Introduction to High-Tension Magnet Wire Dynamics
High-tension magnet wire lies at the heart of critical electrical and electronic systems, enabling efficient energy transfer and signal integrity in applications ranging from aerospace propulsion to electric vehicle drivetrains. As the global push for electrification intensifies, the performance demands on magnet wire have never been greater. Materials must withstand extreme thermal cycles, mechanical stresses and stringent insulation requirements, while maintaining conductivity and reliability over extended service lifespans. This emergence of complex use cases has propelled ongoing innovation in insulation chemistries, conductor alloys and manufacturing precision.
Within this evolving landscape, stakeholders-from material scientists to OEMs-must navigate shifting regulatory environments, supply chain challenges and rising raw material costs. By exploring the technological breakthroughs, policy-driven market shifts and competitive dynamics that define this arena, decision-makers can better align product roadmaps, procurement strategies and investment priorities. This executive summary begins with an overview of the fundamental drivers reshaping the high-tension magnet wire sector and then delves into the most impactful transformations, trade policy consequences, segmentation insights, regional dynamics and leading corporate activities. The synthesis culminates in practical guidance for industry leaders seeking to capitalize on emerging opportunities and mitigate risks amid unprecedented market complexity.
Transformative Shifts Reshaping the Magnet Wire Landscape
The high-tension magnet wire market is undergoing rapid transformation as legacy approaches give way to novel solutions driven by digitalization, sustainability and performance optimization. First, electrification megatrends across aerospace, automotive and renewable energy sectors are amplifying demand for wires that combine ultra-high temperature tolerance with minimal weight penalties. Advanced insulation materials such as polyimide composites and epoxy resins with nanofiller enhancements are replacing older standards to achieve higher dielectric strength and thermal stability.
Simultaneously, manufacturing technologies are shifting from batch-based processes toward continuous, automated lines enabled by real-time quality assurance systems. Inline sensors now detect microscopic conductor defects, while machine-learning algorithms predict process deviations before they impact yield. These developments are driving higher throughput and tighter tolerances without sacrificing cost efficiency.
Moreover, end users are seeking more transparent and traceable supply chains. Blockchain-backed platforms are emerging to verify raw material origin and compliance with environmental and labor standards. This convergence of performance-driven product innovation, process automation and digital traceability is redefining competitive benchmarks and resetting expectations across the entire value chain.
Cumulative Impact of United States Tariffs 2025
The impending implementation of United States tariffs in 2025 has added a new layer of complexity to raw material sourcing and cost management. Aluminum and copper wire imports-once crucial to balancing domestic production capacity-now face heightened duties that can significantly inflate input expenses. Suppliers are responding by evaluating alternative feedstocks, including hybrid composites that blend conductive copper cores with lighter aluminum strands to optimize both cost and performance.
At the same time, many manufacturers are regionalizing production footprints to mitigate tariff exposure. Investments are being directed toward facilities in low-duty jurisdictions, and strategic partnerships with local coil winding and insulation specialists are accelerating. However, these adjustments often entail longer lead times and require close alignment of technical specifications across geographies.
Policy volatility has also prompted firms to bolster inventory buffers and renegotiate supplier contracts with flexible pricing clauses. Legal teams are increasingly involved in procurement negotiations to ensure compliance and to manage the risk of retroactive duty assessments. These collective measures underscore the significant ripple effects that tariff policy can impose on margin structures, supply chain resilience and long-term strategic planning.
Key Segmentation Insights
High-tension magnet wire products are often categorized by construction type, insulation material and conductor composition, each influencing application suitability and performance trade-offs. For instance, enamelled wires-whether single strand or stranded-are prized for ease of coil winding, while polyimide-insulated variants command premium positions in high-temperature environments. Insulation selection itself spans epoxy resins for cost-effective moderate-temperature use, polyester for chemical resistance and polyimide for extreme thermal cycles. Conductor composition further diversifies offerings: pure copper wire delivers unmatched conductivity, aluminum wire reduces weight in transport applications, and hybrid composites seek to blend both attributes seamlessly.
Beyond physical profiles, performance traits such as operating temperature range directly inform design choices. Wire rated for high-temperature service is essential in aviation power electronics, whereas medium- and low-temperature variants suit industrial motors and household appliances. Tensile strength and flexibility ratings differentiate wires designed for dynamic motion-like those in robotic arms-from more static wound coils. Voltage rating classifications, whether insulated for high-voltage transformers or non-insulated for compact electric motors, further refine application targeting.
End-use segmentation illuminates demand patterns: aerospace systems call for ultra-lightweight, high-dielectric solutions; automotive equipment prioritizes wires engineered for electric and hybrid vehicles; electrical machines rely on variants tailored to generators, motors and transformers. Technological features such as advanced insulation techniques, continuous versus batch manufacturing and ISO-certified quality assurance influence supplier selection. Finally, distribution efficiency, production capacity and raw material sourcing considerations shape supply chain strategies, ensuring availability and cost control.
This comprehensive research report categorizes the High-Tension Magnet Wire market into clearly defined segments, providing a detailed analysis of emerging trends and precise revenue forecasts to support strategic decision-making.
- Product Profile
- Performance Traits
- End Use Applications
- Technological Features
- Supply Chain Characteristics
Key Regional Insights
Regional dynamics play a pivotal role in shaping high-tension magnet wire strategies. In the Americas, regional manufacturers leverage domestic metal supplies to support growing electric vehicle infrastructure and renewable energy projects, optimizing distribution networks to serve both North and South America. Europe, Middle East and Africa present a diverse landscape: automotive electrification in Western Europe is fueling demand for high‐temperature, high‐voltage solutions, while energy transmission upgrades across the Middle East and Africa are driving need for durable transformers and generator wire. In Asia-Pacific, rapid expansion of electrical machine production-spanning consumer electronics, industrial automation and e-mobility platforms-is intensifying competition among local and multinational wire providers. To navigate these varied requirements effectively, stakeholders are adopting region-specific formulations and collaborating closely with local integrators to align product performance with regulatory and environmental mandates.
This comprehensive research report examines key regions that drive the evolution of the High-Tension Magnet Wire market, offering deep insights into regional trends, growth factors, and industry developments that are influencing market performance.
- Americas
- Asia-Pacific
- Europe, Middle East & Africa
Key Companies Insights
The competitive environment is characterized by a mix of specialized innovators and established conglomerates. Companies such as Advanced Wire Products Inc. and Apex Magnet Wire Systems Ltd. focus on niche insulation technologies and customized alloy formulations. Atlas Wire Technologies Inc. and CircuitMag Solutions Corp. have centered their strategies on integrated manufacturing processes, leveraging real-time quality assurance to reduce defect rates. DuraWire Solutions Corporation and Dynawire Solutions Inc. are known for their investments in continuous production capabilities and raw material traceability platforms.
ElectroMag Components Inc. and Electric Core Components Corp. differentiate through proprietary high-tensile conductor treatments, while Elite Magnet Wire Solutions LLC and Energex Wire Systems Inc. specialize in ultra-lightweight hybrid composites for aerospace and automotive applications. FutureWire Innovations Inc. and High Voltage Wireworks Ltd. focus on high-voltage transformer wires, and Imperial Magnetics LLC and Innovatech Wire Solutions Ltd. emphasize advanced polyimide insulation for extreme thermal environments.
MagnaVolt Industries Inc., Magnet Masters Inc. and MagnetiCore LLC have expanded their footprints through strategic acquisitions, complementing their core capabilities with Electromagnetic Design expertise. MagnetoTech Industries Inc., Neo Magnetics Group Inc. and Pioneer Insulated Wires Inc. have built reputations on flexible winding solutions and custom testing services. Precision Magnetics Inc., Precision Wire Solutions LLC and ProtoWire Research LLC lead in ISO-certified quality assurance, while Quantum Magnetics LLC and Quantum Wire Systems Corp. push boundaries in conductor alloy innovation. Solaris Magnetics Corp., Sonic WireWorks Inc. and SteelCore Magnetics Ltd. have optimized their distribution efficiency, and UltraMagnet Components Inc., Vector Magnetics GmbH and Vertex Advanced Components Inc. balance production capacity with sustainable sourcing. Vulcan Electric Controls Ltd. and Zenith Wire Manufacturers Inc. round out the landscape by providing turnkey coil and transformer assembly services integrated with magnet wire supply.
This comprehensive research report delivers an in-depth overview of the principal market players in the High-Tension Magnet Wire market, evaluating their market share, strategic initiatives, and competitive positioning to illuminate the factors shaping the competitive landscape.
- Advanced Wire Products Inc.
- Apex Magnet Wire Systems Ltd.
- Atlas Wire Technologies Inc.
- CircuitMag Solutions Corp.
- DuraWire Solutions Corporation
- Dynawire Solutions Inc.
- Eclipse Magnet Wire Corp.
- Electric Core Components Corp.
- ElectroMag Components Inc.
- Elite Magnet Wire Solutions LLC
- Energex Wire Systems Inc.
- FutureWire Innovations Inc.
- High Voltage Wireworks Ltd.
- Imperial Magnetics LLC
- Innovatech Wire Solutions Ltd.
- Integral Wire Technologies Inc.
- Ionix Wire Technologies Inc.
- MagnaVolt Industries Inc.
- Magnet Masters Inc.
- MagnetiCore LLC
- MagnetoTech Industries Inc.
- Neo Magnetics Group Inc.
- Pioneer Insulated Wires Inc.
- Precision Magnetics Inc.
- Precision Wire Solutions LLC
- ProtoWire Research LLC
- Quantum Magnetics LLC
- Quantum Wire Systems Corp.
- Solaris Magnetics Corp.
- Sonic WireWorks Inc.
- SteelCore Magnetics Ltd.
- UltraMagnet Components Inc.
- Vector Magnetics GmbH
- Vertex Advanced Components Inc.
- Vulcan Electric Controls Ltd.
- Zenith Wire Manufacturers Inc.
Actionable Recommendations for Industry Leaders
Industry leaders should prioritize a multi-pronged approach to sustain growth and resilience. First, accelerate integration of advanced insulation materials-especially polyimide nanocomposites-to meet escalating performance benchmarks in e-mobility and aerospace sectors. Second, modernize manufacturing footprints by transitioning from batch to continuous processes, supported by inline digital inspection systems that reduce scrap and rework. Third, diversify raw material sourcing through strategic supply agreements and explore hybrid composite formulations to mitigate exposure to copper and aluminum price volatility. Fourth, deepen collaboration with downstream OEMs by co-developing custom winding and quality assurance protocols, ensuring seamless product integration and reducing time to market. Finally, expand regional production or distribution hubs to navigate tariff landscapes effectively and to align closely with local regulatory requirements, leveraging partnerships with logistics specialists and contract winders.
Explore AI-driven insights for the High-Tension Magnet Wire market with ResearchAI on our online platform, providing deeper, data-backed market analysis.
Ask ResearchAI anything
World's First Innovative Al for Market Research
Conclusion
As the high-tension magnet wire sector advances into an era defined by electrification, automation and sustainability, the interplay between material innovation, process optimization and supply chain agility will determine competitive advantage. Leaders who embrace cutting-edge insulation chemistries, invest in seamless digital manufacturing ecosystems and forge strategic alliances across regions will be best positioned to meet the evolving demands of e-mobility, aerospace and renewable energy markets. By integrating robust quality assurance frameworks and flexible sourcing models, companies can future-proof their operations against regulatory shifts and raw material uncertainties. In doing so, they will not only address immediate performance requirements but also lay the groundwork for next-generation power and signal transmission solutions.
This section provides a structured overview of the report, outlining key chapters and topics covered for easy reference in our High-Tension Magnet Wire market comprehensive research report.
- Preface
- Research Methodology
- Executive Summary
- Market Overview
- Market Dynamics
- Market Insights
- Cumulative Impact of United States Tariffs 2025
- High-Tension Magnet Wire Market, by Product Profile
- High-Tension Magnet Wire Market, by Performance Traits
- High-Tension Magnet Wire Market, by End Use Applications
- High-Tension Magnet Wire Market, by Technological Features
- High-Tension Magnet Wire Market, by Supply Chain Characteristics
- Americas High-Tension Magnet Wire Market
- Asia-Pacific High-Tension Magnet Wire Market
- Europe, Middle East & Africa High-Tension Magnet Wire Market
- Competitive Landscape
- ResearchAI
- ResearchStatistics
- ResearchContacts
- ResearchArticles
- Appendix
- List of Figures [Total: 26]
- List of Tables [Total: 725 ]
Call to Action: Connect with Ketan Rohom for Your Market Research Report
To explore the full depth of insights and actionable data on high-tension magnet wire dynamics, contact Ketan Rohom, Associate Director of Sales & Marketing. Engage directly with an expert to tailor the findings to your strategic priorities and ensure your organization capitalizes on emerging technologies, policy shifts and competitive trends. Reach out today to secure your comprehensive market research report and drive informed decision-making.
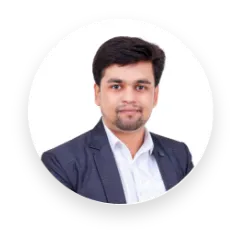
- When do I get the report?
- In what format does this report get delivered to me?
- How long has 360iResearch been around?
- What if I have a question about your reports?
- Can I share this report with my team?
- Can I use your research in my presentation?