Introduction to the High-End SMD Rework Equipment Market
The high-end surface-mount device (SMD) rework equipment sector has emerged as a pivotal enabler of precision repair, prototyping, and customization in electronics manufacturing. Over the past decade, rapid advancements in miniaturization and complex multilayered assemblies have heightened the demand for equipment capable of handling delicate active and passive components with micron-level accuracy. Today, stakeholders across automotive, aerospace, healthcare, and consumer electronics rely on sophisticated rework platforms to maintain production yields, reduce waste, and accelerate time to market.
Navigating this landscape requires a thorough understanding of the interplay between cutting-edge technologies-ranging from laser and infrared reflow to ultrasonic and hot air systems-and stringent quality standards. As complexity grows, so does the necessity for modular solutions that integrate heating, cooling, and precise handling within single or networked work cells. This executive summary sets the stage for a comprehensive exploration of transformative industry shifts, tariff impacts, segmentation analysis, and actionable recommendations that will empower decision-makers to capitalize on emerging opportunities.
Transformative Shifts Redefining SMD Rework Processes
Electronics manufacturing is undergoing a paradigm shift driven by the convergence of miniaturization, additive processes, and Industry 4.0 automation. In response, rework equipment has evolved from standalone stations into integrated, semi-autonomous cells that leverage real-time analytics and adaptive control strategies. As a result, quality assurance has moved beyond post-process inspection toward inline monitoring, enabling closed-loop adjustments to solder profiles and airflow dynamics on the fly.
Simultaneously, the incorporation of laser rework and non-contact infrared technologies has redefined precision limits, especially for heat-sensitive substrates and complex microchip arrays. Add to this the rising prominence of hybrid manufacturing workflows-where additive deposition and subtractive rework co-exist-and the industry is witnessing a fundamental reconfiguration of assembly lines. Consequently, equipment manufacturers are partnering with software providers to offer digital twins and predictive maintenance dashboards, fostering unprecedented reliability and uptime.
Assessing the Cumulative Impact of 2025 US Tariffs
In 2025, newly imposed United States tariffs on semiconductor equipment and related components have reverberated across global supply chains. Manufacturers who source hot air systems, laser modules, and precision handling assemblies from tariff-affected regions now face increased landed costs, leading to strategic sourcing adjustments. Many have relocated assembly operations or diversified supplier bases to mitigate cost escalations.
Moreover, the tariffs have incentivized domestic production of critical subassemblies, accelerating investments in local manufacturing capabilities. While these measures buffer some direct tariff exposure, they also necessitate capital allocation for tooling, workforce training, and compliance certifications. In turn, original equipment manufacturers are revisiting pricing models to balance margin preservation with customer demand for affordable rework solutions. As a ripple effect, aftermarket service contracts and consumable revenues have gained importance as stable revenue streams in a fluctuating tariff environment.
Key Segmentation Insights Across Product, Component, Industry, Technology, Application, Functionality, and Business Models
Deep analysis reveals that product-type segmentation shapes both capital expenditure and operational workflows. Benchtop systems continue to serve R&D and small-batch producers, whereas mobile rework units cater to field maintenance applications. Standalone systems dominate high-volume facilities, with fully automated cells handling bulk rework, manual stations addressing bespoke repairs, and semi-automated lines balancing throughput with flexibility.
Component-type segmentation further refines equipment specifications. Active assemblies, especially application-specific integrated circuits, demand pinpoint laser or non-contact infrared modules. Passive elements such as capacitors and resistors call for controlled convection via hot air or ultrasonic agitation. Power electronics-thyristors and transistors-require bespoke thermal profiles to ensure junction integrity.
Meanwhile, end-user industries dictate feature priorities: electric vehicle battery management boards and infotainment clusters demand rigorous thermal management; laptop and smartphone repair shops emphasize quick changeovers; bioelectronics and medical imaging sectors require ultra-clean environments; manufacturing automation and robotics rely on high-throughput capability; 5G infrastructure and optical fiber network equipment necessitate sub-micron alignment.
Technological differentiation is equally pronounced. Convection-based hot air systems deliver uniform heat spread, while non-contact infrared minimizes thermal mass impacts. Laser rework, leveraging CO2 and Nd:YAG sources, excels at microchip removal. Ultrasonic systems, operating at high frequencies, break solder joints without excessive heat.
Application-driven segmentation underscores use cases from component replacement to faulty board repair, and from product customization to rapid prototyping. Functionality segmentation highlights all-in-one platforms that integrate heating, cooling, and vision systems, as well as dedicated cooling or heating stations. Lastly, business model segmentation reflects evolving go-to-market strategies, spanning direct OEM sales, distributor networks, and digital marketplaces.
This comprehensive research report categorizes the High-End SMD Rework Equipment market into clearly defined segments, providing a detailed analysis of emerging trends and precise revenue forecasts to support strategic decision-making.
- Product Type
- Component Type
- End-User Industry
- Technology
- Application
- Equipment Functionality
- Business Model
Key Regional Insights Shaping Market Dynamics
Regional dynamics underscore distinct growth trajectories and investment patterns. In the Americas, strong R&D hubs and service centers are bolstering demand for modular bench and standalone rework systems, while reshoring initiatives drive domestic capacity expansion. In contrast, Europe, Middle East & Africa markets emphasize regulatory compliance and sustainability, prompting suppliers to enhance energy efficiency and reduce solder wastage. Asia-Pacific remains the largest adopter, fueled by robust consumer electronics manufacturing in Southeast Asia and China, as well as burgeoning automotive production in India and Japan. Here, low-cost mobile rework units coexist with state-of-the-art automated cells in advanced factories. These geographic variations influence product roadmaps, aftermarket support structures, and strategic partnerships, making regional alignment critical for sustained competitiveness.
This comprehensive research report examines key regions that drive the evolution of the High-End SMD Rework Equipment market, offering deep insights into regional trends, growth factors, and industry developments that are influencing market performance.
- Americas
- Asia-Pacific
- Europe, Middle East & Africa
Key Companies Driving Innovation and Market Leadership
The competitive landscape features a diverse set of specialized equipment vendors. Ersa GmbH continues to innovate in convection and selective soldering platforms, whereas Hakko Corporation leads in modular hot air and infrared stations. JBC Soldering SL drives breakthroughs in ergonomic handheld rework tools, and Metcal (OKI Brand) integrates advanced thermal management into its benchtop systems. Nordson Dage’s X-ray inspection integration with rework cells sets new quality benchmarks. Pace Worldwide focuses on portable high-precision units for field technicians, while SEHO Systems GmbH delivers turnkey automated reflow and selective soldering lines. VJ Electronix excels in high-frequency ultrasonic rework systems. Weller Tools GMBH persists as a legacy brand with user-friendly entry-level solutions. Zhongshan Jegatech Electronics Co., Ltd. competes on cost-effective, scalable assemblies for emerging markets.
This comprehensive research report delivers an in-depth overview of the principal market players in the High-End SMD Rework Equipment market, evaluating their market share, strategic initiatives, and competitive positioning to illuminate the factors shaping the competitive landscape.
- Ersa GmbH
- Hakko Corporation
- JBC Soldering SL
- Metcal (OKI Brand)
- Nordson Dage
- Pace Worldwide
- SEHO Systems GmbH
- VJ Electronix
- Weller Tools GMBH
- Zhongshan Jegatech Electronics Co., Ltd.
Actionable Recommendations for Industry Leaders
Industry leaders should prioritize modularity and digitalization to maintain a competitive edge. First, forging alliances with software providers to integrate cloud connectivity and machine-learning analytics will enable predictive maintenance and yield optimization. Second, diversifying supply chains by qualifying multiple component vendors reduces exposure to tariff-driven cost fluctuations. Third, investing in staff training on advanced technologies-such as laser rework calibration and ultrasonic solder removal-ensures consistent process quality. Fourth, developing retrofit kits that upgrade legacy rework cells for closed-loop temperature control and vision-assisted alignment can unlock revenue from installed bases. Finally, expanding service offerings through subscription-based models and outcome-oriented contracts will create recurring revenue streams and deepen customer engagement.
Explore AI-driven insights for the High-End SMD Rework Equipment market with ResearchAI on our online platform, providing deeper, data-backed market analysis.
Ask ResearchAI anything
World's First Innovative Al for Market Research
Conclusion: Embracing Agility and Innovation for Market Leadership
The high-end SMD rework equipment sector stands at the intersection of technological innovation, regulatory shifts, and evolving customer expectations. As tariffs reshape cost structures and regional imperatives redefine growth corridors, success hinges on agility, collaboration, and a relentless focus on value delivery. By synthesizing advanced thermal, optical, and mechanical capabilities within modular platforms, and by embedding digital intelligence at every stage, equipment providers can meet the exacting demands of next-generation electronics fabrication and repair. Ultimately, those who invest in ecosystem partnerships, workforce development, and service-centric business models will lead the market’s transformation.
This section provides a structured overview of the report, outlining key chapters and topics covered for easy reference in our High-End SMD Rework Equipment market comprehensive research report.
- Preface
- Research Methodology
- Executive Summary
- Market Overview
- Market Dynamics
- Market Insights
- Cumulative Impact of United States Tariffs 2025
- High-End SMD Rework Equipment Market, by Product Type
- High-End SMD Rework Equipment Market, by Component Type
- High-End SMD Rework Equipment Market, by End-User Industry
- High-End SMD Rework Equipment Market, by Technology
- High-End SMD Rework Equipment Market, by Application
- High-End SMD Rework Equipment Market, by Equipment Functionality
- High-End SMD Rework Equipment Market, by Business Model
- Americas High-End SMD Rework Equipment Market
- Asia-Pacific High-End SMD Rework Equipment Market
- Europe, Middle East & Africa High-End SMD Rework Equipment Market
- Competitive Landscape
- ResearchAI
- ResearchStatistics
- ResearchContacts
- ResearchArticles
- Appendix
- List of Figures [Total: 30]
- List of Tables [Total: 943 ]
Call-To-Action: Connect with Ketan Rohom to Access Full Market Analysis
To gain comprehensive insights and strategic guidance on the high-end SMD rework equipment market, reach out to Ketan Rohom, Associate Director of Sales & Marketing, and secure your in-depth research report today.
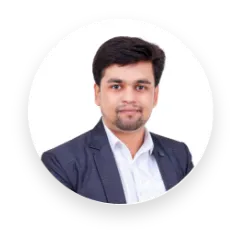
- When do I get the report?
- In what format does this report get delivered to me?
- How long has 360iResearch been around?
- What if I have a question about your reports?
- Can I share this report with my team?
- Can I use your research in my presentation?