Introduction to the High Value-Added Investment Casting Landscape
The high value-added investment casting sector is undergoing rapid transformation, driven by evolving customer requirements and technological breakthroughs. Investment casting, known for its precision and versatility, serves critical markets such as aerospace, medical devices, and power generation. As demand for complex geometries and stringent metallurgical properties grows, manufacturers are challenged to deliver superior surface finishes, tight tolerances, and enhanced mechanical performance. This executive summary explores current dynamics, highlighting key shifts and strategic imperatives for stakeholders.
Over the past decade, material science advancements and digital process controls have elevated the quality benchmarks for cast components. Consequently, leading producers are leveraging artificial intelligence and automation to refine mold design, optimize thermal profiles, and accelerate cycle times. Simultaneously, regulatory pressures and customer expectations for sustainability have prompted the adoption of eco-friendly binders and recycled feedstocks. By comprehensively examining these developments, decision-makers can identify opportunities to differentiate through innovation, cost efficiency, and supply chain resilience.
Transformative Shifts Reshaping the Investment Casting Landscape
The investment casting landscape is shifting beneath our feet, reshaped by four transformative forces. First, additive manufacturing integration is redefining mold fabrication, enabling conformal cooling channels and intricate cores that were once impossible. Second, the infusion of machine learning into process monitoring is empowering real-time defect detection and predictive maintenance, minimizing scrap rates and unplanned downtime. Third, sustainability mandates are driving the use of biodegradable waxes and low-emission furnaces, aligning production with global decarbonization targets. Finally, geopolitical dynamics and supply chain disruptions have encouraged nearshoring strategies, ensuring continuity for critical defense and aerospace programs.
These shifts are not mutually exclusive; rather, they coalesce into a new paradigm where digital twins simulate every thermal gradient, robotics handle fragile shells, and data analytics fine-tune alloy chemistry. Consequently, casting specialists who embrace these trends are poised to outperform in quality, speed, and environmental stewardship. Conversely, those who resist change risk obsolescence as customers increasingly prioritize partners capable of delivering next-generation components under tighter cost and regulatory constraints.
Cumulative Impact of U.S. Tariffs on Investment Casting in 2025
In 2025, the cumulative impact of United States tariffs has imposed a substantial cost burden on imported raw materials and finished castings. Tariffs on ferrous alloys, aluminum, and specialty metals have elevated input costs by up to 15%, prompting manufacturers to reassess sourcing strategies. Many casting operations have responded by diversifying suppliers across Latin America, Southeast Asia, and Eastern Europe to mitigate exposure. Simultaneously, tariff-induced price hikes have accelerated vertical integration, with some foundries investing in in-house melting and alloying capabilities to secure steady supply and better margin control.
However, these measures come with capital expenditure demands and extended lead times, challenging smaller producers with limited financial flexibility. Meanwhile, end-users in oil and gas and industrial machinery are seeking long-term contracts to stabilize procurement costs, shifting risk onto casting vendors. As a result, supply agreements now often include cost-adjustment clauses tied to tariff fluctuations, fostering transparency but adding contractual complexity. Moving forward, proactive engagement with policy developments and close collaboration with trade experts will be essential for casting leaders to navigate this evolving tariff environment.
Deep Dive into Segmentation Insights Across Materials, Processes, and Applications
The investment casting market can be dissected through seven interrelated segmentation lenses, each revealing distinctive growth drivers and competitive dynamics. Based on material type, the market divides into ferrous alloys-iron and steel-and non-ferrous alloys, including aluminum, copper, magnesium, titanium, and zinc, each chosen for properties like strength-to-weight ratio or corrosion resistance. In terms of process, traditional directional solidification branches into columnar grain and single crystal variants, while rapid investment casting encompasses additive manufacturing and rapid tooling, accelerating mold production cycles.
Application segmentation highlights aerospace, automotive, industrial, medical, and oil and gas. Within aerospace, demand for commercial aircraft, military platforms, and spacecraft components underscores the need for high-temperature nickel superalloys. Automotive casting spans commercial vehicles, electric vehicles, and performance cars, with EV adoption driving lightweight aluminum and titanium castings. Medical applications bifurcate into orthopedic implants and surgical instruments, requiring biocompatibility and surface finish control. In oil and gas, downstream, midstream, and upstream operations rely on wear-resistant parts for pumps, valves, and pipelines.
From an end-use perspective, casting demand originates in aerospace and defense, automotive, healthcare, and industrial machinery, each with unique certification and quality assurance protocols. Material characteristics-density, durability, and surface finish-further refine selection criteria, with durability sub-segments focusing on corrosion and high-temperature resistance. Supply chain segmentation identifies distributors, end-users, and raw material suppliers, the latter including ceramic material and metal suppliers responsible for feedstock quality. Finally, technological integration spans 3D printing technologies, artificial intelligence, and automation, the last of which leverages robotics to enhance repeatability and reduce manual errors. Collectively, these segmentation insights help stakeholders prioritize investments, tailor offerings, and anticipate shifting demand across the casting value chain.
This comprehensive research report categorizes the High Value-Added Investment Casting market into clearly defined segments, providing a detailed analysis of emerging trends and precise revenue forecasts to support strategic decision-making.
- Type
- Process
- Application
- End-Use Industry
- Material Characteristics
- Supply Chain
- Technological Integration
Key Regional Dynamics Shaping Investment Casting Demand
Regional market dynamics reveal distinct competitive landscapes. In the Americas, robust aerospace and defense spending-particularly in the United States-and growing electric vehicle production in North and South America drive demand for high-value castings. Casting facilities here focus on lean manufacturing and compliance with stringent environmental regulations. Meanwhile, the Europe, Middle East & Africa region exhibits a balanced mix of legacy aerospace hubs, expanding renewable energy infrastructure, and thriving automotive clusters in Germany, France, and Italy. Foundries are investing in green technologies and additive integration to meet both emissions targets and high-precision requirements for industrial machinery.
In the Asia-Pacific, rapid industrialization and escalating demand for consumer electronics, medical devices, and regional aerospace projects are propelling market growth. China and India lead in new capacity additions, while Japan and South Korea concentrate on advanced alloys and process automation. Although regulatory frameworks vary widely across the region, many nations are adopting tighter quality standards to support imports for global supply chains. Consequently, casting providers with scalable operations and technology-driven quality assurance systems are best positioned to capture opportunities across these diverse regional markets.
This comprehensive research report examines key regions that drive the evolution of the High Value-Added Investment Casting market, offering deep insights into regional trends, growth factors, and industry developments that are influencing market performance.
- Americas
- Asia-Pacific
- Europe, Middle East & Africa
Competitive Landscape and Profiles of Leading Casting Manufacturers
Leading firms are distinguishing themselves through strategic initiatives, technological investments, and global footprints. Alcoa Corporation continues to leverage its upstream aluminum capabilities, while Arconic Inc. integrates lightweight alloy expertise with digital mold simulation. ATI’s focus on specialty alloys for aerospace and defense underscores its material science leadership. Under 3M’s Ceradyne banner, advanced ceramic casting solutions are gaining traction in wear applications. CIREX B.V. specializes in precision tooling and core production, enabling rapid turnaround for complex geometries.
Doncasters Group Ltd. combines thermal spray technology with casting to improve component lifespan. Hitachi Metals, Ltd. benefits from deep metallurgical know-how in high-performance heat-resistant alloys. Howmet Aerospace Inc. and Precision Castparts Corp. compete fiercely in the nickel-based superalloy segment, supplying critical gas turbine and jet engine parts. Richmond Industries, Inc. offers niche capabilities in large structural castings. Signicast, a Form Technologies Company, focuses on mid-volume aluminum and zinc components. TITAL GmbH, an Arconic company, emphasizes titanium castings for aerospace. Wall Colmonoy Corporation is renowned for its hard-facing alloys, while Zollern GmbH & Co. KG delivers steel and superalloy castings across European markets. Together, these players define competitive benchmarks in quality, innovation, and supply chain integration.
This comprehensive research report delivers an in-depth overview of the principal market players in the High Value-Added Investment Casting market, evaluating their market share, strategic initiatives, and competitive positioning to illuminate the factors shaping the competitive landscape.
- Alcoa Corporation
- Arconic Inc.
- ATI (Allegheny Technologies Incorporated)
- Ceradyne, Inc. (3M Company)
- CIREX B.V.
- Doncasters Group Ltd.
- Hitachi Metals, Ltd.
- Howmet Aerospace Inc.
- Precision Castparts Corp.
- Richmond Industries, Inc.
- Signicast, A Form Technologies Company
- TITAL GmbH (An Arconic Company)
- Wall Colmonoy Corporation
- Zollern GmbH & Co. KG
Actionable Recommendations to Drive Growth and Operational Excellence
To navigate increasing complexity and capture emerging opportunities, industry leaders should pursue five strategic actions. First, accelerate digital transformation by deploying process-integrated sensors and machine learning algorithms, enabling predictive quality control and energy optimization. Second, diversify raw material sourcing by establishing partnerships with suppliers in low-tariff jurisdictions and exploring recycled alloys, thereby enhancing supply chain resilience and cost predictability. Third, invest in sustainable process innovations, such as binder-less shell systems and renewable energy-powered furnaces, to meet tightening environmental standards and reduce lifecycle carbon footprints.
Fourth, expand cross-functional collaboration between design, engineering, and quality teams to drive concurrent product and process development, shortening time-to-market for complex components. Finally, cultivate talent by upskilling the workforce in automation, data analytics, and advanced metallurgy, ensuring operational excellence and fostering a culture of continuous improvement. Implementing these recommendations will enable casting providers to outperform on quality, cost, and sustainability metrics, delivering strategic value to customers in critical end-use industries.
Explore AI-driven insights for the High Value-Added Investment Casting market with ResearchAI on our online platform, providing deeper, data-backed market analysis.
Ask ResearchAI anything
World's First Innovative Al for Market Research
Conclusion: Aligning Technology, Resilience, and Sustainability
As investment casting evolves, success will hinge on balancing innovation with pragmatic supply chain strategies. Companies that integrate digital twins, additive manufacturing, and sustainable practices will set new quality and efficiency standards. At the same time, proactive tariff management and supplier diversification will safeguard margins in an uncertain policy environment. Leveraging segmentation insights-from material choice to application requirements-enables tailored offerings that resonate with aerospace, automotive, medical, and industrial customers alike.
Ultimately, partnerships forged on transparency, collaborative development, and shared risk will define market leadership. By aligning technological prowess with robust operational frameworks and environmental responsibility, casting specialists can navigate volatility and capitalize on demand for ever more sophisticated components. This executive summary underscores the strategic imperatives that will shape the next chapter of the high value-added investment casting industry.
This section provides a structured overview of the report, outlining key chapters and topics covered for easy reference in our High Value-Added Investment Casting market comprehensive research report.
- Preface
- Research Methodology
- Executive Summary
- Market Overview
- Market Dynamics
- Market Insights
- Cumulative Impact of United States Tariffs 2025
- High Value-Added Investment Casting Market, by Type
- High Value-Added Investment Casting Market, by Process
- High Value-Added Investment Casting Market, by Application
- High Value-Added Investment Casting Market, by End-Use Industry
- High Value-Added Investment Casting Market, by Material Characteristics
- High Value-Added Investment Casting Market, by Supply Chain
- High Value-Added Investment Casting Market, by Technological Integration
- Americas High Value-Added Investment Casting Market
- Asia-Pacific High Value-Added Investment Casting Market
- Europe, Middle East & Africa High Value-Added Investment Casting Market
- Competitive Landscape
- ResearchAI
- ResearchStatistics
- ResearchContacts
- ResearchArticles
- Appendix
- List of Figures [Total: 30]
- List of Tables [Total: 817 ]
Take the Next Step: Connect with Our Associate Director for the Full Report
To explore the full market research report and gain deeper insights, contact Ketan Rohom, Associate Director, Sales & Marketing, to discuss how this analysis can inform your strategic decisions and drive competitive advantage.
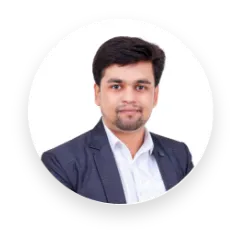
- When do I get the report?
- In what format does this report get delivered to me?
- How long has 360iResearch been around?
- What if I have a question about your reports?
- Can I share this report with my team?
- Can I use your research in my presentation?