The High Performance Alloys Market size was estimated at USD 10.36 billion in 2024 and expected to reach USD 10.91 billion in 2025, at a CAGR 5.44% to reach USD 14.24 billion by 2030.

Unlocking the Potential of High Performance Alloys
High performance alloys have emerged as indispensable materials across industries that demand exceptional strength, corrosion resistance, and temperature tolerance. From the intricate components of aerospace engines to the critical implants used in medical procedures, these advanced materials underpin technological breakthroughs and operational reliability. Their unique chemistries and tailored microstructures deliver properties unattainable with conventional metals, enabling designers and engineers to push the boundaries of performance in extreme environments.
As global infrastructure projects intensify and environmental regulations tighten, the demand for alloys that endure high stresses and corrosive conditions has surged. Manufacturers are investing in novel alloy compositions and innovative processing techniques to meet rigorous application requirements while balancing cost pressures. Simultaneously, the crossover between additive manufacturing and traditional metallurgical processes is reshaping how components are designed, produced, and validated.
This executive summary provides a concise yet comprehensive overview of the high performance alloys landscape, highlighting transformative market shifts, the impact of evolving trade policies, critical segmentation insights, and strategic recommendations. It equips decision-makers with the actionable intelligence needed to navigate supply chain complexities, leverage regional growth dynamics, and partner effectively with leading suppliers.
Evolutionary Forces Redefining Alloy Markets
The high performance alloys market is undergoing a fundamental transformation driven by technological breakthroughs, sustainability imperatives, and shifting end-user needs. On the technology front, the maturation of additive manufacturing has unlocked geometries and material utilization rates previously considered impractical. This shift has forced conventional processes such as casting and forging to evolve, integrating digital design tools and real-time process monitoring to enhance quality and repeatability.
At the same time, heightened regulatory scrutiny over carbon footprints and resource efficiency is compelling industry stakeholders to optimize alloy chemistries for recyclability and reduced energy consumption. Manufacturers are exploring low-embodied-energy feedstocks and embracing closed-loop supply chains to comply with stringent environmental standards while preserving material performance.
Concurrently, application domains are redefining performance benchmarks. Aerospace and defense sectors demand alloys that withstand extreme temperatures and corrosive atmospheres, whereas the automotive industry prioritizes lightweight structures that bolster vehicle efficiency without compromising safety. These divergent requirements are fueling the rapid development of specialized alloys and driving strategic partnerships between material scientists, component makers, and end-users.
Navigating the 2025 Tariff Ripple Across U.S. Trade
In 2025, the cumulative impact of revised U.S. tariffs on imported high performance alloys has introduced a ripple effect across global supply chains, reshaping sourcing strategies and pricing dynamics. Suppliers in North America are recalibrating their production footprints to mitigate duty-induced cost increases, while import-dependent manufacturers are securing alternative partnerships in tariff-exempt regions to maintain competitive positioning.
The tariff adjustments have also influenced inventory management practices. Companies are elevating safety stock levels to buffer against potential customs delays, leading to increased working capital requirements. Procurement teams are negotiating longer-term contracts with domestic mills to lock in favorable pricing and guaranteed throughput, thereby reducing exposure to tariff volatility.
Meanwhile, end-users are re-evaluating their value chains, seeking end-to-end transparency to assess landed costs and compliance risks. This heightened diligence has underscored the importance of robust data analytics and supplier scorecards, enabling organizations to optimize material flows and anticipate policy shifts. As a result, firms that proactively adapt to the revised tariff environment are gaining resilience and forging stronger ties with strategic alloy producers.
Decoding Market Segments Driving Alloy Innovation
The high performance alloys market can be dissected through several critical lenses that reveal where innovation and demand are most concentrated. When assessing alloy types, stakeholders encounter five core families. Aluminum-based systems encompass copper, lithium, silicon, and zinc alloys formulated for lightweight applications, while copper-derived materials including beryllium copper, bronze, and copper-nickel blends serve roles in conductivity and wear resistance. Stainless steels, spanning austenitic, duplex, ferritic, and martensitic grades, provide versatile corrosion performance across industries. Superalloys built on cobalt, iron, nickel, and titanium matrices deliver exceptional strength at elevated temperatures, vital for turbines and propulsion systems. Titanium alloys, in turn, divide into alpha and beta variants distinguished by their microstructural stability under diverse loading conditions.
The form in which these alloys are supplied further shapes their use cases. Bars-available as rounds or squares-offer robust feedstock for machining and forging operations. Powders facilitate additive manufacturing processes that yield complex geometries. Sheets produced in thick and thin gauges meet requirements for structural panels and heat exchangers. Tubes serve sectors from oil and gas to medical devices, while wires-offered as solid or stranded configurations-enable electrical applications and spring manufacture.
Manufacturing processes exert significant influence over material performance. Additive manufacturing unlocks design freedom, enabling lattice structures and internal cooling channels. Casting techniques, whether die casting for precision or sand casting for large-scale components, introduce unique microstructures. Extrusion-conducted under cold, warm, or hot conditions-optimizes grain flow for strength and ductility. Forging operations, whether closed or open die, refine mechanical properties through controlled deformation. Powder metallurgy routes deliver near-net-shape parts with minimal machining waste.
Application-driven segmentation highlights the breadth of end uses. Aerospace demands aircraft components, spacecraft assemblies, and turbine engines engineered for cyclic loads and thermal extremes. The automotive sector leverages alloys in exhaust manifolds, fuel delivery systems, high-performance engines, and suspension hardware to advance vehicle efficiency and power output. Chemical and petrochemical plants employ corrosion-resistant alloys in piping, reactors, and valves. Defense and military platforms rely on armor plating, weapon systems, and aircraft structures that meet rigorous reliability standards. Electronics harness conductive and thermal management properties for semiconductors and heat sinks. Energy projects, spanning oil and gas exploration to renewable installations, utilize alloys that endure aggressive environments. Medical devices draw on biocompatible alloys for implants and surgical instruments that demand precision and long-term stability.
Finally, the distinction between aftermarket channels and original equipment manufacturers underscores divergent procurement models. Aftermarket suppliers focus on refurbishment and upgrade cycles, while OEMs integrate bespoke alloy components into new product lines, calibrating metallurgical specifications to proprietary designs.
This comprehensive research report categorizes the High Performance Alloys market into clearly defined segments, providing a detailed analysis of emerging trends and precise revenue forecasts to support strategic decision-making.
- Type Of Alloy
- Product Form
- Manufacturing Process
- Application
- End-User
Regional Dynamics Shaping Alloy Adoption Globally
The geographic landscape of the high performance alloys market reveals distinct growth trajectories and supply chain strengths across key regions. In the Americas, robust industrial infrastructure and vertically integrated supply chains support advanced metalworking clusters. North American producers have capitalized on proximity to major end-users in aerospace, automotive, and energy, establishing state-of-the-art fabrication facilities and specialized R&D centers.
Across Europe, the Middle East, and Africa, diversity in economic maturity and resource endowments shapes alloy adoption patterns. Western Europe’s stringent regulatory framework and focus on sustainability drive demand for low-carbon production methods and recyclable materials. Meanwhile, Middle Eastern investment in petrochemical and defense sectors has spurred localized alloy production capabilities. In Africa, emerging markets are gradually harnessing high performance alloys in infrastructure and mining operations, though capacity constraints and skills gaps remain challenges.
The Asia-Pacific region continues to register dynamic expansion as governments channel funding into high-tech manufacturing and renewable energy projects. East Asian nations lead in additive manufacturing innovation, integrating alloys into next-generation electronics and automotive supply chains. Southeast Asian economies are enhancing metal processing competencies to capture a greater share of regional demand, while South Asia’s growing industrial base signals rising requirements for corrosion-resistant and heat-tolerant materials.
This comprehensive research report examines key regions that drive the evolution of the High Performance Alloys market, offering deep insights into regional trends, growth factors, and industry developments that are influencing market performance.
- Americas
- Europe, Middle East & Africa
- Asia-Pacific
Strategic Profiles of Leading Alloy Manufacturers
The competitive landscape of high performance alloys is characterized by a blend of global conglomerates and specialized niche players, each leveraging unique capabilities to differentiate offerings. Major integrated steel and specialty metal producers dominate in volume supply, benefiting from extensive production networks, proprietary metallurgical know-how, and broad product portfolios. These leaders continually expand their alloy roadmaps, invest in pilot-scale additive manufacturing lines, and implement digital twins for process optimization.
In parallel, regional and boutique alloy manufacturers have carved out positions by focusing on custom alloy development and rapid prototype services. Their agility in responding to niche application demands-from bespoke aerospace alloys to biocompatible implant materials-has made them preferred partners for original equipment manufacturers seeking tailored solutions.
Furthermore, strategic partnerships between material science innovators and component producers are reshaping go-to-market approaches. Collaborative research agreements, co-located research centers, and shared testing labs accelerate time-to-market for next-generation alloys. These alliances underpin a shift toward solution-based business models, where technical support, application engineering, and lifecycle services complement raw material supply.
This comprehensive research report delivers an in-depth overview of the principal market players in the High Performance Alloys market, evaluating their market share, strategic initiatives, and competitive positioning to illuminate the factors shaping the competitive landscape.
- Alcoa Corporation
- AMG Aluminium
- Aperam
- ATI Inc.
- Carpenter Technology Corporation
- Daido Steel Co., Ltd.
- Elementum 3D
- Fort Wayne Metals Research Products, LLC
- High Performance Alloys, Inc.
- Hindalco Industries Ltd.
- Hitachi, Ltd.
- IBC Advanced Alloys
- Magna Group
- Materion Corporation
- Mitsubishi Materials Corporation
- Nippon Yakin Kogyo Co., Ltd.
- Outokumpu Group
- Precision Castparts Corp. by Berkshire Hathaway Inc.
- Sakuma Special Steel Co., Ltd.
- Sandvik AB
- Smiths High Performance
- Stanford Advanced Materials by Oceania International LLC
- Star Wire (India) Limited
- thyssenkrupp AG
- Timken Company
- VDM Metals by Acerinox, S.A.
- Voestalpine High Performance Metals GmbH
Actionable Strategies to Thrive in Alloy Markets
Industry leaders must adopt proactive strategies to capture emerging opportunities in the high performance alloys sector. First, investing in flexible manufacturing platforms that integrate both additive and conventional processing will enable rapid adaptation to shifting product specifications and lead times. Embracing digitalization-through process analytics, real-time quality monitoring, and predictive maintenance-will further enhance productivity and reduce scrap rates.
Second, prioritizing sustainable alloy design and recycling initiatives will align material offerings with global decarbonization goals. Developing low-embodied-energy feedstocks, optimizing alloy chemistries for closed-loop recovery, and obtaining eco-certifications can unlock new market segments and satisfy procurement mandates.
Third, forging strategic alliances across the value chain-from research institutions to end-user OEMs-will accelerate innovation and de-risk technology adoption. Joint development programs focused on application-specific material performance, co-investment in pilot lines, and shared validation protocols can shorten commercialization cycles.
Lastly, strengthening geographic diversification by establishing production and service footprints in high-growth regions will improve supply chain resilience and foster closer collaboration with regional customers. Tailoring alloy formulations to local regulatory requirements and application conditions can further enhance market penetration.
Rigorous Research Framework Underpinning Insights
The research underpinning these insights combines rigorous primary and secondary approaches to ensure depth, accuracy, and relevance. Primary research involved systematic interviews and structured discussions with material scientists, procurement leaders, and senior executives across key industries. These engagements provided firsthand perspectives on emerging alloy requirements, procurement dynamics, and supply chain resilience strategies.
Secondary research encompassed an exhaustive review of technical publications, patent filings, regulatory filings, and industry white papers. Data triangulation techniques were applied to reconcile divergent sources and validate trends. In addition, metallurgical performance reports, trade association statistics, and policy documents were analyzed to gauge market drivers and barriers.
Quantitative analysis leveraged historical shipment data and trade flow records to map supply chain concentrations and anticipate potential disruptions. Qualitative synthesis explored case studies of alloy adoption in demanding applications, drawing lessons on best practices and common pitfalls. A collaborative peer review process with subject matter experts ensured methodological rigor and minimized bias.
Explore AI-driven insights for the High Performance Alloys market with ResearchAI on our online platform, providing deeper, data-backed market analysis.
Ask ResearchAI anything
World's First Innovative Al for Market Research
Synthesizing Trends for Strategic Decision-Making
Throughout this summary, the multifaceted nature of the high performance alloys market has become clear. Technological innovations and sustainability mandates are reshaping both supply and demand, while regulatory and trade dynamics add layers of complexity. Segmentation analysis reveals that tailored alloy compositions, diverse product forms, and specialized manufacturing processes converge to meet exacting application requirements. Regional insights highlight that proximity to end-users, regulatory environments, and investment climates drive distinct growth patterns.
Leading organizations have demonstrated that the ability to integrate advanced processes, embrace digital transformation, and collaborate strategically are critical success factors. Meanwhile, adaptive supply chain strategies that account for tariff fluctuations and capacity constraints will determine resilience in an increasingly volatile global landscape.
As market participants navigate these converging forces, the need for precise, actionable intelligence has never been greater. By synthesizing current trends, segmentation nuances, regional dynamics, and competitive profiles, decision-makers can chart a clear path forward, ensuring that material choices and business strategies align with evolving industry imperatives.
This section provides a structured overview of the report, outlining key chapters and topics covered for easy reference in our High Performance Alloys market comprehensive research report.
- Preface
- Research Methodology
- Executive Summary
- Market Overview
- Market Dynamics
- Market Insights
- Cumulative Impact of United States Tariffs 2025
- High Performance Alloys Market, by Type Of Alloy
- High Performance Alloys Market, by Product Form
- High Performance Alloys Market, by Manufacturing Process
- High Performance Alloys Market, by Application
- High Performance Alloys Market, by End-User
- Americas High Performance Alloys Market
- Europe, Middle East & Africa High Performance Alloys Market
- Asia-Pacific High Performance Alloys Market
- Competitive Landscape
- ResearchAI
- ResearchStatistics
- ResearchContacts
- ResearchArticles
- Appendix
- List of Figures [Total: 26]
- List of Tables [Total: 961 ]
Secure Your Comprehensive Alloy Market Report Today
Ready to gain a competitive edge in the high performance alloys market? Connect with Ketan Rohom, Associate Director of Sales & Marketing, to secure your comprehensive market research report today. Benefit from tailored insights, in-depth analysis, and strategic guidance that empower your decision-making process. Reach out now to explore how this authoritative report can support your growth objectives, identify untapped opportunities, and position your organization at the forefront of alloy innovation. Don’t miss the chance to access the definitive resource for driving success in this dynamic industry.
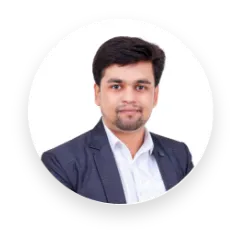
- How big is the High Performance Alloys Market?
- What is the High Performance Alloys Market growth?
- When do I get the report?
- In what format does this report get delivered to me?
- How long has 360iResearch been around?
- What if I have a question about your reports?
- Can I share this report with my team?
- Can I use your research in my presentation?