatistics
- ResearchContacts
- ResearchArticles
- Appendix
- List of Figures [Total: 28]
- List of Tables [Total: 1077 ]
Call-To-Action: Connect with Ketan Rohom to Access the Full Report
To gain a comprehensive understanding of market dynamics, competitive landscapes, and strategic growth opportunities in high accuracy die bonder technology, reach out to Ketan Rohom (Associate Director, Sales & Marketing) to purchase the full market research report. Harness the insights needed to make informed decisions and stay ahead in this rapidly evolving industry.
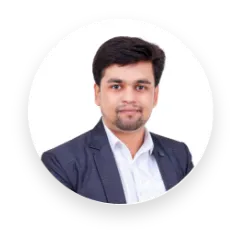
- When do I get the report?
- In what format does this report get delivered to me?
- How long has 360iResearch been around?
- What if I have a question about your reports?
- Can I share this report with my team?
- Can I use your research in my presentation?