Introduction: High Performance Synthetic Fibers in Modern Composite Applications
High performance synthetic fibers have emerged as foundational elements in modern composite engineering, delivering unmatched strength-to-weight ratios and tailored mechanical properties. Innovations in polymer science and manufacturing processes have propelled materials such as Pbo, polyacrylonitrile, polyamide, and polyethylene to the forefront of applications spanning aerospace structures, automotive components, and advanced sports equipment. As industries demand composites with superior fatigue resistance, high tensile strength, and exceptional thermal stability, the ability to fine-tune fiber composition and integration has never been more critical.
This executive summary provides a methodical exploration of the forces shaping the synthetic fiber composites market. It highlights transformative shifts in industry dynamics, evaluates recent policy impacts, and distills insights from key segmentation and regional analyses. By synthesizing competitive intelligence on leading manufacturers and innovators, this overview equips decision-makers with actionable knowledge to seize emerging opportunities and mitigate risks. Throughout, we maintain a clear emphasis on strategic alignment, technical rigor, and market relevance to facilitate informed investment and development decisions.
Transformative Shifts Reshaping the Synthetic Fiber Composite Landscape
The synthetic fiber composites landscape is undergoing profound change, driven by converging technological, regulatory, and end-use demands. Breakthroughs in nanotechnology integration and advanced surface modification techniques have enabled the creation of ‘‘smart’’ composites capable of real-time health monitoring and adaptive load distribution. Simultaneously, sustainability imperatives are reshaping raw material choices, with bio-based fibers and renewable feedstocks gaining traction alongside traditional polymers.
Regulatory shifts are compounding these technological advances. Stricter emissions standards in the automotive sector are accelerating adoption of lightweight composite structural parts, while stringent aerospace safety requirements are pushing manufacturers to qualify next-generation Pbo fibers and high-tensile polyethylene for critical flight components. Across defense systems and marine applications, demand for enhanced impact resistance and environmental durability underscores the need for fibers that meet both mechanical and chemical stability criteria.
End-use diversification is another transformative factor. Beyond conventional aerospace and automotive domains, composites reinforced with co-mingled and hybrid fiber architectures are finding applications in wind energy blades, protective equipment, and emerging electric vehicle components. This cross-sector proliferation reflects a broader trend: the transition from commodity synthetic fibers to highly engineered, application-specific solutions.
Cumulative Impact of United States Tariffs 2025 on Fiber Composite Supply Chains
The introduction of new United States tariff measures in 2025 has disrupted the global supply chains for high performance synthetic fibers and composite manufacturing inputs. Tariffs on raw precursors for polyacrylonitrile and specialty modified Pbo have increased production costs for domestic fabricators, prompting many to reassess sourcing strategies. As a result, manufacturers have sought alternate suppliers in Asia-Pacific and Europe, where differential duty rates and free trade agreements help mitigate incremental import expenses.
These policy changes have catalyzed strategic realignments. Some integrated producers have shifted toward in-house precursor synthesis to control pricing volatility and ensure material traceability. Others have fast-tracked investments in automation-driven innovative manufacturing techniques to offset tariff-induced cost inflation. The reconfiguration of supply routes has also intensified competition among global resin transfer molding and filament winding equipment providers, as fabricators prioritize leaner, more flexible production setups.
In parallel, end-users are responding to cost pressures by optimizing composite designs for maximum material efficiency. High modulus fibers with superior fatigue resistance are being specified in place of traditional reinforcements, reducing overall composite volume without sacrificing performance. These adaptations underscore a broader market dynamic: regulatory headwinds are accelerating technical innovation and supply chain diversification, ultimately driving a more resilient and competitive synthetic fiber composite ecosystem.
Key Segmentation Insights Driving Product Development and Market Demand
A granular examination of market segmentation reveals the multifaceted drivers shaping demand and development. By fiber composition, the market encompasses Pbo, polyacrylonitrile, polyamide, and polyethylene variants, with modified Pbo emerging as a specialized segment for ultra-high modulus applications in aerospace and defense. In structural applications, demand spans aerospace components, automotive components, construction materials, defense systems, marine components, and sports equipment, each with distinct mechanical and regulatory requirements.
Mechanical properties further differentiate product positioning: fibers characterized by creep resistance, cyclic performance-which includes dynamic load characteristics-and fatigue resistance are prioritized for long-life infrastructures and high-cadence machinery. High modulus and high tensile strength fibers address applications demanding minimal deflection under extreme loads, while impact resistance remains critical for protective equipment and crash-worthy automotive structures.
Thermal and chemical stability also plays a pivotal role. High temperature resistance and environmental durability drive selection for turbines, marine hulls, and chemical processing vessels, whereas low thermal conductivity and chemical resistance influence insulation panels and pipeline reinforcements. Manufacturing techniques introduce another layer of complexity: compression molding, filament winding, prepreg processes, pultrusion, and resin transfer molding each yield divergent composite architectures. Among these, automation-driven and hybrid processes are gaining favor for their balance of throughput and precision.
End use applications weave these factors into cohesive solutions: aerospace structures and automotive structural parts benefit from bio-based and nanotechnology-integrated fibers, while protective equipment and sporting goods capitalize on surface-modified smart composites. Wind energy blades demand scalable pultrusion and filament winding approaches. Finally, fiber integration strategies-ranging from advanced weaving to interlayer reinforcement-enhance load transfer, and innovation fronts such as smart composites and next generation materials illustrate the ongoing evolution of the synthetic fiber composites domain.
This comprehensive research report categorizes the High Performance Synthetic Fibers for Composites market into clearly defined segments, providing a detailed analysis of emerging trends and precise revenue forecasts to support strategic decision-making.
- Fiber Composition
- Structural Application
- Mechanical Properties
- Thermal And Chemical Stability
- Manufacturing Techniques
- End Use Applications
- Fiber Integration
- Innovation And Technology
Regional Dynamics Shaping Synthetic Fiber Composite Adoption Across Key Markets
Regional dynamics reveal contrasting adoption patterns and strategic imperatives across the Americas, Europe, Middle East & Africa, and Asia-Pacific. In the Americas, established aerospace and automotive clusters are accelerating the integration of high-tensile and creep-resistant fibers into next-generation platforms. Manufacturing hubs in North America are also pioneering automation-driven prepreg processes to bolster domestic supply chains.
Europe, the Middle East & Africa (EMEA) region is characterized by stringent environmental and safety regulations that prioritize chemical resistance and environmental durability. EMEA composite fabricators leverage pultrusion and resin transfer molding to meet robust civil engineering and defense requirements, while research centers in Western Europe drive advances in bio-based fibers and surface modification.
Asia-Pacific stands out for its rapid industrialization and capacity expansion, particularly in automotive and wind energy sectors. Manufacturers here are investing heavily in dynamic load-characterized cyclic performance fibers and hybrid reinforcement architectures. The region’s expansive resin transfer molding and pultrusion facilities are also fueling competitive pricing and driving global supply for cost-sensitive applications.
This comprehensive research report examines key regions that drive the evolution of the High Performance Synthetic Fibers for Composites market, offering deep insights into regional trends, growth factors, and industry developments that are influencing market performance.
- Americas
- Asia-Pacific
- Europe, Middle East & Africa
Key Company Profiles and Competitive Positioning in the Synthetic Fiber Sector
Competitive analysis underscores a diverse landscape of established conglomerates and agile innovators. Industry stalwarts such as 3M Company, BASF SE, Dow Inc., and DuPont de Nemours, Inc. continue to leverage deep R&D pipelines to enhance polymer chemistries and surface treatments. Specialty fiber leaders including Teijin Limited, Toray Industries, Inc., and Mitsubishi Chemical Holdings Corporation focus on next generation materials and modified Pbo for aerospace and defense applications.
Corporate ventures such as FiberTech Innovations Inc. and UltraComposites Inc. are advancing nanotechnology integration and smart composite solutions, while Reliance Fiber Composites Ltd. and Prime Materials Corporation expand into bio-based fiber synthesis. Mid-tier players like Indorama Ventures Public Company Limited and Hyosung Corporation are forging partnerships to scale up high temperature resistant and low thermal conductivity fiber lines. Simultaneously, CompoFiber Materials Inc., Granite Polymer Company, and PolyOne Corporation are optimizing pultrusion process efficiencies to meet burgeoning demand in wind energy and construction materials.
Meanwhile, Solvay S.A. and SGL Carbon SE are reinforcing their positions in high tensile strength and impact resistance segments through strategic acquisitions. Emerging challengers such as Nexa Synthetic Fibers Corporation and SynTex Advanced Composites Ltd. specialize in hybrid reinforcement and automation-driven innovative techniques, positioning themselves to capture niche markets. Global giants like LyondellBasell Industries N.V., Kuraray Co., Ltd., and Kolon Industries, Inc. continue to diversify across fiber composition and manufacturing techniques, ensuring broad portfolio coverage. This competitive mosaic underscores the importance of integrated value chains, cross-sector collaborations, and continuous innovation.
This comprehensive research report delivers an in-depth overview of the principal market players in the High Performance Synthetic Fibers for Composites market, evaluating their market share, strategic initiatives, and competitive positioning to illuminate the factors shaping the competitive landscape.
- 3M Company
- BASF SE
- Celanese Corporation
- CompoFiber Materials Inc.
- Dow Inc.
- DSM Composite Solutions, LLC
- DSM Composites, Inc.
- DuPont de Nemours, Inc.
- FiberTech Innovations Inc.
- Granite Polymer Company
- Hexcel Corporation
- Hyosung Corporation
- Indorama Ventures Public Company Limited
- Kolon Industries, Inc.
- Kuraray Co., Ltd.
- LyondellBasell Industries N.V.
- Mitsubishi Chemical Holdings Corporation
- Mitsubishi Rayon Co., Ltd.
- Nexa Synthetic Fibers Corporation
- Owens Corning Incorporated
- PolyOne Corporation
- Prime Materials Corporation
- Reliance Fiber Composites Ltd.
- SGL Carbon SE
- Solvay S.A.
- SynTex Advanced Composites Ltd.
- Teijin Limited
- Toray Industries, Inc.
- UltraComposites Inc.
- Victrex plc
Actionable Recommendations for Industry Leaders to Navigate Emerging Challenges
Industry leaders should pursue a three-pronged strategy to sharpen competitive advantage. First, invest in scalable automation-driven and hybrid manufacturing techniques to optimize throughput and reduce per-unit costs, thereby offsetting external cost pressures such as tariffs or feedstock volatility. Second, advance material innovation by deepening research into bio-based fibers, nanotechnology integration, and smart composite architectures, ensuring rapid commercialization through co-development partnerships with end users.
Third, align product portfolios with evolving regulatory standards by enhancing chemical resistance, environmental durability, and high temperature performance. Collaborative engagements with certification bodies can accelerate qualification of advanced Pbo and modified polyacrylonitrile fibers for critical aerospace and defense programs. Additionally, exploring joint ventures in emerging regions of Asia-Pacific and the Middle East can secure strategic access to growth markets and localize supply chains.
Sustained success will also require dynamic segmentation strategies: leverage data-driven insights to tailor offerings across applications-from wind energy blades requiring pultrusion expertise to sporting goods demanding high impact resistance. By integrating advanced weaving, co-mingled structures, and interlayer reinforcement into modular design toolkits, companies can respond nimbly to bespoke performance requirements and shorten time-to-market.
Explore AI-driven insights for the High Performance Synthetic Fibers for Composites market with ResearchAI on our online platform, providing deeper, data-backed market analysis.
Ask ResearchAI anything
World's First Innovative Al for Market Research
Conclusion: Capitalizing on the Evolving Synthetic Fiber Composite Ecosystem
The high performance synthetic fiber composites sector stands at the nexus of technical innovation, regulatory evolution, and global supply chain realignment. Companies that align their R&D investments with sustainability goals and adopt flexible manufacturing platforms will outpace competitors constrained by legacy processes. Strategic collaborations-spanning raw material suppliers, equipment manufacturers, and end users-will accelerate material qualification and application testing, ensuring that novel fibers achieve rapid market adoption.
Looking ahead, market resilience will hinge on the ability to anticipate policy shifts and design adaptive supply chains that incorporate diverse geographic sourcing. At the same time, harnessing insights from advanced segmentation and regional analyses will enable precise targeting of growth pockets in electric vehicle integration, renewable construction, and defense modernization. By maintaining a dual focus on incremental performance gains and transformative fiber innovations, industry players can capitalize on the evolving composite ecosystem and deliver sustainable, high-value solutions.
This section provides a structured overview of the report, outlining key chapters and topics covered for easy reference in our High Performance Synthetic Fibers for Composites market comprehensive research report.
- Preface
- Research Methodology
- Executive Summary
- Market Overview
- Market Dynamics
- Market Insights
- Cumulative Impact of United States Tariffs 2025
- High Performance Synthetic Fibers for Composites Market, by Fiber Composition
- High Performance Synthetic Fibers for Composites Market, by Structural Application
- High Performance Synthetic Fibers for Composites Market, by Mechanical Properties
- High Performance Synthetic Fibers for Composites Market, by Thermal And Chemical Stability
- High Performance Synthetic Fibers for Composites Market, by Manufacturing Techniques
- High Performance Synthetic Fibers for Composites Market, by End Use Applications
- High Performance Synthetic Fibers for Composites Market, by Fiber Integration
- High Performance Synthetic Fibers for Composites Market, by Innovation And Technology
- Americas High Performance Synthetic Fibers for Composites Market
- Asia-Pacific High Performance Synthetic Fibers for Composites Market
- Europe, Middle East & Africa High Performance Synthetic Fibers for Composites Market
- Competitive Landscape
- ResearchAI
- ResearchStatistics
- ResearchContacts
- ResearchArticles
- Appendix
- List of Figures [Total: 32]
- List of Tables [Total: 605 ]
Call to Action: Engage with Our Specialist to Secure Your Comprehensive Report
To secure a comprehensive understanding of these market dynamics and support strategic decision-making, contact Ketan Rohom, Associate Director of Sales & Marketing. He will guide you through the research report’s detailed analysis and provide tailored insights to accelerate your competitive positioning. Reach out today to obtain the full market research report and leverage expert intelligence to drive your growth initiatives.
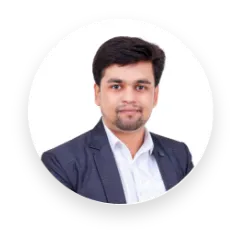
- When do I get the report?
- In what format does this report get delivered to me?
- How long has 360iResearch been around?
- What if I have a question about your reports?
- Can I share this report with my team?
- Can I use your research in my presentation?