Introduction: Navigating the High Solids Coatings Revolution
The high solids coatings market is at a pivotal juncture where sustainability objectives, regulatory mandates and technological advancements converge to redefine performance benchmarks. As industries increasingly prioritize environmental stewardship without compromising on durability or aesthetic appeal, high solids coatings emerge as a compelling solution. These formulations, characterized by elevated resin content and reduced solvent emissions, address stringent volatile organic compound (VOC) regulations while delivering robust protective layers across diverse surfaces. This executive summary offers decision-makers a concise yet comprehensive overview of market forces, policy shifts and innovation trajectories shaping the future of high solids coatings.
In this introduction, we explore the driving factors behind the accelerated adoption of high solids systems. Regulatory landscapes in North America and Europe have imposed progressively tighter VOC limits, urging formulators to seek alternatives that maintain application efficiency and finish quality. Simultaneously, end-user industries such as automotive, aerospace and construction demand coatings that offer superior corrosion resistance, faster cure times and enhanced life-cycle cost advantages. Technological breakthroughs in resin chemistry and additive packages further enable high solids coatings to match or exceed performance attributes of conventional solvent-borne counterparts.
The ensuing sections dissect transformative shifts in the competitive environment, quantify the impact of impending U.S. tariffs, reveal critical segmentation insights, examine regional and corporate dynamics, and conclude with actionable recommendations. This narrative equips experts and decision-makers alike to navigate complexity, capitalize on emerging opportunities and craft strategic initiatives for sustainable growth.
Transformative Shifts Reshaping the High Solids Coatings Landscape
The high solids coatings landscape is witnessing transformative shifts driven by evolving regulatory frameworks, sustainability imperatives and end-user demands for performance optimization. Regulatory agencies in major markets are accelerating timelines for VOC reductions, prompting formulators to reformulate solvent-borne coatings toward high solids or water-based systems. In parallel, procurement teams in the automotive and aerospace sectors are emphasizing life-cycle cost analysis, revealing that tools such as high solids epoxy primers deliver superior corrosion protection and reduced application costs over asset lifespans.
Moreover, digitalization and smart manufacturing trends are fostering closer collaboration between raw material suppliers, equipment manufacturers and paint applicators. Real-time data analytics now inform spray parameters and curing profiles, enabling precise control over film thickness and surface finish. This integration not only minimizes waste but also promotes consistent quality across high solids spray and flow applications. At the same time, rising raw material costs, especially for specialty resins and crosslinkers, are reshaping supply chain dynamics and accelerating consolidation among smaller formulators.
Finally, innovation in resin backbones and additive packages is yielding next-generation high solids coatings that elevate abrasion resistance, chemical tolerance and UV stability. These advancements are opening new application frontiers in marine, industrial and protective segments where substrate longevity and maintenance intervals are critical. As these transformative forces intensify, stakeholders must adapt strategies to align product portfolios, value propositions and go-to-market models with the rapidly shifting industry terrain.
Cumulative Impact of United States Tariffs Effective 2025
The enactment of new United States tariffs in 2025 will have a significant cumulative impact on the high solids coatings sector, altering cost structures and competitive positioning. Tariffs on imported specialty resins and performance additives are expected to drive up raw material prices, in some cases by double-digit percentages. This will put formulators under pressure to absorb costs or pass increases along to end-users, influencing contract negotiations and procurement strategies. Consequently, domestic resin producers may gain a temporary advantage, although they will face heightened expectations to ramp up capacity and ensure reliable supply chains.
Further, surcharges on finished coatings imports from key manufacturing hubs in Asia are set to erode margins for international suppliers, compelling them to explore local production alliances or invest in U.S.-based toll manufacturing. In turn, enterprises reliant on imported formulations will need to reevaluate inventory management and lead-time buffers, balancing the risk of supply disruption against the cost of holding excess stock. These dynamics are likely to accelerate consolidation among mid-tier players as they seek scale to negotiate raw material contracts and leverage in-house distribution networks.
In addition, the new tariffs may catalyze R&D investments in alternative chemistries and bio-based resins that are not subject to import duties, further diversifying the high solids coatings portfolio. Organizations that proactively adjust to this tariff environment-through strategic sourcing, vertical integration or technology partnerships-will be best positioned to maintain competitive pricing and secure market share in North America’s rapidly evolving coatings ecosystem.
Key Segmentation Insights Delivering Granular Market Understanding
A detailed examination of market segmentation offers essential insights into targeted strategies and value propositions for high solids coatings. When analyzing the market by application type, it becomes evident that aerospace coatings tailored for aircraft and defense applications demand superior thermal stability and chemical resistance, while the automotive segment must balance OEM coatings for factory finishes with refinishing products that deliver rapid cure and color fidelity. The construction dimension spans commercial exteriors requiring weather-resilient topcoats, infrastructural protective layers for bridges and pipelines, as well as residential interior and exterior paints with low odor and fast dry times. Industrial uses capture machinery, marine applications and metal works, where abrasion resistance and anti-corrosive properties are critical.
In the product type category, epoxy-based systems dominate industrial primers due to their adhesion and corrosion control; acrylic coatings, both thermoplastic and thermosetting, lead in architectural and automotive clearcoat performance; polyester variants, whether saturated or unsaturated, provide flexible yet hardwearing finishes for metal fabrication; and polyurethane formulations, including acrylic urethane and moisture-cure options, are prized for their gloss retention and chemical resilience. Technology type segmentation highlights powder coatings, available in thermoplastic or thermoset chemistries, as sustainable alternatives in appliance and metal furniture markets. Solvent-based systems, from traditional solvent-borne to ultra-low VOC blends, remain vital in niche applications where film-build and leveling are paramount. Water-based coatings, categorized into high solids and low solids waterborne formulations, continue to gain share thanks to environmental compliance and ease of cleanup.
From the perspective of end-user industries, automotive and transportation coatings encompass commercial vehicles, passenger cars and railways, all demanding stringent performance standards. The building and construction segment splits into exterior claddings and interior life-safety coatings, while the energy sector covers oil & gas assets that require flame-retardant finishes and renewable energy structures such as wind turbines necessitating UV-resistant topcoats. The industrial & OEM space, including electronics and packaging, calls for coatings that offer electrical insulation, anti-tamper properties and decorative aesthetics. Finally, resin type distinctions, from modified or pure alkyd coatings to fluoropolymer resins like FEP, PTFE and PVDF, through heat-resistant silicone and silicone alkyd, reveal opportunities for application-specific performance and differentiation.
This multi-dimensional segmentation framework enables manufacturers and suppliers to align R&D, marketing and sales efforts with the precise technical requirements and purchasing behaviors of each sub-market, enhancing product development pipelines and channel management.
This comprehensive research report categorizes the High Solids Coating market into clearly defined segments, providing a detailed analysis of emerging trends and precise revenue forecasts to support strategic decision-making.
- Application Type
- Product Type
- Technology Type
- End-User Industry
- Resin Type
Key Regional Insights Highlighting Geographic Dynamics
A regional analysis of the high solids coatings market reveals nuanced drivers and adoption patterns across the Americas, Europe Middle East & Africa and Asia-Pacific. In the Americas, stringent federal and state VOC regulations combined with robust automotive manufacturing investments in Mexico and the United States are fuelling growth in high-performance epoxy and polyurethane systems. Latin American markets are gradually transitioning from solvent-borne to water-based high solids solutions, supported by incentives for reducing industrial emissions and by infrastructure modernization programs.
In Europe, Middle East & Africa, regulatory harmonization under the REACH framework and regional VOC directives has accelerated R&D into ultra-low VOC high solids technologies. The Middle East’s construction boom and Africa’s expanding oil & gas infrastructure present sizable demand for corrosion-resistant and durable coatings, while renewable energy installations in North Africa drive uptake of UV stable high solids formulations on solar panel frames and turbine towers. Europe itself remains a leader in powder coating adoption, leveraging advanced curing technologies and emphasis on circular economy principles.
The Asia-Pacific region commands a significant share of global coatings consumption, propelled by rapid industrialization, urbanization and growing automotive and electronics manufacturing. China continues to dominate demand for high solids products in shipbuilding, rail and commercial vehicle coatings, with government policies incentivizing green manufacturing. Southeast Asian nations are scaling up high solids waterborne adoption in residential and commercial construction, while Japan and South Korea focus on specialty high solids chemistries for electronics encapsulation and semiconductor equipment protection.
This comprehensive research report examines key regions that drive the evolution of the High Solids Coating market, offering deep insights into regional trends, growth factors, and industry developments that are influencing market performance.
- Americas
- Asia-Pacific
- Europe, Middle East & Africa
Key Companies Insights Shaping Competitive Dynamics
Leading players shape the high solids coatings market through extensive product portfolios, global distribution networks and continuous innovation. AkzoNobel N.V. leverages its strong R&D capabilities to push high solids innovations in both industrial protective coatings and decorative segments, while Asian Paints Limited capitalizes on local manufacturing footprints and consumer insights to drive waterborne high solids adoption in emerging markets. Axalta Coating Systems, LLC. excels in automotive OEM and refinish systems, offering tailored high solids primers and clearcoats that meet OEM specifications for color consistency and corrosion control.
BASF SE utilizes its chemical expertise to develop novel resin backbones and crosslinkers that enable superior film performance, particularly in protective and industrial maintenance applications. Benjamin Moore & Co. emphasizes premium residential and commercial products that balance low VOC emissions with high coverage and durability. Hempel A/S focuses on marine and energy sector coatings, pioneering high solids formulations for offshore platforms and wind turbine foundations. The Jotun entities-Jotun A/S and Jotun Group-sustain a leadership position in protective and marine coatings, integrating sustainability metrics into every stage of their high solids product lifecycle.
Kansai Paint Co., Ltd. and Nippon Paint Holdings Co., Ltd. drive innovation in automotive coatings through localized R&D centers tailored to regional OEM requirements, while PPG Industries, Inc. maintains a broad portfolio across protective, industrial and architectural segments. RPM International Inc. leverages its specialty subsidiaries to offer niche high solids chemistries for infrastructure and rail markets, and The Sherwin-Williams Company, along with its Valspar business, delivers comprehensive solutions spanning powder, solvent-based and water-based high solids lines. Tikkurila Oyj rounds out the competitive landscape by focusing on decorative coatings with emphasis on color and finish performance in Scandinavian and Eastern European markets.
This comprehensive research report delivers an in-depth overview of the principal market players in the High Solids Coating market, evaluating their market share, strategic initiatives, and competitive positioning to illuminate the factors shaping the competitive landscape.
- AkzoNobel N.V.
- Asian Paints Limited
- Axalta Coating Systems, LLC.
- BASF SE
- Benjamin Moore & Co.
- Hempel A/S
- Jotun A/S
- Jotun Group
- Kansai Paint Co., Ltd.
- Nippon Paint Holdings Co., Ltd.
- PPG Industries, Inc.
- RPM International Inc.
- The Sherwin-Williams Company
- Tikkurila Oyj
- Valspar Paint (The Sherwin-Williams Company)
Actionable Recommendations for Industry Leaders to Drive Growth
To capitalize on the accelerating demand for high solids coatings, industry leaders should pursue a strategic blend of innovation, partnerships and operational excellence. First, intensify R&D collaborations with chemical suppliers and equipment manufacturers to co-develop next-generation resin and crosslinker systems that push performance envelopes while minimizing environmental impact. Adopting lean manufacturing and digital process controls will enhance throughput, reduce waste and deliver consistent quality, thereby securing cost advantages in a tariff-constrained environment.
Second, cultivate targeted alliances with regional distributors and applicators to deepen market penetration in growth geographies. Tailored training programs and technical support initiatives will ensure correct application techniques and foster customer loyalty. Third, leverage advanced data analytics to optimize resin sourcing and inventory management, mitigating the effects of supply chain volatility and ensuring just-in-time responsiveness to spikes in demand. Finally, integrate sustainability credentials across product marketing and corporate reporting, reinforcing compliance narratives and resonating with stakeholders who prioritize green procurement and ESG objectives.
Explore AI-driven insights for the High Solids Coating market with ResearchAI on our online platform, providing deeper, data-backed market analysis.
Ask ResearchAI anything
World's First Innovative Al for Market Research
Conclusion: Positioning for Sustainable Leadership in High Solids Coatings
In summary, the high solids coatings market stands at the confluence of regulatory tightening, raw material cost pressures and evolving end-user performance demands. Stakeholders who proactively align R&D, supply chain strategies and market engagement with these macro-drivers will outpace competitors and secure sustainable value creation. Embracing digitalization, fostering strategic partnerships and championing next-generation chemistries are essential to navigate complexities and capitalize on the transition toward greener, high solids coating solutions.
This section provides a structured overview of the report, outlining key chapters and topics covered for easy reference in our High Solids Coating market comprehensive research report.
- Preface
- Research Methodology
- Executive Summary
- Market Overview
- Market Dynamics
- Market Insights
- Cumulative Impact of United States Tariffs 2025
- High Solids Coating Market, by Application Type
- High Solids Coating Market, by Product Type
- High Solids Coating Market, by Technology Type
- High Solids Coating Market, by End-User Industry
- High Solids Coating Market, by Resin Type
- Americas High Solids Coating Market
- Asia-Pacific High Solids Coating Market
- Europe, Middle East & Africa High Solids Coating Market
- Competitive Landscape
- ResearchAI
- ResearchStatistics
- ResearchContacts
- ResearchArticles
- Appendix
- List of Figures [Total: 26]
- List of Tables [Total: 1036 ]
Call-To-Action: Secure Your Detailed High Solids Coatings Market Research Report Today
For a comprehensive, in-depth analysis of market trends, competitive landscapes and technological breakthroughs in high solids coatings, reach out to Ketan Rohom, Associate Director, Sales & Marketing, to acquire the full market research report. His expertise will guide you through tailored insights and data-driven recommendations to inform your strategic decision-making and accelerate growth.
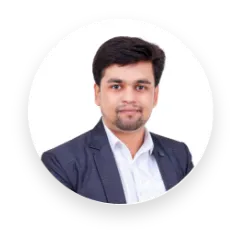
- When do I get the report?
- In what format does this report get delivered to me?
- How long has 360iResearch been around?
- What if I have a question about your reports?
- Can I share this report with my team?
- Can I use your research in my presentation?